January 2019, Vol. 246, No. 1
Features
Today’s Oil Patch Success: 'It’s Technology, Stupid!'
By Richard Nemec, Contributing Editor
If you were a fly on the wall of any oil or natural gas company’s quarterly earnings conference calls, you’d get an earful these days about technology and innovation that are driving some extraordinary efficiency and cost-savings gains.
Both exploration and production (E&P), and midstream have their success stories, and the senior executives for operations are not shy about touting seemingly continuing positive results from quarter to quarter, even coming out of a three-year global price depression for oil.
In the midst of the conference call season in November, Marathon Oil Corp. Executive Vice President/COO Mitch Little described the company’s third-quarter decision to “swap out one of our hydraulic fracking crews in the Eagle Ford basin to a different type of service model,” which allowed for more vertical integration of commodities and supplies internally.
“The efficiency side where we’re seeing continued improvement across the basins in terms of pump time or a number of stages completed-per-day drilling efficiencies go hand-in-hand with that, and we continue to pursue opportunities that would expand using things like self-sourcing, and also looking at local or more regional sand sources that have a lower cost of transportation, Little said. “So, it’s really an all-of-the-above strategy, and our teams are intensely focused on the entire capital efficiency equation – both the well performance and well cost sides.”
In reporting strong third-quarter earnings, Houston-based Occidental Petroleum Corp. (Oxy) executives made the same pitch in November, touting unlimited efficiency gains in its favored Permian Basin, both in Texas and New México, where the mid-sized E&P has extensive holdings.
The new Vice President for Investor Relations, Jeff Alvarez, also heads up Oxy’s Permian Operations since senior executive Jody Elliott retired, and he had his own earful, starting with a 24,000 boe/d increase in total Permian production for Oxy in the third quarter, hitting 225,000 boe/d overall for the quarter, a 60% boost from totals in the same period in 2017. Alvarez told a tale of bringing in the international E&P’s highest all-time producing wells in the Permian while setting low-cost, per-well production records.
Alvarez made clear the glowing results came from Oxy’s ability to excel in its subsurface operations and other phases of unconventional well design and production processes.
“These repeatable, record-breaking results are a testament to our subsurface capability,” he said, adding that Oxy in a 12-month (2017-18) period delivered more than half of the best-ever Permian wells. “We continue to see improvements in all areas, and I think when we look at it from a returns and value creation standpoint, the improvements are going to happen for a very long period of time.”
The Mowry and Niobrara shales are in the range of premium return rates with very low development costs, according Houston-based EOG Resources Inc.’s Executive Vice President David Trice, who spoke earlier in 2018 on a quarterly call.
He added that EOG’s share of the plays equals 1.2 Bboe from 875 premium locations using 660-foot spacing with at least half of the resource expected to be crude oil. “The Powder River Basin (PRB) is now ready to become a meaningful contributor to EOG’s future growth.”
EOG executives talked just as bullishly about the midstream gathering and processing infrastructure the company has available or is planning for the PRB. Lance Terveen, senior vice president for marketing at EOG, said there are four processors for liquids-rich natural gas in the operating area “with significant high-pressure gathering systems and back-up systems as contingencies.”
In response to questions from analysts, CEO Bill Thomas cautioned that the real uptick in production volumes in the Mowry and Niobrara shales is not likely until late 2019 and into 2020, because activity will need to be increased earlier in 2019 with the building out of takeaway infrastructure.
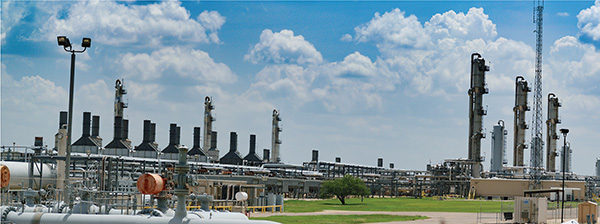
Late in 2018, the U.S. Interior Department reported record revenues from oil and gas development on federal lands in fiscal 2017, increasing by $400 million. Economic output for the first time in several years increased to $292 billion with the number of new jobs increasing by 230,000 to 1.8 million. Five western states were among the top producers of contributions to gross domestic product (GDP) in their jurisdictions: Wyoming ($12.7 billion), Texas ($11.3 billion), New Mexico ($10.1 billion), California ($5.7 billion and Colorado ($5.6 billion).
In the midstream sector, similar types of advanced technology and process improvements take place daily in pipeline, compressor stations and other related infrastructure in the oil and gas space. The industry rarely talks about them, except for forums like the quarterly earning calls.
At the Virginia-based Pipeline Research Council International (PRCI) and its Houston-based laboratory, corrosion prevention and methane detection are ongoing focuses. One of hundreds of research projects has helped develop a multi-phase project resulting in a simplified portable analyzer emission test method for measuring NOx and CO emissions from natural gas-fired combustion sources, such as compressor engines.
