January 2014, Vol. 241 No. 1
Features
North Slope Gas Pipeline Challenge: Goldilocks Effect of Permafrost
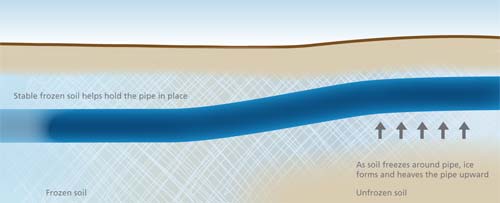
A tricky challenge for moving Alaska’s North Slope natural gas to market is designing a pipe that will remain safely buried for decades in hundreds of miles of chilled earth, permafrost and discontinuous permafrost.
If the gas in the pipe — and thus the pipe itself — is too warm, it could melt permafrost, weakening the ground’s support. The pipe could sag, possibly causing it to leak or burst. If the gas is too cold, water in the soil could draw toward the frigid steel, like iron shavings to a magnet, and form an ice bulb under or along the buried pipe, pressing it toward the surface, possibly causing it to split or crack.
Call it the Goldilocks challenge. The temperature of the gas should be neither too hot nor too cold for the soil, but just right.
Besides keeping the temperature in and around the pipe just right, the project developers must prove to federal regulators that the steel pipe is strong enough — with a smart margin of safety — to handle the stresses as underground ice pushes it around. Soil movement from earthquakes and landslides also can put extreme bending stresses on the pipe.
Nobody wants the pipe to leak or break, not the pipeline owners, gas shippers, utilities that ultimately buy the gas, regulators, project financiers or anyone else with a stake in the project’s success. Controlling the gas temperature is a partial answer. That’s been the plan for a chain of Alaska North Slope gas pipeline projects that have come and gone over the past 40 years.
In early 2012, a partnership of TransCanada and ExxonMobil said it had just that idea in mind — temperature control — for its now-dormant idea to pipe North Slope gas down the Alaska Highway route to Alberta.
“North of the Brooks Range, the natural gas in the pipeline is proposed to be cooled to below freezing to maintain the stability of thaw-sensitive soils, thereby reducing thaw-related movement of the pipeline,” the companies said in filings with regulators. “For (compressor) stations located south of the Brooks Range, seasonal variation in station discharge gas temperature is planned to range from approximately 25° F in the winter to approximately 45° F in the summer.”
That effort since has morphed into a similarly designed pipeline project to export LNG to Asia. An 800-mile gas pipeline would cross Alaska north to south in permafrost — ground that remains frozen year-round — for the first 180 miles or so, then through soil that gradually warms south of the Brooks Range. The liquefaction plant and shipping terminal would be at the end of the line, at tidewater.
That’s the general picture; but a temperature-control solution is not the only issue. If the project developers operate the pipe close to and slightly above the steel’s ultimate strength limit, as is likely, federal regulators will require that an Alaska gas pipeline get a special permit for safety. The permit would address how the engineers and metallurgists will outfox thaw settlement and frost heave and the extraordinary strain these can place on the pipe.
To the regulators, caution is the prudent path. The pipeline could endure stresses from gas inside the pipe compressed to breathtaking pressures. It could face bending and warping forces from outside the pipe from soil and frost-heave conditions unlike those found anywhere else in the country.
Why Jockeys Are Small
One point to get clear right at the start is that steel pipe is not necessarily a rigid, unyielding, unchangeable solid.
Steel pipe will expand when pressurized natural gas pulses through it, pushing against the pipe’s interior wall. The pipe will stretch and bend into new shapes without breaking, given the right conditions and forces. That’s why steel pipe can be contoured to rise up hills or plunge below rivers.
“All pipes flex a little. … That’s the beauty of metal,” said an official with the federal Pipeline and Hazardous Materials Safety Administration. “It’s not like glass.”
In 2011, the Exxon/TransCanada venture-tested pipe samples from mills around the world at an Edmonton, Canada, lab. The trials aimed to appraise the steel’s strength by replicating stresses on the pipe samples — built to the companies’ specifications — from frost heaves and thaw settlements. In one test, the lab used lasers and strain gauges to measure how 33-foot lengths of pipe responded to internal hydrostatic pressure as well as to external pressure from rams pushing and bending the pipe. At what point would the pipe deform and be unable to maintain its original shape?
Other trials were designed to test how the pipe would elongate under pressure. Bolt it to a heavy-duty frame and then pull. The specs called for the 33-foot lengths to stretch to just over 34 feet and still be OK.
