June 2017, Vol. 244, No. 6
Features
Composite Sleeves Address Mechanical Damage to Pipelines
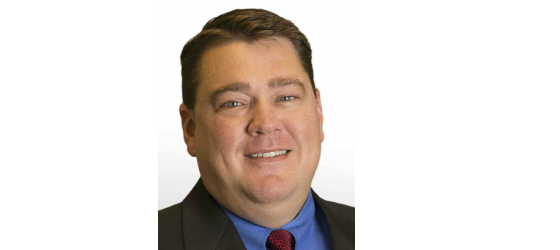
Pipeline operators work hard to ensure their pipelines are protected from external corrosion. However, it can be more challenging for operators to keep their pipelines safe from third-party interference. While pipelines are buried, well-marked, and permission is meant to be obtained before digging near a pipeline, in some cases a third party will cause mechanical damage. This can include dents and gouges, which tend to be caused by construction and agriculture, or contact with rocks in the backfill and settlement.
Between 1994 and 2013, one-third of the serious incidents on all types of pipelines were caused by mechanical damage during excavations. This is more than any other single cause1. However, a dramatic reduction of these incidents has trended over the last 20 years due to significant efforts made by the pipeline industry to increase public awareness and engage all stakeholders to the location of underground pipelines.
Depending on the severity and type of dent or mechanical damage, remediation may be considered by the pipeline operator. Composite pipeline repair sleeves are an extremely popular alternative to traditional repair methods such as “cut and replace,” welded sleeves and clamps. They can effectively repair a pipeline with up to 80% external metal loss defects. Composite sleeves have a proven, decades-long track record that has been developed, tested and peer-reviewed as being a suitable system of reinforcement on mechanically damaged liquid and gas pipelines.
Over time, a pipeline will experience some amount of cycling which needs to be addressed as well. The action of pressure cycling on a dent will eventually lead to the initiation of fatigue cracks, and ultimately failure, if not properly addressed. Composite sleeves have been shown to extend the life of a damaged pipe by immobilizing the defect and controlling re-rounding and bulging of the weakened area. It is required to use a filler material underneath the composite to effectively control movement of the dent during pressure cycles.
Composite sleeves are a suitable repair for most types of mechanical damage on pipelines. The four main codes/guidelines utilized to allow the repair of mechanical damage using composite sleeve repairs are:
- ASME B31.4 (2016)
- ASME B31.8s (2016)
- CSA Z-662 (2015)
- PRCI repair manual (2006)
Testing
In 1987, the Gas Research Institute (GRI, now GTI) assembled a team of pipeline professionals and research organizations to lead a comprehensive program to verify the effectiveness, durability, and performance characteristics of a repair that permanently restores the serviceability of the pipe. GRI engaged Houston-headquartered Stress Engineering to lead the mechanical damage aspects of the program. The testing included dent and gouge repairs.
The 1997 GRI Report No. GRI 97-0143, Evaluation of a Composite System for the repair of mechanical damage in Gas Transmission Lines, involved full-scale tests completed on 12-inch diameter pipe with D/t ratios of 51 and 68 having 15% dents with gouges. Pressure cycles were initially applied between 0 and 50% MAOP for 50,000 cycles, and then between 0 and 100% MAOP until failure. The results showed that the Clock Spring repair system procedure was effective in increasing the fatigue life for the repaired defects by two orders of magnitude when compared to unrepaired sections.
In addition, Clock Spring products were installed over several pipe diameters with increased D/t ratios (96) and gouged depths (30% and 50% of the wall) with repairs applied at 0%, 50%, and 90% MAOP were cycled to prove acceptable fatigue of over 250,000 cycles. Fatigue testing indicates that composite repair sleeves extend fatigue life by an order of magnitude over grinding as the sole repair. The results of this study provided several important insights as to the importance of inspection and the removal of cracks or stress risers from the defect.
Since this landmark study, Clock Spring has had 25 years of dent performance of highly fatigued pipelines globally. The composite sleeve repair system is manufactured in a factory under controlled conditions and then bonded to the pipeline. This type of repair allows greater repeatability, quality and predictability in the pipeline repair installed at the mechanically damaged repair location.
Composite Sleeve Application
Clock Spring composite sleeves are installed by certified technicians in three relatively quick steps. The pipeline does not need to be shut down during the repair process.
Step 1: Pipe preparation – Commercial sand blast to remove coating, removal of stress concentrators in accordance with applicable codes and inspect dent area for surface cracking.
Step 2: Molding the filler into defected area – This incompressible material fills the dent area and acts as a load-transfer agent to transfer the stresses from the pipe to the composite sleeve. If molded, a visual inspection before the installation of the surface can verify good fit-up of the sleeve.
Step 3: Fit the composite sleeve onto the pipe and cinch it down to ensure maximum strength in repair.
Once these steps are complete the composite will cure within one hour and the pipe is ready to be recoated and backfilled.
Case Study
A pipeline dent becomes an immediate concern if the dent is severe or sharp enough to induce cracking. If the dent was caused by third-party damage, such as gouging, this can also initiate cracking. Both of these immediate concerns can also be related to coating disbondment. A coating disbondment issue can lead to corrosion which also affects the integrity of the dent.
An example of addressing this threat using the above procedure for repair features a molding step before the installation of a Clock Spring repair sleeve. An 8% dent with a gouge approximately 10 inches long was dressed to remove stress concentrators and prepared before a single-wrap mold formed the filler material in the dent region, building back the ovality of the pipeline. The molding step ensured constraint of the dent once the repair sleeve was installed.
A dent represents permanent damage to a pipeline by deformation. Dents typically result from a purely radial displacement of the pipe wall during either construction or from external land movement of the pipe across a hard surface, such as a rock. For example, 30-inch diameter gas pipeline with bottom-side dent was repaired using Clock Spring’s ‘Spool Feeder’ method due to limited clearance and confined space.
Conclusion
One of the many challenges operators face each day is keeping their pipelines safe from the public. It is important that operators are aware of the methods available for repairing mechanically damaged pipe and have a plan in place for when they encounter it. Composite sleeves have been used to constrain the dent.
Composite sleeves are proven to provide almost two orders of magnitude improvement in fatigue life compared to grinding alone and almost three for unrepaired pipe. The strain, as the dent tries to flex, is transferred through the incompressible material into the composite repair.
It is also important that operators fully assess the composite they want to utilize to repair their pipelines, as not all composite repairs are the same. Any company offering a composite repair system for mechanical damage should be able to back up its claims of repair suitability with valid and independent testing.
1 DOT/PHMSA (2014) Pipeline Significant Incident files. Available at http://primis.phmsa.dot.gov/comm/DamagePrevention.htm.
Comments