October 2013, Vol. 240 No. 10
Features
Safety First: Columbia Pipeline Group Removes PCBs From Compressor Stations
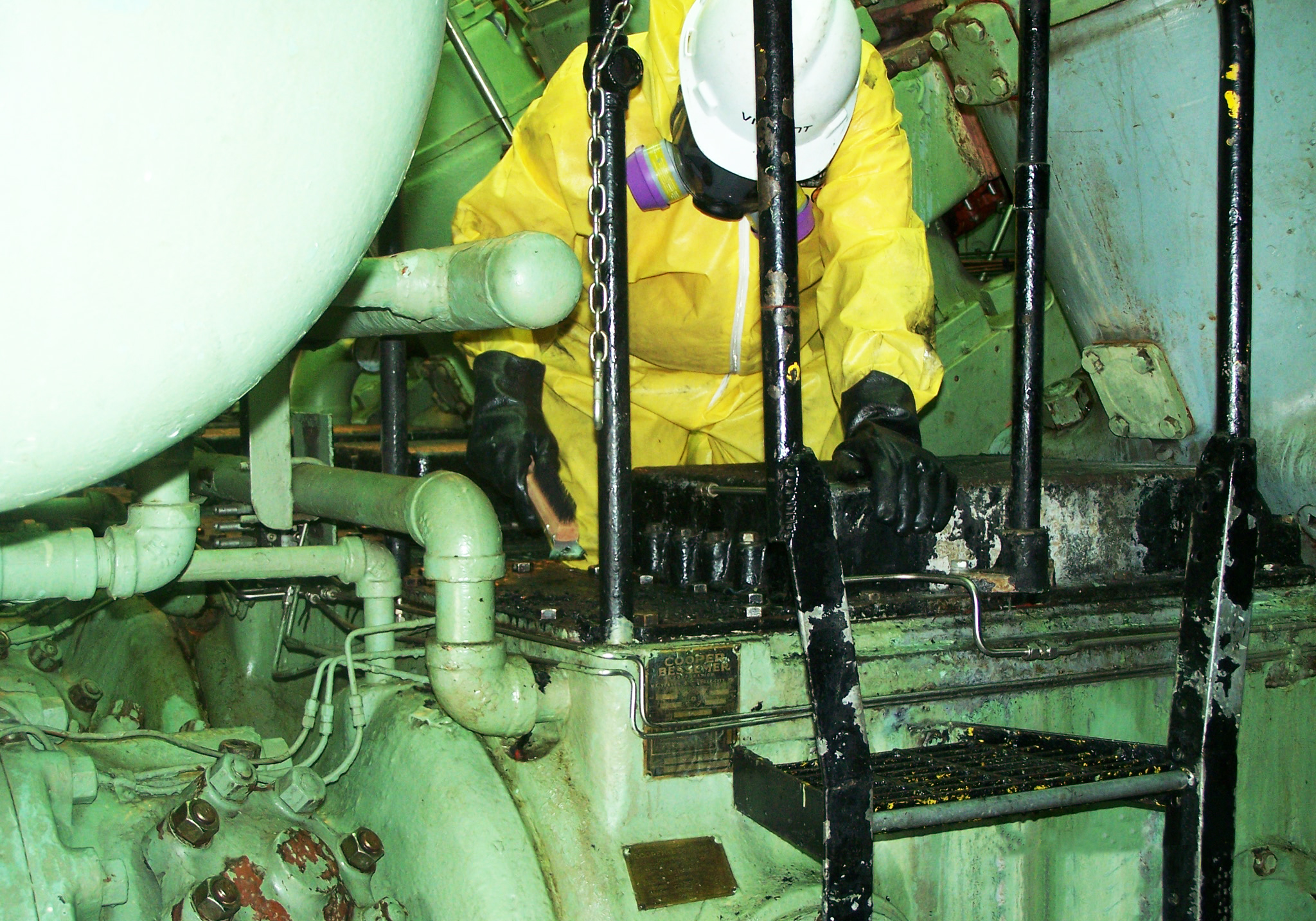
Removing polychlorinated biphenyls – commonly known as PCBs – from existing facilities is no easy task, so just imagine the added challenge of removing PCBs from active compressor stations that deliver natural gas to hundreds of communities in five states. Columbia Pipeline Group is facing just this challenge as it remediates 36 operating stations by 2014.
