July 2010 Vol. 237 No. 7
Web Exclusive
Energy Demand Propels Custody Transfer Flow Measurement
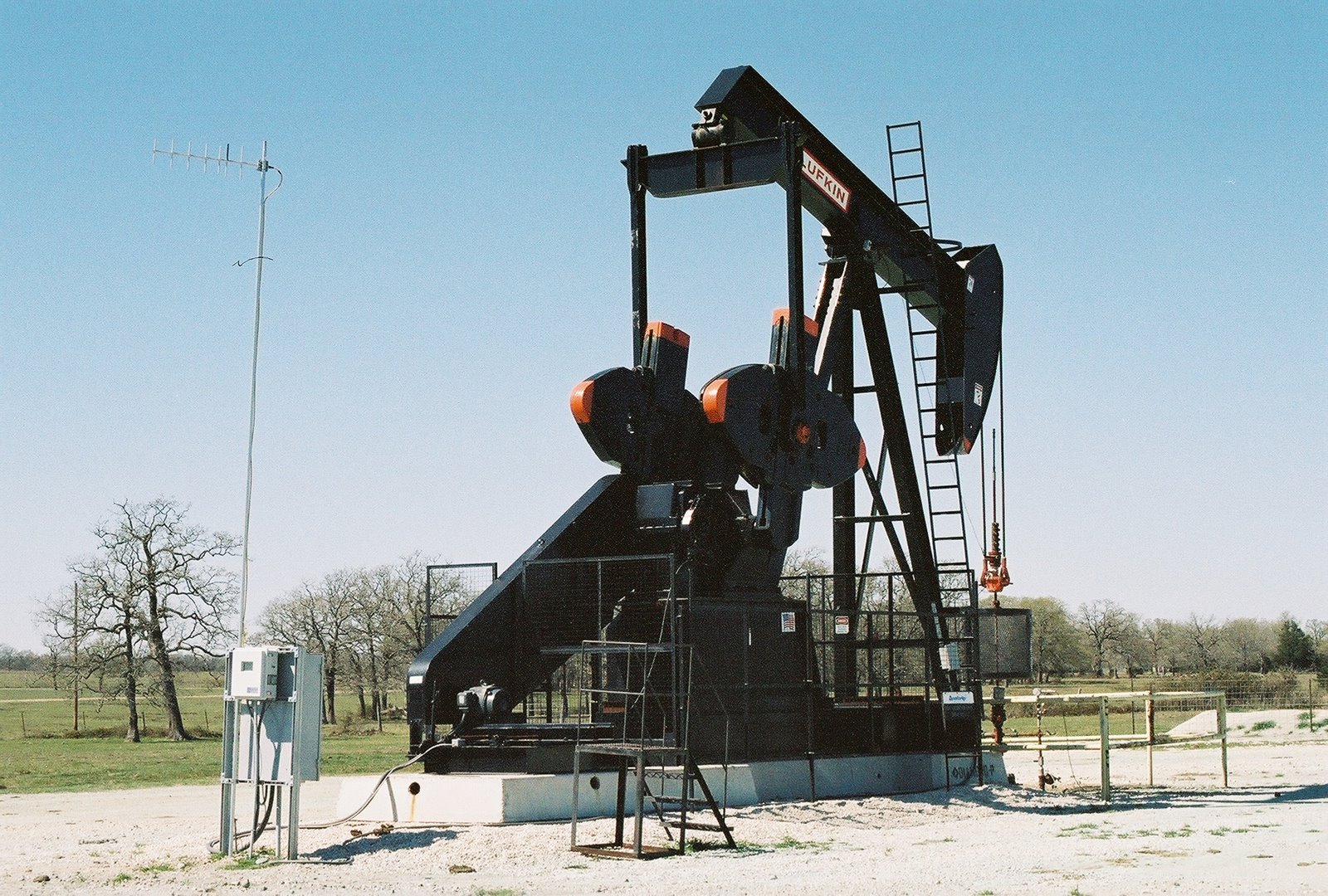
The world’s drive for energy has put oil and gas flow measurement in the spotlight. Rising oil prices, along with increasing prices for natural gas, have made it more important to oil and gas producers, distributors and end-users to have accurate and reliable measurements of flow. As many of the world’s economies recover from a severe recession, demands for energy are increasing.