Stresses and strains that bend, compress and otherwise distort seemingly rigid objects are commonplace in this world. Take bones, for example. Racetrack touts know a bit about the subject. The more weight a racehorse carries, the more its leg bones will deform at each stride before regaining their normal shape and length when the hoof rises. The weight is the stress. The bone compression is the strain.
More weight means more compression. More compression means shorter strides. Shorter strides can mean the difference between a win, place or also-ran race. The horse can still perform — that is, run the race. But bone stress and strain affect its performance. That’s why jockeys don’t weigh very much.
Trial And Error
Engineers know quite a lot about construction in cold climates. For example, they know to bury city sewer and water mains below the frost level to make sure everything flows smoothly.
Some lessons were born of mistakes. Roads that slumped away. Buildings that tipped on their axes. Smooth runways that were here today but gone in the spring. Forest clear-cuts that exposed soil to more solar heat and spawned soupy quagmires.
Russia laid its first Arctic gas mainlines in the 1970s. Frost heaving burped some of them to the surface. A 1979 Russian professional journal noted the challenges as “Permafrost conditions cause stresses of varying magnitude in the pipeline and … sometimes lead to breaks.”
Also in the 1970s the oil industry developed North America’s first Arctic oil field — Prudhoe Bay on Alaska’s North Slope — and built the Trans-Alaska oil pipeline to an ice-free port 800 miles south of Prudhoe. (This field’s natural gas would be the main reserves behind an Alaska LNG export project; for now, without a pipeline, the produced gas mostly is reinjected into the Prudhoe reservoir.)
The Alaska oil pipeline has operated continuously since 1977. Half of it is buried in soil that isn’t frozen so won’t thaw or slump as warm oil courses through the pipe. The other half is in in permafrost areas and troublesome discontinuous permafrost soils. For those miles, the pipe is above ground, propped on 78,000 frames — called vertical support members, or VSMs — that are engineering marvels. To keep the VSM’s anchored during summer warmth, they’re outfitted with 124,000 special pipes that draw heat from the ground to keep it frozen.
Planning and constructing the oil pipeline served up many lessons on Arctic construction. For example, an initial idea of burying the pipeline along the entire route was soon dropped as unworkable. In a few places totaling about four miles of the 800-mile-long route, the pipe actually is buried in permafrost, but only after placing it in a refrigerated trench to keep the soil from thawing.
Even after the pipeline began carrying oil in 1977, the lessons kept coming. During the pipeline’s first six years of operations, the owners dug up at least eight buried sections that had buckled or cracked due to thaw settlement or frost heaves.
A gas pipeline experience will be different, because gas, unlike some oil, moves just fine when chilled below 32° F. So, in theory, the gas pipeline can be buried along almost its entire route.
But getting the temperature just right is trickier than it sounds.
Builders of a 500-mile oil pipeline through discontinuous permafrost from Northwest Territories to Alberta in Canada planned to flow the oil at ground temperature when the line started up in 1985. But the ground temperature actually varied more than thought, depending on the surface and soils. The oil wound up changing ground temperatures, according to Peter J. Williams in his book “Permafrost & Pipelines: Science in a Cold Climate.”
Permafrost thawing occurred when the pipe crossed from unfrozen to frozen ground. “However, a larger amount of thawing occurs initially because of the disturbance of the ground surface caused by the laying of the pipe and backfilling. Generally speaking, disturbance of the natural vegetation upsets the exchange of energy at the ground surface in such a way as to raise the temperatures of the ground slightly, and this is very important if the ground is almost at thawing point anyway,” Williams wrote.
Winter, Water And Wicking
Teams of scientists have studied burying chilled-gas pipelines in cold soil many times over the decades.
In the early 1970s, when the first plans were hatched for moving Prudhoe Bay gas to market, a consortium of pipeline and oil companies set up testing sites in Canada and Arctic Alaska to study what happens when a gas pipeline interacts with what’s called the “cryosphere” — the Earth’s frozen surface.
In the late 1970s and early 1980s, a new consortium won U.S. and Canadian approval to lay a gas pipeline from Prudhoe Bay through Canada. It, too, studied how to nest a chilled-gas pipeline in cold earth. In particular, its tests examined how insulating the pipe or placing non-frost-susceptible soil under the pipe could deter frost heaving.
From 1982 to 1994, a team of Canadian and French scientists also studied the challenge. The Canadians were interested in Arctic construction. The French had a controlled-environment lab built after frost during a cold 1960s winter heaved their roads into rollercoaster rides.
A 2004 Russian study documented permafrost thawing and pipeline failures in Norilsk, in north-central Siberia. The scientists concluded that buried lines are 40 times more prone to bad problems than above-ground pipe when gas temperatures are above freezing and not controlled.
