January 2023, Vol. 250, No. 1
Features
How Geogrid Advancements Can Benefit Pipeline Operators
By D. Scott Phillips. Professional Engineer (PE), Tensar
(P&GJ) — Since the first gas well was drilled in the U.S. in 1825, there have been many advancements in technology and engineering to make the capture and pipeline transportation of oil and gas better and more efficient. These advancements have resulted in now-industry standard methods such as hydraulic fracturing, horizontal drilling, 3-D seismic imaging, and many more.
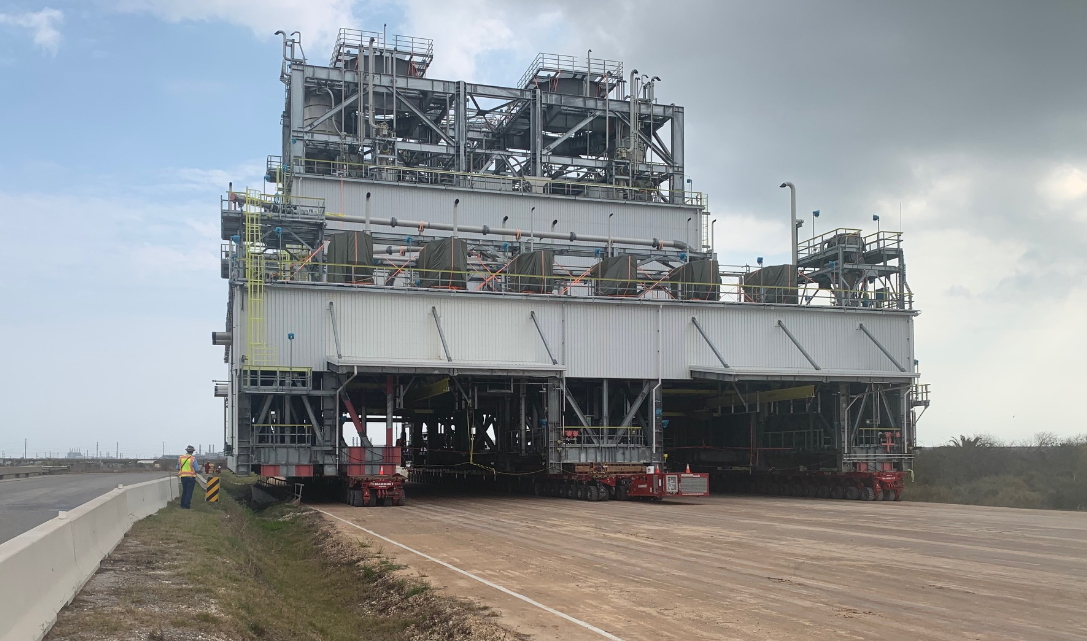
Just as advancements have been made in technologies to acquire oil and gas, so have the methods used to construct and maintain these essential operations. Reliable, high-performance structures like berms and aggregate surfaces used for well pads and pipeline access roads are of tremendous importance to keep any operation running smoothly.
In the case of large berms, their performance if ever needed is an important part of environmental safety. Poor soils, weak subgrades, and harsh weather or environmental conditions can make the construction and maintenance of sites and facilities more difficult, dangerous, and costly.
However, tremendous advancements in geogrid technology have allowed significant improvements to these surfaces so they can support much heavier loads, require less maintenance, and perform for far longer periods of time.
What Are Geogrids?
Although geogrids have been around for more than 45 years, how they are used and how their technology has advanced over the decades may not be widely known. Geogrids are made of geosynthetic materials such as polypropylene, HDPE’s and PVC-coated polyesters, and are used to solve civil and geotechnical engineering problems and challenges in or on the ground.
Geogrids enhance the functions of conventional soil materials to make construction more efficient, cost-effective, and reliable. Designs using geosynthetics should be based on the function(s) of the selected materials to meet the engineering and performance objectives.
All geogrids have openings, or apertures, which allow aggregates to strike through and be confined, thereby creating mechanically stabilized layers. This confinement allows loads to be spread-out over a larger surface area, which in-turn enables the aggregate surfaces to support heavier machinery, drilling equipment and other vehicles used in the oil and gas fields.
