March 2018, Vol. 245, No. 3
Features
Minimize Corrosion Reduction in Power Distribution
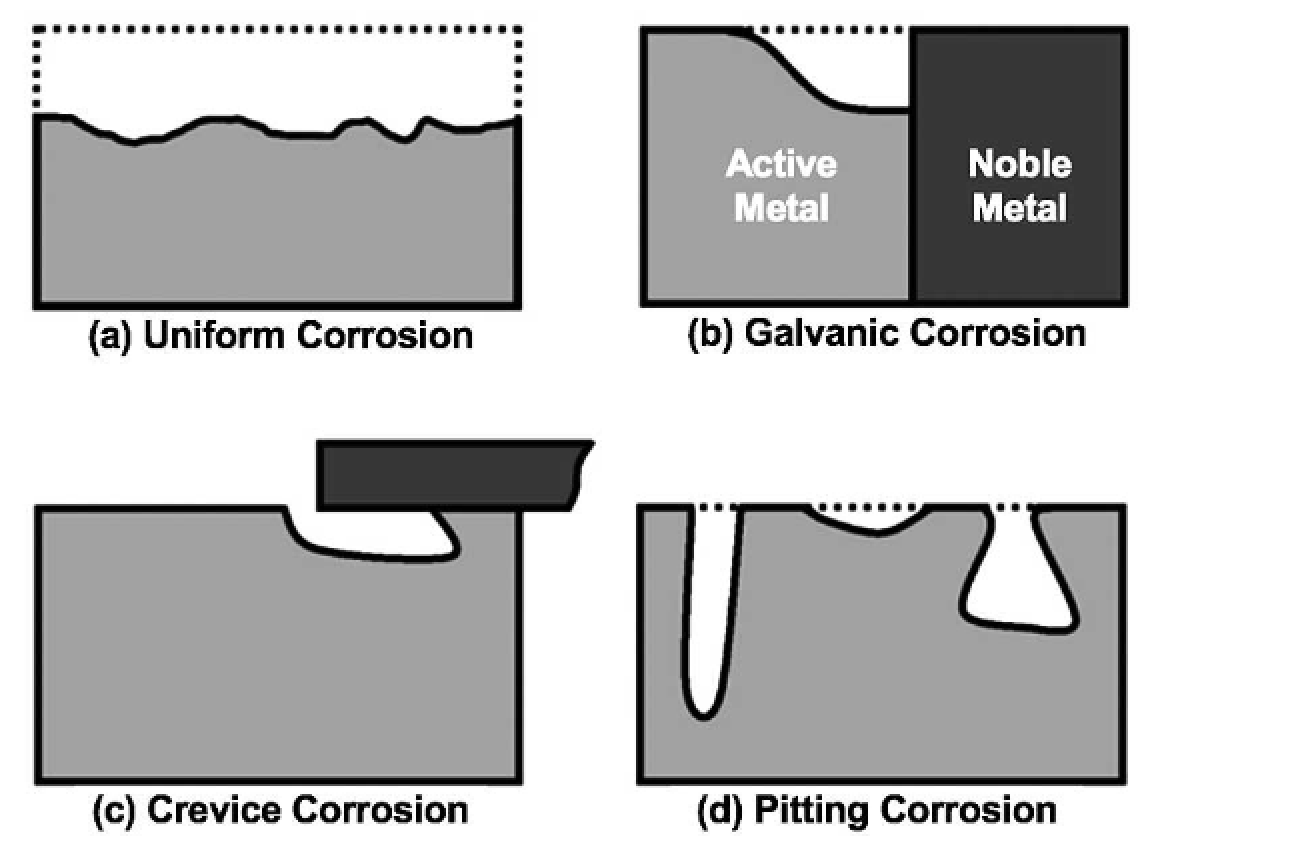
We have all experienced corrosion in the form of rusting bridges, road salt corroding aluminum wheels and rusting our vehicles. These same corrosion processes occur in power distribution equipment, especially in offshore or near-shore locations, with the potential for causing catastrophic failures. Corrosion is a naturally occurring process that affects virtually all metals, though at different rates.
Corrosion can be a cosmetic issue, but most likely will always affect the function of a device/part/component in a negative way. Power distribution systems not functioning as designed may result in significant safety or performance concerns.
Corrosion can never be stopped, but the rate of corrosion can be slowed down through the selection of proper materials including selection of base materials and coatings. Additionally, a robust maintenance program will help evaluate when corrosion has affected critical functions that can be addressed prior to safe operations being compromised.