During a review process by the company, Columbia discovered that air compressors, which historically used PCB-containing synthetic oils within a “closed-loop system,” were emitting molecular-sized PCBs inside the facilities every time they were used. Many of the PCBs were absorbed by paint found on engines, walls, floors and pipes.
The Challenge
With only three years to remediate active natural gas compressor stations that are geographically scattered, with locations in West Virginia, Ohio, Virginia, Pennsylvania and Kentucky, Columbia decided to take an aggressive approach to get the job done safely and efficiently.
Columbia partnered with Applied Geology and Environmental Science, Inc. (AGES), an environmental consulting company based in western Pennsylvania; Contractor Services, Inc. (CSi), a West Virginia-based company that provides energy and environmental services to the natural resources industry; and VIASANT, an environmental services company based in Illinois, which has extensive experience in PCB remediation for the utility industry.
With multiple vendors, working many hours and performing high-risk tasks the project was quite complex. On top of that, the company had to keep the facilities running, because they serve customers in hundreds of communities.
“You never know what each day will bring on this project,” says Rob King, president and chief hydrogeologist for AGES. “VIASANT and CSi are cleaning tanks, drain lines and sump pumps one day and building scaffolding the next day to remove paint from compressor stations in one building that are literally the size of a football field.”
The Safety Approach
Before the program began Columbia mandated the crews must attend a “Life Saving Rules” session, which is a primer on the safety issues and rules for working in its facilities. VIASANT and CSi are each responsible for remediating multiple compressor stations and roughly follow the same approach to daily activities on the numerous sites. At each station, the crews are taken through site-specific orientations to ensure awareness and adherence to station-specific policies and procedures.
Additionally, a health and safety officer conducts environmental and air quality analysis of the work areas to determine if the lower explosive levels (LEL), oxygen levels and volatile organic compounds (VOC) levels are adequate. The safety officer remains on site and continues to monitor the levels throughout the day. These steps are essential in providing a safe working environment for the crew.
The crews kick off each day by conducting a morning safety meeting at which they review a job safety analysis (JSA) that outlines the discussion and documents how every task was handled. This includes discussing the necessary equipment, tools and materials to be used that day, as well as how to prepare and protect themselves from known or anticipated hazards. No task is too minute to discuss. For instance, the crew may review the proper use of a ladder or the safest way to climb scaffolding.
In addition, an afternoon safety meeting is held during which the crew discusses the remaining work for the day and reviews observations from the first half of the day. A representative from AGES is on site for the safety tailgate meetings and reviews the work with Columbia and documents the progress with the EPA.
One of the chief concerns is that with the crews doing repetitive tasks each day, there is the risk of complacency. Additionally, the crews must know how to stay out of the way of the Columbia workers who are keeping the gas flowing. The safety meetings help the crews make necessary adjustments to that end.
“Our collective approach to work is centered on a behavioral-based safety system,” said Jim Pisani, president of VIASANT. “The premise is simple. There is no such thing as an accident. Our goal is to change behavior before an incident occurs so proper planning and training is critical. We also enforce a ‘stop work authority,’ where each worker on site – from the site safety officer to the hourly individual – can stop work if there is a safety risk. It’s the staple of the entire program.”
Scott Freshwater, president of CSi, pointed to the added challenge for crew members who work while wearing so much protective gear, saying, “They are confined, it’s difficult to breathe, and they are working inside of a large plastic containment. The work is already challenging, but these added factors make for very slow and tedious work.”
Tools Of The Trade
The remediation work ranges from removing paint from walls, floors, doorways, gas bearing pipes and compressor engines to cleaning storage tanks and drain lines, as well as removing roofs and completely demolishing buildings.
The crew generally begins by building a containment seal around what is being worked on during a given day. Since crews always work in Level C, workers also wears white Tyvek safety suits, gloves and booties in addition to air purifying respirators. Depending on the task, HEPA fans are also used in the area to filter the air.
Once the area is prepped, the crews tackle paint removal in a variety of ways. A number of factors determine the best method and tool to use for a specific task. A few examples include:
• Concrete walls and floors: If paint is loose and peeling, hand-scraping is the easiest way to remove the coating. But, it is not always so straight forward, and a diamond grinder, which leaves a smooth and clean surface, is frequently used. Timing of work completion depends on the number of layers of paint and how much electrical equipment the crew is working around. To work in small, tight areas, a needle gun, which is a pneumatic air tool with 7-inch long needles and a vacuum that collects dust, is effective.
