March 2018, Vol. 245, No. 3
Features
Not Your Ordinary Run of the Mill
Tenaris unveiled its $1.8 billion state-of-the-art seamless pipe mill in Bay City, Texas, recently before local, state and federal representatives, including U.S. Department of Energy Secretary Rick Perry and Texas Governor Greg Abbott. Tenaris customers, community members and employees also joined the ceremonial launch.
The 1.2 million-square-foot mill incorporates a high level of automation and cutting edge technologies into its production of seamless pipe. The facility is also the company’s most environmentally efficient mill, seeking LEED certification.
Tenaris President Luca Zanotti talked to P&GJ about what sets this facility apart.
P&GJ: What sets this pipe mill apart from its competition?
Zanotti: Tenaris’s new Bay City mill is the most sophisticated, productive and environmentally efficient mill in the world. The 1.2-million-square-foot facility is equipped with cutting edge technologies and a high level of automation that is integrated into its production process to optimize safety and efficiency. The mill has the capacity to produce 600,000 tons of oil country tubular goods (OCTG), annually.
P&GJ: Can you explain the production process?
Zanotti: The manufacturing of seamless pipes involves the transformation of solid steel billets into pipe, which are pierced, heated and stretched to desired lengths, before being finished (threaded, tested for quality), prepped and delivered to customers.
What really drives this type of product is the environment – the nature of the reservoir in which the well is being drilled and also well depth is critical. Some of the benefits of using seamless pipes are their ability to withstand and perform reliably in demanding conditions where there is, for example, high pressure, high temperatures, corrosion or other possible complex conditions that require a higher steel grade used in the manufacturing of seamless pipe.
Tenaris produces welded and seamless pipe in both API steel grades and proprietary grades to enhance the pipes’ performance. Tenaris’s mill will produce seamless OCTG for the oil and gas sector, mainly casing and line pipe.
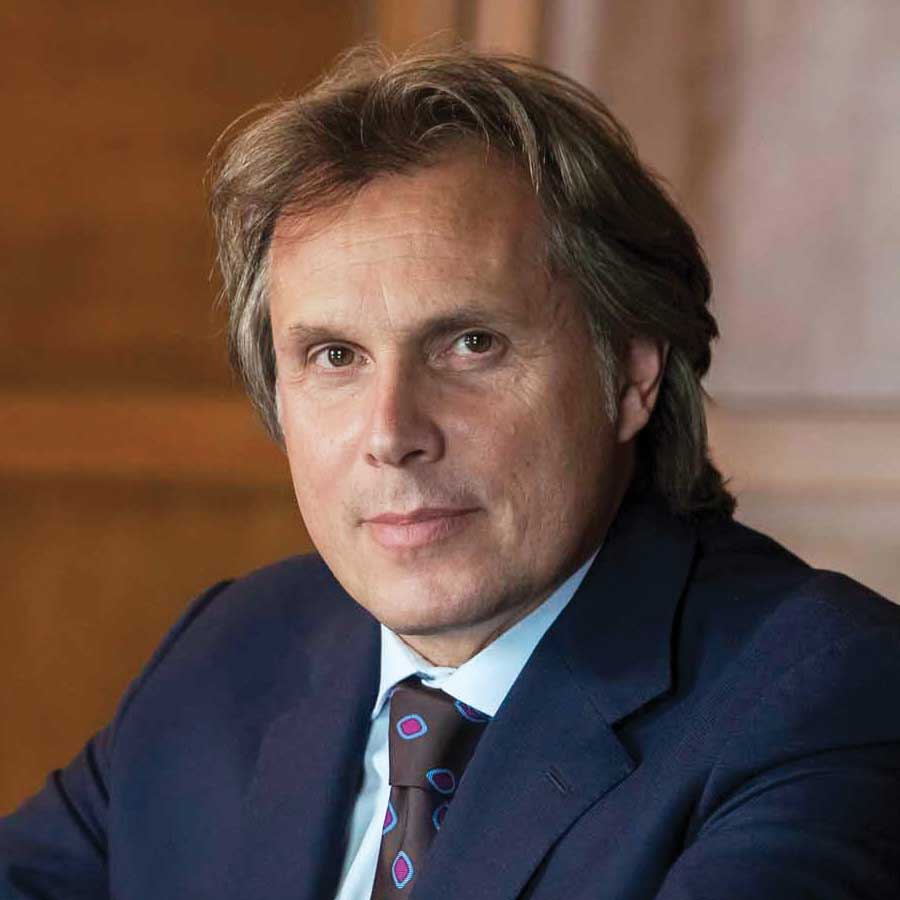
P&GJ: What is your outlook on the future of U.S. oil & gas?
