Compression: Pumping It Up Toward Perfection

In today’s climate change-constricted world, engineers who are comfortable with the role compression can play in unraveling the mystery of how to eliminate methane leaks and still produce newly unlocked massive North American natural gas supplies will always be in high demand.
It is this sort of industrial puzzle that keeps folks on their toes at organizations such as the Gas Machinery Research Council (GMRC), the Pipeline Research Council International (PRCI) and the Interstate Natural Gas Association of America (INGAA).
Methane emissions from the natural gas transmission pipeline and storage sector have been on federal air regulators’ radar for some time and an equally hot topic for INGAA and its member companies.
In mid-summer 2015, INGAA officials were touting the latest data from a Colorado State University (CSU) study showing federal government estimates on methane leaks that were at least 27% higher than data compiled by the CSU researchers that used data from 2,292 new onsite measurements and equipment at 922 separate facilities. Thus, CSU built a new computer model to calculate overall emissions from the pipeline/storage sector.
CSU-led research concluded that 0.35% of the methane transported by the transmission/storage sector in 2012 – the most recent year with complete data – was released into the atmosphere. That is markedly lower than federal estimates of 0.48%.
“As confirmed in the CSU-led study, there have been significant changes in the composition of the compressor fleet itself, and other technologies used in compressor stations during the 35-plus years since collection of the data that formed the basis for the [federal Environmental Protection Agency] emission factors used for the gas transmission/storage sector in the EPA greenhouse gas [GHG] inventory,” said Terry Boss, INGAA’s senior vice president for environment, safety and operations.
Boss underscored the fact that no one knows precisely how much of the decades-long reductions in emissions are attributable to the changes in compression, but “it is clearly a very significant contributor.”
Based on preliminary data in mid-2015, GHG reductions appear to have dropped significantly, sources at PRCI indicate. The research organization’s analysis of the data indicates the “majority of the methane leak emissions from compressor stations are related to a small number of components.” Emissions reported in 2012 were approximately two-thirds of those reported the previous year.
INGAA officials echo the rest of the oil and gas industry in reiterating that ongoing decisions about new and replacement compressor engines will always error on the side of the newest technology. These decisions, they maintain, stress customer needs, reliability and environmental compliance, the latter being an ever-greater factor.
In addition, many INGAA member companies are involved in consortium research projects helping develop new compression technology, such as ongoing work with PRCI.
Major pipeline operators and engine/compressor manufacturers are members of PRCI’s Compressor and Pump Station Technical Committee, and they provide the direction and review for PRCI’s research efforts associated with compression equipment, said Gary Choquette, PRCI senior program manager for facilities.
The compression sector is nothing like what the predecessors of today’s generation of engineers and technicians dealt with. Regulations increasingly are driving safety and environmental requirements. Operating skills depend much more on information technology (IT) that is constantly changing, and it’s raising the level of the sophistication of the work, allowing things to be done more quickly and accurately, Choquette and others in the industry say.
Much of the work being done on the PRCI compression committee is focusing on:
• Improving the accuracy of the air-emission dispersion models, such as the Environmental Protection Agency (EPA) AERMOD tool.
• Assessing the effect of dynamic changes in fuel composition on engine performance and emissions and developing control methods to optimize the engine operation.
• Developing and assessing technologies to reduce oil carryover into the exhaust and the associated particulate emissions.
• Performing enhanced modeling and assessing control methods for exhaust catalysts.
• Developing methods to continuously monitor equipment operation for performance and efficiency.
• Developing and assessing technologies that improve the efficiency of compression equipment and reduce other sources of GHG emissions.
A top priority for operators is keeping up with compliance requirements, and the challenge is to find as many ways as possible to extend the life of legacy compressors by finding economical retrofit solutions that preserve safety and reliability while meeting the more stringent environmental requirements. This is where puzzle-solving skills and the application of various IT advances become critical, according to Choquette, who said there are potential multimillion-dollar savings at stake in just one compressor unit.
Among the innovations that promise to upgrade safety and efficiency in compression is a technology dubbed Performance Augmentation Network (PAN), operating on two compressors in the Williams pipeline system in northeastern Pennsylvania. The GMRC and Williams’ Craig Linn, engineering director for Northeast U.S. operations and chair of the GMRC’s board, have helped fund and steer the collaborative technology advances that promise big dividends.
