November 2015, Vol. 242, No. 11
Features
Combating Noise in Gas Pipeline Transmission
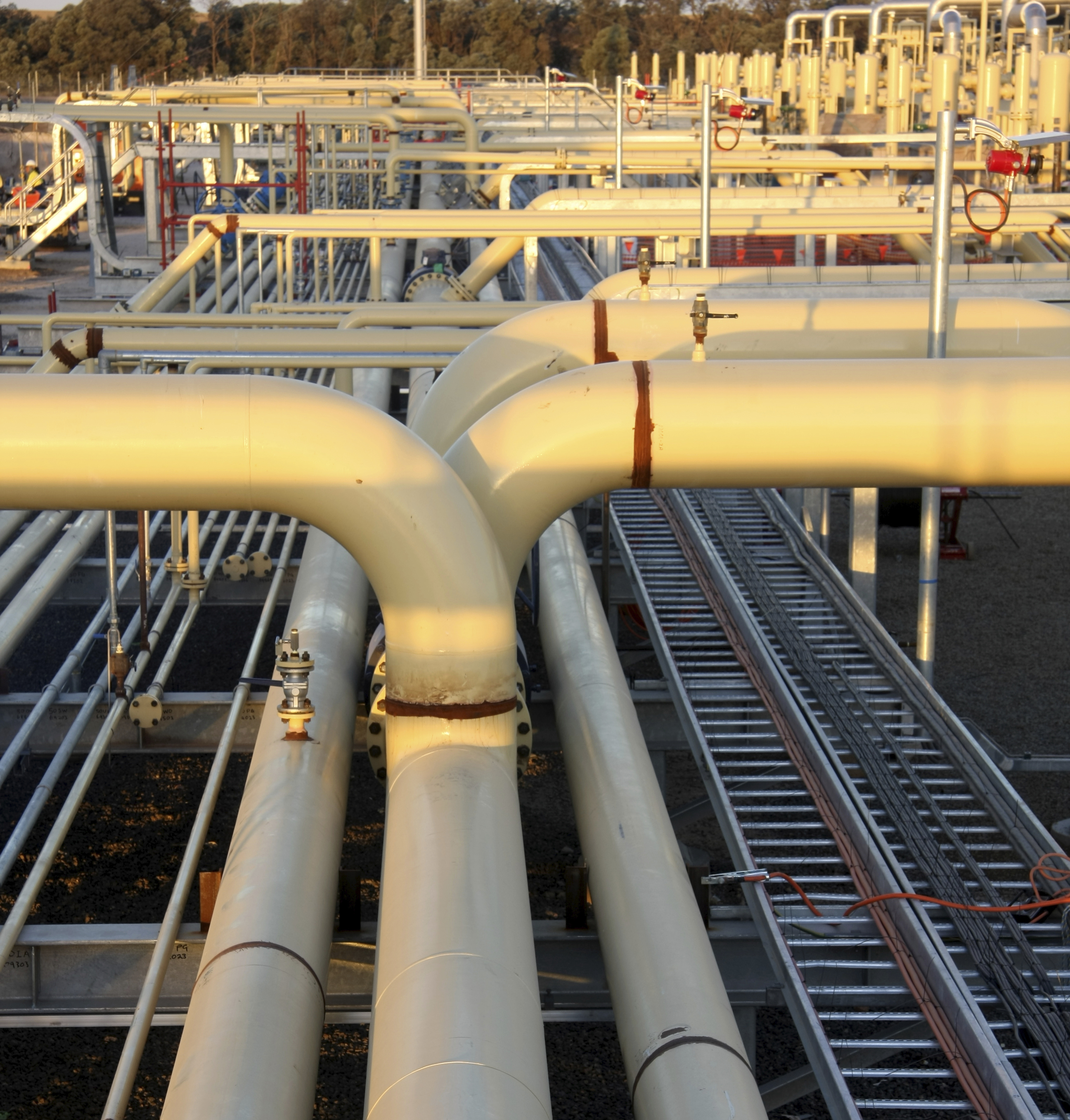
Pipelines have been established for many years as the simplest and most economical way to transport high quantities of natural gas over long distances, moving gas from new shale fields and other production sources to LNG stations, local utilities, industrial plants and natural gas–fired electric power plants.
