EACOP Unveils 897-Mile Heated Oil Pipeline with Advanced Environmental Safety Technology
(P&GJ) — The East Africa Crude Oil Pipeline (EACOP), set to be the world's longest heated crude oil pipeline at 1,443 km (roughly 897 miles), has disclosed details of its advanced safety features. Costing around $4 billion, the EACOP utilizes a network of electrical and fiber-optic cables for heat and real-time satellite surveillance to prevent leaks.
The heated crude oil pipeline will carry oil from Uganda to the Indian Ocean coast of Tanzania.
Due to pump its first crude oil in 2025, the EACOP integrates a sophisticated fiber-optic network for continuous online connectivity, ensuring real-time monitoring via satellite along its entire length. This technology enables rapid detection of pressure changes, minimizing environmental damage and commercial losses.
“With its extensive fiber-optic network allowing online connectivity, EACOP promises to be one of the world’s smartest and safest bulk pipelines with real-time monitoring along its entire length via satellite,” said Dozith Abeinomugisha, Director in-charge of Midstream developments at the Petroleum Authority of Uganda (PAU).
Safety staff will be able to detect any pressure change indicative of a leak, sabotage or pilfering within seconds and isolate the relevant section of pipe to keep environmental damage and commercial loss to a minimum.
Both the PAU and EACOP’s holding company will have real-time monitoring centers at their respective offices to receive immediate updates via satellite uplink. This means that monitoring is not dependent on local mobile phone or radio networks, guaranteeing greater reliability.
The remote data monitoring and transmission technology known SCADA (Supervisory Control and Data Acquisition) works even though the pipe will be buried between 1 and 3 meters underground, providing safety staff with a complete, live picture of the entire pipeline.
With EACOP planners aware of the importance of mitigating climate change, renewable energy will be used as much as possible for all pumping, heating, monitoring, and storing. The Ugandan section will be entirely carbon neutral with 80MW of solar and hydro providing all the power needed while work is continuing on the Tanzanian side to develop similar levels of renewable capacity.
The design and construction of EACOP, which began in 2018, has been one of the greatest challenges of African infrastructure engineering in recent history.
First, engineers had the challenge of how to pump crude oil that at surface temperature is not in liquid form and therefore resistant to flow, but more in a waxy state reminiscent of shoe polish.
Not uncommon in the oil sector, where so called `sweet’ crude of a fine quality such as Uganda’s solidifies after being pumped up from high-pressure, high-temperature reserves deep underground, the normal solution is to heat pumping infrastructure to ensure it remains liquid.
But the colossal 1,443-km (897-mile) length of the EACOP route, more than twice that of the current longest heated crude oil pipeline, which stretches 660 km (410 miles) across Gujarat state in India, posed an additional headache.
In order for flow to be maintained, the EACOP has to be kept at a temperature of at least 50°C (122 Fahrenheit). Testing showed that if the crude oil is flowing at high rates under high pressure initial heating at the pipe head to 80°C (176 Fahrenheit) will be enough to keep it moving, as the rate of cooling is so slow it remains above the 50 °C threshold along its entire 1,443 km.
But if flow rates and pressure come down it will cool more as it moves, threatening to solidify and block the flow. To get round this, two heating stations have been added to the design, capable of boosting the crude oil temperature back towards 80°C to ensure strong flow.
To keep it above 50°C heating cables will run the entire length of the pipe using a technology known as Long Line Heat Tracing (LLHT) which works on a similar principle as a kettle element, using resistance to generate heat when an electric current passes through a specially chosen high resistance filament.
With temperature so critical, EACOP’s conventional 24-inch-wide carbon steel pipe had to be carefully redesigned for heat and monitoring.
Uganda’s crude oil being sweet (with no corrosive impurities such as sulphur) means that the pipeline does not have to be lined on the inside as such high-grade crude oil has minimum corrosion effect on steel. So, for protection the pipe need only be lined on the outside.
In addition to a standard Fusion Bonded Epoxy (FBE) resin protective coating 400-600 microns thick on the outside, engineers have added a much thicker 70mm `smart’ layer of insulation made from polyurethane, with special channels down which electrical heating element LLHT cables and fiber-optic lines needed for SCADA will be fitted.
The entire pipe will then be covered with an outer, hard, protective coat of 5-7mm protective High-Density Polyethylene (HDPE), meaning EACOP will effectively have four layers: inner steel, epoxy resin, polyurethane and finally polyethylene.
Related News
Related News
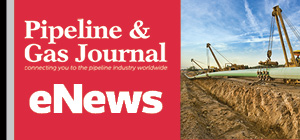
- 1,000-Mile Pipeline Exit Plan by Hope Gas Alarms West Virginia Producers
- Valero Plans to Shut California Refinery, Takes $1.1 Billion Hit
- Three Killed, Two Injured in Accident at LNG Construction Site in Texas
- Boardwalk’s Texas Gas Launches Open Season for 2 Bcf/d Marcellus-to-Louisiana Pipeline Expansion
- Traverse Pipeline Approved to Move 1.75 Bcf/d of Gas Along 160-Mile South Texas–Katy Route
- New Alternatives for Noise Reduction in Gas Pipelines
- Construction Begins on Ghana's $12 Billion Petroleum Hub, But Not Without Doubts
- DOE Considers Cutting Over $1.2 Billion in Carbon Capture Project Funding
- Valero Plans to Shut California Refinery, Takes $1.1 Billion Hit
- Newsom Seeks to Aid Struggling Refiners Following Valero’s California Exit
Comments