August 2024, Vol. 251, No. 8
Features
Pulling Off the Near-Impossible: Stalled Pig Rescue Mission Returns Pipeline to Normal
Sponsored ContentBy Rolf Gunnar Lie, Regional Director, Eastern Hemisphere Sales, T.D. Williamson
For the most part, the equipment meant to keep pipelines up and running remains up and running itself. When something goes wrong, a routine repair is often all it takes to set things right.
But when a third-party provider’s stalled cleaning pig prevented the replacement of essential valves in an offshore gas export pipeline (GEP), there was no quick, off-the-shelf solution to the problem — at least not without the financial and environmental costs of blowing down the entire pipeline.
Fortunately, there was still a way out. As T.D. Williamson (TDW) proved, it just took ingenuity, collaboration and engineered-to-order technology.
Malfunctions, Obstacles and Choices
Considering that GEPs transport the entire production between offshore fields and onshore processing terminals, there’s a lot riding on their reliable performance. That’s why regular pigging activities are part of every GEP integrity management plan. It isn’t unusual for GEP operators to run cleaning pigs weekly or monthly.
Whatever the frequency, pigging can’t proceed without fully functional, well-maintained components at the pipeline’s launching and receiving ends. A faulty pig trap, pig trap valves or emergency shut-down valves (ESDV’s) can make pigging difficult, if not impossible.
However, when two pig trap valves on a GEP platform offshore Asia stopped sealing properly, it wasn’t just a disrupted pigging schedule that concerned the operator. The internal leak was also causing pressure build-up at the pig launcher and further delaying an overdue in-line inspection (ILI).
To complicate matters even more, a third-party’s 28-inch, bi-directional cleaning pig was stalled in the GEP’s production tee located immediately beyond the pig trap valves. Although the stalled pig wasn’t completely obstructing pipeline flow, it made the line unpiggable. This made it impossible to move forward with the valve replacement project, which depended on T.D. Williamson (TDW) deploying its in-line SmartPlug® isolation technology to create a safe work zone. SmartPlug technology is introduced into the pipeline via the pig launcher, then propelled by pipeline product, external pumps or compressors to the isolation point, where it is remotely activated.
The operator weighed multiple strategies for recovering the stalled pig, including using another bi-directional pig to push it to the onshore receiver. However, if the pig got stuck farther in the pipeline, it might require a challenging subsea rescue. Pulling the pig back to the launcher was a less risky option, but without a standard tool to do the job, it wouldn’t be a quick or simple fix.
Unsure of how best to proceed, the operator turned the pig recovery project over to TDW. Their multi-phase response began with figuring out why the pig stalled.
A Good Thing Gone Wrong
When pigs stall during operation it’s generally because a considerable amount of debris has collected in front of them. To avoid this, pigging service providers drill holes into the pig’s body or discs to create “bypass.”
Bypass allows product to flow through and ahead of the pig as it travels through the pipeline, which generates turbulence that flushes the debris or holds it in suspension. Achieving the right amount of bypass is critical. If there’s too little bypass, there won’t be enough turbulent flow to clear away debris; too much bypass, and there won’t be enough differential pressure behind the pig to drive it forward.
In this case, TDW engineers discovered that the operator’s pigging service provider had attempted to optimize turbulence by modifying the pig so a relatively large volume of gas could flow through it, creating more turbulence and reducing differential pressure behind the tool.
However, because of the pig’s heavy polyurethane (PU) disc stack-up, it took a lot more differential pressure to move the tool. Once the pig entered the barred production tee, even more bypass was created, reducing the differential pressure to the point where there wasn’t enough drive on the pig to keep it going.
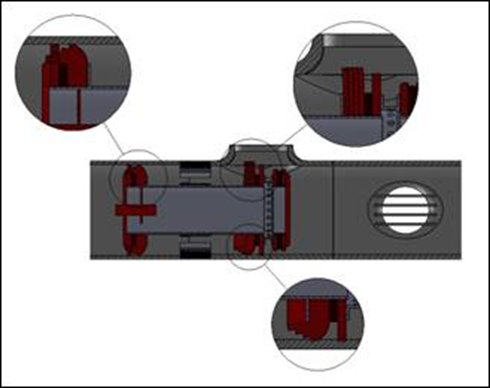
Testing Success
Once they understood what happened, engineers at the TDW Global Solutions Center in Stavanger, Norway, turned their focus to designing, testing and manufacturing a successful solution.
TDW envisioned a pulling tool comprising a wire and hydraulic cylinder attached to two “stronghold” anchor points, one in the pig body and another behind the launcher.