Natural gas pipelines only consume an average of 2-3% of the gas’s potential energy to overcome frictional losses along the route, making them more cost-effective than the use of road or rail transport.
Pressure differentials are used to “push” the gas through transmission pipeline. However, as pipelines get longer, it becomes necessary to increase the pressure used and to add compression stations.
Typically sited every 50-100 miles, compressor stations keep the natural gas flowing by boosting the pressure of the gas to compensate for pressure losses along the pipeline. Gas compressors work by increasing pressure, reducing the gas volume and increasing the density of the fluid.
Pipeline networks have become increasingly complicated, encompassing more branches, necessitating the inclusion of distribution hubs and metering stations via which the gas from a high-pressure line can be routed to various lower pressure distribution lines.
For example, high-pressure main feed lines can run at 1,200 psig, with medium-pressure main lines at 600 psig and low-pressure main lines at 200 psig. Distribution and pressure reduction occurs across “city gates” which are pressure-reducing, custody transfer, and metering stations. These stations can often be located in urban environments. In Los Angeles, for example, gas is imported via pipeline, stored around the city at a number of underground gas storage facilities, and withdrawn based on local demand requirements.
What is Noise and How is it Created in Pipelines?
The main methods typically used to grow pipeline capacity are increasing gas compression and increasing pipeline diameter. Since the 1940s, pipeline companies have used both measures to improve the capacity and hydraulic efficiency of the systems. However, it is usually more cost-effective to increase gas compression, as the more the gas can be compressed (with higher pressure), the smaller the pipeline diameter can be.
In order to increase gas compression, more and more powerful, and subsequently more expensive, compressor stations will be needed. However, the cost of these stations will be lower in the long run than the cost of larger pipe diameter for the entire length of the run.
The trade-off for this economic benefit is an increased potential for noise generation as the equipment needed to achieve the high gas pressure can be a significant noise source. Compressors are noisy, as can be the control valves which regulate gas flow through the pipeline at the source station, compressor stations, distribution hubs and metering stations.
The conversion of static pressure to kinetic energy at the vena contracta in the control valve creates high-velocity jets which can be subsonic, sonic or even supersonic. Turbulence and sonic shock waves create a noise spectrum with a characteristic peak frequency.
In cross-country pipelines with compressor stations, potential noise-producing control valve applications include recycle valves, vent to valves that provide emergency pressure protection and blowdown valves. In gas-storage facilities, a wide range of control valve applications include gas-receiving, compression for storage, withdrawal, dehydrating, odorizing, and pressure reduction to distribution pipelines.
Typically, control valves have a controlling diameter much smaller than that of the inlet/outlet piping. Consequently, expanders are added to transition the flow from the smaller valve to the larger pipe. The expansion of the gas through this valve outlet expander can be another source of noise. This source is exaggerated when the expansion is achieved with eccentric reducers, compared with the use of concentric expanders.
Why is Noise Such a Problem?
Excessive noise generation can be damaging to people’s hearing and disruptive to the environment. The Environmental Protection Agency (EPA) has produced numerous studies documenting the dangers of acute noise, including high blood pressure, coronary disease, migraine headaches, and low-birthweight babies. The World Health Organization (WHO) published a report in 1999 called Guidelines for Community Noise, to standardize risk assessment and management of noise dangers among participating countries.
Between 70dBA and 85dBA, the noise source becomes quite pronounced. However, long-term exposure to noise at this level is unlikely to damage human hearing. At 85dBA and above, the noise source reaches a level where sustained exposure can begin to damage human hearing. For these reasons, guidelines from the Occupational and Safety Hazard Administration (OSHA) mandate an 85dBA limit for exposure of up to eight hours.