Two entrepreneurial firms, Optimum Pumping Technology (OPT) in Allegheny County, PA, and Cambridge, OH-based ACI Services Inc. have collaborated to retrofit PAN, which Optimum and its founder Glen Chatfield helped create. They collaborated in creating the retrofit compressor equipment, working with the GRMC and Institute of Natural Gas Research at Penn State University. They are hoping the interest in compression advancements will spark national attention in both the public and private sectors. PAN is the culmination of eight years of research and development.
Installed on both the Zick and Lathrop units at Williams, PAN was applied to an Ariel JGT/4 single-stage reciprocating compressor driven by a Caterpillar G3516 gas engine, rated at 1,380 bph at 1,400 rpm. Both packages were fabricated by Houston-based Enerflex Systems.
Generally, compressors are categorized as reciprocating or centrifugal, but there are various drivers for both types, such as reciprocating engines, turbines and electric motor drives. The reciprocating engines come in slow-speed integral units (250-300 rpm) and high-speed separable units (900-1,200 rpm). Couplings between the driver and the compressor also take various forms such as direct drive and gear couplings.
“By canceling pulsations, rather than dampening them as current bottle pulsation control approaches do, the PAN reduces system pressure losses,” ACI Services’ Norm Shade wrote in a 2014 report on the system to GRMC. “Further, it reflects pressure waves back to individual cylinder suction and discharge flanges at precise times during the compression cycle when the valves are open.”
Williams’ Linn added that PAN reduces pulsation and vibration resulting in the ability of the compressor to run with higher flow, improving safety. It allows the compressor to operate at a point further away from what is commonly known as the “surge line” (6% shift) on the compressor map.
As part of the collaborative effort that created this advancement that has now passed most of its tests with Williams, OPT included its “virtual pumping system” software that was developed from years of experience designing high-performance reciprocating engines, and ACI included its patent-pending tuning section transition (TST) collectors. The collectors allow the PAN system to cancel – not just mitigate – pulsations in the compression.
Another efficiency and safety factor in compression, “torsional vibration” spawned a massive collaborative effort in 2013-15 led by ACI Services and supported by 39 industry experts from 26 companies, including motor, engine, compressor, coupling/variable frequency drive manufacturers, analysis/testing companies, end-users, and engineering consultants. The result was a new GRMC “guideline and recommended practice” for operators on torsional vibration.
“It educates those who are responsible for a compressor installation as to what to expect from a torsional vibration analysis, as well as the significance of the different elements of the analysis,” said Williams’ Linn in discussing the new operating guide, GMRC Guideline and Recommended Practice for Control of Torsional Vibrations in Direct-Driven Separable Reciprocating Compressors.
Drilling down into the 21st century variety of compression is a complex web with innovation and regulation focusing on GHG emissions, control systems, compression types, air/fuel mix and even the levels of oil consumption in cylinders. For the compression engineers, these are the pieces that comprise a constantly shifting puzzle.
In the air quality arena, of late there have been industry-led field studies to improve the accuracy of the EPA’s AERMOD modeling tool that is used to verify compressors’ compliance with ambient nitrogen dioxide (NO2) standards. The latest NO2 standards have made it more difficult for operators to demonstrate compliance using AERMOD, according to experts at PRCI.
“A joint project ongoing with INGAA, the INGAA Foundation, the American Petroleum Institute [and PRCI] is gathering actual ground-level concentrations that can be used to enhance the AERMOD tool,” PRCI’s Choquette said. This summer the last of the monitors for the studies were being put in place, he noted.
As the controversial Obama administration Clean Power Plan demonstrates, emissions are a central, bottom-line focus for any type of industrial operation in the 21st century. Among the ongoing industry upgrades for compression are multiple efforts to create and enhance what Choquette calls “continuous engine performance monitoring (CEPM).” The compressor operators are also working hard to develop a better understanding of the fundamental reactions in catalytic reduction technologies for exhaust emissions.
PRCI, in 2015, completed research focused on upgrading the quality of portable emission instruments used in testing NOx and carbon monoxide (CO) emission rates, developing a modified approach to quality assurance/quality control (QA/QC) criteria. It has tied more closely the portable analyzer test methods and protocols to appropriate QA/QC requirements. Separately, there are also now more advanced laser-based technologies to measure exhaust of NOx and CO.
Lasers are seen by compression engineers as a possible alternative to current continuous emissions monitoring systems (CEMS). One expert indicated to P&GJ that it may turn out to be a better economic option than existing technologies for operations that are required to install CEMS.
