June 2017, Vol. 244, No. 6
Features
What to Look for When Updating Pipeline Valves in Urban Areas
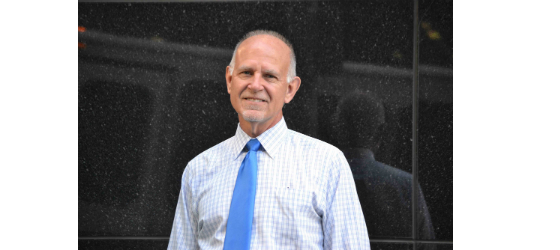
SoCalGas is committed to investing in its natural gas system to ensure safe, reliable, and affordable service for its more than 21 million customers across Southern California. SoCalGas’ five-year capital plan is comprised of $6 billion in infrastructure investments, including $1.2 billion this year for improvements to distribution, transmission and storage systems and for pipeline safety.
A key component of that investment is maintaining and upgrading the roughly 800 mainline valves that separate the company’s pipelines into sections. Earlier this year, SoCalGas announced that it will upgrade or replace 50-60 pipeline valves in 2017 to further enhance the safety of its system.
A key component of the upgrades to the network is the use of technology allowing valves to be opened or closed remotely by system operators from a central control location. These are called remote control valves (RCVs).
Other valves, called automatic shutoff valves (ASVs), are equipped with a control device that automatically triggers the actuator and shuts off the flow in the event of a large pressure drop. RCVs and ASVs are by no means unique to SoCalGas, but the company’s Pipeline Safety Enhancement Plan (PSEP) team has considerable experience with upgrading valves in urban areas.
Urban Areas
Many of the valves the PSEP are automating are in city streets or intersections, while the existing manual valves simply have pinion shaft extensions. Automating these valves means adding actuators, which requires that vaults be constructed in city streets. SoCalGas’ mainline valves, particularly in urban settings, are bridled to feed high-pressure regulator stations. Crossover valves exist to feed other transmission pipelines. There are also blowdown valves to allow blowdown capability at each mainline valve.
SoCalGas has found these associated valves often interfere with the space needed for vaults. As a result, the project scope can grow from automating existing mainline valves to replacing the entire valve assemblies and, possibly, relocating the valves to other locations altogether.
Apart from the typical obstacles inherent in all pipeline and valve upgrade work, valve automation projects in urban areas present an unusual set of challenges. Here are several examples:
Land acquisition: You’ve heard the old real estate adage about location, location, location. Well, there’s a price to be paid for certain locations. Property in urban/populated areas simply costs more than in rural areas. No surprise there, but the rates used in estimating land value add a wrinkle in urban settings.
Utilities generally appraise property at non-residential rates. Sometimes landowners have a different perception and appraise the same piece of property at residential rates. These owners believe the value of their property is higher, requiring further negotiation to arrive at a fair piece for the land in question.
Often, SoCalGas is not looking to purchase property outright, but to acquire a temporary right-of-entry or an easement designated for underground gas, electric, water, sewer, telephone and cable lines. In a populated area, the negotiations can be complex and time-consuming. SoCalGas relies on existing valve locations to use existing land rights, easements and pipeline assets. When appropriate, SoCalGas evaluates other properties during the scoping and selection phases to ensure cost-effectiveness.
Vaults for automation equipment: SoCalGas tries to reduce the footprint of its vaults, when possible, by using different actuator technologies. The company prefers using double-acting scotch-yoke actuators. Depending on pipeline diameter, these scotch-yoke actuators can be large, requiring sizable vaults to house them. In those cases, SoCalGas will evaluate other pneumatic or electric actuators for smaller footprints.
Figure 1: The concrete vault that houses the actuator (left), along with the mainline valve.
Acquiring permits for vaults in a populated area poses an additional challenge – in some cities, it can take up to six months to approve vault permits. It’s best to determine the city’s requirements and, if applicable, approved manufacturers as part of the initial design phase. A rule of thumb is the smaller the vault, the easier the negotiation for permitting. Another factor to consider is whether the vault is pre-cast or poured in place. Pre-cast vaults are typically less expensive to install; however, site conditions or construction space limitations may limit their use.