Custody transfer is one of the most important applications for flow measurement. In custody transfer applications, the ownership of a fluid is transferred from one person or company to another. For these applications, it is important that both parties agree on the type of flowmeter being used and on the conditions under which the flowmeter is being used. Having this agreement reduces the likelihood that a dispute will arise at a later time over the amounts being measured.
The main types of flowmeters used for custody transfer of natural gas are differential pressure (DP), turbine and ultrasonic. DP and turbine flowmeters have been around for many years, while ultrasonic flowmeters are a more recent participant in this market. Both DP and turbine flowmeters have the advantage of having been studied for many years, so their performance in gas flow is well understood. These two flowmeter types were first to receive industry approvals for use in custody transfer applications. Industry approvals have played a key role in determining which types of flowmeters are used for custody transfer.
Differential Pressure Flowmeters
DP flowmeters are made up of a DP transmitter and a primary element. The primary element places a constriction in the line, resulting in reduced pressure downstream from the element. The DP transmitter detects the difference in upstream and downstream pressure and uses this value to compute the flowrate. There are many different types of primary elements, including: orifice plates, venturi tubes, pitot tubes, flow nozzles, wedge elements and laminar flow elements.
While each of these primary elements has its advantages and disadvantages, orifice plates are the most widely used type of primary element. And the standards that have been written for DP flowmeters have been written for DP flowmeters with orifice plates. Both the American Gas Association (AGA) and the American Petroleum Institute (API) have played an important role in laying out standards and criteria for the use of DP flowmeters for custody transfer applications. The AGA began in 1927 by publishing a preliminary report on the use of differential pressure flowmeters using orifice plates. In 1930, this report became AGA-1, the first industry standard published on the use of orifice meters in gas flow measurement. This was followed up in 1935 with the publication of AGA-2, which incorporated the results of additional tests.
Shipments of Primary Elements Worldwide for Flow by Type in 2009 (percents of dollars)
Source: Volume X: The World Market for Flowmeters, 2nd Edition (Flow Research)
In 1955, the AGA came out with AGA-3, which is the report number usually associated with orifice plate flowmeters. This third report–built on AGA-1 and AGA-2–also incorporated the results of tests to determine the effects of installation piping, among other factors. This report was issued again in revised form in 1992. The 1992 version of AGA-3 included the results of tests on the use of flow straighteners and upstream piping requirements. This is still the most current version of AGA-3, although Part Two of this report was reissued in 2000. Part Two deals specifically with specification and installation requirements for natural gas flow measurement with orifice meters.
One advantage of DP flowmeters is that they are the most studied and best understood type of flowmeter. They also have a very large installed base, having been used for many years for gas flow measurement. Because of the tendency of end-users to “replace like with like,” DP flowmeters will continue to be the most widely used for flow measurement. DP flowmeters have also been benefiting from the surge in oil and gas exploration and production. In some cases, DP flowmeters are the only flowmeter type that is suited to handle the pressures associated with deep sea operations.
One disadvantage of DP flowmeters is that they introduce a pressure drop into the flowmeter line. This is a necessary result of the constriction in the line that is required to make the DP flow measurement. Other disadvantages are associated with specific types of primary elements used. Orifice plate meters are subject to wear and they also can be knocked out of position by impurities in the flowstream. This affects the accuracy of the measurement.
One important development in the use of DP flowmeters for custody transfer applications has been the development of single and dual chamber orifice fittings. These fittings are specialized units with orifice plates mounted in a holder. Dual-chamber orifice fittings make it possible to change the orifice plate without shutting down the flow. Providers of single and dual-chamber orifice fittings include Emerson Daniel, Canalta Controls and The Measurement Company.
Turbine Flowmeters
Richard Woltman is generally credited with inventing the first turbine flowmeter in 1790. Woltman, a German engineer, studied the loss of energy in open canals. He published several studies on hydraulic engineering in the 1790s. A type of turbine meter is still named for him today. The Woltman flowmeter is used to measure water flow in large quantities.
