December 2019, Vol. 246, No. 12
Features
Reducing Risk At Compressor Stations Through Gas Flame Detection
By Patrick Enroth, Gas Applications Manager and Bill Crosley, Systems Product Manager, Det-Tronics
Natural gas is transported via a network of over 2 million pipeline miles (nearly 3.3 million km) spanning 130 countries across the globe. The movement of natural gas through pipelines requires re-pressurization approximately every 40 to 70 miles, depending on the region and conditions.
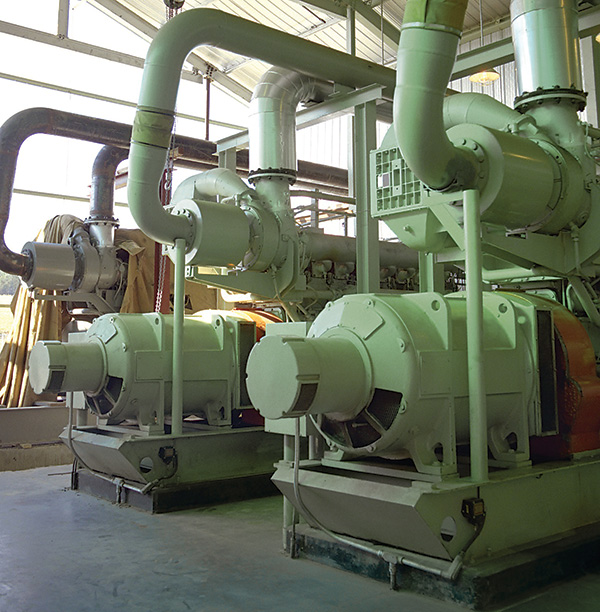
These pressure boosts compensate for pressure losses that occur in the pipes when natural gas travels long distances, and they are accomplished at compressor stations housed either inside a facility or outdoors.
While performing this vital re-pressurization, the equipment at compressor stations is subjected to considerable mechanical and thermal stresses, which wear down compressor components and make them prone to leaking.
As a result, compressor stations are a significant source of fugitive greenhouse gas emissions, producing over 50 Bcf of methane emissions annually from leaking compressors and components such as valves, flanges, connections and open-ended lines, according to estimates.
Since compressor stations are often located in remote, sparsely populated areas, many of them are unattended. This means leaks of combustible gases can potentially go unnoticed, and fire can go undetected for extended periods of time.
At manned compressor stations, toxic gases can pose dangers to life and health. Natural gas often contains significant amounts of acidic gases such as hydrogen sulfide (H2S), which is considered immediately dangerous to life and health (IDLH) at levels of 100 ppm and higher by the Occupational Safety and Health Administration (OSHA).
Detection Standards
Automated gas leak detection was found to be the top passive method of fire protection used at North American compressor stations, according to a comprehensive survey of station owners, conducted by Solomon Associates, a Dallas-based business-management consulting firm. Reliable gas leak detection and fast flame detection are two methods for protection against fire-related catastrophes at compressor stations.
The United States natural gas pipeline industry follows Department of Transportation (DOT) guidelines for minimizing safety risks at compressor stations. DOT Document 49, CFR, Part 192, prescribes minimum safety requirements for pipeline facilities and the transportation of gas.
When dealing with fire and toxic gas-related risk, the most widely used U.S. standards come from the National Fire Protection Association (NFPA). Many NFPA codes and standards for specific processes reference NFPA 72, the National Fire Alarm and Signaling Code. Chapter 17 of NFPA 72 provides requirements for various types of detectors that can be used to spot indications of fire and toxic gases or vapors.
The best way to know that detectors meet safety standards, such as those in NFPA 72, is to specify equipment certified by an accredited third-party testing laboratory and certification body to perform in hazardous areas and in environments where it is intended to be installed.
Properly accredited third-party testing and certification provides potential users with an independent and unbiased product evaluation. For example, FM Approvals 3260 is the performance standard for optical flame detectors, and FM 6310 and 6320 are performance standards for combustible gas detectors – all of which provide independent validation of the manufacturer’s performance claims.
Detection Technologies
NFPA 72 describes a gas detector as “a device that detects the presence of a specified gas concentration.” A gas detection system should be capable of giving an early warning of both the presence and the general location of an accumulation of flammable gas or vapor. In addition, advanced gas detection systems offer intelligence that allows diagnostic functions, historical data logging and communications.
Fixed point detectors should be used for both combustible gas and toxic gas detection. Employing electrochemical, catalytic or infrared (IR) technology, these detectors activate when they come in contact with combustible or toxic gases and measure the gas concentration at the point where they are located.
Since fixed point detectors must come in contact with a gas to detect it, their performance can be limited by environmental factors such as wind, rain or indoor ventilation systems. If a compressor station is an open-air facility, for example, wind can cause point-type gas detectors to miss leaks.
Another combustible gas detection technology used at compressor stations is line of sight (LOS). Many LOS gas detectors emit an IR light source to continuously monitor combustible hydrocarbon gas concentrations between two points that can be over 100 meters apart. Besides offering long-range protection, LOS systems can be calibrated for a specific hydrocarbon gas, such as methane. LOS combustible gas detectors can offer an additional layer of detection to augment fixed point combustible gas detectors that may be challenged by environmental conditions previously mentioned.
Unlike point detectors, LOS detectors do not need to be in direct contact to detect gas; however, the gas cloud must intersect the light beam. Moreover, this path must be clear of obstructions for LOS detectors to work properly. LOS detectors are not capable of measuring gas concentrations within the lower explosive limit (LEL) but rather provide a 0–5 LFL-meters concentration, which is the product of gas cloud concentration and length (LFL-meters). Therefore, this technology cannot distinguish between a smaller combustible cloud of gas and a larger non-combustible cloud. This LOS technology limiting factor, along with it being incapable of pinpointing a leak location, makes LOS detectors ideal for pairing with fixed point detectors.