The principle is similar to a reverse snowshoe effect, only instead of snow, the materials are poor soils; and instead of a snowshoe supporting a 200-pound person, the geogrid-reinforced surfaces support thousands of vehicles weighing tens-to-hundreds of thousand pounds. In addition to the ability to support heavier loads, using geogrids minimizes differential settlement, which reduces everything from routine blading and surface maintenance to rig lean and crane pad stability.
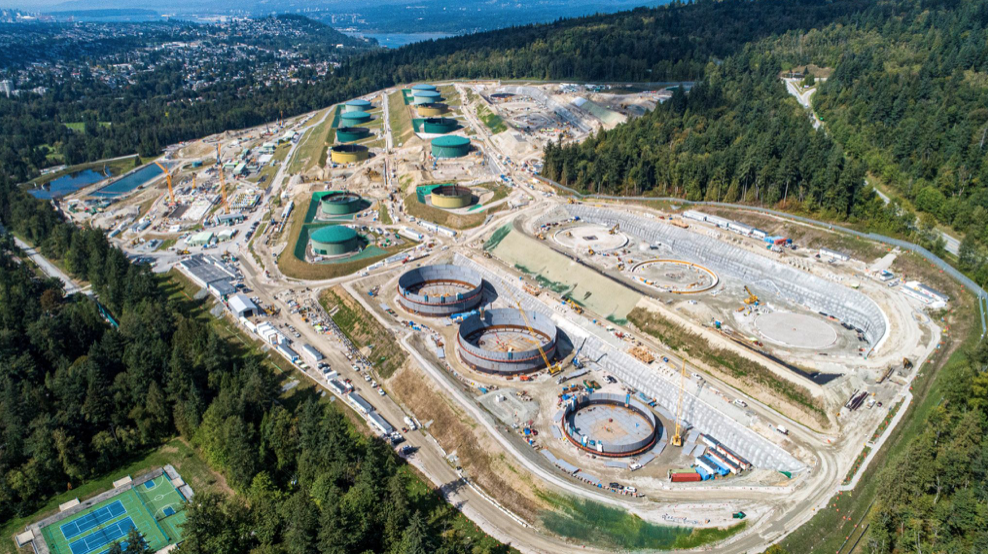
Types of Geogrids
There are three primary types of geogrids: uniaxial, biaxial and multiaxial:
Uniaxial geogrids: These were designed for and used in applications where the loads are primarily, if not exclusively, in a single direction and static. Typical oil and gas applications using this type of geogrid include walls, slopes, levees, berms and embankments. The open aperture structure interlocks with fill material to provide superior load transfer from the soil to the geogrid.
This results in cost-saving benefits for contractors, owners and operators that include structures with smaller footprints, less required fill materials, less construction traffic, and reduced carbon emissions. Facing components can range from a basic vegetated slope to decorative blocks to concrete panels.
An example of a typical project where uniaxial geogrids were used is the Transmountain Expansion Project (TMEP) in Vancouver, British Columbia. This expansion is a twinning of an existing pipeline between Strathcona County, Alberta, and Burnaby, British Columbia, increasing the total pipeline capacity by almost 600,000 bpd. A portion of the work across the pipeline included a 13-tank expansion and secondary containment on all new and existing tanks.
Because of its proximity to residential neighborhoods, commercial establishments, and important water supplies, and because expansion space was limited, uniaxial geogrids were used in the construction of thousands-of-feet of the containment berms.
By using geogrids of different strengths, it enabled the contractor and owner to benefit from less construction traffic through the adjoining neighborhoods, faster construction (which is tremendously important given the short construction season in British Columbia), lower environmental emissions, and required fewer square meters of land.
In addition, uniaxial geogrids are often used in the design and construction of containment levees around and within petroleum refinery facilities subject to hurricanes or other weather phenomena. The results are stronger, taller levees and less total settlement, and thus better protection to important gas and pipeline facilities and infrastructure.
Biaxial geogrids: These were invented by Dr. Brian Mercer almost 50 years ago, have square or rectangular apertures and were the first geogrids used for horizontal trafficked surfaces.
These surfaces are used mostly by wheeled vehicles and subjected to some type of moving, or dynamic, loading. In a typical application, biaxial geogrid is placed on existing natural ground and 10 or more inches of aggregate, crushed concrete, or other non-soil fill material is placed on top of the geogrid.
