September 2011, Vol. 238 No. 9
What's New
How to Use Ethernet to Improve Your Midstream Oil and Gas Communications
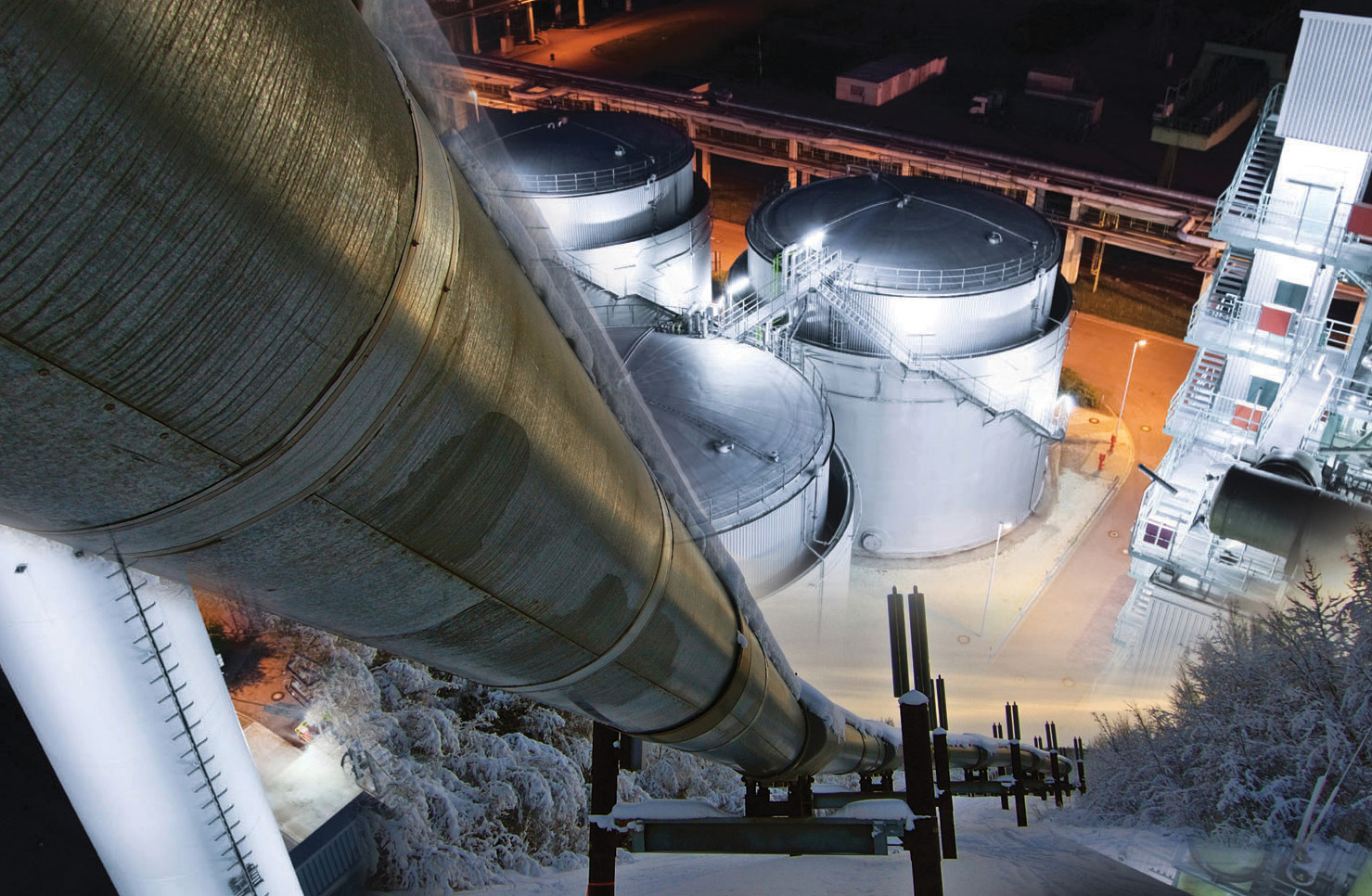
Midstream oil and gas markets typically use three types of networks. The first type is for control and for safety shutdown systems, typically starting at the controller level and extending down to I/O and instruments. The second type is for Supervisory Control and Data Acquisition (SCADA) systems, starting at the controller level and extending up to MES and to ERP systems. The third type of network is intranets for internal communications such as VoIP, dedicated email servers and file transfers. On any of those networks, switching to Ethernet may decrease costs and improve connectivity. This paper outlines the scenarios where Ethernet can deliver the most value.
