Pipeline Stations: From Pre-Commissioning to Start-Up

Commissioning involves the use of a disciplined, systematic methodology to convert the constructed compressor station into an integrated and operational unit within a gas transmission system.
This process should be implemented in a safe and efficient manner within a defined time-frame and budget. The successful operation of a compressor station strongly depends on the quality of three stages of the commissioning: pre-commissioning, core commissioning and start-up. New guidelines, latest lessons learned and modern practical notes must be addressed.
There is relatively little literature published on commissioning and start-up issues, and there have been significant shortages of good commissioning personnel worldwide, particularly for compressor stations.
In many cases, the trial-and-error approach during commissioning continues to be a common approach. However, suggestions made in this article should save valuable time during the process.
A large portion of a commissioning time is often spent on preparation, which includes development of a commissioning plan, preparation of commissioning documentations, development of operating procedures and handover procedures.
The implementation of commissioning is the most critical part of a compressor station project, which could include acceptance tests, cleaning activities, pre-commissioning, commissioning punch-listing, core commissioning activities and handover to the operation.
The last stage of a commissioning is the close-out, which consists of close-out reservations, complete as-commissioned document mark-ups, the assistance to continued operation, trouble-shooting and the close-down. Commissioning consists of three stages:
• Pre-commissioning, the entire process at the end of the construction and installation phase which prepares a compressor station to move to the core (main) commissioning phase.
• The core (main) commissioning stage, in which various systems of a station are placed into initial operation.
• The start-up takes place when the compressor station is brought into actual operation.
Based on various reports, the machinery commissioning stage is extremely critical for any compressor station project. In many cases, compressor packages cannot be properly operated at defined operation conditions because of commissioning problems. This article provides guidelines to help get machinery commissioned, started and operational.
In simple terms, the commissioning is a series of checks, tests and final activities that confirm a compressor station is fit for operation. The key is a standardized and systemized approach to commissioning.
Station Commissioning
Key topics related to the commissioning include:
• Flushing and cleaning.
• Systems assessment, along with calibrations and adjustments.
• Establishing procedures and protocols, particularly those related to start-up, normal shutdown and emergency shutdown.
• System configuration and instrument/control system checks, including verification of alarms and trips.
Opinions are divided over life expectancy of compressors and equipment within a compressor stations. However, there is no doubt that a proper commissioning is one of the most important factors for long-term trouble-free operation.
The maintenance service period for a clean service compressor could be many years if the design is commissioned properly. For instance, the maintenance service period for electric motor-driven centrifugal compressors in clean gas services could be four to six years. For gas turbine-driven compressors, the selected gas turbine usually defines the service period, which could be one or two years.
For a poorly commissioned industrial machinery package, the life expectancy could run less than a year. A large number of failures in compressor stations could be prevented by a better condition monitoring system. An important stage for any compressor station commissioning is to make the condition monitoring system fully operational.
An essential element in the commissioning stage is inspection and verification of spare parts. Based on experience, about 4-7% of all spare components could be flawed; parts replacement may be required during commissioning. In some rare cases, a minor repair could be needed on equipment, machinery or facilities during commissioning. All fabrication and repair procedures should be in-hand for this stage.
The most useful guidelines for compressor station commissioning involve practical issues related to design, material and fabrication defects; assembly and installation errors; and off-design operations or errors in operation.
This third potential problem, “error in operation,” is responsible for a large portion of failures at compressor stations. Unintended conditions, such as temperature, pressure, velocity and load, have caused many difficulties, even resulting in catastrophic failures.
Commissioning Staff
The commissioning team should include experts with different backgrounds, such as compressor experts, instrument engineers, process experts, control specialists, electrical engineers and operation specialists. A shortage of skilled workers is a sad reality in the commissioning sector. Actually, some compressor stations and compressor packages could be commissioned by unqualified personnel. This can result in short-term and long-term problems.
A commissioning staff should be familiar with all site-specific regulations, codes, specifications, procedures and work instructions. In other words, even the most experienced commissioning experts and engineers should read and understand documents, manuals and instructions.
Each commissioning engineer is actually the manager of a team of other engineers and technicians for an assigned commissioning task; the team is responsible for some packages and systems. It is difficult to give a general rule on the number of assigned systems to each commissioning team. Each commissioning engineer and his team normally can handle four to 10 systems or packages, depending on complexity, size and details of packages and systems.
Operation and maintenance staff presence is usually encouraged. This helps for a smooth handover to the operation team; it also ensures all lessons learned through commissioning are retained by the operations team. In addition to the operations team, the maintenance team should be made fully aware of the nature and details of compressor packages and compressor station facilities.
Commissioning Budget
As a rough estimate, commissioning for a compressor station can run 3.5-4.5% of the total capital cost. The commissioning budget typically includes 65-75% for manpower; contingency for engineering of commissioning modifications is a significant factor and could be as much as 15-30% of total commissioning budget.
On occasion, special instruments or rental equipment could be required for commissioning with significant costs incurred. Examples include instruments for site performance tests, equipment for cleaning services and special safety equipment. Additionally, photography plays an important part in commissioning.
Safety, Management
Commissioning representatives should attend various safety functions, such as Hazard and Operability (HAZOP) gatherings and the pre-start-up safety review (PSSR). PSSR is the last opportunity to catch and solve any safety issue before the start-up.
