December 2013, Vol. 240 No. 12
Features
Selection Process Of Compressor, Turbine Units
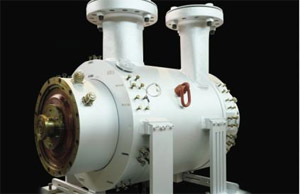
This article looks at the various ways of writing specification documents for compressors and turbines and compares the effect of three distinct approaches on the process of equipment definition.
The specification of gas pipeline compressor equipment is the fundamental step in planning a new system or upgrading an existing system. The pipeline and system hydraulics will determine the operating conditions for the new station or the addition to the existing equipment, which will initiate the project and start the process of preparing a request for quotation (RFQ) to be sent out to suppliers and contractors.
While the RFQ will contain instructions and contractual requirements, such as deliveries and legal obligations, the core of the document is the equipment specifications. The following sections will concentrate on the specification of the equipment and the various ways in which it may be set out. Most important is, of course, the operating conditions of flow and pressure that the station will be required to provide, defined by the system hydraulics as discussed above.
Specification Options
There are several ways to undertake the task of preparing the specification for the RFQ, and each owner company has its preferred method and standards. From the simple concept of defining the need of the customer in an RFQ and preparing the specification for the bidding process, there are several steps which may be very basic or very complex.
In setting out these methods, we will compare generic examples, which are based on actual cases, but are not intended to represent any particular company or project.
Needs Of The Customer
The need of the pipeline operator can be expressed very simply: to provide a compressor and driver to pump gas over a range of pressure ratio and flow conditions economically and efficiently for a period of time, and, if required, to be adaptable to changes of conditions with time. The definition of this task can literally be written on the back of an envelope, but this is only one part of the equation.
Once the role of the compression unit has been defined, the relation between the power unit and the pipeline infrastructure surrounding the unit, including control and monitoring, pipeline connections, buildings, environmental controls and safety, will involve specifications of the interfaces and ancillary equipment that are particular to the customers’ system and standards. These project-specific requirements do not form part of the basic machinery specification and fall outside our scope.
Technical Specification
Simple solution – The basic specification can be outlined by defining the operating pressures, flow and site parameters, then leaving to the suppliers the details of describing and defining a unit which fits these requirements. The problem with this method is it becomes difficult to evaluate a number of bids on a comparative basis – that is, to evaluate, fairly, the many facets of competing proposals.
In particular, the basic specifications of each proposal may vary and some aspects may not be related to accepted industry standards. This is manageable provided there are only a few bidders, preferably no more than three, and the prequalification of the preferred bidders has been done carefully.
Despite these problems, some organizations have managed, with success, to purchase machinery on the basis of a fairly simple functional specification. It should be noted that the responses to these simple specifications are usually backed by accepted industry standards such as API standards.
API method – The previous section leads on to a specification based on appropriate API standards. In this case the functional specification is backed by API 616 and 617, which define key elements of the machines. There are several ways of using the API standards in formulating an invitation to bid. One method is simply to set out the API standard as the basis and add the functional requirements in the form of engineering notes.
The evaluation of proposals is then simplified in that the key items can be checked off against the standard sheets, with the exceptions noted and identified for review. Costs associated with the exceptions and variations can then be evaluated and the capability of the proposal to meet the functional requirements will then become the basis for the final judgment.
In some cases, it has been found appropriate to develop a more detailed and descriptive format in which the functional specification may form the basis of the invitation to bid, backed by the API data sheets.
This can be more helpful to both bidder and purchaser in that the background to the project may be better defined and the description may lead to more dialogue prior to bid, resulting in a more complete and defined proposal.
All can do specification – As organizations become larger and more focused on the business of operation, the number of specialists capable of undertaking engineering design details has been reduced. There has been a move to farm out the specification and selection of machinery to outside sources. This has resulted in more comprehensive documentation to cover all options.
Some organizations use a very comprehensive specification as the basis for a proposal. This specification is intended to cover all possible applications and all types of turbines and compressors and be used as a standard for all projects requiring turbines and compressors.
It has become convenient for some organizations to employ consultants to draft a “standard specification,” which may be used as the basis for any project requiring turbomachinery. While this may reduce the front-end work on preparing a project specification, it can substantially increase the work of the bidder and the purchaser.
Difficulties arise because wide-ranging specifications will create many exceptions that the bidder must identify and note and the purchaser must check and confirm. While there may be some benefits to having a specification that can be pulled off the shelf for all projects, the work required to undertake the subsequent evaluation and selection can add considerably to the time taken to reach a purchase decision.