Download this article as a PDF.
In modern communication systems, Ethernet is used in all three network types to enable easier and tighter integration between all levels of the corporation. Physically connected and wireless Ethernet networks provide a competitive advantage by providing a low cost and widely supported infrastructure across the enterprise.
Midstream Oil and Gas Markets Communication Requirements
The midstream sector is primarily involved with the transportation of oil and natural gas from extraction sites to refineries. In an integrated oil major, the midstream sector is often included as an extension of either the upstream or downstream division of the organization. In other cases, a separate entity provides midstream transport and storage.
The midstream oil and gas sector requires widely distributed networks as distances can range from many acres for an intermediate or end terminal tank farm, to entire continents for a pipeline system. In many cases, installing and maintaining private or proprietary networks over these distances doesn’t make economic sense, particularly for pipelines.
Therefore, storage and transport facilities often look to piggy back onto existing infrastructure such as cellular and the cloud, and also the Ethernet protocols on which these communications systems are largely based. The Internet and its associated cloud are almost exclusively based on Ethernet, causing tremendous growth and driving standardization.
Ethernet and the OSI Model
An example of this standardization can be seen in Figure 1, “Ethernet and the OSI Model”. Most every version and variant of Ethernet is commonly represented in the lower layers 1 to 4. The layers above 4 are determined by the application for which the Ethernet infrastructure is being used.
Note that the User Layer shown in Figure 1 is not part of the OSI 7-Layer model, but is important to industrial applications because this is where all the different fieldbus and industrial protocols reside. Modbus is the exception to this rule as it is a Layer 7 protocol.
As shown in Layer 1, virtually any physical media can be used for Ethernet communications including but not limited to copper, fiber or wireless. No matter what media is chosen, the Layer 3 IP functions manage connectivity and acts as a universal service provision interface.
Both the International Telecommunications Union’s Standardization Sector and the IEC have accepted IP as a network and access protocol. This has led to tremendous growth of IP-based solutions for midstream oil and gas operational applications like control, SCADA and Intranets.
In the area of control, fieldbus protocols such as EtherNet/IP, Foundation Fieldbus and Profibus are often used. As the name implies, EtherNet/IP is Ethernet-based, and most other fieldbus protocols including Foundation Fieldbus and Profibus are moving towards Ethernet.
In the past, many of the fieldbus protocols use twisted-pair serial communications as represented by the box in the lower right of Layer 1. By transporting the same message in an IP packet, the functionality of the particular fieldbus network can be ported over to Ethernet. This yields the ability to utilize the Internet as part of the network, and to utilize other open system advantages (Table 1).
In midstream oil and gas control, SCADA and Intranet applications—it’s necessary for signals to be transmitted to the IP address or port used to connect to the larger network, and this is where the choice of physical media becomes important. The choice of media is dependent on a variety of factors including but not limited to distance, required bandwidth, environmental conditions, space constraints and the amount of electromagnetic interference (EMI).
Copper has been the traditional physical connection medium. However, as data rates increase, copper’s limitations with respect to the distances that it can reliably transmit signals in the typical electrically noisy industrial environment become a detrimental factor. As a result, there continues to be a move away from copper to fiber and now to wireless.
Fiber supports faster communication speeds, has more bandwidth, can be used for longer distances and is virtually immune to lightning and other electrical disturbances. Fiber is therefore commonly used in Ethernet backbones and other high traffic and/or long distance applications.
Like copper, wireless has distance and interference limitations, but it can provide substantial savings over physical media wiring in many applications (see Sidebar: Wireless Makes Its Way). Wireless can often be deployed in a mesh topology to provide increased reliability. With a mesh topology, wireless signals can automatically seek the best communications path among nodes on a dynamic basis. Today’s industrial wireless networks can also be deployed in topologies that support redundancy.
Because the distance that a wireless signal is able to travel is approximately linear to the frequency of the signal, lower wireless frequencies like 900MHz can travel approximately 3 times further than 2.4 GHz radios and therefore are generally more reliable in distributed installations such as tank farms. For pipeline applications, a combination of wireless and physical media is often employed.
Wireless Makes Its Way
Today, nearly every automation system component can be purchased with an Ethernet port. For many of these components, Ethernet communications can be wireless, generally for about half the cost of a wired solution.