Total Shipments of Turbine Flowmeters Worldwide: 2007 – 2012 (Millions of Dollars)
Source: Volume X: The World Market for Flowmeters, 2nd Edition (Flow Research)
The word “turbine” means “spinning thing,” which fits in well with the technology. Turbine flowmeters have a rotor with propeller-like blades that spins as water or some other fluid passes over it. The rotor spins in proportion to flowrate. The speed of the rotor is detected by a variety of methods, including mechanical shafts and electronic sensors.
Even though the origins of turbine flowmeters go back to 1790, it wasn’t until the 1940s that turbine meters began to be used for fuel measurement. Turbine meters were used on military planes to measure fuel in World War II. Soon afterward, companies in the petroleum industry began to use them to measure the flow of hydrocarbons.
The AGA published its first report on the use of turbine meters in 1981. This report was issued as AGA-7, Measurement of Fuel Gas by Turbine Meters. This report was revised and reissued in 1996. In 2006, the AGA issued the most recent version of AGA-7, Measurement of Natural Gas by Turbine Meters. This report addresses meter design requirements, installation specifications and meter maintenance checks. It also provides equations for measuring both volumetric flow and mass flow, using turbine meters.
While the first version of AGA-7 was issued more than 50 years after the initial release of AGA-3, this report was published well in advance of the later reports on ultrasonic flowmeters. As a result, both DP flowmeters using orifice plates and turbine flowmeters became entrenched in the market for gas flow measurement. This gave both types of flowmeters an advantage in installed base over new-technology flowmeters that were introduced at a later time.
Turbine flowmeters do best when measuring clean, steady, high-speed flow of low-viscosity fluids. They have a significant cost advantage over ultrasonic flowmeters, especially in the larger line sizes. The prices of turbine meters may also compare favorably to the prices of DP flowmeters, especially in cases where one turbine meter can replace several DP meters. Like DP flowmeters, turbine meters are well-understood and have been studied for many years.
One disadvantage of turbine flowmeters is that they have moving parts that are subject to wear. Suppliers have responded to this by introducing more durable materials of construction, including ceramic ball bearings. Turbine flowmeters also have a problem with fluids containing impurities. Despite these disadvantages, properly calibrated turbine flowmeters can equal the accuracy of multipath ultrasonic flowmeters used for custody transfer of natural gas.
Ultrasonic Flowmeters
Ultrasonic flowmeters were first introduced into industrial markets in Japan in 1963 by Tokyo Keiki. In the 1970s and 1980s, Panametrics (now owned by GE Sensing) and Controlotron (now owned by Siemens) were the technology leaders in developing ultrasonic flowmeters for liquid and gas flow measurement. Controlotron focused mainly on clamp-on technology, while Panametrics developed inline as well as clamp-on ultrasonic flowmeters. When the technology was first introduced, it was not well understood and some people got a negative impression of the technology. As ultrasonic technology became more widely used and better understood in the 1990s, it was able to overcome some of the earlier limitations.
Ultrasonic flowmeters have both a sender and a receiver. They send an ultrasonic signal across a pipe at an angle and then in the reverse direction. The ultrasonic signal travels faster with the flow than against the flow. The ultrasonic flowmeter measures how long it takes for the signal to travel across the pipe and how long it takes for the signal to cross the pipe in the opposite direction. The difference between these times is proportional to flowrate. This is the technology used by transit time ultrasonic flowmeters. Doppler flowmeters bounce the signal off of particles in the flowstream and detect a frequency shift in the reflected signal.
Total Shipments of Ultrasonic Flowmeters Worldwide: 2007 – 2012 (Millions of Dollars)
Source: Volume X: The World Market for Flowmeters, 2nd Edition (Flow Research)
One important event in ultrasonic flowmeter technology has been the development of multipath ultrasonic flowmeters. While ultrasonic flowmeters can often achieve good accuracy by using a single ultrasonic signal, they can achieve higher accuracies with multiple signals. Multipath ultrasonic flowmeters use three or more signals, or “paths,” to measure flow velocity in three or more locations. Only multipath flowmeters are sufficiently accurate to be used for custody transfer of natural gas.