Each exception or qualification to the specification needs to be discussed with the bidder and the result entered into the evaluation process. This may be good for the consultant engaged to do the work, but it can add considerably to the time and the cost.
Performance specification – As already noted, the purpose of the RFQ is to purchase equipment that will pump a given quantity of gas along the pipeline. Therefore, each bidder has to show how the proposed machinery will be able to perform to meet the specified conditions of flow and pressure.
The bidders will have to take into account site-ambient conditions, elevation and temperature variations, and changes in upstream and downstream conditions, which will have been set out in the RFQ. They will also have to give fuel consumption data for the relevant conditions and estimated compressor efficiency at the required data points. This will include a map of compressor characteristics. In addition, the bid will include both initial capital costs and maintenance costs over the anticipated plant life, with spare parts costs for key items.
Evaluation process – Evaluation of the bids involves a comparison of the specification with the bid document. Since there is rarely a perfect bid, it may be necessary to decide on the extent to which compromises may have to be accepted. In evaluating bids, the objective is to select the most appropriate unit to perform the duties required at a competitive price. Therefore, every aspect of performance needs to be examined; the better the bid responds to each point of the specification, the more likely it will be accepted.
The more specific to the task the specification is, the fewer the points will be to be investigated and discussed with the bidder. Discussion and resolution of issues takes time, and the more this can be reduced by the clarity of the specification and the proposal, the better.
While the technical parts of the RFQ are the central factors to the final decision, they may not be the whole story. They represent the essential factors – the “musts” – but there are factors of judgment – the “wants” – that can influence the final decision. Several methods can be used to formalize the evaluation procedure.
One method that has been used successfully separates the “musts” from the “wants” and introduces a weighting system into the scoring process, which will lead to a final, arithmetic, result.
The musts are the costs, performance requirements, delivery, and matching key items in the technical specification. These will be the deciding factors, but in cases with only small differences between the bidders, the “wants” analysis enters into play. The percentage allocated to the “wants” can be varied, although typically about 10% would be the final arbiter, given that all other performance factors are reasonably equal. When this is combined with the required information from the technical specification and the performance estimates, the preferred bidder can be selected. This system is transparent and auditable.
It is perhaps worthwhile to note that the project manager or project coordinator chosen by the bidder will be a key factor in project success. Another key will be quality and manufacturing excellence, a rigid quality assurance program and the evidence of application and adherence to the program. This method can be used for all types of specification and the spreadsheets will reflect the relative complexity of the type of specification.
Time required for evaluation – Because each project is different, it is not easy to define the probable time needed for bidding and evaluation; however, on the basis of past experience, the following estimates are relevant.
Option 1 – This first method will probably take more time prior to bidding for discussion with the bidders to clarify intent and mutual understanding of the specification relevant to the particular project. The bids themselves should be of high quality. The evaluation process will probably take three or four weeks. The total elapsed time will probably be eight to 10 weeks.
Option 2 – The second method should abbreviate the pre-bid time because the data will be clearly set out. The evaluation post-bid will probably take the same time as Method 1; the overall time taken for the process will probably be six to seven weeks.
Option 3 – With the “all can do” specification, both pre-bid and post-bid times will probably increase as there may be considerable clarification required to adequately define the key needs of the project. Recent experience suggests that the process can extend to more than 12 weeks, and even after selection there may be details still to be resolved.
In all cases, prequalification is important in ensuring that the most qualified bidders are included in the invitation to bid RFQ.
Conclusions
While the authors do not advocate for any of the above methods, note the possible amount of time required for the process from initial project concept to completion and the possible impact on the project’s overall timeframe.
There are obvious difficulties in subcontracting the process to an outside agency, which can introduce complications and add to the time needed for completion, but in the absence of engineering expertise in-house, this may be unavoidable. It is, therefore, essential that the chosen method be clearly defined and in a form that is truly transparent.
Authors:
Tony Cleveland is president of Cleveland Engineering Services Ltd. in Canada, involved in a number of energy-related projects including improvements in energy use and efficiency. His early industry experience includes Bristol aero engines (later Rolls-Royce), and Solar in USA. Cleveland then joined British Gas (BG) as manager of the Machinery Department and was involved in the planning, design and selection of equipment for the BG natural gas transmission system. In 1975 he moved to Canada and worked on northern pipeline development with several major organizations.
Saeid Mokhatab is an independent gas engineering consultant, specializing in the design and operations of natural gas transmission pipelines. He has been actively involved in several international pipeline/compressor station EPC projects and has published numerous technical papers and books on the relevant subjects. Mokhatab is a frequent contributing editor to Pipeline & Gas Journal.
Comments