October 2016, Vol. 243, No. 10
Features
Integration of Engineering-Based Integrity Management Program
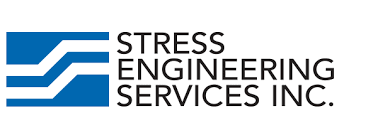
Managing pipeline integrity requires greater rigor than in previous years. The goal is to continue operating an aging infrastructure without incident while also meeting increased regulatory requirements and optimizing integrity dollars.
The industry currently has the basic tools to solve the simple or common integrity threats. In the context of this discussion, “tools” implies any resources used to address integrity issues, namely inspection technologies and analytical tools for evaluating the collected inspection data.
It is our observation that most pipeline companies perform integrity management using in-house methods or resources developed by consultants. As one would expect, much of this work is based on prior research and experience in dealing with specific anomalies.
Research has addressed the severity of plain dents through organizations such as the Pipeline Research Council International, Inc. (PRCI) and the American Petroleum Institute (API). Much of this work has been based on experimental results or numerical modeling using finite element analysis.
Over the past decade, increased emphasis has been placed on the importance of integrity management assessments. This is due in part to regulatory activity, but also because of the aging infrastructure of our nation’s pipeline systems. This article presents ideas associated with the development of an engineering-based integrity management program (EB-IMP).
This program is based in part on the principles embodied in the API 579 Fitness for Service document. At its core, API 579 makes use of a three-level assessment process to evaluate the fitness for service of a particular component or system. Much of this work was driven by the downstream needs in U.S. refineries. However, there are several sections within this document applicable to pipelines, including sections on corrosion in field bends and evaluating the effects of seam and girth welds in dents.
This article describes a five-step process for evaluating pipeline imperfections based on the EB-IMP. A flow chart of the process (Figure 1) builds on the basics of API 579. Pipeline companies can use the EB-IMP to evaluate the integrity of a selected anomaly using a methodology that integrates analysis and testing methods, as well as using prior experience and regulations set forth in the appropriate codes and standards.
History
Integrity assessment has always been a part of operations and maintenance activities. As the pipeline infrastructure has aged, industry first developed basic analytical tools and as their importance became apparent, these tools improved to meet the increasing needs. Then, as integrity concerns were identified, assessment methods were developed for the anomalies.
The Code of Federal Regulations (CFR), which governs gas transportation maintenance of pipelines, first required prescriptive methods, but were recently replaced with performance-based requirements.
Regulatory Oversight
The Pipeline and Hazardous Materials Safety Administration (PHMSA), formerly the Office of Pipeline of the U.S. Department of Transportation, has historically regulated the pipeline industry under Title 49, Transportation, of the Code of Federal Regulations, using a set of prescriptive requirements for design, operation and maintenance. Historically, this included specific repair options for a range of anomalies.
Recently, the regulations have allowed operators to repair anomalies using “a method that reliable engineering tests and analysis show can permanently restore the serviceability of the pipeline.” This change allows the pipeline industry flexibility when analyzing and repairing pipeline anomalies. In terms of technology, this phrase often leads to the deployment of composite repair technologies. This has been the case especially over the past decade.
Additionally, a small number of high-profile incidents have demonstrated that the original prescriptive code alone cannot ensure pipeline integrity. This resulted in the introduction of the Integrity Management Program, Title 49, Part O, which is a performance-based regulation requiring operators to demonstrate that the integrity of their respective pipelines in high-consequence areas (HCAs), typically involving greater population concentrations.
PHMSA also allows operators to develop an alternative solution to the prescriptive requirements on a case-by-case basis, with the understanding that the proposed solution will ensure pipeline integrity through other measures. These performance-based approaches offer many opportunities for individual pipeline operators to improve the integrity of their system by using EB-IMP solutions and more efficiently direct operation and maintenance dollars.
Basic Assessment Tools
The natural gas transmission industry has embraced the use of new technologies and strives to implement improvements to ensure safe pipelines. There are several examples that can be cited to demonstrate this point. One such example is pipeline corrosion. Industry first gathered wall-thickness data using low-resolution magnetic flux leakage (MFL) inline inspection (ILI) tools.
The results from these tools were recovered via charts and many man-hours of effort were spent to analyze the charts. The results from these analyses provided information on anomalies and indicated where resources should be directed in conducting physical examinations of pipelines. As the performance of ILI tools improved using better sensors, data storage and analysis, the information quantity and quality available grew exponentially.
Data may be pre-processed onboard the ILI tool, later analyzed in detail by the experts working for the tool supplier, and then provided to the pipeline company for use in making decisions regarding pipeline integrity and remediation requirements.
Other integrity threats have followed similar paths over the years. For example, ILI technology used to find mechanical damage, selective-seam corrosion and cracking has improved significantly over time.
Development of Eb-Imp Solution
API Recommended Practice 579, Fitness-For-Service, was developed for the refining and petrochemical industries in 2000 and takes advantage of improvements in inspection and analysis by providing a basic method for assessing “metallurgical conditions and analysis of local stresses and strains, which can more precisely indicate whether operating equipment is fit for its intended service.” These analyses address integrity concerns arising from historical design or fabrication imperfections or deterioration as a result of service conditions such as cracking or corrosion.
There are two elements not explicitly addressed in API-579. The first concerns the use of experimental methods, which can include in situ measurement techniques, to evaluate integrity. The other missing element concerns the development of repair techniques for the remediation of sub-standard equipment. It is recognized that the former might be a challenge in plant environments (performing a full-scale burst test on a multimillion-dollar vessel, for example).
