April 2012, Vol. 239 No. 4
Features
Effective Integrity Management With Advanced Communication Technologies
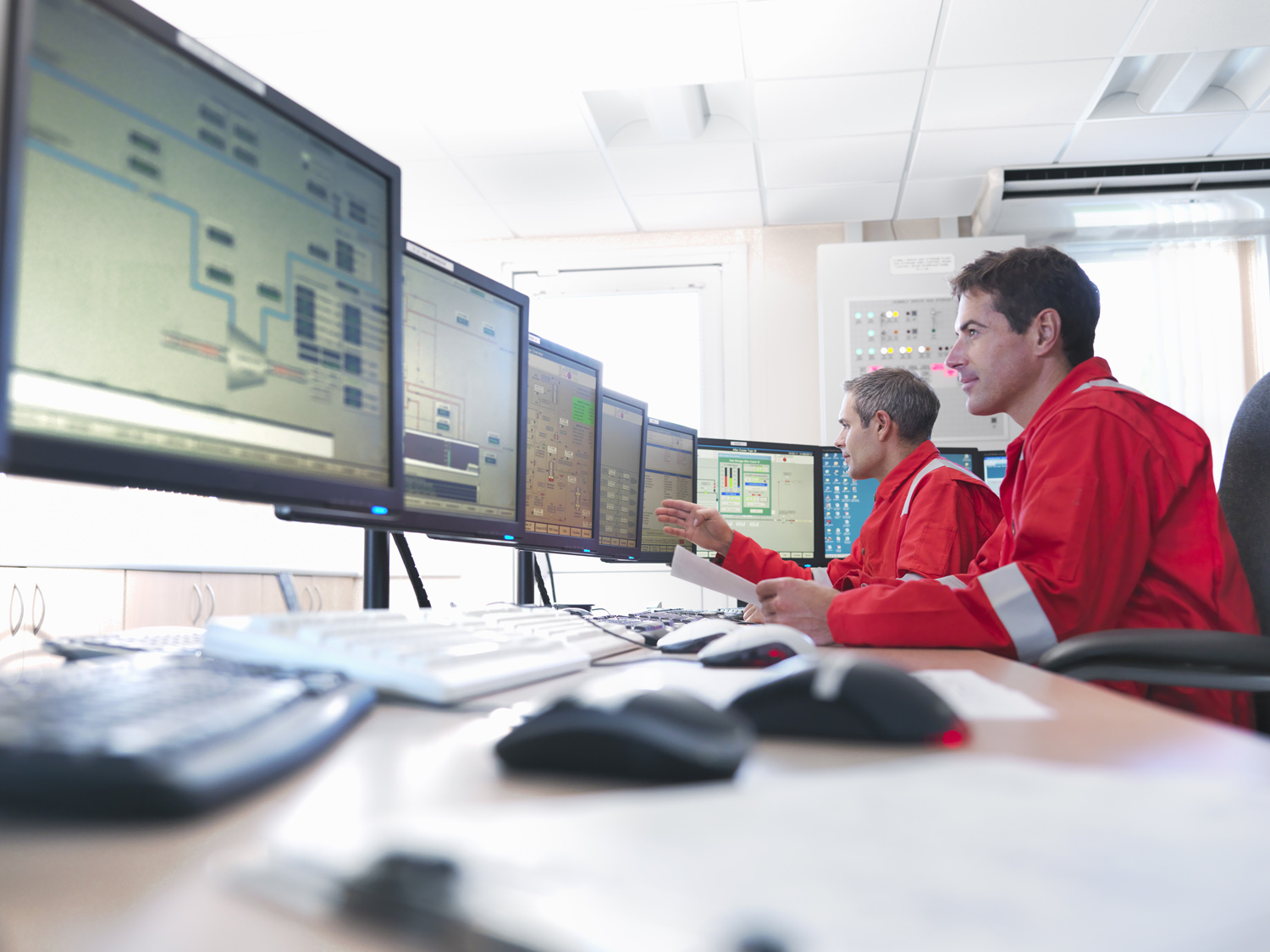
More than 2 million miles of natural gas pipeline in the United States distribute natural gas to customers every day. Considering the amount of natural gas flowing across the country at any given time, gas providers have an exceedingly good safety record. While serious incidents are uncommon, all it takes is one major event like the San Bruno explosion in September 2010 to focus national attention on the potential risk of natural gas and the need for continued diligence on the part of the gas industry.