• Gas-bearing pipes: The effort required to remove paint from pipes and tanks ranges from simple to intense. At times, it’s as easy as removing existing paint from a pipe and recoating it. However, there are many pipes that must be cleaned, inspected and approved by Columbia’s corrosion technician and then recoated, which makes a big difference in the approach and time required.
For more difficult jobs, a sponge blaster is used. This tool is a small sponge with a metal aggregate embedded in it. When it hits metal, it expands, removes the paint and dust is caught in the sponge. It gets metal down to white metal, which means it is rust and paint free. To recoat the surface, bristle blasters, which look like a right-angle drop grinder, are just the right tool for preparing a metal surface to be painted. New or clean pipe is hard and smooth so it’s like painting a mirror or glass. The bristles rough up the surface, much like sandpaper, so that paint can adhere to the steel pipe.
• Compressor engines: Stripping down huge compressor engines and repainting them is the most time-consuming and the most dangerous work the crews face. Many times, scaffolding must be built due to the sheer size of the engines. Working at high elevations within the buildings is one of the biggest safety concerns on this project. In fact, Columbia won’t allow the crews to work on scaffolding that isn’t approved and inspected by an engineer.
To remove the paint, sand blasting is typically used. First, a containment seal is built around the engine. Then the crew members, who wear helmets and blast suits for protection, put hoses and ventilation fans in place. One person feeds the sand while another does the actual blasting. Hearing loss is also a concern; therefore, hearing protection (ear plugs and ear muffs) must be worn due to the heightened decibel levels. The crew members can only work in high-decibel areas for an allotted time, so labor shifts need to be rotated.
After completing daily tasks and letting the work area settle for 30 minutes, a HEPA vacuum is used to remove debris and dust from the area, and then the surface is cleaned with a solution. The containment seal is then torn down, and materials are put in drum liners, which are approved containers for disposal. It takes about two days to fill up one drum, and then it is sealed and put in storage with a containment built around it, while it awaits proper disposal approved by the EPA.
When cleanup is complete, the crew moves to the contamination reduction zone and decontaminates their suits, gloves and respirators, before their shift finally comes to a close.
Best Practices
To support and foster a leading safety culture, there can’t be too much communication. Consistent, clear communication provided in the twice-daily safety tailgate meetings has been the linchpin of this remediation project. The crew must not only understand what work they must perform, but also how and why.
Communication takes place at all levels. Senior leaders at Columbia, AGES, CSi and VIASANT also perform weekly status calls and site walk-throughs. They review completed work and the activities planned for the upcoming week. This gives facility personnel the opportunity to provide the appropriate advance work and work area clearance to allow for the safe execution of upcoming tasks.
Columbia also sends a combination of internal and third-party auditors to the various sites to watch tasks being performed. This allows for adjustments to be made along the way, instead of discussing how something should have been handled once the project is complete.
In addition, CSi and VIASANT complete a “weekly worker observation form” and turn it into Columbia and AGES. They select a task to highlight each week, such as stripping an I-beam with an ice blaster, then conduct a mini-audit and share the results.
“Near misses” are also reported. Senior leaders share root cause, circumstances and explain resolutions. All of the players have three weekly calls and openly discuss what goes well and what goes wrong.
Results
At the end of July, the crews were fast approaching 200,000 man hours, and Columbia is on track to have the remediation completed by the 2014 deadline. The following have been remediated without injury:
• 300,000 square feet of walls and ceilings
• More than 120 compressor engines
• 40,000 square feet of concrete floors
• 13,000 linear feet of superstructure
• More than 350 equipment pedestals
• More than one mile of operational piping
Neither VIASANT nor CSi has had one recordable Occupational Safety and Health Administration (OSHA) incident during the nearly 200,000 man hours worked, which internally is called “goal zero.”
“Columbia said at the beginning of this project that it was going to do it right and not cut corners,” said King. “They never complain about scheduling, hours worked or the budget for safety-driven initiatives. And, their overall attitude trickles down to all of the workers. Columbia is really at the forefront of safety remediation practices.”
Author
Marc Okin, due diligence and remediation manager for NiSource, the parent company of Columbia Pipeline Group, has worked in the natural gas and remediation industry for 26 years. During his career, he has led hundreds of projects and safely investigated and remediated more than 200 compressor stations. Okin ensures the safety program, “Safe by Choice, Not by Chance,” is practiced by all contractors and employees who work on the company’s remediation projects.
Comments