July 2012, Vol. 239 No. 7
Features
Managing Mandated Change in Pipeline Control Room Operations
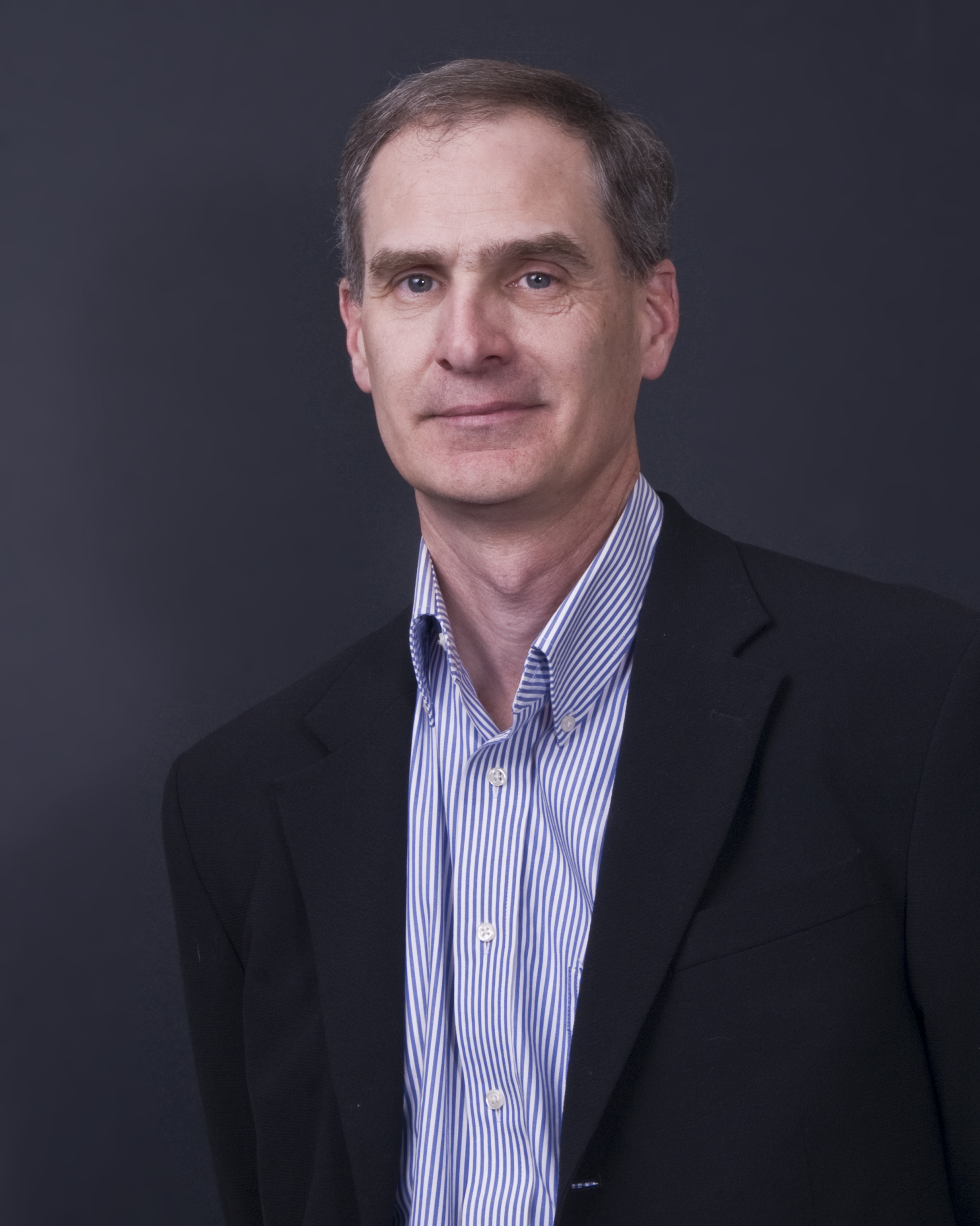
Creating a process for 49 CFR control room regulation compliance requires a great deal of thought, but ensuring that the hard work put into the investigative and implementation phases continue past a few months can require even more thought. To realize these benefits, pipeline operators must rise to meet a number of challenges, not the least of which is managing change.
Change management, as it relates to 49 CFR 192.631 and 49 CFR 195.446 and API 1165 and 1168 is at the same time a product, a process and a theory. It is about changing day-to-day business operations and changing responses to abnormal and emergency situations and this all requires changing behavior. This must start with a clear understanding of where operations are today and a plan for how everyone in your company — senior company officers, managers and control room operators — can transition effectively to new ways of doing things. Before putting an embedded software shift handover system in place, for example, the SCADA manager must consider and manage employee behavior to alleviate their fear of failing to use it correctly.