Engineering a tool to pull a pig out of a pipeline involves making countless decisions, including determining the recovery force required to pull the pig back safely and successfully. To make a calculation they could feel confident with, TDW built an exact replica of the offshore pipeline launcher where they recovery-tested a pig identical to the stalled tool.
Before they could be sure that pulling the pig back was the answer, TDW had to consider that the pig’s PU sealing discs fold backward during operation. To be able to reverse the pig out of the pipeline, there had to be enough pressure to flip and fold the discs in the opposite direction.
Each test provided a better understanding of the pressure required to flip the discs and achieve a successful recovery. The third recovery test established a recovery force of 13 tons.
Easy Installation
The next step was deciding how and where the recovery tool would grip the pig. Without a firm hold on the pig, the recovery process would be futile.
The TDW team agreed that the strongest gripping points for the recovery tool were the bypass holes — meaning the same elements that had contributed to the pig stalling in the first place would be integral to the recovery process.
As for the tool itself, engineers designed it so spring-loaded pulling arms would engage or click in place inside the bypass holes, then a locking mechanism lance would install the recovery tool onto the pig body. The pinger receptacle inside the stalled pig would help guide the gripping mechanism into the bypass holes, and a camera system inside the recovery tool would allow technicians to see when the gripping mechanism successfully engaged inside the pig.
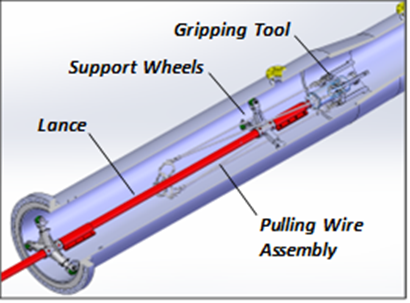
An Important Dry Run
With a manufactured recovery tool in hand and the operator-furnished cleaning pig equipped with new discs, engineers returned to the test rig for a dry run. This exercise was intended to both prove the tool’s efficacy and performance under near-real-world conditions and optimize procedures. Given that the pipeline would be shut down for the recovery, knowing how long it would take to complete various tasks — including assembling the lance, engaging the tool and retrieving the pig — provided ample confidence that the pig could be rescued on an acceptable timeline.
The diligence paid off. Once onsite, it took TDW crews only five hours to:
- Open the quick-opening closure on the launcher.
- Assemble the lance and gripping tool and insert them into the pipeline.
- Lock the pig gripping tools into the pig bypass holes.
- Hook up the pulling wire.
- Begin the recovery operation.
- Retrieve the pig from the launcher.
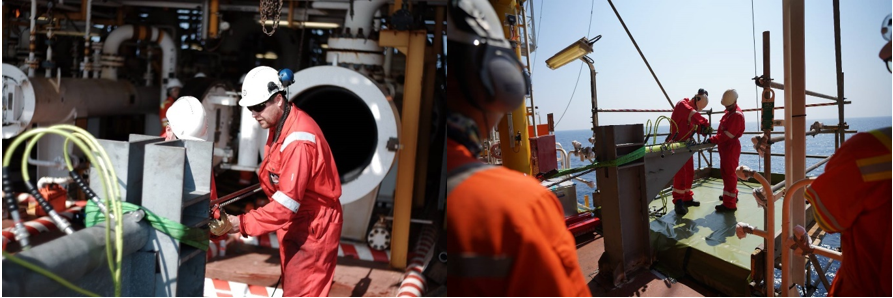
With the obstacle removed from their way, the TDW SmartPlug team took the project reins and prepared the line for valve replacement.
Risk — and Emission — Mitigation
Safety is always a priority during pipeline isolations. There’s no place for personnel injuries or asset damage.
Before any SmartPlug operation, it’s standard practice and a DNV Type Approval requirement to collect and document engineering information and to perform a piggability study. In this case, TDW also conducted two risk management studies, identifying more than 60 items for mitigation.
After that, TDW mobilized the SmartPlug tool from Stavanger to the worksite. There, technicians loaded the tool into the recently cleared pig trap, then used a treated seawater pumping service to pig it 47 meters (154 feet) to the predetermined position. With a safe isolation in place and the SmartPlug tool’s plug modules verified for proper sealing, the operator replaced the faulty valves, and then TDW unset and retrieved the SmartPlug system.
