March 2016, Vol. 243, No. 3
TechNotes
SwRI-Designed Computer Model Predicts Corrosion Risks
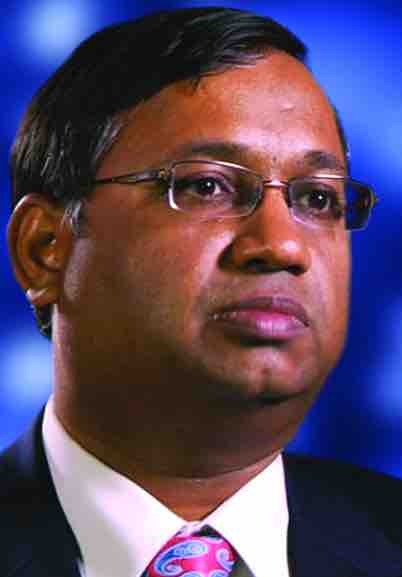
Oil and gas pipelines crisscross the nation beneath critical infrastructure, such as highways, railroads and waterways, as well as passing through population centers. Because over half of U.S. pipelines date to the 1950s and 1960s, corrosion prevention and related repairs are increasingly important to avoid pipeline failures that can lead to toxic spills or devastating explosions.
Ironically, pipeline segments that lie beneath some of the most sensitive areas are also among the most difficult to inspect. Because these segments need extra protection to avoid damage from nearby excavation, settlement, traffic loads and erosion, the carrier pipe is often encased within a larger-diameter reinforcing pipe.
These segments, called cased pipelines, are subject to not only the normal corrosion caused by time, moisture and soil chemistry, but also electrolytic corrosion from contact between the metals of the carrier pipe and its casing. In addition, the outer casings can adversely affect cathodic protection (CP) systems installed to reduce corrosion.
Cased pipelines often are sealed or have a separating medium such as wax placed between the layers of pipe. Over time, the seal can break, allowing the space between pipe layers to become filled with soil or water. Furthermore, the spacers that separate the carrier and casing pipe can break down over time, creating metallic contact between the carrier and casing pipes.
It is estimated that there are close to 1 million cased crossings in the United States, and about 40% of them may have degraded to the point of metallic contact between pipe layers.
External, visual inspection of cased pipelines is often impractical because of their location. Some are inaccessible. In other cases, obtaining a permit to perform an inspection dig may be difficult or impractical. Inspection of a cased pipe segment requires uncovering the segment, opening the space between pipe layers and inserting an instrumented probe between layers to inspect the inner pipe’s integrity.
Internal inspection by sending a tubular, instrumented device known as a “pig” through the carrier pipeline along with the product requires no excavation, but it is expensive and usually done only once every five years.
Modeling Hidden Risks
Engineers at Southwest Research Institute (SwRI) have developed the CAsed Pipeline COrrosion Model, or CAPCOM®, to predict the corrosion condition of these double-layer pipeline segments. CAPCOM uses a specialized application of the finite element method (FEM) to arrive at a mathematical model of the pipeline’s condition in relation to corrosion.
Mathematicians use FEM to model complex surfaces, structures, or even weather systems, by breaking the problem down into a large number of much smaller, simpler-to-solve components called “finite elements.” (Imagine approximating the area of a circle by turning it into a great number of extremely thin, pie-slice triangles.) Solutions to those smaller element equations are then recombined into a solution that approximates the whole. For a cased pipeline, FEM provides a tool for making improved predictions of the integrity, service life and corrosion risk.
A common source of corrosion in pipelines and many other metallic structures, such as ships or offshore oil platforms, is an electron exchange that happens when two dissimilar metals touch each other or are linked by an electrically conductive fluid, or electrolyte. (Salty sea water is an electrolyte; so are wet soil and rainwater with dissolved minerals.) As with a battery when the switch is turned on, a flow of electrons (electric current) begins, robbing metal molecules from the negative connection, or anode, and depositing them at the positively charged end, or cathode.
To mitigate this metal loss, pipeline operators employ cathodic protection, which makes the metal pipe the cathode of the “battery” and substitutes an easily corroded ”sacrificial” metal to act as the anode. The sacrificial metal corrodes instead of the protected metal of the pipeline. For pipelines and some other large structures, a direct-current electrical power source is installed to provide sufficient current. CP systems are used to control corrosion on critical steel structures of all sizes, from pipelines and ships to outboard motors and home water heaters.
In pipeline segments where visual or inline inspection is limited, CAPCOM can provide valuable information on corrosion conditions. By estimating pipe-to-soil electrical potential along the cased pipeline segment, and possible corrosion rates on the carrier pipe, CAPCOM can help determine whether the cased pipeline section is adequately protected, or if it is time for preventive maintenance.