While somewhat arcane, these research efforts eventually lead to equipment, processes and materials that help elevate safety and reliability levels. This year, PRCI completed a study of mitigating soil-side corrosion on the bottom plates of above-ground petroleum storage tanks, addressing a major maintenance focus of tank operators. It looked at so-called vapor corrosion inhibitors’ (VCI) effectiveness in preventing corrosion to a level comparable to cathodic protection systems for tank bottoms, concluding that the VCIs are “clearly comparable” to cathodic protection.
Industry research organization Gas Technology Institute (GTI) is working on a multitude of projects to quantify and mitigate methane emissions from various sources and identify opportunities for reduction in greenhouse gas emissions. Advanced technologies for methane capture from gas operations such as transmission compressors and upstream efforts are under development. GTI is serving as the program administrator for the Collaboratory for Advancing Methane Science (CAMS) to better understand global methane emissions.
The consortium was created by leading energy companies, Cheniere, Chevron, Equinor, ExxonMobil, and Pioneer Natural Resources, and the new industry-led collaborative research consortium will pursue scientific studies addressing methane emissions along the natural gas value chain, from production through end use. Studies will deliver factual data that can be used to inform regulations and policy development and communicate findings to the general public. A research study to develop a model or methods for improving understanding of spatial and temporal regional methane emissions profiles with a focus on oil and gas sources in key basins will begin in early 2019.
To support gas company staff and other stakeholders in making major operational and repair vs. replacement decisions, GTI developed an Enterprise Decision Support System (EDSS) that integrates gas-system data and knowledge from various sources into a single information platform that addresses all aspects of natural gas distribution and transmission system operations. Researchers are also creating advanced risk assessment and mitigation models that apply to underground storage, complex pipeline risk assessment, and LNG
(GTI), Southwest Research Institute (SwRI) and corporate research at General Electric have developed a way to recover heat from simple-cycle gas turbines used in pipeline compressor stations or used in large-scale liquefied natural gas (LNG) compression and regasification operations. GTI, SwRI and GE have developed an early commercial version of a supercritical carbon dioxide (sCO2) technology.
This is how GTI’s John Marion, senior program director, explains the research tie-ins to gas pipeline and processing applications:
“The early commercial entrant application of supercritical carbon dioxide (sCO2) cycles today is waste heat recovery from small simple cycle gas turbines, such as those used for gas pipeline compressor stations (example: Echogen, Siemens-Dresser). These typically have no heat recovery or heat recovery, such as by ORC [organic Rankine cycles] is not feasible. Applications to gas processing where there may be high energy demands, such as for LNG compression and/or regasification are also possible. Also, the compact nature and environmentally robust (non-freezing) nature of sCO2 systems has drawn interest in offshore platform and ship applications.”
GTI also has been involved in advances in fracking processes that continue unabated because of ongoing programs such as fracking test sites in the Permian Basin’s Delaware and Midland sub-basins.
In January 2018, GTI was awarded funding from the U.S. Department of Energy National Energy Technology Laboratory (DOE/NETL) for cost-shared research and development on hydraulic fracturing efficiency. Anadarko Petroleum Corp. and Shell Exploration and Production Co. agreed to co-host a new field test site in the Delaware where multiple experiments to evaluate well completion, optimize design and quantify environmental impact are being carried out. Work was set to start in late-2018 at an Anadarko-operated location, and other industry partners have been invited to join the project.
The new HFTS2-Delaware field test site located in Block 55 T1, Loving County, Texas, will feature different depth, pressures, and permeability than the site of GTI’s first collaborative project, HFTS1–Midland. Each location requires specific techniques for optimal production based on local geologic complexity.
In Colorado’s plentiful Denver-Julesburg (DJ) Basin experienced a steady upswing in oil and gas production in 2018 and ushered in an increased thrust in new and upgraded midstream infrastructure. This came after the state’s voters soundly defeated an anti-drilling ballot measure (Proposition 112) that would have stifled new oil, gas development statewide.
“While it’s impossible to forecast market conditions with any certainty, the economics and technology around oil and natural gas development are healthy, so we can likely expect additional Colorado-based infrastructure investments heading into 2019,” said Dan Haley, CEO of the Colorado Oil and Gas Association (COGA). “Those investments are key, so that we can stay ahead of capacity constraints and not limit our opportunities for success.”
In the DJ, Extraction Oil & Gas Corp. CEO Mark Erickson said he anticipates “years of development” with what his E&P has designated as its “Hawkeye” area, taking in Niobrara Shale and some of the Codell Sandstone area. In a recent quarterly conference call, he called it “highly delineated” with 30 wells that have demonstrated production results “on par with the best wells in the DJ.” In late 2018, he was envisioning up to 1,000 horizontal well laterals in the area at an all-in cost of $75/acre.
Extraction, which launched as a public company in 2017, has seen a surge in its Colorado operations and has predicted enhanced drilling techniques would help deliver double-digit growth this year. “We expect this project to generate solid well economics and strong full-cycle returns,” he said. Extraction currently has about 160,000 acres in the core of the basin, and another 155,000 acres in the northern extension of the DJ.