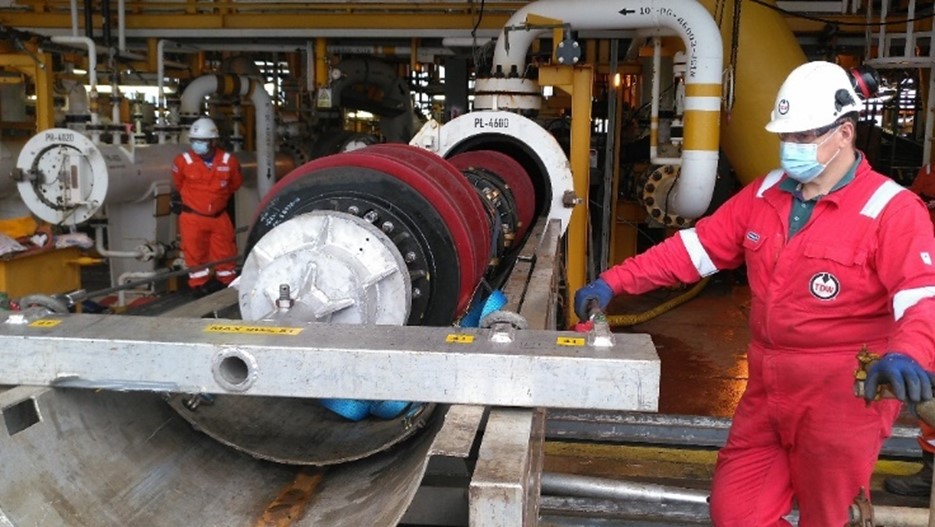
Not having to depressurize the GEP for valve repair saved the operator approximately 300 million standard cubic feet per day (MMSCFD) in inventory loss and six or seven turnaround days including the time to repressurize the pipeline.
A Better Pigging Plan
That wasn’t the end of the project, however. Given the operational and financial implications associated with the stalled pig, TDW wanted to minimize the possibility of a repeat occurrence by bolstering the operator’s pigging plan.
Like the stalled pig recovery effort, this one also required a multi-step approach. First, TDW engineered a customized cleaning pig based on proven VANTAGE® technology used for batching, displacement and cleaning.
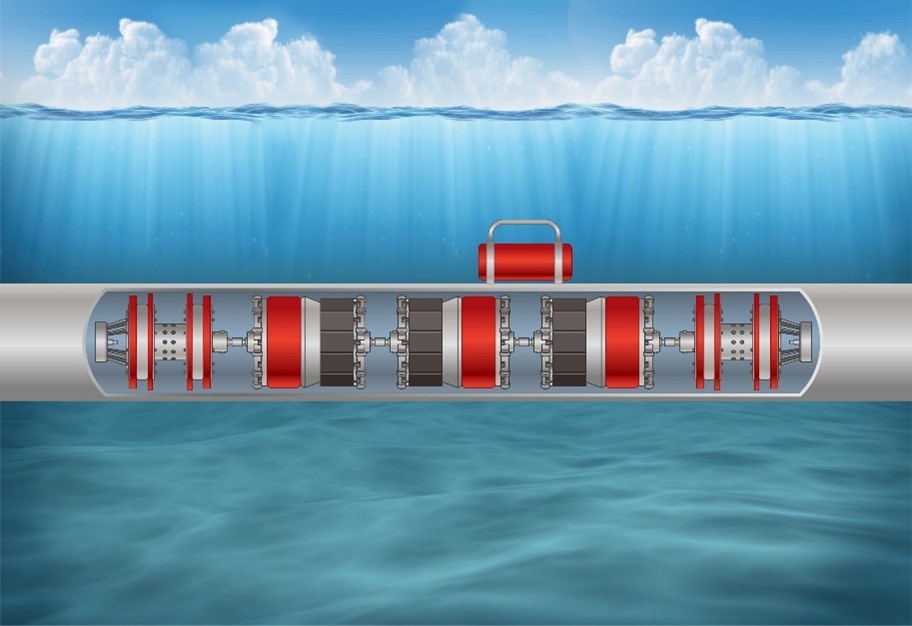
Next, it made the bespoke tool the centerpiece of a new, conservative progressive pigging program built around using a series of increasingly aggressive cleaning pigs. After just five pigging runs, the offshore portion of the GEP met the operator’s cleaning specifications. The pipeline was also ready for its long overdue in-line inspection; its interior walls were free of any dirt or debris that could interfere with ILI tool sensors and result in inaccurate or incomplete data.
The operator resumed normal production and normal pigging with fully functional valves and sound pipeline components.
The Role of Human Innovation
Technology is an indispensable part of modern life, and we can generally count on it to do its job well, saving us time, money and effort. When technical problems occur, though, it’s good to know that human innovation and sheer determination can outmuscle stubborn machines, achieving one-of-a-kind solutions.
Comments