That said, safety has always been a top concern for all gas utilities as they strive to make their systems 100% safe.
The natural gas industry has long contended with the integrity of their distribution systems. With the advent of distributing natural gas to consumers in the late 1800s, events associated with gas leaks started attracting crowds and making headlines. One of the first recorded events happened one month after natural gas first flowed into Columbus, OH on January 24, 1890 when two homes exploded. It was later discovered that “a joint on the gas main had not been properly sealed.” (source: Tebben, Gerald, The Columbus Dispatch, http://www.dispatch.com/content/stories/local/2012/01/24/natural-gas-explosion-kills-four-injures-32.html, -accessed Feb. 21, 2012)
There have been a number of events since the 1890 Columbus incident, but statistically the annual numbers have dropped significantly as gas utilities have adopted proactive procedures for the safe and reliable delivery of natural gas.
Safety Technologies – They’ve Come A Long Way
Canaries were one of the first solutions to be used for detecting harmful gases. Deep in coal mines, miners would bring canaries with them as an early warning signal against harmful gases. If methane gases were present in the tunnels, the canaries would stop singing, get sick and possibly die. This signal would give the miners the chance to vacate the tunnels before succumbing themselves. Fortunately for canaries, detection technologies have come a long way.
To monitor the integrity of natural gas pipelines, various technologies address different physical aspects of the lines to avoid dangerous events caused by line leaks, line degradation or a sudden change in pressure or temperature. Measuring methane leaks is performed using a variety of sensor technologies, including electrochemical, infrared, semiconductor, holographic and ultrasonic detectors. Pipe corrosion is monitored with cathodic protection and voltage surveys, whereas pressure and temperature are measured and recorded through various devices including volume correctors.
These technologies all perform vital sensor functions by collecting data on key performance indicators along a distribution pipeline, enabling utilities to monitor, inspect and mitigate potential issues. Maintaining pipeline integrity helps to minimize the possibility of events associated with a change or imbalance in natural gas or pipeline properties.
Gas AMI – A Second Layer Of Safety
While SCADA systems are typically relied on for communicating sensor data back to the utility, legacy modem technologies or field crews to collect data are also employed to monitor pipeline conditions. Advanced metering infrastructure (AMI) communication networks for gas utilities can augment these systems by adding a layer of smart monitoring capability or serve as a standalone monitoring solution for enhanced safety and reliability. With a gas AMI solution, collecting field data for proactive monitoring of pipeline conditions can become a daily routine for utilities.
Gas AMI includes advanced telemetry technologies that integrate with different pipeline sensors. The telemetry devices leverage gas AMI communications infrastructure to backhaul critical distribution sensor data back to the utility. This solution allows utilities to get near real-time notification of leak, pressure and potential corrosion conditions and monitor their system’s status on any given day.
“Itron is very excited about the ability of new AMI technologies to integrate with different sensor devices and present timely and relevant data so that utilities can increase the reliability of their distribution systems,” says Carl Porter, vice president of gas sales and marketing for Itron.
Augmenting a SCADA system or using a standalone solution, utilities can proactively evaluate and mitigate any deficient conditions with timely maintenance to avoid a possible event. When it comes to managing pipeline integrity, gas AMI technologies provide key performance data that could be the difference between reliable natural gas delivery and a headline.