A 2006 Alaska conference on engineering pipelines in permafrost drew delegates from all over, including a large crew from Russia, to share knowledge and learn more.
In 2010, a team of ExxonMobil engineers, including some involved with the Alaska project, submitted a paper to an international pipeline conference in Canada describing industry research on designing pipelines to resist ground movement. “The importance of using strain-based design pipelines is growing due to the increasing number of projects in challenging environments such as permafrost, offshore ice hazards, active seismic areas, and in high temperature/high pressure operations,” the paper began.
Much is known now about the topic, including:
• Permafrost at temperatures near freezing can contain ice and water. The water can freeze to the pipe, which could cause heaving problems even in permafrost.
• Pressure differences within the ground after a chilled-gas pipe is buried is what helps water migrate to the pipe.
• Frost heaving generally is more likely to occur in fine-grained unfrozen soils than in coarse-grained sand or gravel or very-fine-grained soils such as clay. The Alaska project’s 2013 field season is devoted partly to drilling bore holes to understand more precisely the pipeline route’s soils.
But the rule of thumb immediately above has exceptions. Frost heave occurred in clean sand and gravel in a recent study when the temperature oscillated above and below freezing, said Margaret Darrow, an assistant professor in the University of Alaska Fairbanks Mining & Geological Engineering Department. “So even sand and gravel can heave under the right conditions.”
And clay can frost heave, too. A likely route for an Alaska gas pipeline doesn’t have much clay but it does have silt that contains some clay, said Vladimir Romanovsky, an internationally recognized permafrost expert with the University of Alaska Fairbanks Geophysical Institute. “That is a bad recipe if you want to avoid frost bulbs.”
Winter construction can be a smart way to go. This likely will be the choice for construction of the Alaska gas pipeline. The soil layer above permafrost that freezes and thaws with the seasons — the “active layer” — will be frozen in winter. At that time of year, trenching through this insulating layer, if done correctly, shouldn’t expose the permafrost below to air that could warm it and make it vulnerable to thawing.
Transitions are danger zones. If the pipe is exiting a permafrost zone and entering unfrozen soil, it could frost heave in the unfrozen soil while being locked tight into the permafrost. That could put acute strain on the steel at the transition point. A similar strain on the steel could occur when the pipe transitions between unfrozen soil that doesn’t tend to frost heave and soil susceptible to heaving. A joint U.S.-Japan study in Fairbanks from 1999 to 2003 examined this particular bugbear in detail.
Some Alaska-specific insights have occurred, too, including these keys:
• Not all soil in the permafrost region north of the Brooks Range is necessarily frozen, such as soils under rivers.
• Ground south of the Brooks Range isn’t uniformly unfrozen. Instead it is pocked with permafrost patches and ice lenses that prompt geoscientists to label the area “discontinuous permafrost.”
Enter The Safety Cops
Federal oversight of gas pipeline safety dates to the 1960s, an era of upheaval when the environmental movement was born, among other societal changes.
If the pipeline safety crusade had a single catalyst, it arguably was the explosion of a 30-inch gas transmission line that blew a crater 15 feet deep, 75 feet long and 30 feet wide in a Natchitoches, LA, neighborhood, leveled five houses, melted cars and killed 17 people, including nine children.
President Lyndon Johnson soon urged formation of a national pipeline safety agency. He got his wish in the Natural Gas Pipeline Safety Act of 1968. A growing U.S. population and a growing network of gas pipelines were on a collision course for disaster, Johnson said. “This bill creates — for the first time — comprehensive, complete and enforceable safety procedures regulating the pipeline transportation of flammable, toxic and corrosive gases,” Johnson said on signing the act into law.
The nation’s new Department of Transportation — elevated to cabinet-level status in 1967 — got the pipeline safety assignment. Eventually, the authority went to the department’s Pipeline and Hazardous Materials Safety Administration (PHMSA).
PHMSA regulates the safe construction and operation of gas transmission lines, such as the 800-mile line that would serve an Alaska LNG export terminal or a similar, smaller-size in-state pipeline that a state of Alaska agency is designing.
Pipelines can go awry at any step along the way. And there are a lot of steps in which poor quality control can cause problems: Making the steel. Rolling it into pipes. Coating it to deter corrosion. Loading, unloading and transporting it. Welding pipe lengths together. Installing pipe into the ground. Trenching and refilling the trench. Finding and fixing defects during decades of operation.
Federal pipeline inspectors will tell you about how the best laid plans can go wrong, such as a new, multibillion-dollar gas pipeline in the Lower 48 states that, when tested before startup by flowing pressurized water through it, spouted like a lawn sprinkler.
So they’ve crafted rules about how to build and operate a gas pipeline safely.