Both operating efficiencies and emission mitigation advances are tied closely to IT-driven control systems improvements, and that is another area on which the industry research and development efforts are tightly focused. PRCI and others counted multiple efforts in various stages of development at mid-year 2015, with much of the effort looking at improving air/fuel controls for large-bore and lean-burn engines. As a result, operators can consider:
• Better tools to determine the air-flow requirements to provide a given NOx emission level, leading to better ways to develop turbocharger specifications.
• A modeling of engine air flow rates and scavenging efficiency based on given operating conditions and emission rates.
• A standardized code for a technology transfer method to implement optimized air/fuel control methods.
“Improvements in air/fuel control result in more reliable compliance to NOx emissions over a broad operating range and a large range of fuel compositions,” Choquette said. “It also helps to maximize energy efficiency and therefore minimize CO2 emissions.” Conversely, improper air/fuel control can cause damaging engine detonations and misfires, he warned.
PRCI has developed methods to estimate GHG emission rates from the different pneumatic devices, offering help for allowing operators to target modifications to the devices with the highest emission rates and in better designing new facilities that can reduce the GHG footprint of compression.
There are also new ways for optimizing engine controls for fast-unfolding changes in the composition of the fuel gas stream. And for legacy engines, which are increasingly being upgraded to extend their working lives, there is an engine power cylinder cycle level control.
Industry experts continue to focus on efficiency and safety gains that can be wrung out of the compression system, noting that this translates into cost and environmental benefits. This means looking in-depth at every piece of the compression pie. For example, there are efforts ongoing to develop what Linn calls a “theoretical basis for oil consumption in reciprocating compressor cylinders.” He said the prize is twofold.
“First, there are operating cost reductions by injecting the appropriate amount of oil to maintain operation and reduced wear on power and compressor cylinders,” he said.
“Second, there is the benefit of reducing the amount of carryover oil that gets into the pipeline, which then requires inline pipeline mechanical cleaning through the use of cleaning pigs, rubber cupped tools or sphere-type pigs.”
Many of the advancements collectively are important for retrofitting legacy compressors and extending their useful lives, along with offering real steps forward in the design and manufacturing of future compression systems. It will continue to take sound planning and in-depth analysis to decide how much retrofitting and how much replacement is needed as compression grows in step with increased U.S. oil and gas production.
There are no clear quantitative formulas for determining the relative merits of retrofitting vs. replacement, said Linn.
“There are generally accepted design philosophies that determine the economics associated with increased horsepower, looping of existing pipelines or adding new grassroots pipelines,” he said.
Linn’s laundry list of considerations include: the gas velocity (30-60-feet/second) and pressure drop/mile (10 psi/mile) impact compression vs. pipe expansion decisions, along with operating/maintenance costs and permitting aspects.
Don’t all of the ongoing advances force operators to go for the cheapest option, which often is retrofitting? Not necessarily, according to Choquette.
He called the decision of extending the life of existing infrastructure vs. replacement a “complex matrix of multiple issues,” including environmental constraints, reliability, safety, expected life and economics.
“If the expected life of a unit (based on declining production reserves) is only five years, it is most likely that the operator would elect to extend the life of the unit even if that meant an increased risk to reliability; the economics would be difficult to justify a replacement unit,” he said.
Richard Nemec is P&GJ’s West Coast correspondent based in Los Angeles. He can be reached at: rnemec@ca.rr.com.
[inline:Nemec1.png]
[inline:Nemec2.png]
Source: EIA
[inline:Nemec3.jpg]
Related News
Related News
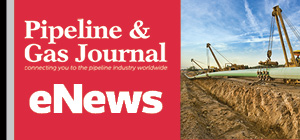
- Kinder Morgan Proposes 290-Mile Gas Pipeline Expansion Spanning Three States
- Enbridge Plans 86-Mile Pipeline Expansion, Bringing 850 Workers to Northern B.C.
- Intensity, Rainbow Energy to Build 344-Mile Gas Pipeline Across North Dakota
- Tallgrass to Build New Permian-to-Rockies Pipeline, Targets 2028 Startup with 2.4 Bcf Capacity
- TC Energy Approves $900 Million Northwoods Pipeline Expansion for U.S. Midwest
- A Systematic Approach To Ensuring Pipeline Integrity
- U.S. Pipeline Expansion to Add 99 Bcf/d, Mostly for LNG Export, Report Finds
- Enbridge Adds Turboexpanders at Pipeline Sites to Power Data Centers in Canada, Pennsylvania
- Great Basin Gas Expansion Draws Strong Shipper Demand in Northern Nevada
- Cheniere Seeks FERC Approval to Expand Sabine Pass LNG Facility
Comments