Corrosion Basics
Corrosion is the reaction of a metal with its environment, usually in a destructive manner. The corrosion reaction is a chemical and/or an electrochemical process of converting the metal to an oxide, hydroxide or sulfide.
Understanding the underlying cause of corrosion will help minimize the destructive process, save money, time, and most importantly maintaining the intended safe operation of the equipment. An understanding of the basic types of corrosion will help specify and select the best corrosion protection scheme for the specific pieces of equipment. The different forms of corrosion that can be readily found in power distribution systems.
(a) Uniform corrosion
(b) Galvanic corrosion
(c) Crevice corrosion
(d) Pitting corrosion
A. Uniform corrosion, or general corrosion, occurs where the environment has similar access to all locations of the exposed metal surface, and the resulting corrosion is evenly distributed over this surface at a consistent rate.
It is the most common form of corrosion and is especially visible. Over time, uniform corrosion will eventually result in product failures impacting performance and safety.
B. Galvanic corrosion, sometimes referred to as bimetallic or dissimilar metal corrosion, occurs when two metals are in electrical contact in the presence of an electrolyte conductive solution.
C. Crevice corrosion occurs in small sheltered gaps or cracks. Corrosion can proceed in a crevice formed between two metal parts, between a metal and a non-metal part, or due to a design flaw.
D. Pitting corrosion is very similar to crevice corrosion in that it is a localized attack. A drop of corrosive fluid or even water will create a localized galvanic cell where the center of the droplet is the anode with potentially a very large cathode.
This localized area will start to corrode and eventually develop into a pit. Once the pit forms it acts as a self-serving crevice and corrosion can progress rapidly, inducing the same chemical mechanisms as described above in crevice corrosion
Monetary Effects
Corrosion is one of the largest single expenses in the U.S. economy, yet it rarely receives the attention it requires. The annual cost of corrosion globally is estimated to be $2.5 trillion per year. This figure is based on a calculation method used by the National Association of Corrosion Engineers (NACE), using a fixed percentage (3.4%) of the GDP.
This cost includes only direct costs as indirect costs related to safety or environmental consequences are difficult to measure. However, these costs should still be considered in the overall corrosion preventative strategy.
In a recent study conducted by the executive branch and Government Accountability Office (GAO), researchers found that by preventing corrosion instead of treating it as it happens, the annual cost of corrosion could be reduced by as much as 40%.
Using corrosion control practices provides a cost benefit as well as avoids failures that can result in catastrophic events.
Corrosion Costs
Although costs differ in relative significance from industry to industry, several generalized elements combine to make up the total cost of corrosion. The highest costs of corrosion are business interruptions that occur when equipment and assets fail to perform as intended.
Direct costs will include costs that are directly related to corrosion and can be placed into two main categories:
The design, manufacturing and construction costs include material selection, protection technologies and costs related to labor, equipment and overhead. In addition, there is corrosion management, which has related costs including:
- Corrosion-related inspection
- Corrosion-related to maintenance
- Repairs due to corrosion damage
- Material costs related to replacement of corroded components
- Labor costs related to replacement of corroded components
- Inventory costs for backup material
- Rehabilitation and refurbishment
- Indirect costs such as environmental cleanup, litigation costs and downtime/loss of production
Corrosion by Industry
According to a study conducted by Electric Power Research Institute of the United States (EPRI), more than half of all unplanned power outages are due to corrosion. This falls in line with several other studies that have shown generally half of all failures within an industry segment tend to be corrosion-related.
According to a 2002 study conducted by the U.S. Federal Highway Administration, the top five industries affected by corrosion are utilities, transportation, production and manufacturing, government, and infrastructure.
In this study, the U.S. GDP from 1998 ($8.79 trillion) was used. The US GDP for 2013 was $16.77 trillion. By using the calculation method from NACE of 3.4%, the direct cost of corrosion in the U.S. is roughly $570 billion.
Available Solutions
Proper specification and selection of electrical products in highly corrosive environments will reduce long-term cost and reduce risk of failure. Several decisions need to be made when selecting electrical equipment that will be subject to corrosion. These decisions include answers to the following basic questions:
- Where will the equipment be placed, and what corrosive elements are most likely to be present?
- What types of material finishes and coatings are available in the equipment that can slow down the corrosion process?
- What equipment design options are available that can be selected in the specification process to aid and extend the corrosion free life cycle of the equipment?
- What is the recommended maintenance of the equipment selected for installation, and is there a robust maintenance program available to ensure said maintenance is implemented?
