October 2024, Vol. 251, No. 10
Features
Is the Oil and Gas Industry Ready for the Generational Shift?
Sponsored Content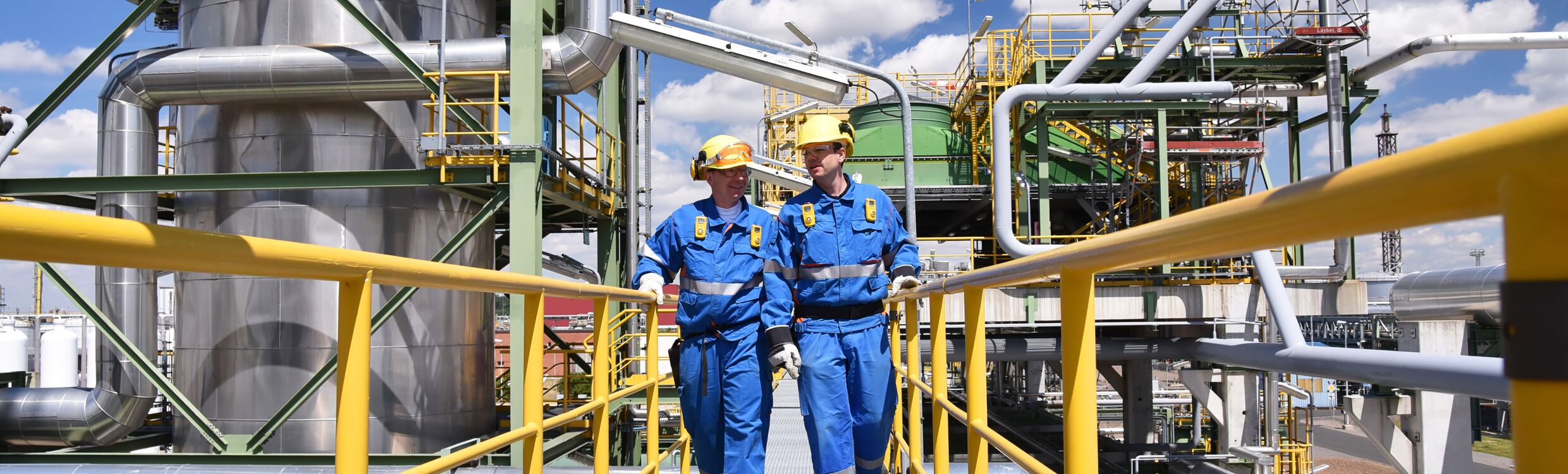
How one organization transformed its approach to empower employees.
As the oil and gas industry faces a monumental generational shift, a key question looms over its future: is it ready for the wave of retirements and the rise of a new, younger workforce? The industry's challenges are compounded by technological advancements, changing skillsets, and the need for continuous operational efficiency. Companies must find innovative ways to transfer the deep knowledge of older workers to the younger generation, while also adapting to the demands of a digitally savvy workforce.
The impact of this shift cannot be understated. Veteran employees with decades of expertise are leaving the workforce at an accelerating rate, taking with them a vast repository of knowledge critical to the operation of complex oil and gas facilities. Simultaneously, younger workers are entering the industry with different expectations, particularly around the use of technology and access to information. They expect mobile, instant access to knowledge and tools that help them do their jobs more efficiently. This changing workforce dynamic is pushing companies to adopt digital technologies to bridge the gap between experience and innovation.
The need for digital transformation. The solution to these challenges lies in digital transformation. The oil and gas sector, historically slow to adopt new technologies, is now recognizing the necessity of modernizing operations to remain competitive and safe. At the heart of this transformation is the shift towards digital platforms that make knowledge and operational content accessible, manageable, and actionable.
One industry-leading oil and gas organization recognized the importance of this shift early on. Faced with the same generational challenges as the rest of the industry, this organization sought to digitally transform its operations and learning systems. By partnering with Hexagon, they implemented AcceleratorKMS®, a comprehensive knowledge management system that drastically improved the accessibility and usability of critical operational information across their global sites.
The results were profound. Through the implementation of a digital approach, the company was able to:
- Reduce the time to search for training materials by 25%, giving workers quicker access to the information they need in the field.
- Eliminate redundant content by 30%, ensuring that only relevant and up-to-date information was being used, increasing efficiency and reducing confusion.
- Reduce the time to track task completions by 25%, improving management oversight and ensuring compliance with safety and operational protocols.
- Cut the time required to complete assessments by 50%, accelerating the learning process and empowering workers to make better decisions in real time.
Moreover, user satisfaction across all facilities reached 4.1/5, with 85% of users agreeing that the time to maintain content was significantly reduced. These outcomes demonstrate the power of digital transformation in enabling companies to not only retain valuable knowledge but also enhance the way this knowledge is accessed and applied in the workplace.
Bridging the generational gap with technology. This case study is more than just a success story—it's a blueprint for how the oil and gas industry can navigate the generational shift. By digitizing learning and operational content, companies can ensure that younger workers have the tools they need to succeed while also preserving the invaluable knowledge of their older counterparts.
The AcceleratorKMS® platform, for instance, made learning content more mobile and connected. Workers in the field no longer had to rely on outdated, paper-based procedures; instead, they could access the latest instructions and updates from their mobile devices, ensuring they always had the most current information at their fingertips. This not only improved safety but also reduced frustration and allowed workers to focus on the task at hand, confident that they had all the information they needed.
Another key benefit of digital tools like AcceleratorKMS® is the ability to automate processes that were previously managed manually. Real-time tracking of procedures, automated reporting, and decision-making tools within the platform helped field workers navigate unexpected situations without guesswork. By providing a digital framework for knowledge transfer, the system facilitated quicker decision-making in the flow of work, ultimately leading to more efficient operations.
Readers can access the full case study here.
Preparing the future. As the oil and gas industry continues to evolve, the role of digital transformation becomes more critical. Companies that embrace these changes will be better positioned to address the challenges of a shifting workforce and ensure the continuity of their operations. The success of organizations like the one featured here serves as a clear indicator of the potential benefits that come with embracing digital technology.
The generational shift presents both a challenge and an opportunity. By investing in technology that supports knowledge transfer, streamlines operations, and empowers a digitally fluent workforce, oil and gas companies can not only weather this shift but thrive in it. The future belongs to those who are prepared, and in an industry as complex and demanding as oil and gas, preparation means embracing the tools that will drive the next generation of success.
The generational shift in the oil and gas industry requires more than just passing down knowledge—it demands a rethinking of how that knowledge is shared, applied, and retained. The integration of digital solutions is key to ensuring that companies can not only survive but excel as they navigate this critical transition. The time to act is now, and those who embrace the shift will be the ones leading the way into the future.
About Hexagon. Hexagon is a global leader in digital reality solutions, combining sensor, software and autonomous technologies.
Hexagon’s Asset Lifecycle Intelligence division helps clients design, construct and operate more profitable, safe and sustainable industrial facilities. We empower customers to unlock data, accelerate industrial project modernization and digital maturity, increase productivity, and move the sustainability needle.
Hexagon’s technologies help produce actionable insights that enable better decision-making and intelligence across the asset lifecycle of industrial projects, leading to improvements in safety, quality, efficiency and productivity, which contribute to economic and environmental sustainability.
Hexagon has approximately 24,500 employees in 50 countries, and net sales of approximately €5.4 B. Learn more at www.hexagon.com, and follow us @HexagonAB.
Comments