The good news is that many of the communications and information-sharing improvements called for by 49 CFR compliance mirror many of the change management measures that organizational development experts often recommend. Pipeline managers who are aware of these, and plan compliance activities accordingly, can be much more certain that changes they make will be effective and sustainable.
Change Management History
Let’s take a brief look at the history of change management.
Management theorists have examined and researched change management for a long timeTwo of the most influential theories were put forth by the Prosci Research institute and psychologist Kurt Lewin. Prosci identified the following five elements of successful change in an organization or group: 1) acknowledgement, which describes the stage at which both management and employees recognize the need for change; 2) desire, which focuses on the willingness to change; 3) knowledge, which addresses the employee’s understanding of how to meet the requirement for change; 4) ability, which considers whether the employees actually have the capability to act on that knowledge; and 5) reinforcement, which considers the organization’s ability to sustain the change.
Commonly referred to by the acronym ADKAR, the Prosci approach also identifies the five corresponding tactical phases illustrated in Figure 1. They include determining the 1) Business Need, 2) Project Definition and the 3) Business Solution, 4) specifying the New Process Systems necessary to achieve the business solution and 5) Implementation of the plan.
Figure 1: Prosci ADKAR change management model and associated tactical phases
Kurt Lewin, one of the earliest researchers in change management, put forth another element by drawing additional attention to the emotional factors associated with the desire to change.
A prominent theory of Lewin is the Freeze-Unfreeze theory. He groups these factors into following three phases:1) an Unfreeze phase, often triggered by a crisis or major organizational change; 2) a Change phase, where the new ways are forming; and 3) a Refreeze phase, during when the new procedures are accepted.
Understanding 49 CFR compliance, in the context of both the Lewin and Prosci models, can help bring about successful change.
Acknowledging The Need For A Safer Pipeline
Most pipeline organizations have recognized the need for change and are now attempting to make those changes. Certainly the desire for worker and environmental safety and the desire to avoid fines for non-compliance make for the strong business case that the Prosci model alludes to. An aging workforce is another point that will drive the need for change. The required change could certainly provide the emotional context that Lewin discusses in his theories for success.
At this point, pipeline management must re-examine how they are doing business and may have to challenge all assumptions about why they do things the way they do. This is especially challenging if they are trying to do so in the midst of a crisis. Success at this phase, Lewin says, requires a strong, but democratic style of leadership as opposed to autocratic and laissez-faire styles. He believes that democratic leadership increases the likelihood of success because it fosters agreement and freer thinking, which are necessary because commonly held practices and beliefs may have to change. Leadership can’t mandate elimination of old habits, but must strike a balance between being the voice that clears confusion while driving toward an end goal, all while fostering the communication from disparate members.
So while the Prosci model tells us that everyone must clearly acknowledge the business need for compliance with 49 CFR regulations, Lewin adds “that it is the job of the leader to make sure that happens, and it must be done by identifying the commonly held beliefs and assumptions that will change and by involving stakeholders in the process and discussions from the outset.”
Acknowledgement enables progress to the second tactical step of project definition, which, for 49 CFR compliance, might begin with a close look at the alarm management process. The overall 49 CFR Control Room Management program revolves around managing alarms, and, in fact, response to abnormal and emergency events is referenced 28 separate times in the regulations. So where Prosci analysis might bring us to the need for Alarm management, Lewin helps us address not only need to change but also the emotional barriers. “We have always had this many alarms and the pipeline operates okay,” an operator might say, exhibiting Lewin style denial. One way to unfreeze that resistance would be to bring in a third party that can unemotionally evaluate the system and guide the company through the data collection process and rationalization process.
The Desire To Change
Once a company has acknowledged a problem and has a defined project to address it, the Prosci approach calls for addressing the desire to make the change, and Lewin would further direct attention to the emotional factors which reinforce adherence to the status quo. This is unfreezing which is a job he places squarely on the shoulders of a democratic leadership style.
And surely, in addition to management skills and charisma, what any democratic business leader has to work with is financial incentive. Pipeline managers must be able to see in dollars and cents how the mandated change will affect and help improve their bottom line. Likewise, all frontline operators and other employees must see the link between planned projects and their paychecks.
The financial implications of regulatory compliance are well-illustrated by a 2008 instance in which a pipeline company was fined more than $5 million because its training system was inadequate. The government said that while they were technically in compliance using manual training tools, they should have implemented state of the art tools that simulated the hydraulic reactions in the pipeline. Furthermore, the simulator technology would allow the operators to work off-line through the exact same HMI they were using in the control room, thereby simulating the hydraulic reactions on their system in a flight-simulation-style environment.The government also said they should be applying a leak detection system so that the operator could work not only in the same SCADA environment, but could also see how leaks were developing. This requirement is included also in CFR 49 195.446 section h(4), which calls for, “training that will provide a controller a working knowledge of the pipeline system, especially during the development of abnormal operating condition>”.