It is important to note that biaxial geogrids are virtually the same products today as they were many decades ago and have seen no significant advancement in their performance or potential cost-savings.
Multiaxial geogrids: This type is the most advanced types of geogrid that offers many more quantifiable benefits. These geogrids use either triangular or hexagonal-shaped apertures and were developed after acquiring decades of research and in-ground performance data.
The higher performance of multiaxial geogrids is due to the ribs running in multiple different directions. Since a wheel load radiates 360 degrees from the point-of-contact, having load-absorbing ribs in multiple directions provides far greater support and confinement than biaxial geogrids that have only two ribs.
Improved confinement, not an individual property like tensile strength or stiffness, is what results in the reduction of required section thicknesses. These reductions in required aggregate fill can be quite significant – ranging from several inches to several feet, depending on the existing conditions and the type of vehicles, when compared to biaxial geogrids. In addition to the aggregate alone, significant cost savings can be realized on machinery and labor.
Operators of oil and gas sites can rest assured that the reduction in materials doesn’t equate to a sacrifice in performance since these stabilized structures become much stronger surfaces.
A typical application for using multiaxial geogrids in the oil and gas industry is in the construction of temporary heavy haul roads that must support huge loads, both total and per tire. Oftentimes, the primary goals are the same – reduce the amount of aggregate required to construct the temporary road, minimize the potential for any differential settlement, and decrease the total time-of-construction.
Due to the risk and cost, it is common for owners and operators to hire experienced Professional Engineers to provide designs for these roads that are reinforced with multiaxial geogrids. And, it is common for temporary roads to be maintained and used for many years, and sometimes indefinitely, as oil and gas facilities build-out or maintain equipment, pipelines, tanks and other structures in a plant.
An example of one of many temporary heavy haul roads that have been constructed in the past three years is one built in 2020 along the Gulf Coast to support up a 12,000-ton Self-Propelled Module Transporter (SPMT), which was used to transport units and components from a major port landing to the project site.
The aggregate road, reinforced with multiaxial geogrid, was almost 5 miles in total length, had to accommodate 108-foot-wide loads with 140 psi wheel loads, and had to ensure it would hold-up for at least 100 passes of over 30 ultraheavy modules. And the road had to do all that without any significant repairs of the surface. The result was very minimal, planned maintenance and a road that performed so well over a period of 18 months, it was partially converted to a permanent plant access road.
