February 2016, Vol. 243, No. 2
Features
Heat Exchangers Certified for Pipeline Components Cooling

Owners and operators of fuel and other energy pipelines are well aware of the changed regulatory environment in the wake of the 2010 BP Deepwater Horizon oil spill in the Gulf of Mexico.
As the public’s fears escalated because of the environmental damage and loss of life that followed the rig blowout, regulatory focus turned to prevention. One operational function under current scrutiny is preventing sparking or ignition sources that could be catastrophic to the pipeline, worker and public safety, and the environment.
The regulatory changes are particularly applicable to one of the most critical operational necessities – the cooling of electro-mechanical devices and controllers for every facet of the pipeline industry from oil extraction to refining and distribution.
For most operators, the cooling method of choice has been air conditioners, with the primary certificated method in the United States and Canada (UL/cUL) and in Europe (IECEx and ATEX). However, existing air conditioner designs do not meet revised, more stringent certification criteria for hazardous locations, such as oil platforms, refineries and oil distribution centers.
Heat exchangers, acknowledged as energy-efficient alternatives for A/Cs, could not be considered because none were certified by any of the U.S. or European organizations for specific hazardous location usage.
Since then, certification requirements from UL/cUL (also referred to as Underwriters Laboratories) and ATEX/IECEx includes changes for enclosures to prevent A/C units from creating ignition sources due to relays, switches and thermostats. Fortunately, operators now have a certificated alternative.
Air-to-air and air-to-water heat exchangers have been granted certification for Class 1/Division 2 hazardous locations in North America and Class I/Zone 2 in Europe – a first for this method of enclosure cooling. That should be good news for a number of reasons including safety, efficiency and energy cost controls.
Technology Changed
Regulations define hazardous locations as areas where the presence of flammable liquids, gases, vapors and dust constitute a risk for fires or explosions. A gas or vapor environment in which explosive mixtures are not likely to occur under normal operating conditions is classified in the United States and Canada as Class 1/Division 2 and in Europe as Class I/Zone 2.
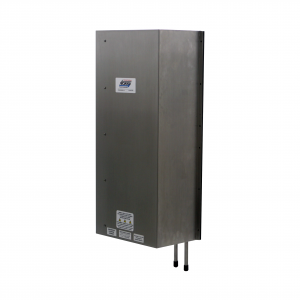
Pipelines and refineries are obviously classified as hazardous locations, as are power-generation plants and food silos. Equipment cooling strategies at any of these hazardous locations could not be certified unless the possibility of an ignition source, such as sparks or high heat from electrical equipment, was eliminated.
That left operators with only three certificated methods of equipment cooling prior to 2015: air conditioners, vortex (compressed) air coolers or fans suitable for use in combustible environments. Heat exchangers, while considerably more efficient than the others, were not certificated at the time because of core design in which heat was transferred by aluminum sheets stacked or folded together to enable the flow of air.
The issue here was the possibility of a source of ignition. A static or electric charge could build within the sheets, possibly leading to a spark or explosive mixture at the location of the heat exchanger – a danger that eliminated any possibility of hazardous location use for this design of HX.
What changed was the introduction of heat pipe technology, which replaced the previous core design. A heat pipe core with fins transfers heat from inside the cabinet to outside without the buildup of a static charge so the chance for spark generation is eliminated.
These HX units function safely in non-purged enclosures with built-in design features that fall under “non-sparking” or “protected-sparking” classification, as per UL/cUL and ATEX/IECEx standards.
Certification of these air-to-air and air-to-water heat exchangers has been granted by UL/cUL for Class 1/Division 2 A, B, C and D group types in the U.S. and Canada.
UL, one of the leading safety science organizations in North America, certifies equipment for hazardous locations and conducts manufacturer audits. For Europe’s Class 1/Zone 2, IECEx and ATEX certification have been awarded by the International Electrotechnical Commission.
As is often the case, it took considerable time to secure the North American and international certifications for the heat pipe-based heat exchangers. One reason for the delay was because the certifying agencies had no similar source or prior certification experience for comparison other than air conditioners or swamp coolers – two technologies significantly different from heat exchangers. It took several years before the agencies were able to complete research and affirm certification for this type of technology.