However, full-scale testing is ideally suited for pipelines. In this regard, one purpose of the EB-IMP solution is to analyze relevant data and then develop cost-effective remediation methods to address integrity concerns. The resulting five-step process provides operators with a complete solution for the specific threat with the intent of meeting code requirements for a reliable engineering solution.
Referring again to Figure 1, review the five steps involved in the assessment process. A body of text is included in this figure that reads:
“After having completed the five-step process in evaluating a specific pipeline anomaly, the objective is to develop a general purpose assessment tool that permits a general evaluation of similar imperfections. In order to do this, the tool creator must have a firm understanding of the respective anomaly, including critical variables and potential modes of failure.”
As noted, the intent after having completed all five steps in evaluating a particular pipeline imperfection is to look for important variables and patterns that permit the development of a generalized tool. If this is not done, the operator misses an opportunity to build on existing knowledge and will be forced to repeat similar assessments in the future. The better option is to develop generalized assessment tools that permit the evaluation of a wide range of variables.
In the pipeline industry one of the best examples of a useful tool was the development of ASME B31G, and eventually RSTRENG, for assessing the severity of corrosion in a given pipeline. The critical variables associated with the tools were corrosion depth and length, along with information on the pipe such as diameter, wall thickness and material grade.
Collecting Critical Data
For most integrity assessments, the first step is often ILI inspection of the pipeline to determine where additional scrutiny is required. When integrity concerns are known, ILI may not be required. Following identification of the segment of concern, the detailed design, operating conditions and field measurements are gathered. These details are then used for the analysis. The data gathered will be used to determine the extent of the effort and perform the final analysis required. The quality of data collected in this stage of the effort is vital to ensure successful completion of the EB-IMP and deployment of a general-purpose tool useful for future assessments.
Level I Analysis – Basic: The effort involves the most basic form of an analysis that is possible. Typically, this includes performing an assessment based on industry codes or standards. For most pipeline operators this will mean referencing the original construction codes like ASME B31.8 for gas pipelines and ASME B31.4 for liquid pipelines.
Level II Analysis – Detailed: This requires more detailed information than a Level I assessment. The efforts involved in this phase are more complicated and the results are less conservative than those calculated using Level I methods. Examples of what might be involved in a Level II assessment would be calculations based on closed-form solutions such as those contained in API 579 or other engineering resources. This work is typically performed by an engineer experienced in pipeline design and operation.
Level III Analysis – Numerical: When the Level I and II analyses indicate that either the operating pressure must be re-rated in the pipeline or that a repair is necessary, it is possible to perform an assessment using numerical methods such as finite element analysis. The level of rigor is significant when compared to calculations completed as part of either a Level I or Level II assessment. On the other hand, the reward for completing a Level III analysis is a reduction in the safety margin associated with the previously two levels and a greater understanding about the actual load capacity of the pipeline or component.
As a point of reference, a Level I assessment will provide the design pressure for a given pipeline system. However, a Level III assessment calculates the ultimate pressure for the pipeline and a design pressure is then calculated from that value based on a given design margin. In this regard, the operator has a far greater understanding about the actual load capacity of his pipeline and the safety associated with his operation of the line.
It is likely the eventual EB-IMP general-purpose tool development will rely heavily on the finite element models generated as part of this phase of work. Typically, the original assessment looks only at one specific set of conditions for a given anomaly, whereas the FEA work associated with the general tool development considers a range of variables and operating conditions.
Level IV – Testing: The results of the engineering and FEA analysis can be confirmed via a testing program. A system has been developed for the pipeline industry that utilizes testing methods to augment integrity management efforts. Testing can involve either pipe material removed from service or pristine pipe, depending on the needs of the study. For example, if a pipeline company is interested in the performance of vintage girth welds subject to cyclic-pressure service, it would be prudent to remove girth welds from the field and test them.
On the other hand, if an operator is merely trying to quantify the relative severity of different-sized dents in the area of a girth weld, it would be possible to fabricate samples using modern pipes and welding techniques and then install the dents prior to testing. Fundamentally, the question that must be asked prior to testing is if the interest lies in actually quantifying the severity of vintage material or properties, or only in establishing general trends related to the anomalies’ severity.
Level V – Repair solution design: Remediation of common integrity threats can be accomplished using accepted repair procedures and these methods are, for the most part, well-suited and conservative. The information gathered and the analysis can also be used to develop a repair procedure tailored to meet the specific needs of the situation. These tailored repair solutions offer safe, cost-effective solutions in lieu of the one-size-fits-all, cut-out method of repair. The design for the repair can also be modeled using an FEA to evaluate suitability.
Conclusions
This article presented the fundamental elements associated with the development and use of an engineering-based integrity management program and provides the basics required to perform assessments based on this approach. It is the authors’ opinion that the distinction of this approach is the integration of actual pipeline data, coupled with analysis and testing efforts, to tailor engineering-based processes to address specific threats for a given pipeline system.
The result is that the EB-IMP process can address single critical integrity threats, or the process can be used to develop a general-purpose tool to address a range of threats found at several locations across a pipeline system. The process is based on basic engineering principles, followed by testing to confirm analysis results and reduce the potential for generating overly conservative restrictions on pipeline maintenance and operation.
The result is a process that remediates integrity threats, optimizes maintenance dollars and generates the documentation for in-house due-diligence efforts that can demonstrate system integrity to regulators and others.
Comments