Another important safety requirement is that no equipment can be brought into service until its registration, documentations and safety checks have been completed.
There are always constrains of fast-track, sub-projects in commissioning of any compressor station with many changes usually required during commissioning. Any hidden defect or issue of the design, manufacturing, delivery and installation stages should be resolved or corrected in the commissioning phase.
Management of change (MOC) requires a systematic, sound procedure. Changes could present many safety and reliability issues to compressor packages and the compressor station if not managed properly using a robust MOC procedure.
Priority, Schedule
The end phase of the installation of a compressor station is a critical point and can present some scheduling challenges. In particular, site installation teams should invest time and re-arrange priorities in a way that assists commissioning activities.
During the final stage of compressor station installation, the commissioning manager should generally give the whole organization its directions. At this stage, the compressor station piping and instrumentation diagrams (P&IDs) can become the main reference for checking the installation and construction.
At the end of the installation and construction phase (85-90% completion), the site group should adopt a change from its installation philosophy to an approach needed for the commissioning.
The pre-commissioning activities, and subsequently commissioning activities, should be started in a timely manner. It should not be too early since having a commissioning team involved in construction could be problematic. All engineering and installation changes should be implemented before the start of pre-commissioning activities to avoid re-works.
Pre-commissioning checks should not be started early because changes and modifications can occur that require rechecking. On the other hand, the commissioning team should be involved in final completion activities, tests and last-stage inspections.
For the commissioning, a backward approach is usually preferred. In this way, the completion order could be:
• Power, light, utility, water, air and similar, including power generation and utility packages.
• Control systems.
• Gas discharge system (pipeline) or recycle loop for start-up and initial operation.
• Main units, including compressor packages.
• Gas suction system (pipeline).
Reprioritizing is the key for a successful and timely commissioning of a compressor station. One of the worse scenarios is at 90% of installation, the team becoming busy with systems, machineries, packages and units not within the required early systems to be handed over and commissioned. The correct prioritization can lay the foundation for success.
Commissioning engineers should be involved in installation and construction activities during the last 15-20% of the work, particularly observing leak and performance tests, and final completion activities. Otherwise, a considerable amount of time will be lost.
Priority should be given to units and items that add value and can be used for the commissioning of other systems or handed-over to operations. It is important that the construction team follow the commissioning plans and priorities.
Natural flow of commissioning work based on the backward concept should be established so any system being completed helps with an efficient start-up. Priority is a significant factor in any commissioning; it shows how the commissioning team plans to approach the commissioning and start-up. It should be clearly discussed and documented.
As an example, in many compressor stations the lighting system has been one of the latter systems delivered, probably because of low priority associated with it. This is not a good, safe practice. It is extremely important that all lighting systems be ready and operational as soon as possible. Such systems can offer great benefits and safety for entire commissioning and start-up activities. Working in the dark or using temporary lighting (with long-exposed cables) causes risks.
Great care is needed for commissioning time schedules. For commissioning and start-up schedules, all steps should be predicted and proper time should be allotted for each step.
Many completion and commissioning activities, such as last-minute corrections, modifications in facilities or packages, or changes in piping can alter machine alignment. The proper time should be allowed for the realignment of machineries – something often neglected.
Recommissioning activity can be another forgotten item in commissioning planning. If machinery, such as a compressor package, has been commissioned, this package should be recommissioned when the package is hooked up with all other systems.
Only after the integration can a compressor package be tested in a situation that resembles the actual working full-load condition. Proper time and resource allowances should be respected for recommissioning of different packages.
The time required for the oil flushing of machineries is usually underestimated. It often requires two or three times as long as common estimates. For special and complex lubrication oil systems, a complete and high-quality oil flushing could take three to 12 days.
Correct time frames should be set for cleaning checks, internal inspections and boroscoping. The machinery package that is handed over from construction to commissioning personnel should be properly inspected for cleanliness. Usually, facilities and machinery are not as clean as required during the handover.
Author: Amin Almasi is a lead mechanical engineer, specializing in rotating equipment and pipelines in Australia. He is a chartered professional engineer of Engineers Australia (MIEAust CPEng – Mechanical) and IMechE (CEng MIMechE) and holds master’s and bachelor’s degrees in mechanical engineering.
[inline:Stations_almasi.jpg]
Related News
Related News
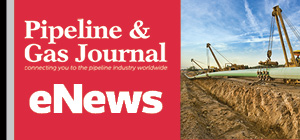
- 1,000-Mile Pipeline Exit Plan by Hope Gas Alarms West Virginia Producers
- Valero Plans to Shut California Refinery, Takes $1.1 Billion Hit
- Three Killed, Two Injured in Accident at LNG Construction Site in Texas
- Greenpeace Ordered to Pay $667 Million to Energy Transfer Over Dakota Access Pipeline Protests
- Boardwalk’s Texas Gas Launches Open Season for 2 Bcf/d Marcellus-to-Louisiana Pipeline Expansion
- New Alternatives for Noise Reduction in Gas Pipelines
- Construction Begins on Ghana's $12 Billion Petroleum Hub, But Not Without Doubts
- Missouri Loses Control Over 1.5 Million-Mile Gas Pipeline Network as Feds Step In
- Gazprom’s Grandeur Fades as Europe Moves Away from Russian Gas
- Greenpeace Ordered to Pay $667 Million to Energy Transfer Over Dakota Access Pipeline Protests
Comments