With natural gas production topping 5 Bcf/d in the Niobrara formation of the Rocky Mountains, including the PRB of Wyoming and the DJ Basin of Colorado, the region is becoming a new center for infrastructure build-out, aided by various technology innovations and advances. Both of the basins are targeted for additional processing plant and pipeline capacity, according to RBN Energy LLC’s Housley Carr, who discussed the growth in a November blog post.
In the U.S. Energy Information Administration’s (EIA) latest Drilling Productivity Report issued in November, Niobrara gas production in December 2018 is expected to climb month/month (m/m) to an estimated 5.19 Bcf/d from 5.15 Bcf/d. Niobrara oil output is forecast to increase m/m to 671,000 bpd in December from 664,000 bpd. With “major crude oil-focused PRB and DJ Basin producers planning for expanded crude output in 2019 and beyond, production of associated gas is expected to continue rising,” Carr said.
In North Dakota, where the Bakken Shale makes the state the second-largest oil producer nationally with more than 1 MMbpd production, the state’s veteran chief oil and gas regulator, Lynn Helms, director of the state Department of Mineral Resources, is convinced local operators’ grasp of technological advancements and process innovations is ahead of the rest of the U.S. basins. He insists that the Bakken is further along the technology curve than other U.S. shale basins, and it has remained “cutting edge” in its technology applications, such as fracking techniques, lateral length, and the speed in drilling laterals.
Even in just the last six months [of 2018], “productivity of wells is significantly better now,” said Helms, citing drilling by an operator in Mountrail and southern Burke Counties that has drilled some extended (2.5- to 3-mile) lateral wells, resulting in production rates that Helms said were up to three times greater than the usual rates in the area.
“It is encouraging that the Bakken continues to maintain its place as No. 1 or No. 2 [nationally] in productivity-per-rig,” said Helms, while also acknowledging that the Bakken still must compete against both the Permian and Anadarko basins, where there are a lot more leaseholds still to be acquired. He thinks once those basins reach a similar level of maturity to that of the Bakken, some of the operators may bring more investment dollars back to North Dakota where they can “make more money for every dollar invested.”
Laterals beyond two miles are starting to multiply in non-core parts of the Bakken, Helms said, noting that in the five-county core the two-mile laterals are still the norm. In addition, the newest drilling rigs are capable of what Helms called “incredibly fast drilling times,” even in the longer laterals. Statistical analyses by North Dakota’s state engineers have shown that newer wells drilled today are much more productive in their seventh month of operation, compared to wells at a similar interval six years ago.
“Compared to a 6-year-old well on average, wells now produce about 70,000 barrels more in the seventh month of their life,” Helms said.
In recent years, the continuing bullishness surrounding Bakken development, industry players say, is driven by technology advances and innovation described at annual meetings of the North Dakota Petroleum Council (NDPC). Advances in fracking, enhanced oil recovery (EOR) and resource assessment technologies are common among the list of the prospects outlined during presentations by experts and state officials.
“The Bakken doesn’t just contribute oil, it provides the drive to innovate,” according Charlie Gorecki, director of subsurface research/development at the North Dakota Energy and Environmental Resource Center, speaking at the NDPC’s 2017 annual meeting.
While only a small percentage of the overall Bakken resource base is recoverable today, many producers have begun recompleting older wells, also known as refracks, using updated drilling techniques. Refracking wells in the Bakken, considered a prime location for completions, should unlock more production, particularly for EOR. Operators such as QEP Resources moved into refracking in the Bakken using a program that had earlier yielded success in the Haynesville Shale.
Houston-based Anadarko, a super-independent with serious stakes in the Permian, DJ and PRB, cited “next generation technology development and systems solutions” for being able to slash its capital expenditure budget for 2019 while predicting higher production levels at 260-270 MMboe.
In the Eagle Ford in Texas and elsewhere, the drilling rig specialist Helmerich & Payne Inc. was gearing up in 2019 for increased interest in its super-spec FlexRigs for operators that are increasing lateral lengths and doubling down on the use of pad drilling. Helmerich CEO John Lindsay was telling analysts in November that the U.S. market for super-spec rigs was fully used, however, he was predicting additional demand for the advanced technology in the oil patch.
Out of the DJ Basin to the north, Wyoming-based Titan Casing, an affiliate of the E&P JCA Companies, reported on the results of its partnership with one of Colorado’s largest E&Ps and Ensign USD to advance oilfield safety and environmental protections by using drilling rig hydraulic systems to operate casing power tongs in place of diesel-powered hydraulic power units at drill sites. Titan officials claim the adjustments have advanced safety, economics and environmental protections.
Noting that the carbon footprint of the drilling operation is greatly lowered with the absence of diesel use, Titan Vice President Erik Rodriguez said his company has “put countless hours of research and development into making this system efficient and safe. We have changed all hydraulic valve banks to create a closed loop system.”
One factor seems abundantly clear about the future of oilfield and midstream development – change will be constant, and operators will have to adapt and innovate or deal with the adverse consequences of not doing so. Maintaining status quo won’t be an option. P&GJ
Richard Nemec is a Los Angeles-based P&GJ contributing editor who can be reached at rnemec@ca.rr.com.
Comments