Methane Detection
Gas leaks are often the result of many different issues, often times outside the control of the utility. Gas leaks can be difficult to pinpoint and mitigate. Telemetry devices utilizing a gas AMI network can collect measurements from methane gas sensors and transmit readings indicating the presence of methane. If a pre-set threshold for methane concentrations is passed, an alarm communicates the sensor reading and location to the utility. At this point, the sensor begins sampling the surrounding air every 15 minutes. If the second threshold for methane concentrations is breached, another alarm is sent, indicating a potentially critical condition. Depending on protocols, a field investigation would be triggered to isolate the leak and the appropriate actions can be taken. The tiered alarm system enables utilities to actively monitor methane concentrations to determine if an actual leak exists or if a reading was an anomaly and false alarm.
Cathodic Protection
Natural gas pipelines are buried in environments that naturally promote corrosion. Cathodic protection technologies help prevent and detect pipeline corrosion with surveys performed biannually or annually. This approach requires highly trained field staff and collects one of two data points per year. Rather than performing two surveys, gas AMI telemetry devices proactively monitor for pipeline corrosion by collecting daily voltage readings without the need to roll a truck. If a section of pipeline is unknowingly nicked during excavation, the weakened pipe can be subjected to corrosive effects. Daily surveys could detect the diminished integrity of the pipe earlier than an annual or biannual survey, providing more opportunity for corrective action.
Pressure
The fact that natural gas pipelines are pressurized to optimize distribution also creates the need to assure proper pressure is maintained along the lines of pipe. A drop in pressure could result in lost customers, expensive relights and safety concerns, while an increase in pressure could adversely impact field assets and/or meter reading accuracy. By using an electronic volume corrector or pressure recorder and a telemetry device to collect hourly pressure data, gas utilities are offered another level of pressure monitoring beyond their SCADA system. This second monitoring layer enhances safety by triggering alerts if pressure moves below or above preset thresholds, thus avoiding potentially adverse pressure-related events.
Gas AMI – Enhanced Safety At The Premise
A part of gas AMI solutions, advanced ERT® modules are capable of hourly meter reads and two-way communications to the gas meter, offering increased capabilities that promote safety and reliability to the premise.
Remote Shut-off at the Premise
A gas utility’s safety concerns also extend into the customers premise as they address leaks within the home. Previously, if a gas leak was suspected and communicated to the utility, a truck was sent out to investigate. This could mean a potentially dangerous situation for crews going into a home filled with natural gas. Utilities could avoid such scenarios by remotely shutting off gas service to the home using a remote disconnect valve enabled by the two-way communications of a gas AMI solution. Or using a drive-by system, a truck sent to the premise could trigger the disconnect valve without going into the home. The ability to remotely shut off gas flow into a home can enhance field crew and customer safety.
Event Investigations
System integrity isn’t only focused on pipeline safety, but also the customer’s premise. Up until now, without access to granular meter data, any gas-related event at a premise was routinely considered a gas leak, often with an assumed liability by the utility. With datalogging gas ERT modules, which are part of a gas AMI solution, gas utilities can now have a “black box” to help with event investigations. ERT modules store 40 days of hourly meter data, giving gas utilities a historical view into the precise measurement of gas flows thru the meter. If an event investigation is necessary, the ability to look back at actual premise gas flows can be a powerful tool to better understand what really happened. Utilities can see if there was an abnormally high flow rate into the premise just prior to the event. It may also help determine what occurred behind the meter to have caused the high flow rate. Access to this type of information can alter the investigation focus from a gas leak to other probable causes and possibly reduce a utility’s exposure to litigation and liability costs.
“Itron will install gas AMI technologies at various gas utilities in the near future to help them monitor the integrity of their pipelines. Our customers are looking forward to extending the value of their AMI solutions beyond the meter and into their distribution assets,” says Porter.
Safety procedures have come a long way since canaries were used in coal mines. Innovative technologies like gas AMI have afforded gas utilities additional layers of data communications that enable proactive and cost-effective monitoring of key performance indicators for their distribution systems. Coupled with advancements in meter data collection, gas AMI solutions can help gas providers in their pursuit to enhance the safety and reliability of delivering natural gas.
Author:
Philip Holdbrooks is vice president of product marketing for Itron’s gas products and solutions. He brings more than 25 years of experience in the energy and utilities industry to the position.
Comments