Equipment Placement – Placement of electrical distribution equipment is a significant factor in warding off elements of corrosion. Choosing a location that is protected from elements of wind, rain, excessive vibration and exposure to corrosive chemicals is a best first defense in corrosion resistance.
Material Finishes – Vast improvements have been made in materials, coatings, and finishes in recent years. Conduit outlet bodies, cable and cord fittings, junction boxes and enclosures, motor control and circuit breakers, local control stations, panel boards, switches, luminaires, and plugs and receptacles can be made available from fiberglass-reinforced polyester materials, from low-copper (less than 0.1%) aluminum, from ferrous and malleable irons, from different grades of stainless steel, and from engineered plastics.
Base Material Selection – Ferrous iron, for example, offers great strength and is economical. Ferrous cast irons, when electrochemically coated with a deposit of zinc plating or a hot dip galvanize finish, will resist the corrosive effects of alkalis, many organic compounds, neutral and slightly acidic solutions, and chemically neutral brines.
Aluminum, when its alloy contains a minimal amount of copper of less than 0.0004%, will resist marine atmospheres, sulfur gasses and ammonium nitrate. Limiting the copper content in aluminum will stave off corrosion due to galvanic action.
PVC Coating – Polyvinyl chloride (PVC)-coated galvanized rigid steel conduit systems provide excellent structural strength as well as superior corrosion protection. When properly adhered, the coating is able to withstand environmental elements such as sunlight exposure, extreme temperatures, humidity, salts and acids.
PVC-coated GRC also has the widest range of use where pH levels and chemical resistance are concerned. In areas where weight is a concern, PVC coated aluminum is an option. In order to validate product performance and safety look for third party listings from organizations such as ETL and UL.
Fiberglass – Certain fiberglass reinforced polyesters are specifically formulated for use in the harshest corrosive environments. Stainless steel has a high resistance to rust, and numerous grades of stainless steel are used in Industry.
Preventive Maintenance
1) Corrosion Preventative Strategies: By creating a corrosion prevention strategy, organizations are able to properly implement corrosion prevention technologies and strategies, which will lead to overall cost-savings as well as implement design practices that increase reliability and safety, conserve materials and energy, and reduce costs.
Preventive strategies in non-technical areas:
- Increase awareness of the considerable corrosion costs and potential savings.
- Change the misconception that nothing can be done about corrosion.
- Change policies, regulations, standards, and management practices to increase corrosion cost-savings through sound corrosion management.
- Improve education and training of staff in recognition of corrosion control.
Preventive strategies in technical areas:
- Advance design practices for better corrosion management.
- Advance life prediction and performance assessment methods.
- Advance corrosion technology through research, development, and implementation.
2) Inspection and maintenance program: Using the preventive strategies, a basic inspection and maintenance program can ensure equipment is operating properly and that any corrosion is addressed prior to failure.
Corrosion never stops. Most metals are mined as ores (oxides, sulfides, carbonates, etc.) and are processed into the metals we use in our electrical distribution systems.
Every year, day, minute and second these metals are trying to return to their most stable state: the ores from which they were mined – this is the corrosion process. Corrosion is most readily revealed as an aesthetic issue, but can quickly progress to a state when intended function is compromised.
While the science of corrosion is quite well known and understood, limiting the impact of corrosion is much more of an art. Understanding the underlying principles of corrosion along with the equipment to be protected, the installation environment and the risk of product failure will help to prescribe an appropriate corrosion protection scheme composed of material selection, coating selection, and sheltering equipment.
Equally important to the proper corrosion protection scheme is a robust maintenance program. Preventative maintenance will ensure your equipment is functioning as designed as well as provide early indication of potential product failures limiting unplanned outages. P&GJ
Authors: Jesse W. Taylor is a senior advanced chemical engineer at Eaton. He is responsible for developing new technology platforms, and assists new product development and sustaining efforts from a chemistry perspective. Taylor earned a Ph.D. in inorganic chemistry from Syracuse University, Syracuse, NY and a B.S. from Hartwick College, Oneonta, NY.
Kenneth W. McFarland has been with Eaton for 37 years and currently a field application specialist with Eaton’s Crouse-Hinds, responsible for major project specifications in the western United States with engineering procurement contractor (EPC) businesses. He holds a bachelor’s degree in in business administration-marketing from San Jose State University, San Jose, CA.
Stephanie Ellis is the marketing manager for Robroy Industries and has been with the organization for seven years. She also acts as director for Corrosion College. Ellis holds a bachelor’s degree from Stephen F. Austin State University, Nacogdoches, Texas, and holds a corrosion technologist certification from NACE.
Comments