The most common use of multiaxial geogrids is in aggregate access roads to oil and gas facilities. These roads are constructed where they are needed, not where the soil conditions are the most favorable. And often it’s imperative that vehicular traffic have 24/7 access to certain pipeline facilities and components. In addition, operators are using geogrid in roads adjacent to pipelines to allow for many years of use without any major maintenance.
Whether you need an access road to a tank battery or build a working surface that requires only bi-annual maintenance around a compressor station, using multiaxial geogrids result in surfaces that are more cost-effective, faster to install, and highest performing over the long-term.
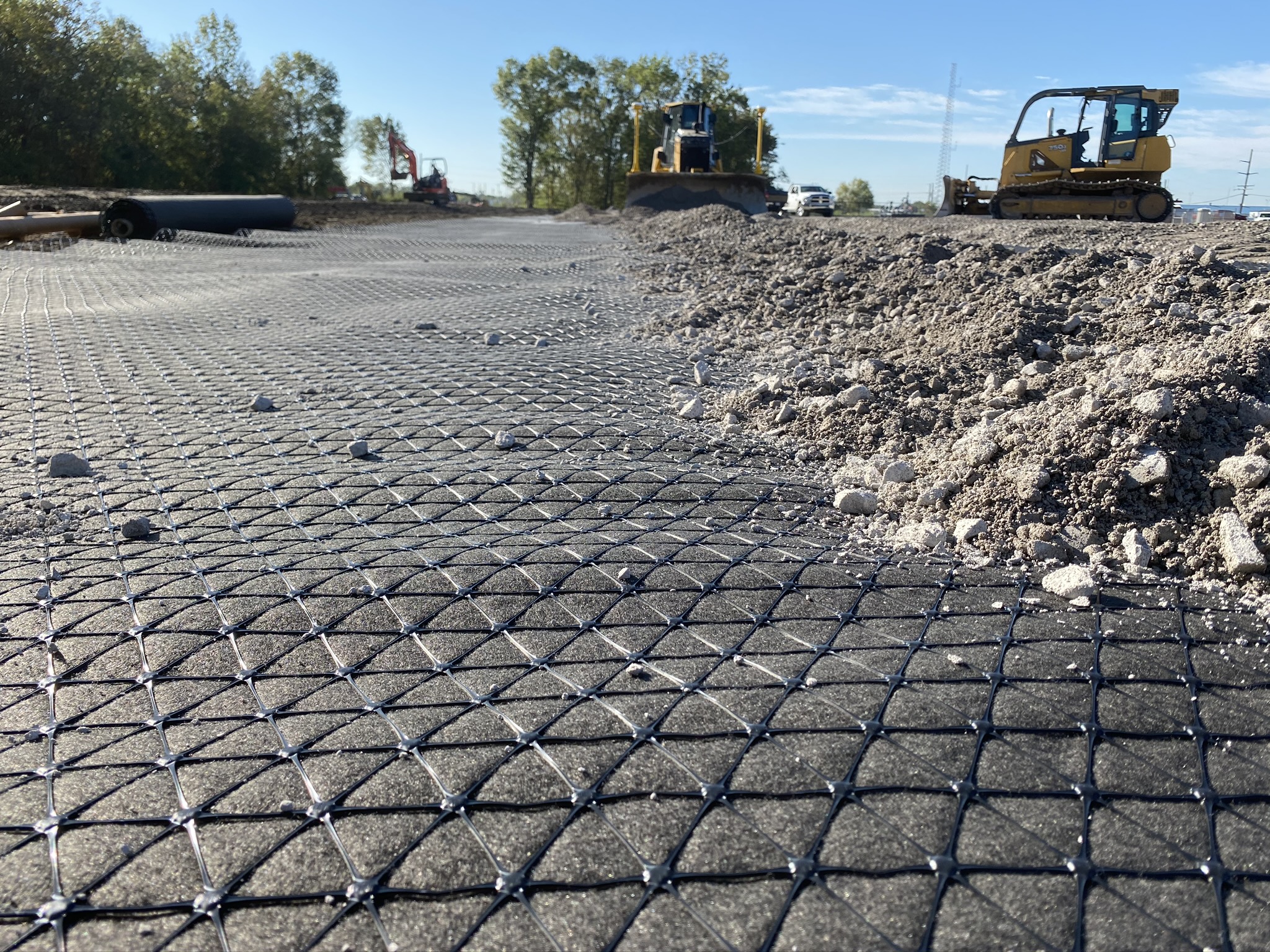
All-Weather Construction
Another major benefit of using geogrids is that they can be installed in almost any weather condition thereby allowing the construction schedule to keep moving during the rainy, cold months. Other methods like chemical stabilization using cement or lime require dry weather, warmer temperatures, specialized equipment and long curing times.
However, geogrid is rolled out and aggregate material is simply placed and spread on top. No specialized equipment or personnel are needed, and construction equipment and other vehicles can be operated on the geogrid-stabilized surface immediately after placement of the aggregate fill.
Roads and working surfaces stabilized with geogrid perform better and last far longer than those without geogrid. Vehicles and other equipment won’t become bogged down in mud since the surface quality is vastly improved. Since these structures require much less maintenance over time, operations remain productive instead of being halted for repairs. And, unlike chemical stabilization, which is soluble over time, and highly dependent on the soil type, geogrid-stabilized surfaces are permanent and consistent.
Although there are many soil stabilization methods available, utilizing geogrid in the design and construction of oil and gas access roads and other aggregate surfaces provides tremendous improvement in performance and longevity. As engineering and technological advancements to multiaxial geogrid technology were made over the past four-plus decades, both construction and maintenance costs were significantly reduced as well.
Site operators have come to rely on the proven ability of geogrid to provide a more cost-effective solution for uninterrupted access to, from and around all oil, gas, and pipeline facilities.
Author: D. Scott Phillips is a licensed Professional Engineer (PE) in multiple states, including Alaska and Louisiana. He has been with Tensar for 20 years, and is the industry manager for Oil, Gas and Petrochemical – North America. Phillips lives in Monroe, Louisiana. He has been involved in the design and onsite support of Tensar projects from Newfoundland to California and from Florida to Vancouver.
Comments