The higher the noise source rises up the dBA scale, the shorter the duration of exposure becomes before damage can occur. At 140dBA, not only is hearing affected, but the human body will actually begin to feel pain from the sound waves.
Noise generated from pipelines can be (and usually is) subjected to restrictions imposed by the OSHA, WHO and the EPA or their local equivalents. Violations of these restrictions can result in severe penalties – including fines and shutdowns – as well as lawsuits from affected residents, businesses and advocacy groups.
Low-frequency noise, usually caused by standing waves, can result in the mechanical vibration of piping and ultimately physical damage to the pipeline structure. In addition, large-scale vortex eddies and shedding from the valve are key causes of low-frequency vibration, as are large-diameter jets from the valve trim.
Similarly, pipes can vibrate radially because of high-frequency noise generated in the valve. This can cause fatigue issues at welded attachments such as drains and thermocouples, with the potential for unforeseen catastrophic failure.
Potential for fatigue failure increases when the ratio of pipe diameter to wall thickness squared increases.
The ability to effectively manage noise and maximize transportation efficiency is affected by increasingly stringent environmental regulations which influence equipment choices and siting of compressor stations.
For example, the pipeline company may have to install electric-powered compression instead of gas-powered compression (even if gas would be more efficient), or relocate compression to a less than optimal area, or even install larger diameter pipeline in lieu of additional compression (which may require additional right-of-way permissions and will be much costlier than compression).
Noise regulation is often defined not by local near-field noise, but by further field noise that can affect local residents. Noise requirements at property lines are generally limited to 55 dBA, and at night the noise levels can drop even lower. This can equate to low noise levels at the valve, sometimes in the 70dBA at the 3 foot level.
Traditional Methods of Noise Attenuation
There are two components of noise: frequency (Hz) and amplitude (dB).Typically, noise amplitude, or magnitude, increases with higher pressure drops, which are an unavoidable issue in gas transmission.
Traditional methods of combating pipeline noise include using thicker or heavier pipe walls, adding acoustic lagging or enclosing the noisy equipment inside a building. However, each of these has its disadvantages.
Heavier pipe walls and thicker insulation become economically unacceptable for larger pipes on very long runs, especially for higher grades of piping material.
Meanwhile, although noise typically propagates and attenuates with distance, it continues to travel through the pipe with little attenuation. Noise attenuates at a rate of 6dB for every doubling of distance from a point source and at 3dB every doubling of distance from a line source (pipe) in free-field environments. However, it attenuates at only 1dB for every 30m of pipe travelled. This means that enclosing the noise equipment in a building is only effective until the pipe exits the building. Consequently, most pipelines are buried, with noise noticeable in the station location only.
Regulating stations can have buildings installed around the stations which can then provide acoustic noise reduction. However, these buildings present a safety risk as, when there are gas leaks, the gas can collect in the building and create hazards of either asphyxiation or explosion.
Finally, in cases of gas storage or in some pipeline systems where source and demand locations can swap, the same gas can flow in the reverse direction through control valves – making it far more challenging to design the equipment to minimize noise.
Best Practice in Noise Reduction
The best way to deal with noise generation is to address it at its source. Pipe walls have far better attenuating properties against higher frequency noise sources. This means that if the frequency of the noise can be made higher by using smaller discharge jets in valve trim designs, maximum advantage can be taken of the pipes’ inherent noise-insulating properties.
When mixing pre-treated gas with production gas coming from the field, it may be necessary to balance this with larger passages if dirty service (gas with entrained solids) is being transported.
Multi-stage letdown can also be employed to reduce trim discharge velocity and so lower the magnitude of the noise generated. The ISA control valve guidelines for velocity and kinetic energy limitations provide useful advice on minimizing trim discharge velocity. Characterized valve trims (EQ% or modified EQ%) should be used to address potential noise generation resulting from variable demands on the system, while concentric expanders should always be employed over eccentric.
For further information visit www.imi-critical.com
[inline:Peterson Chris (2).jpg]
Chris Peterson
Comments