As with all applications, LOS detectors for compressor stations should be designed to withstand heavy vibration and other harsh conditions. Features to look for include high misalignment tolerance, large-area coverage, failsafe operation, low maintenance and infrequent calibration requirements.
A third gas-detection option for compressor stations is acoustic technology. Acoustic detectors work by recognizing the unique “sound fingerprints” of high-pressure gas leaks. Unlike point and LOS technologies, which require gas plumes to move to active sensing regions, acoustic leak detectors can respond almost immediately to a pressurized gas leak, limited only by the speed of sound.
Acoustic detection capabilities are not compromised by wind or rain (making them suitable for harsh outdoor applications and unmanned operations), or obstructions. Acoustic gas leak detectors offer a possible third layer of protection to augment fixed and LOS detectors that may be challenged by environmental conditions previously mentioned.
One downside is acoustic detectors cannot distinguish specific gas types or detect the concentration of the gas being monitored.
All gas detector technologies have limitations that may impact their performance. Therefore, the best way to adequately protect a compressor station is to combine two or more technologies and place detectors in locations that maximize their effectiveness.
Detector Options
There are typically two distinct fire scenarios present in compressor or pipeline protection. The first type is a fast ignition fire, usually caused by pressurized gas leaking from a seal or fitting contacting an ignition source. The fire could grow and impinge upon other pipes and/or machinery creating secondary fires. The second fire scenario is typically caused by an engine failure, which generates a small or momentary fire that may grow until surrounding materials are also on fire.
Flame detectors in these scenarios should have the ability to respond to gaseous and liquid fires over greater distances and to detect partially obscured fires. The flame detectors should also have the ability to respond to small, momentary fires that traditional flame detectors, using time delays of seconds, may miss.
If a fire breaks out at a compressor station despite the presence of gas detectors, the protection system should be able to detect it quickly. Conventional fire protection systems often rely on heat detectors. In open or drafty areas, however, heat from a fire can dissipate, significantly delaying detection by thermal detection equipment, or preventing detection altogether. Even in best-case scenarios, it can take minutes for heat detectors to respond to fires – a delay that can have significant consequences.
Unlike conventional heat detectors, optical flame detectors can respond to fires in seconds. Instead of depending on heat from a fire coming into contact with the sensing element, optical flame detectors detect flame emissions traveling at the speed of light. As described in NFPA 72, these radiant energy-sensing detectors employ IR, ultraviolet (UV), UVIR and multi-spectrum IR (MIR) sensing technologies.
When selecting an optical flame detector, users must match the spectral response of the detector to the spectral emissions of the fires to be detected. Ideally, compressor stations will employ flame detectors with advanced signal processing algorithms that can detect more fire types faster and at substantially longer distances. Today’s trend is to use MIR technology, which provides greater coverage due to increased detection range.
Guidance for the placement of optical flame detectors can be found in Section 17.8.3.2.1 of NFPA 72. This section states that the location and spacing of detectors should be the result of an engineering evaluation that includes the following:
- Size of the fire to be detected
- Fuel involved
- Detector sensitivity and field of view
- Distance between the fire and the detector
- Presence of extraneous sources of radiant emissions
- Response time required
Surveys can also be useful prior to flame detector placement. During such surveys, personnel walk around the station and identify hazardous areas and potential places to mount detectors for adequate coverage. They also look for obstructions that would be in a detector’s line of sight in possible mounting locations.
Proper placement of gas and flame detectors is one way to reduce the chance that detectors will misinterpret non-hazardous situations and activate nuisance alarms, which can cause unnecessary equipment stoppages, downtime and unwanted greenhouse gas emissions related to compressor station emergency shutdowns. Minimizing false alarms is especially important in remote locations where no one is on site to validate whether or not a fire is present.
In addition to giving careful consideration to detector placement, false alarms can be minimized by using multiple detectors to monitor the same area as a way of validating flame detection. To support redundancy, this type of system must include algorithms capable of handling “voting” circuits (with each detector’s interpretation of an event counting as one vote) and making correct decisions based on input from duplicate detectors.
System Control
Along with gas and flame detectors, operators should consider using a control system to facilitate decisions and take action based on detection data. In advanced setups, this control system is third-party approved to monitor detector signals and process those signals to determine the proper response.
The controller is part of a system that includes a variety of input/output modules, displays, switches and status-indicating devices, all of which should be approved for use with the controller. The controller software provides real-time system status and diagnostics and also allows for programming and configuration of gas and flame detectors. The controller should also be capable of communicating fire system information to offsite control systems.
Conclusion
Compressor station owners and operators can significantly reduce fire-related risks to hazardous and remote facilities by deploying a comprehensive gas and flame detection system. When setting up such a system, consider working with professionals who are well versed in industry codes and performance standards, and experienced with compressor station applications.
A comprehensive, robust fire and gas safety system can provide risk mitigation for compressor stations, indoors or out and in the most remote locations.
References:
- Central Intelligence Agency, The World Factbook 2019, Washington, D.C.,
- setxind.com/midstream/compressor-stations-what-how-why/
- United States Environmental Protection Agency, Air and Radiation, “Directed Inspection and Maintenance at Compression Stations,” EPA430-B-03-008
Authors: Patrick Enroth is Gas Applications Manager and has provided technical support to Det-Tronics to customers 2016. He has a bachelor’s degree in mechanical engineering.
Bill Crosley is systems product manager at Det-Tronics and has been with the company for 35 years. He has experience iin interpreting fire and gas codes and standards.
Comments