Like DP and turbine meters, ultrasonic flowmeters have also been the subject of industry approvals, but this process got started quite a bit later. In the mid-1990s, an organization called Groupe Europeen de Recherches Gaziers (GERG) published a monograph on the use of ultrasonic flowmeters for gas flow measurement. This monograph specified criteria for using ultrasonic flowmeters to measure natural gas flow and it laid the groundwork for what was to become AGA-9. The publication of the GERG monograph let to a substantial increase in the use of ultrasonic flowmeters in Europe from 1996-1998.
In 1998, the AGA published its Report AGA-9, which detailed the use of multipath ultrasonic flowmeters for custody transfer of natural gas. Even though it took time for AGA-9 to be implemented, the publication of AGA-9 has had a major impact on the industry. For the first time, end-users had a choice between new-technology and traditional flowmeters to measure gas flow. Many have responded by choosing to use ultrasonic flowmeters, especially for new projects.
Ultrasonic flowmeters have some important advantages over DP and turbine meters. They are largely nonintrusive, create minimal pressure drop and do not have moving parts. They do very well in large line sizes and can be used to measure both gas and liquid flows. They are also beginning to be used to measure steam flow. Ultrasonic flowmeters are highly reliable over time and require a minimum amount of maintenance.
One issue that remains unresolved with ultrasonic flowmeters used for custody transfer of natural gas is how often they need to be recalibrated. Multipath ultrasonic flowmeters are typically sent to an outside calibration facility after they are purchased and before being installed. After that, they need to be re-calibrated periodically to ensure that they are measuring flow accurately. Usually this requires pulling the flowmeter out of service and shipping it to a calibration facility, which might be located in another country or region. This process is expensive and time-consuming and requires having a back-up flowmeter or doing without the flowmeter for several weeks or even longer.
There is currently no generally accepted industry standard about how often ultrasonic flowmeters for custody transfer applications need to be recalibrated. As a result, it is typically up to the company that owns the ultrasonic flowmeter to decide on frequency of calibration. This may be done in consultation with the flowmeter supplier. Discussions with natural gas companies in the Middle East in 2009 revealed that most of these companies had decided on a frequency of between three and seven years for recalibration. This decision is more difficult for companies in the Middle East since there is no flowmeter calibration facility in that region. As a result, most companies in the Middle East send their flowmeters to Europe, the United States, or Canada to be recalibrated.
However the issue of calibration is resolved, there has been a great deal of product development centered around multipath ultrasonic flowmeters in the past five years. Companies in this market include Elster-Instromet, Emerson Daniel, Sick Maihak, FMC Technologies and now KROHNE. Most multipath ultrasonic flowmeters for natural gas flow measurement have four, five, or six paths. However, Caldon (now part of Cameron) has an eight-path multipath ultrasonic flowmeter for measuring petroleum liquids. And Faure Herman (now part of IDEX Corporation) has developed an 18-path ultrasonic flowmeter, also for measuring the flow of hydrocarbon liquids.
Enough Business For All
While DP, turbine and ultrasonic flowmeters are continuing to compete for the loyalties of end-users, there is enough business for all three technologies. Flow measurement of oil and gas is an ever-expanding pie, due to increasing energy demands worldwide. DP and turbine flowmeters have an advantage when it comes to replacement business for existing flowmeters, while ultrasonic flowmeters have the edge for new projects. While ultrasonic flowmeters have the advantage in the long term, the substantial installed base will keep DP and turbine flowmeters competitive for the foreseeable future.
The author
Jesse Yoder, Ph.D., is a frequent contributor to P&GJ. He is president of Flow Research, Inc. in Wakefield, MA. He has 23 years of experience as an analyst and writer in process control. He has written more than 110 market research studies in industrial automation and process control, and has published more than 100 journal articles on instrumentation topics. He is working on three market studies to be published by Flow Research in the next several months: “Volume X: The World Market for Flowmeters, 3rd Edition,” The World Market for Gas Flow Measurement, 2nd Edition,” and “The World Market for Turbine Flowmeters, 2nd Edition.” Ph: 781-245-3200, jesse@flowresearch.com, www.flowresearch.com.
Comments