Zanotti: We continue to see the market strengthening and recovering from the historic downturn with stronger oil prices, an active rig count and overall, through gains in efficiency and technological improvements the industry achieved over the past few years. This has been a remarkable transformation.
Demand for OCTG is recovering. The largest market for these products is the U.S., and Tenaris is currently ramping up its new seamless pipe mill in Bay City, as well as other facilities, domestically and globally. The level of unfairly traded imports is a factor to consider in the recovery for the tubular sector. Korea alone imported more than 20% of the OCTG market in the U.S. in 2017 – the equivalent of about 1.1 million tons of pipe. If the import numbers decrease, there will be space and need for more domestic manufacturing of pipe products, and Tenaris is ready to respond with increased capacity.
P&GJ: How significant is the location of this business to your facility?
Zanotti: Tenaris’s new mill manufactures OCTG to serve the growing U.S. shale market. Beyond its products, the mill reinforces our direct-to-customer business model known as Rig Direct and our vision of how the tubular sector should effectively operate.
Through this model we have better visibility of our customers’ drilling operations, and we can provide them with the right quantity of high quality products, and services. The new mill is strategically located near the most active shale plays in the U.S.
Our mill in Bay City also has an onsite service center; pipe produced from the mill is shipped directly to customer rig sites or stored at our service centers in Freeport, Midland and Oklahoma City. With the new plant and our growing service infrastructure, we can efficiently meet our customers’ on-demand pipe needs.
P&GJ: How does the square footage of this plant compare to conventional plants designed to produce a similar amount of pipe?
Zanotti: What sets Tenaris Bay City apart goes beyond its square footage. The company has leveraged and integrated automation across its footprint to ensure the safety of employees, the efficient flow of processes at the mill, the quality and traceability of our products throughout the entire manufacturing process and short delivery time. This is a plant designed with safety and the environment at the forefront and that optimizes efficiencies in production.
P&GJ: Can you describe the robotics technology and its advantages?
Zanotti: This is a modernized mill with robots and automated machines that move products throughout the facility. The digitalization built into each process ensures the safety of our operators, superior working conditions, and the efficiency in production, reducing time and costs overall.
The mill’s equipment requires a highly skilled workforce. We have an internal program to help train new talent joining the company as well as a partnership with the local college’s manufacturing technology program. The program helps raise awareness and interest in working in the industrial sector. This is a terrific partnership and some graduates of the program have joined our team in Bay City.
The use of technology extends to our service centers where we have a digital tracking system called PipeTracer™ to trace and track each pipe produced at our mills, automating the management of pipe inventory. Our pipes have a QR code that our customers can scan to view product information such as the pipes’ OD, length, and other mechanical characteristics. This is all digital – no paper.
P&GJ: What market need did Tenaris recognize and answer with this $1.8 billion investment?
Zanotti: We are a company with a long-term vision. Before the downturn, and following nearly $8 billion in investments in the U.S., Tenaris made the decision to deepen its presence and build its first green field project – a seamless pipe mill in Bay City, Texas, to better position Tenaris in the U.S., the largest market for OCTG. Prior to this investment, we had domestic welded capacity but not seamless.
The new mill allows Tenaris to better serve its customers with a complete product portfolio of both welded and seamless solutions. The new mill is also the anchor to our growing Rig Direct® business model of delivering our products and services directly to our customers and in sync with their drilling operations. P&GJ
Comments