Clock Spring Casing Spacer Axial Shear Testing Results Released

Clock Spring Company, LP, a manufacturer of permanent and temporary composite pipeline and pipe work repair solutions, has released Axial Shear Testing Evaluates Casing Spacer Integrity and Performance, a white paper highlighting the results of Stress Engineering Services, Inc.’s full-scale upper-bound shear testing, which validates the stronger capacities of the company’s Casing Spacers product. Clock Spring contracted with Stress Engineering to perform the shear tests on its derivative casing spacers product, evaluating and comparing its performance against traditional casing centralizer and spacing solutions.
Contractors and operators install casing spacers and centralizers on carrier pipes to protect pipe integrity. They prevent contact between the carrier pipe and casing, minimizing coating damage and during construction and ensuring centralization when construction is complete. The casing acts as a storage vessel to limit the environmental impact in the unlikely event of a leak and can help protect pipelines against third party interference and damage.
The most commonly used casing spacers are bolt-on devices made of plastic or steel. Other common casing spacers are banded wood skids. Unfortunately, while the theory behind these solutions are sound, the bolts and bands often break or move when crews pull or push carrier pipe through casings. This results in coating damage and also can cause the installed pipe to rest in contact with the casing, which can more quickly lead to corrosion and carrier pipe weakness.
Stress Engineering Services performed shear tests to measure the likelihood of a casing spacer breaking or dislodging during the application of axial force to the pipe and the spacers. The tests compared the Clock Spring solution to traditional bolted solutions by applying concentric and eccentric shear to spacers installed on abrasion resistant outer coating coated steel and PVC pipes. The testing force required to initiate sliding of the Clock Spring solution was approximately 19 times greater than traditional casing spacers and five times harder to keep them moving.
“We are driving innovation to enhance safety and provide stewardship of customer assets and the environment,” said Matt Boucher, Clock Spring President and Chief Executive Officer. “These encouraging results about this easy to install product are greatly gratifying and further validation that we’re on the right track.”
Related News
Related News
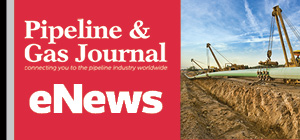
- Kinder Morgan Proposes 290-Mile Gas Pipeline Expansion Spanning Three States
- Enbridge Plans 86-Mile Pipeline Expansion, Bringing 850 Workers to Northern B.C.
- Intensity, Rainbow Energy to Build 344-Mile Gas Pipeline Across North Dakota
- Tallgrass to Build New Permian-to-Rockies Pipeline, Targets 2028 Startup with 2.4 Bcf Capacity
- TC Energy Approves $900 Million Northwoods Pipeline Expansion for U.S. Midwest
- A Systematic Approach To Ensuring Pipeline Integrity
- U.S. Pipeline Expansion to Add 99 Bcf/d, Mostly for LNG Export, Report Finds
- Enbridge Adds Turboexpanders at Pipeline Sites to Power Data Centers in Canada, Pennsylvania
- Great Basin Gas Expansion Draws Strong Shipper Demand in Northern Nevada
- Cheniere Seeks FERC Approval to Expand Sabine Pass LNG Facility
Comments