A Million Tons Of Steel
The Alaska LNG-project pipeline, as currently conceived, would be physically impressive.
The LNG export pipeline sponsors — ExxonMobil, BP, ConocoPhillips and TransCanada — haven’t disclosed the exact specs they’re considering for the pipe, other than to say it would stretch about 800 miles and use up to 1.2 million tons of steel, twice the poundage of steel used for the Alaska oil pipeline.
The two partners taking the lead on the pipeline — Exxon and TransCanada — in 2012 did specify their plans for a somewhat larger-capacity 745-mile pipeline to the Canadian border that would continue on to Alberta:
The steel would average almost 1 inch thick — roughly twice the thickness of the Alaska oil pipeline. Thicker steel should resist bending better. Highly pressurized gas requires thicker steel than found in a typical oil pipeline.
The steel grade would be X80 — extra-strength steel that, if you extracted a plug from it and strained the plug, could withstand 80,000 pounds of pressure per square inch (psi), making it able to handle gas compressed to 2,500 pounds psi. By contrast, gas entering a typical home might be pressurized at a quarter-pound psi.
Pipelines have two built-in seams vulnerable to failure. One lies lengthwise, where the two ends of a steel sheet are fused to form a pipe — a “pipe-seam weld.” The other spans the circumference, where two lengths of pipe are welded together — a “girth weld.” Placing a girth weld where soil is transitioning between permafrost and unfrozen ground could invite trouble.
Designers can engineer pipelines to resist stresses and strains. Devices called “crack arrestors” can stop cracks from spreading and be placed closer together along the Alaska line. Thicker steel pipe is stronger; the pipe might be thicker under roads or rivers where ground pressure is greater. Also, high-strength steels will resist bending better.
But the industry’s ability to make 800 miles of consistent-quality, high-strength steel that’s an inch or more thick and ready for what Alaska can throw at it is out on the edge of the pipeline world would warrant extra attention from safety regulators. PHMSA’s regulations are pretty thorough when it comes to building new lines and operating the 2.6 million miles of oil and gas pipelines it oversees.
However, the regulations don’t really speak directly to the kind of severe longitudinal strain peculiar to Alaska terrain. “Longitudinal” strain refers to forces that can pull and bend the pipe, buckling it or splitting it open, such as slow, gradual bending from frost heaves or thaw settlements. Such as abrupt bending forces from earthquakes or frozen slopes prone to slumping (they have a word for that, too — “solifluction”).
Both PHMSA and the industry are conducting research to understand how much pipelines can take, how to get the best welding results, etc.
Federal regulations require a margin of safety to protect the public. A pipeline must be stronger than the stresses it will endure from pressurized gas or from longitudinal and lateral stresses — sideways and up-and-down pressure — due to soil movement. The more populated an area that the pipeline crosses, the greater the safety margin between the pipeline’s “specified minimum yield strength” and the internal and external stresses the steel experiences.
Another PHMSA safety official familiar with the Alaska project said the buried Alaska gas pipeline under discussion likely would operate with a smaller longitudinal-stress safety margin than the regulations allow. The pipeline would operate past “yield strength” and somewhere close to ultimate longitudinal strength of the pipe. And how do those bending stresses interact with internal stresses on the pipe from pressurized gas?
It’s not at all clear that making the steel stronger and ever-thicker will overcome what Mother Nature can serve up. Part of the answer may be new design techniques that the PHMSA regulations don’t specifically cover and that have come into use in the world of gas pipelines these days.
For the Alaska pipeline’s likely design features not addressed in the regulations, sponsors of the line would need a PHMSA special permit to show the design meets the regulations’ safety spirit. What do the sponsors plan to do to make the pipeline resistant to longitudinal strain? How will they monitor frost heaving and what will they do if they find problems?
The agency doesn’t hand out special permits like Halloween candy, but it has issued some when alternative safety measures are in place. Most special permits speak to pressurizing gas beyond what the pipeline regulations allow or about pipes transitioning between areas with different population densities.
PHMSA recently drafted some strain-based-design guidelines, Part 1 and Part 2, to help project developers in Alaska know what information PHMSA will need before issuing a special permit. A gas pipeline for the proposed Donlin gold-mine project in western Alaska was first to receive the draft guidelines this year. The 313-mile Donlin pipeline would cross about 100 miles of discontinuous permafrost terrain.
The proposed smaller-scale, state-sponsored gas pipeline project from Prudhoe Bay to South Central Alaska also received the guidelines, as did some federal agencies and ExxonMobil, TransCanada and ConocoPhillips, three of the companies considering the Alaska LNG export project.
Bill White may be reached at bwhite@arcticgas.gov.
Comments