Many automation systems are hard-wired for a reason. Wired systems are more easily isolated from the balance of a network, making it is easier to keep other applications from spuriously accessing part of network bandwidth needed for reliable operation. Therefore, in most cases, wireless components are best suited for meeting the needs of supervisory tasks that are able to tolerate variable access times.
Wireless is inherently a shared medium, meaning every device connected to a single access point must share the bandwidth. Although called a shortcoming for wireless by some, it’s important to realize that most fieldbus networks used in process control, even those considered the most deterministic, are also based on a shared-medium concept. Having a shared medium can cause some latency and data collision issues, but with wireless access point switching rates as fast as 20 ms, these issues can be addressed with a properly designed wireless network.
Although often lower in overall cost, wireless can only be driven down to field components so far before the cost of equipping the device with wireless capability becomes more expensive than the cost of the device itself. For example, it’s more cost effective to hardwire a solenoid valve and other nearby components to a local wireless Ethernet I/O block than to add wireless functionality to the valve.
On the other hand, a relatively complex device such as a multi-variable transmitter could very well benefit from a direct wireless connection to the controller.
A key component to a successful wireless system is the supply of low cost and reliable power to the field-mounted components. Fortunately, because wireless systems are designed to be low power consumers, it is often possible to use energy harvesting systems as a way to provide that power.
Industrial wireless sensor networks predominantly use IEEE 802.15.4 based radios and over 85 million IEEE 802.15.4 ICs have been shipped. Driving factors include the uptake of RF4CE in consumer electronics, displacing IR control; the growth of ZigBee in smart metering/smart grid and factory automation applications; and the growing use of 802.15.4 ICs with proprietary software for a wide range of applications ranging from commercial building automation to agricultural monitoring.
In 2009, proprietary solutions accounted for over 85% of the low-power RF market, predominantly for application areas such as automotive devices and wireless PC peripherals. Proprietary low-power wireless IC shipments are forecast to increase at a compound annual growth rate of over 20% for the period 2009-2015; yet by 2015, they are projected to account for less than half of low-power RF IC shipments as momentum grows behind key standardized solutions.
To put this in perspective, a forthcoming IMS Research report has indicated that the world shipments of industrial products that are wireless-enabled are set to grow from an estimated 1.2 million in 2009 to over 3 million in 2015, equating to a compound annual growth rate of 18%.
Ethernet for Control and Safety Shutdown Systems
As described above, Ethernet has become the de facto protocol for connecting not only business enterprises, but also for control, safety shutdown and SCADA systems—particularly in the midstream oil and gas sector.
A typical tank farm requires control and monitoring of tank levels, of flows to and from tanks, and in some cases temperature. Analytical sensors are sometimes used to monitor product quality, and to detect the presence of hazardous gasses.
In terms of flow control, pumps and their associated motors and motor drives are generally used to move oil, and oil flow is monitored by flow transmitters and switches. Modulating control valves are often used to increase or decrease flow. Level can be monitored by either point level switches or continuous level transmitters.
For oil and gas pipelines, control and monitoring of flow, pressure and sometimes temperature are required. To control flow, compressors and pumps are used to move product, and flow or pressure transmitters perform flow monitoring. Compressors often have their own control systems.
Almost all of the instruments, sensors, valves and motor drives typically used in tank farms and pipelines are available with Ethernet connectivity. These components are often connected back to a local centralized controller via some variant of Ethernet, either directly or though input and output modules.
When these I/O modules are mounted remotely, they almost always use Ethernet to communicate with the controller. These Ethernet connections can be hard-wired or wireless, and it often makes sense to connect hard-to-access components such as level transmitters wirelessly.
Using Ethernet for these connections rather than simple discrete and 4-20ma analog wiring allows components to transmit a wealth of information to the central controller. This information can be used to perform diagnostics and predict component failures. Ethernet connectivity also allows a controller to perform basic calibration functions for many components.
Many tank farms and virtually all pipelines and their associated compressor stations are unmanned. The diagnostic, calibration and other functions enabled by Ethernet connectivity between the components and the controllers enable remote control and monitoring.
Safety systems share many of the characteristics of control systems, but components, controllers and networks have to be purchased, installed and monitored in compliance with safety regulations. For example, controllers have to be safety-rated, and components such as flow transmitters often require redundant backup. Fail-safe operation is a requirement with failure to a known safe state in case of controller or component failure, or in case of a power outage.