Knowing How To Change
Once people do buy in to the project, do they know what they have to do to succeed? This is where 49 CFR compliance kicks in to satisfy the ADKAR requirements for knowledge and the clarity that Lewin requires to begin freezing the new order. Indeed, Lewin says there are some things the manager must make absolutely clear and, in this case, the 49 CFR regulations provide a great deal of guidance for doing so. And, this is exactly what the following sections of the regulation discuss:
• Section (b) Roles and Responsibilities. Each operator must define the roles and responsibilities of a controller during normal, abnormal, and emergency operating conditions.
• Section (c) Provide Adequate Information. Each operator must provide its controllers with the information, tools, processes and procedures necessary for the controllers to carry out the roles and responsibilities the operator has defined
• Section (f) 2 Requires field personnel to contact the control room when emergency conditions exist and when making field changes that affect control room operations.
• Section (h) Training: An operator’s program must provide for training each controller to carry out the roles and responsibilities defined by the operator.
• Section (j) Compliance and Deviations. An operator must maintain for review during inspection … records….documentation
These are just a few examples of the knowledge enhancing segments of the regulation. For more detailsa white paper is available.
Being Able To Change
The gap between knowing how to change and actually being able to execute that change can be quite wide. A number of the 49 CFR requirements help fill this gap. Section (g)1, for example, requires completion of a malfunction report when MAOP is exceeded or any accident occurs. But if the process requires the operator to open a SharePoint entry or manually fill out an electronic form, we often hear managers expressing concerns like “our operators are not computer skilled” or “our operators don’t have the time to fill out a form immediately.” The fact of the matter is that compliance and audit control require completing that form.
One possible solution is a workflow tool. It is, in fact, hard to imagine how compliance with sections such as (g) 1 could be cost effectively attained without a workflow tool. Exceeding MAOP, for example, could automatically trigger a software application and enables the operator to fill in a form on his or her operator screen without having to open another application. That form would be pre-dated, pre-routed to managers, linked to the tag and forwarded to shift log book, fully complying with the 49 CFR requirements.
Automated tools fit well with DOT-required standard operating procedures (SOP) requirements. While some of these may be managed manually, others would be much better applied using software tools. A third-party consultant, for example, can help companies rationalize alarms during workshops and then, after the rationalization process, develop SOPs and recommend tools that may help enforce them. Using these software tools may, at first, be daunting for operators, but if the tools are implemented correctly, the advantages will become apparent as controllers see that automated procedures not only free them up to do other tasks during emergency situations, but also perform auditing and paper work reduction chores that otherwise can be very onerous.
Reinforcing The Change
Both Prosci and Lewin come together on the importance of sustaining the change once it is made. Prosci addresses this in his reinforcement phase which is comparable to what Lewin calls the refreeze. The regulation is written such that API 1168 and 49 CFR create an environment that ensures changes will be sustained and conferred with the control room operators. The following sections define those traits:
• Section (c)3; internal communications.
• (e)5; monitor volume of controller workload.
• (f)1-API1168; management of change.
• (f)3; controller process change involvement.
• (g). Access to lessons learned.
In fact, if carried out as specified, most of the elements of the compliance contribute to sustaining the procedures and results. The Prosci model provides a proven analytical sequence, which if followed, can help ensure that the necessary changes are made and sustainable. Lewin’s theories increase the probability of success by reminding us that you can’t simply assuming employees will buy-in to the process.
Competent leadership, as Lewin recommends, is certainly vital for successful, cost-effective 49 CFR compliance, but that may not be enough to close the gap between acknowledging the need for change and achieving change that will last. Leadership– supplemented by automated tools which help involve stakeholders in decisions, communicate requirements and share progress toward meeting those requirements in real time — can go a long way toward closing the gap if they are simple enough and largely transparent to control room operators. Such tools do exist for just about every phase of compliance with 49 CFR 192.631 and 49 CFR 195.446 and API 1168. All of these are native to the SCADA system and they include workflow tools, HMI, simulation tools, operations management and controller communication tools, alarm management tools and field support procedure tools. These are a few of that are available from Invensys and other controls and automation vendors.
Effective change management is but one requirement for successfully implementing sustainable pipeline safety. Others include audit control, quantitative analysis, perpetuation of procedures, validation of data and closed loop analysis of information. Pipeline owners seeking excellence in both pipeline operations and safety will do well to think about these topics when managing change at their facility.
Author
Mark Grant is a SCADA Technical Executive with Invensys with over 20 years of automation experience. He is a recognized expert in 49 CFR Control Room Management and has authored and presented papers on the regulationHe also has supported compliance audits at numerous pipeline facilities.
Comments