CAPCOM can model complex corrosion scenarios, including electrolytic or electrolytic-plus-metallic contact between the carrier and the casing pipe, defects in the carrier pipe’s coating or combinations of these. It can identify the level of polarization of the cased pipeline segment and the rest of the nearby pipeline when there is electrolytic contact between the carrier and casing.
For pipeline segments that use a CP system to prevent electrolytic corrosion, CAPCOM can quantify the system’s effectiveness for mitigating corrosion. It also can quantify how much more CP current may be needed to adequately protect the pipeline when electrolytic contact between the casing and carrier pipe has been confirmed.
How It Works
CAPCOM employs the same basic mathematical input parameters used in existing models of CP systems for uncased pipelines (such as coating quality, pipeline material, anode output, and the electrical current flowing through the soil and the electrolyte). However, it adds inputs related to the casing pipe itself.
For example, CAPCOM inputs for both cased and uncased sections of the pipeline include their dimensions and coating properties, plus soil properties and any electrolytic properties that may exist inside the space between the casing and carrier pipe. CAPCOM analysis also includes the CP design used to protect both cased and carrier pipes in its models.
CAPCOM’s FEM method solves the model equations for predicting corrosion conditions of the cased-pipeline section. Using the FEM formulation, CAPCOM also can represent varying conditions that affect the carrier pipe, such as how the soil conducts or resists electrical conduction at different locations near the cased portion of the pipeline.
This capability sets CAPCOM apart from other CP models, which use a different modeling approach known as the boundary element method (BEM).
BEM-based software works best when modeling a homogenous medium – such as soil of uniform properties surrounding a pipeline – but it has limited ability to model how the surrounding soil or other fill material with varying chemical composition and moisture content affects pipeline corrosion. This limitation precludes using BEM tools for complex cased crossing conditions.
CAPCOM explicitly accounts for electrolytic-plus-metallic contact between carrier and casing pipe and the soil outside the cased crossing to determine the corrosion condition of the carrier pipe.
In CAPCOM, metallic contact and electrolytic contact are accounted for by modeling a resistor and an electrolyte, respectively, between the carrier and casing pipes. CAPCOM also includes specifications for modeling “coating holidays” – places where the protective coating is damaged or missing – both inside and outside the cased pipeline section. After all of the parameters are entered and limits are defined, CAPCOM models the corrosion environment and presents its results in two- and three-dimensional plots.
These plots include pipe-to-electrolyte potential for the cased and uncased carrier pipeline sections, as well as the state of the electrical current the CP system supplies to the carrier pipe. The model reveals whether the CP current is diverted to the casing pipe, indicating metallic contact between carrier and casing pipes. With CAPCOM, users can determine the level of CP the carrier pipe will need and evaluate the risk of external corrosion at “holidays” on the carrier pipe inside the casing.
Comparing Costs
CAPCOM saves costs compared to both visual and inline inspections. Visual inspection requires removing the topsoil over the pipeline, exposing the two ends of the casing pipe, and probing the interior with an inspection tool. Visual inspection can cost $50,000-100,000, depending on the size and location of the casing.
By comparison, analyzing pipelines with CAPCOM software requires only the associated engineering time for the analysis, once the software is purchased. Although the software has an estimated cost of $35,000, it can be used numerous times, allowing this cost to be spread over a number of evaluations.
Inline inspection using an instrumented pig costs $10,000-20,000 per mile, but it generally must cover long segments of pipeline to be practical, because the aboveground “launch” and “trap” stations for inserting and recovering the pig are usually about 20-50 miles apart. Also, pig inspections are generally carried out every five years, which could, in many situations, be insufficient to detect and prevent corrosion-induced damage of carrier pipe.
Limitations, Applications
CAPCOM does require a large number of input parameters to simulate the corrosion conditions of a cased pipeline. These parameters are determined by field measurements, which may not always be available. However, the SwRI team addressed this potential limitation by formulating CAPCOM such that when a parameter value is unavailable, a nominal value with a variability range can be substituted. Thus, pipeline behavior can be simulated for a range of parameters, yielding a range of expected corrosion conditions and electrode potential of the pipeline casing.
As a modeling tool, CAPCOM has applications not only as an alternative to direct pipeline inspection, but also as a tool to assess corrosion-inhibiting products used on pipelines. CAPCOM potentially can save human lives and millions of dollars’ worth of private property and public infrastructure. It enables reliable inspection and life prediction of critical pipeline segments that are, by their very nature, difficult to inspect.
This article is reprinted from Technology Today magazine, copyright Southwest Research Institute.
Author: Pavan Shukla is a senior research engineer in the Geosciences and Engineering Division at SwRI. He has expertise in modeling corrosion and chemical processes using finite and boundary element methods. His current work includes assessing degradation on both metallic and nonmetallic pipeline materials, and predicting localized corrosion-induced damage.
Comments