Similarly, the networks used in safety systems have to be safety-rated, a requirement that can be met with a properly designed Ethernet network. The entire safety system from the controllers to the components to the networks has to be certified to the applicable Safety Integrity Level (SIL).
With either a control or a safety system, the link from the tank farm or the pipeline to a wider area SCADA system will typically be through either the controller or through a local Human Machine Interface (HMI),
generally via a gateway. The connection from the gateway to the SCADA system will almost always be Ethernet-based as this allows communication over widely dispersed geographical areas using standard components and often via existing communications infrastructure.
Control and safety systems for midstream oil and gas applications are process driven in that they continuously scan for I/O changes in the process. On the other hand, SCADA systems are event driven in that updates are only sent to the control system in the event of a change in process. Consequently the bandwidth requirements for SCADA are less than those for a control or a safety system, and the connection itself does not need to have 100% availability.
Ethernet for SCADA Systems
Performance improvements have made Ethernet robust and reliable enough for just about any industrial application. They are largely responsible for driving Ethernet technology to its present role as a universal network solution. For many process industries including midstream oil and gas, Ethernet is the de facto solution of choice as it provides seamless interoperability and system integration.
The flexibility of Ethernet as implemented via fiber, copper, and wireless makes it an obvious choice for pipelines where high-maintenance buried cable can be replaced by wireless connections where and when necessary.
For most midstream SCADA applications—the lack of speed, limited bandwidth and occasional downtime of wireless are acceptable as process changes such as tank level or pipeline pressure aren’t inherently fast acting. SCADA-specific protocols running on top of Layers 1-4 can provide predefined connection networks among various tank farms and compressor stations.
In a typical SCADA system architecture, each tank farm or compressor station controller is referred to as a Remote Terminal Unit (RTU). These RTUs are linked to one or more centralized control and monitoring centers via Ethernet and various protocols running over IP. The entire communication system is designed to handle data flow interruptions and re-coordinate databases among the RTUs and the centralized control and monitoring centers if communications are interrupted.
Traditionally, RTUs with serial interfaces didn’t need more than 10 kbps of bandwidth. Despite increases in the amount of diagnostic and other data communicated among RTUs and control and monitoring centers, bandwidth requirements have not increased substantially due to traffic management techniques such as updating on change of state only. With its packet-based structure, IP efficiently easily supports remote monitoring and configuration of RTUs at these limited data rates.
But for hot stand-by, shared operation and back-up functionality, SCADA systems need an IP-bandwidth of at least E1 capacity (2048kpbs), easily provided by most modern Ethernet systems operating in the 100 Megabaud or higher range. As a result, most midstream oil and gas SCADA applications use less than 1% of available Ethernet bandwidth, making determinism no longer the critical factor it was in the past.
The Ethernet infrastructure is developing rapidly in the process control industry. Thanks to advancements in the technology, most recently in the wireless arena, Ethernet is becoming all-pervasive in not only SCADA systems, but also in the Intranets that connect to these SCADA systems.
Ethernet for Intranets
An Intranet is a private computer network that securely shares part of an organization’s information or operations with its employees. In midstream oil and gas and other markets, corporate networks or Intranets typically use Ethernet as their underlying communications network.
The same concepts and technologies of the Internet such as clients and servers running on the IP suite are used to build an Intranet. Ethernet is a family of frame-based computer networking technologies for local area networks (LANs). As shown in Figure 1, Ethernet defines a number of wiring and signaling standards for the Physical through Transport layers to define a common means of network access as well as a common addressing format.
The bottom four layers of the OSI model are common for all forms of IP-based communications, making integration and data transfer between the corporate LAN/Intranet and the SCADA system relatively straight forward. Of course, ease of integration comes with the price of potential security risks if appropriate precautions are not taken (see Sidebar: Security Considerations for Industrial Ethernet).
ISA-95 has developed a model and series of standards to define how data moves between various levels of the enterprise and to provide better overall integration of not just the network infrastructure, but also of the data itself. Figure 2 summarizes the 4 levels of data transfer in a typical enterprise. Note that Level 0 is the process itself and therefore is not part of the data transfer definitions.
For midstream oil and gas applications, Levels 1 and 2 are where the control and safety systems reside, and the SCADA system is part of Level 2 and/or 3.
Other organizations such as MIMOSA have developed similar diagrams, often referred to as a Purdue Model of the enterprise. These models separate the enterprise based on its functionality or purpose rather than the hardware on which it is based. With the move to tighter integration of these systems there is significant effort underway to make the data itself as easily integrated as the hardware.