Higher costs: Permit conditions in urban areas could have a dramatic impact on the cost of a valve automation project. For example, a permit could restrict working hours to minimize noise in a neighborhood, thus reducing productivity, or it could impose aesthetic requirements on aboveground equipment, adding additional cost.
Construction costs are often higher in an urban environment. These include the need to cut concrete and excavate (vs. digging dirt in a rural area), traffic control (adding/removing traffic cones and electric signs), plating over an excavation during non-working hours so traffic can resume, and greater security and public safety measures.
Some urban areas require noise-canceling plates. PSEP engineers often consider moving valve stations from the street to a new location on the sidewalk which is much safer for the public and company crews. In one recent automation project, for safety reasons, SoCalGas’ crews had to remove and then rebuild a brick wall to relocate a valve from the street to the sidewalk.
Figure 2: A wall in Garden City, CA had to be removed and rebuilt so that a valve could be relocated from the street to the sidewalk in an aboveground cabinet.
Substructures in urban areas: In many urban locations, there are multiple utilities in the right-of-way. Paper and electronic research is normally used to create base maps for initial scope development. SoCalGas has also used ground-penetrating radar for verification. Once potential locations are narrowed down, the team completes more invasive examinations, such as potholing or slot trenching, to ensure proper placement of vaults and valve assemblies.
At times, SoCalGas has to contact other utilities to determine if conflicting substructures can be relocated. Some substructures require significant space to maneuver around, such as large oil pipes or storm drains. In those cases, it’s easier just to find another location.
Permitting and compliance: Depending on the location, many entities could have a stake in securing permits for valve automation projects. For one project that is adjacent to Los Angeles International Airport, SoCalGas had to secure permits from the city of Los Angeles, L.A. Metro, the L.A. Department of Transportation, L.A. World Airports (the airport manager) and the FAA – the process took nine months.
Dennis Bragin, PE from the Bureau of Engineering in the Los Angeles Department of Public Works, said he appreciated the coordination this project requires.
“SoCalGas and its contractors have been very diligent in executing the permit for this valve automation. This project is crucial to public safety, and it was important for the permitting process to be thorough, yet expedient,” he said.
Public relations and community outreach: Construction projects in urban areas draw interest – and at times complaints about traffic, noise and disruption – from a range of sources: commercial property owners, government agencies, homeowner associations and neighboring residences, to name a few. Effective outreach and communication with the community and elected officials goes a long way toward mitigating problems. It’s critical to know who’s involved early on and to stay in constant contact with all parties.
Lisa Ann Rapp, public works director for Lakewood, CA, said she was pleased with the outreach efforts on recent PSEP valve automation projects.
“The work was particularly challenging because all three projects were on a very busy street and they were long in duration – several months each,” she said. “The PSEP team did a very good job notifying businesses and residents on what was being done and why. The community appreciated that information, knowing it was all about public safety.”
Urban settings often are subject to external factors beyond a utility’s control. For example, California Assembly Bill 1937, which became law Jan. 1, 2015, requires gas utilities to provide at least three working days’ notice to all schools and hospitals within a 500-foot radius of any non-emergency excavation or construction related to gas pipelines, even potholing. This law, of course, does not apply only to urban locations, but the notification generally poses fewer problems in a rural area.
Further complicating matters are conflicting rules in different cities at the same location (for example, a city on one side of a street could require only day work, but another city across the same street could want only night work, requiring lengthy negotiations to reach a compromise acceptable to all).
Author: Rick Phillips is the senior director for SoCalGas and San Diego Gas & Electric’s Pipeline System Enhancement Plan (PSEP), a multibillion gas transmission pipeline rehabilitation project. In his leadership role on PSEP, he put in place a program management organization, as well as a project execution organization. Prior to his current role, Phillips led a team of company personnel and contractors on an enterprise-wide technology upgrade program. He holds a bachelor’s degree from the University of California, Irvine.
Comments