November 2013, Vol. 240 No. 11
TechNotes
Hydrotesting Combination Technologies Mitigating Corrosion Risks Saves Operator Time and Money
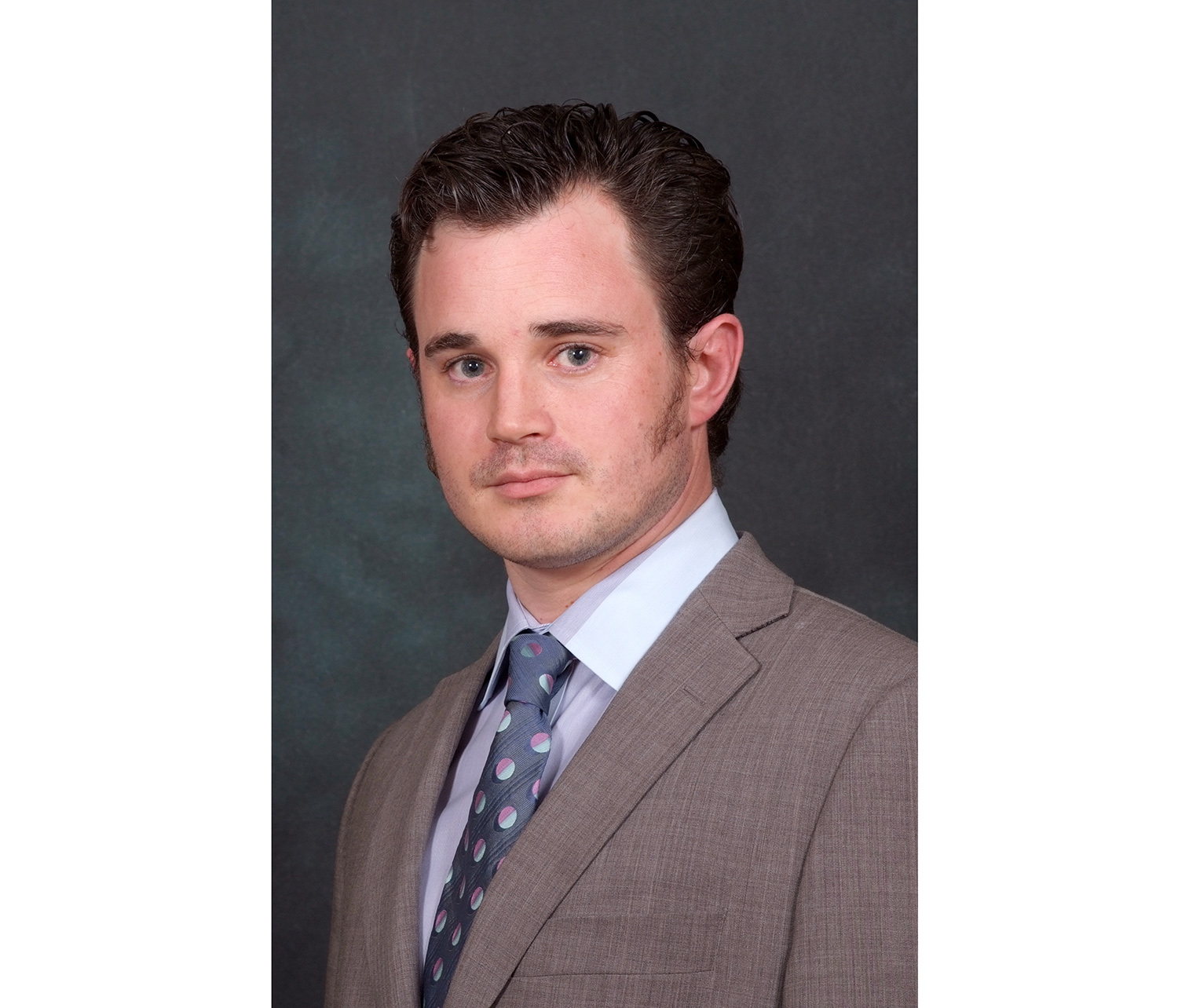
Regular evaluations, effective integrity management solutions and proper monitoring are all key factors in successful pipeline integrity management and maintenance programs.
When it comes to new pipeline commissioning projects, operators are faced with many challenges, including safety, risk mitigation, budgets and speed to market. One critical element prior to commissioning is the utilization of a hydrotesting technique in order to identify defects or damage during manufacture and installation. The challenge presented most often in hydrotesting is that the water used may be corrosive and contaminated with bacteria that will negatively impact the integrity of the pipeline. These negative effects may include localized and general corrosion caused by microbiological activity – or the presence of oxygen.
As the oil and gas industry evolves, pipeline corrosion technology must improve to meet increasing challenges to mitigate pipeline corrosion and asset damage. For hydrotesting and other preservation applications, this includes the research and development of chemical products that meet stringent environmental regulations and display fast-acting and effective performance.