Intranets, SCADA, control and safety networks use much of the same Ethernet infrastructure. This makes it much easier to provide data communications across the gaps between the levels in Figure 2. These gaps also represent the areas in which firewalls and other forms of security are included in the network to protect and prevent a security breach from adversely affecting the operation of either the business or control systems.
Security Considerations for Industrial Ethernet
In 2009, a control system cyber security expert advised the U.S. Senate Committee on Commerce, Science, and Transportation that “current industrial control system cyber security is where mainstream IT security was fifteen years ago—it is in the formative stage and needs support to leapfrog the previous IT learning curve.”
Cyber security must address deliberate attacks such as internal breaches, industrial espionage and terrorist strikes—as well as inadvertent compromises of the information infrastructure due to user errors, equipment failures and natural disasters.
Fortunately, many of the same tools and technologies used to provide security in the office environment such as firewalls, Intrusion Detection Systems, VLANS and VPNs can also be deployed in control systems, thus making it possible to quickly gain ground and catch up on the IT learning curve.
One of the most effective cyber attacks to date on control systems was Stuxnet. Before discovery, Stuxnet was active for at least one month and probably six months. It infected at least 100,000 computers, and possibly many times more connected and associated systems.
Stuxnet was particularly serious for two reasons. First, it took advantage of vulnerabilities that were unknown and un-patchable in the Windows operating system. Second, it was one of the first worms to target an industrial automation system, as opposed to the more common tactic of attacking office-based computing systems. This indicates that attackers are now aware and capable of exploiting vulnerabilities in industrial automation systems.
One of the major thrusts of the midstream oil and gas industry is integration from storage and transport facilities to corporate offices. These integrated systems will rely on real-time two-way open communications, making integration viable but also creating cyber vulnerabilities.
Conclusion
Midstream oil and gas tank farms and pipelines will continue to be a critical part of the energy industry infrastructure. To perform integration within and among the Intranets, SCADA systems, control systems and safety systems in these facilities, control centers and corporate offices—companies are looking to use existing infrastructure and the Ethernet protocols on which this infrastructure is based.
The flexibility of Ethernet and the tremendous success of the Internet have made IP the universal service provision interface. Combining this with the range of media support by Ethernet—namely fiber, copper and
Tank farms wireless—makes Ethernet an obvious choice for midstream oil and gas applications, which tend to require a wide range of form factors dispersed over both small and large footprints. Ethernet flexibility and scalability has also lead to a tremendous growth of IP-based solutions for operational applications like network control and SCADA.
As data rates increase, copper has limitations on the distances it can reliably transmit signals in the typical electrically noisy industrial environment. As a result, there continues to be a move from copper to fiber and now to wireless. Most midstream control, safety and SCADA applications use less than 1% of available bandwidth of a modern Ethernet network, making Ethernet’s theoretical lack of determinism a non-issue.
Open systems have many benefits over legacy proprietary architectures. However, openness comes at a price, specifically the risk of security breaches.
Ethernet defines how to move bits and bytes from one system to another, but does not establish data integration model requirements. Fortunately, models and standards that separate the enterprise based on its functionality or purpose rather than the underlying hardware are in development and will show how various levels of the enterprise can be integrated via consistent data models.
Midstream oil and gas applications require a high degree of flexibility as determined by both the geography and by the specific industrial environment. These markets are driven by the movement of data between the business Intranet and the field operating units. Ethernet, with its high degree of flexibility and use of common components, is a natural fit and lowest cost solution to integrate data in these applications.
References:
1. Midstream Oil Industry Oilfield Directory http://www.oilfielddirectory.com/article/detail.php?id=106
2. “SCADA over IP-based LAN-WAN Connections” http://library.abb.com/global/scot/scot221.nsf/veritydisplay/51912692be234e5ec1256d11002c73e9/$File/802.pdf
3. “Achieving Next-Generation Connectivity” http://www.belden.com/pdfs/Techpprs/Belden_Wired-Wireless_WP.pdf
4. “Energy Harvesting Forum” http://imsresearch.com/news-events/press-template.php?pr_id=1083)
5. Get Smart About Electrical Grid Cyber Security WP: http://www.belden.com/pdfs/techpprs/PTD_Cyber_SecurityWP.pdf
Technical Support: 1.717.217.2270
www.belden.com/hirschmann
©Copyright 2011, Belden, Inc. WPOG-Ethernet 082011
Comments