How It Works
HXs’ low power draw eliminates the need for separate circuits. Unlike air conditioners in remote areas, the certified HXs can be powered with either AC fans or DC fans with solar battery packs. The benefit of the latter should be obvious for maintaining panel cooling operations in remote hazardous locations – pipeline operators no longer have to rely on either air conditioners or generators to power them.
Air circulates throughout the cabinet to prevent hot spots and to draw the hot air over the core. Hazardous location-capable HXs are rated to operate in the temperature range of -10°C to 70°C. A neoprene gasket and flange eliminate the possibility of air exchange and contamination inside or outside the cabinet or panel.
The HXs are capable of providing a NEMA 4X and IP66 level of ingress protection for expensive electronics within the cabinets from the harmful elements that often exist in a pipeline environment.
Heat exchangers can dissipate heat generated by variable frequency drives – controllers used for many pipeline pump operations. VFDs contain electronic elements that control the RPM as well as torque of the motors by varying motor input frequency and voltage. They generate significant amounts of heat, depending upon the horsepower of the pump.
Some of the most efficient VFDs in the market convert 6-7% of the input horsepower to heat – a sizable percentage that HXs are designed to dissipate.
Air-to-air HXs maintain ambient cooling, which is sufficient to ensure the operation and increase the lifespan of most electronic components. Heat exchangers can be DC or AC equipped.
Unlike the air-to-air HXs with heat pipe core technology, air-to-water heat exchangers operate with a core of copper tubing and can be easily connected to a water supply. If the water source is found to be contaminated with corrosive elements, a stainless steel core is preferable to copper tubing.
For an offshore oil rig that relies on the ocean’s salt water for its cooling source, the stainless steel core has already proved its value. The core protects the exchanger and the components it must cool from the corrosive properties of the salt. The rig operator and owners report normal cooling without any reduction of the electronics’ functions.
Cost Comparison
Component cooling of pumps and other controllers for pipeline operations can be prohibitively expensive if the air conditioners are the primary source. No one should be surprised that air conditioners are considerably more expensive to operate than heat exchangers if for no other reason than A/Cs tend to run 24/7.
One example: a standard industrial air conditioner will require at least 7 amps to operate while the certificated heat exchangers pull only 1 amp per fan. Additional A/C energy requirements far exceed those of the heat exchanger; e.g. NEMA 4X (IP66) air conditioning cabinet cooling units may require as much as 5,000 Btu, depending on the severity of the conditions in which they operate.
Comparisons of A/Cs with HXs for pipeline component cooling should include projected lifespan. Constant usage of air conditioners generally results in a much shorter lifespan. In harsh external environments, the projected lifespan of the typical industrial A/C is only two years while the certificated air-to-air heat exchangers can last many years longer, or as long as their heat pipe core has not been compromised.
As one would expect with non-stop air conditioning, energy costs are considerably higher. Low-energy heat exchangers, which do not have to run 24/7 to maintain cooling, require much lower expenditures.
Another point to consider is the degree of cooling. HXs cool at ambient temperatures, sufficient to dissipate heat and protect electronics. A/Cs, on the other hand, chills the electronics at much colder temperatures than are necessary to protect them.
Ambient cooling is more than capable of maintaining and even increasing the lifespan of components. Neither compressors nor refrigerants are used by either type of HX, even though air-to-water exchangers can provide below ambient temperatures on those occasions when they may be necessary.
Operator’s Experience
The experience of Alliance Pipeline of Calgary, AB and Eden Prairie, MN with certificated heat exchangers confirms the HX’s effective performance in the challenging pipeline environment.
Alliance said it implemented HX component cooling along its pipeline with the installation of 10 remote units in locations devoid of power lines. With air-to-air exchangers operating on battery-powered 24 VDC circuits, Alliance reported consistent use of solar-powered batteries because the locations have ample direct sunlight. Heat exchangers are situated in small pump stations where direct sunlight and equipment in the stations generate heat.
Author: Rahul Mulinti is the engineering manager at Noren Products, Menlo Park, CA.
Comments