October 2016, Vol. 243, No. 10
Features
Management Remains Key Issue in Pipeline Safety
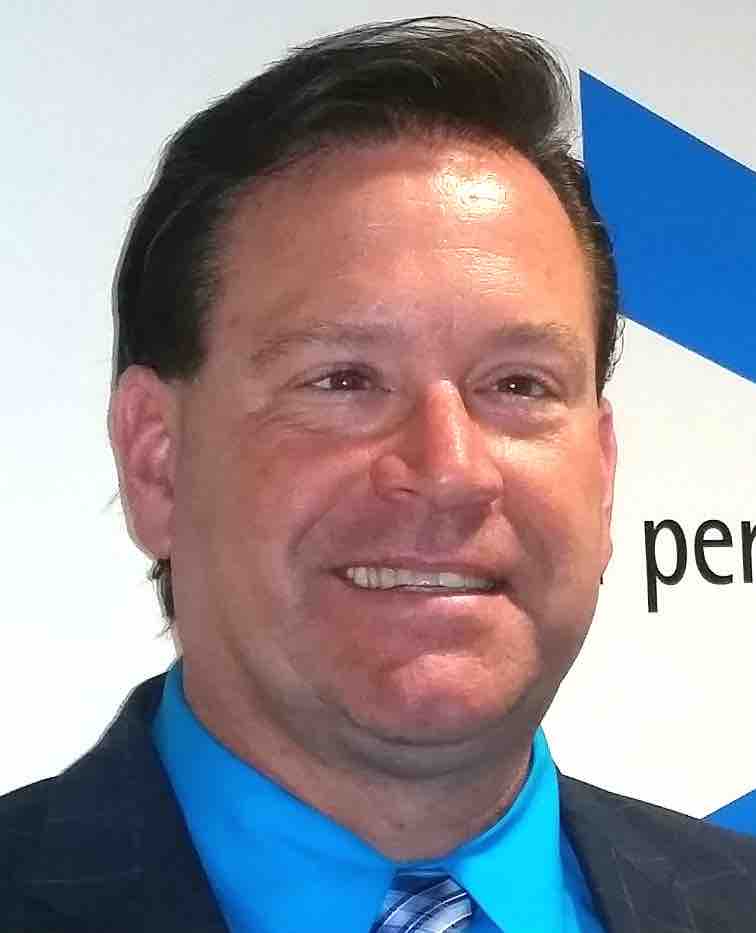
The rupture of a pipeline near Santa Barbara, CA on May 19, 2015 resulted in the release of an estimated 2,934 barrels of crude oil on land, on beaches and into the Pacific Ocean. The incident had serious consequences for the pipeline operator, which has spent over $150 million on the response effort, cleanup and related matters.
A year after the event, the U.S. Department of Transportation’s Pipeline and Hazardous Materials Safety Administration released the results of their investigation into the rupture. Their Failure Investigation Report identified external corrosion as the primary reason for the failure. The report also found, however, that several other factors contributed to the severity of the release, including the company’s failure to protect the pipeline from corrosion, and its failure to detect and respond to the pipeline rupture once it took place.
The American Pipeline Institute’s RP 1173:2015 (Pipeline Safety Management Systems) represents an industry effort to prevent such events. As RP 1173 points out, external corrosion, third-party operations and excavation have been the three top physical causes of pipeline disasters in the United States for over a decade. Underlying all three of these causes, however, is a less than full commitment by pipeline companies to having a safe work culture, one which embraces a continual improvement process. Industry-leading practices are well-recognized and understood, but pipeline operators need a clear path to establishing and maintaining safe management practices throughout the entire life cycle of their pipeline assets.
Establishing an effective safety management system is – or should be – a comprehensive, top-to-bottom process that engages not only the pipeline company’s management and employees, but its external stakeholders and its entire ecosystem of vendors, suppliers and contractors. Ideally, the process starts with a strong commitment from company leadership and senior management, up to and including the board of directors. An executive sponsor should have clear responsibility for program development and execution, with the full support of company management.
At this stage, the company needs to make it clear that safety management is a top priority, and that the executive sponsor will be in charge of a change-management program designed to educate all involved about the need for adjustments and the steps necessary to achieve that goal.
The next step in the process is stakeholder engagement. Internal and external stakeholders should be fully involved in efforts to articulate asset management policies and strategies for putting these policies into practice. The interests and concerns of various internal and external stakeholders should be mapped so potential areas of conflict can be identified and addressed. All involved parties should have an understanding of the company’s asset management objectives and the initiatives that will be undertaken to achieve these objectives.