One of the most important aspects of this application is disposal and impact on the environment. The PRESERVAN range has been developed to the highest environmental standards as mandated by the North Sea CEFAS registration process. All products are non-SUB and many are Gold Band rated, representing the highest possible environmental compliance in terms of biodegradation and bioaccumulation potential.
Clariant Oil Services’ PRESERVAN products are single-blend, multi-functional formulations that contain oxygen scavenger, biocide, corrosion inhibitors and dyes to enhance the integrity of pipelines. As well as preventing corrosion, the presence of dye can help to identify corrosion issues in oil and gas export pipelines, topside production facilities, subsea, umbilical, risers and flowlines (SURF), open or closed annuli and J-tubes, water injection lines and vessels and storage tanks.
The high level of performance offered by the multi-functional products is equivalent to dosing with individual products separately, therefore decreasing complexity, reducing chemical movement, eliminating chemical compatibility issues and offering operators decreased treatment time and cost.
To demonstrate the effectiveness of the product range, orbisphere testing in a laboratory was conducted to measure and record dissolved oxygen concentration using testing procedures based on industry standards of the American Petroleum Institute (API) as well as the National Association of Corrosion Engineers (NACE). Additionally during testing, Linear Polarization Resistance (LPR) electrochemical technique was used to measure and record fluid corrosivity and corrosion protection.
Results from these tests showed that PRESERVAN 5500 rapidly reduced the dissolved oxygen concentration to below 10 ppb within 12 minutes at 25°C and 16 minutes at 4°C. Using the LPR corrosion monitoring technique, it quickly decreased the corrosion rate in the first hour to 0.01 mm/year and stabilized at 0.0027 mm/year, representing 99.5% inhibition.
Bacteria testing included the latest NACE TMO 212-2012 for detection, testing and evaluation of MIC. The state-of-the-art molecular test method quantitative polymerase chain reaction (qPCR) was selected to test biocidal performance. qPCR, a modification of end-point PCR, detects amplified DNA during the PCR process. A highly sensitive camera detects fluorescence produced by the incorporation of a fluorescent binding dye in the sample, which gives rise to a more accurate and precise quantification of DNA. Unlike conventional culture-based methods such as most probable number (MPN), qPCR provides a qualitative, highly specific and accurate determination of active, inactive and even dead bacteria in any given sample.
To ensure the study was as harsh as possible, all five key bacteria species responsible for MIC were included in the qPCR testwork: Desulfovibrio desvlfricans (SRB), Shewanella putrefaciens (IRB), Thiobacillus thioparus (SOB), Pseudomonas aeruginosa (biofilm) and Methanolibacter arachidis (methanogen).
Results from the laboratory test method showed the product delivered an exemplary kill performance of 99.9% when compared to the controls at 4°C and 25°C.
It was also tested outside of the laboratory, in a pipeline system in the North Sea. A major operator in the North Sea laid a 26” dry gas export pipeline in preparation for commissioning a new oil and gas production FPSO. The pipeline was constructed from carbon steel with a 0.5 mm corrosion allowance, and would be filled with seawater for up to two years. The operator had concerns over the preservation of the integrity of the pipeline due to the corrosive nature of the seawater, and needed a suitable high-performing treatment that would combat the corrosion mechanisms presented by the seawater for two years.
Clariant Oil Services worked with the customer requirements and recommended 500 ppm of PRESERVAN 650. This is a combination product presented in a single blend, which provides rapid scavenging of dissolved oxygen plus controls the proliferation of micro-organisms to reduce the risk of MIC.
In order to provide treatment assurance, laboratory test work was carried out to confirm the corrosion performance. Coupon specimens from the actual pipeline material, including welds, were tested together with raw seawater from the pipeline location. All tests were performed at 4°C.
The results obtained over a 3-month exposure period indicated that PRESERVAN 650 was able to reduce the corrosion rate, and that the integrity of the parent and weld materials was not significantly compromised. The necessary assurances were provided to the operator and the pipeline was commissioned as planned and is now in full operation.
The operator realized significant cost and time savings by mitigating corrosion issues and preemptively testing the integrity of pipelines and pressurized equipment.
Through the utilization of hydrotesting combination technologies prior to new pipeline commissioning, operators are able to foresee potential corrosive and structural integrity issues of the pipeline asset. This testing technique not only enhances the overall integrity management of the asset, but also helps extend the life beyond initial design, while simultaneously managing costs, reducing risk and importantly, improving safety.
Author: Dr. Jonathan J. Wylde is the business manager for Clariant Oil Services in the UK and Netherlands. He oversees a team of more than 50 people and is responsible for the sales, operations and technical departments. He has held this role since January 2011. Before joining Clariant Oil Services, Jonathan was a researcher at BP in its Upstream Technology Group. He ran experiments to evaluate scale inhibition mechanisms for more cost effective and efficient scale management. Jonathan earned his BSc. degree in Geology and a Ph.D. in Physical Chemistry from the University of Bristol. He’s the author/co-author of 68 scientific publications in a variety of technical journals and industry conference proceedings.
Comments