Risk management is the next key element in building a safety management system. The risk management team works with operations, legal, finance and other functions to develop a comprehensive plan for risk identification and mitigation. As part of the plan, the team creates an enterprise-wide risk matrix that places asset safety within the broader context of other risks. The risk management team must also take responsibility for determining whether current risk assessment techniques – whether process-based, technology based or both – are acceptable and in which areas additional investment might be needed.
Taking Action
Strong leadership commitment, stakeholder engagement and risk management can be seen as preparatory and planning stages in which overall safety objectives are established, unmet needs are identified and processes put in place to reach agreed-upon standards and objectives.
EWith these management parameters in place, the program can focus on operational controls to address specific safety concerns. Operational controls can include stronger performance standards, new criteria for barriers to decrease the risk of rupture from excavation, and the implementation of new technology, such as electronic sensors to monitor flow and pressure. Operational controls also encompass the management of change at the field level, with training as needed for both company and third-party workers.
One commonly identified shortfall in safety management is that companies do not always have robust programs for incident investigation and evaluation, including a systematic process for capturing and disseminating lessons learned. This is an area in which innovations in risk management and analytics have improved the identification of non-conforming events which, if left unaddressed, could have significant consequences.
Improved root cause failure analysis techniques can now detail the sequence of events, the causal factors and the changes that result. Gaining a better understanding of how and why adverse events happen helps tremendously in taking the corrective actions needed to ensure such events do not happen again. Of course, the organization only receives such benefits if lessons learned are communicated thoroughly and effectively throughout all levels of the company.
Once operational controls are strengthened, the organization should turn its attention to safety assurance. Safety assurance incorporates both internal surveillance – conducted by designated teams from within the company – and external audits carried out by qualified outside inspectors.
Review of the safety assurance program should determine whether internal and external examinations are conducted with the appropriate frequency, whether they have the right scope and the right level of detail, and whether they are measuring the right things in terms of key performance indicators (KPIs). Another important element in safety assurance is ensuring that reports go to the right level of management and that, if problems are identified, those individuals have the responsibility and the authority to take immediate corrective actions.
Establishing Consistency
Identifying problems, taking corrective action and improving monitoring and surveillance are important elements of any safety management program. Taking the program to the next level, however, means putting in place a mechanism for management review and continual improvement.
When it comes to safety management, complacency is incompatible with excellence. Teams throughout the organization should be assigned roles with clearly defined schedules for improvement activities. The benefits of safety improvement initiatives must be identified, inventoried and communicated to internal and external stakeholders in order to achieve a robust safety culture.
Despite efforts aimed at managing risk, tightening controls and improving assurance, the possibility of a safety-related incident will always exist. The company’s emergency preparedness and response capabilities can mean the difference between a financial, environmental and reputational disaster and a relatively minor problem.
To deal properly with emergencies, the company should have an up-to-date matrix of likely events and create a chain of command with designated responsibilities for all involved. A detailed plan should address both the physical response to any event, and all aspects of internal and external communications. These include notification of and cooperation with the affected community, a plan for working with first-responders, and assembly of the company’s own quick response teams. Simulation exercises and full-blown training drills can help the company spot potential breakdowns in communication processes, resource allocation issues and other concerns.
The company must also undertake ongoing competence, awareness and training programs to ensure that the entire organization has the safety-related skills needed. These skills should be part of the description for each position; employees without the requisite skills should be reassigned or should receive training on an expedited basis.
Finally, documentation and recordkeeping are essential aspects of strong safety management programs. Safety management should have the same formal recording and reporting processes as other corporate functions (such as finance) with clear documentation for standard operating procedures, training and certification of key personnel, compliance with state and federal regulations, adherence to industry and company standards, and formal review and approval processes.
These organizational elements serve two key purposes: They help minimize risk (by encouraging employees to take safety seriously and to follow established policies and guidelines) and, if an event does take place, they help demonstrate the company played by the rules and did everything in its power to operate safely.
Delivering Value
Efforts to improve pipeline safety can only be expected to intensify, with pressure coming from both inside and outside the industry. By linking a disciplined, comprehensive approach to safety management with the adoption of new technologies to identify and remediate issues before they reach disaster proportions, pipeline companies can protect not only their operating assets but their reputations and their long-term ability to generate value for shareholders, customers and their own employees.
Although pipeline companies have been monitoring and gathering information from their pipelines for decades, most operators rarely use even 5% of the data. With the advancement of the Industrial Internet of Things (IIOT) and the ability to capture, visualize and compute the vast amount of data coming in, pipeline operators can now leverage technology to assist safety management.
One example of this capability is the Intelligent Pipeline Solution from GE and Accenture, the industry’s first comprehensive industrial internet solution for pipeline management.
By integrating data from across the enterprise into a common data platform with a visualization tool, companies have access to a traceable, verifiable and complete data set both to be proactive in decision-making and to speed response in the case of an incident. The company can know all the details of the asset at a location of an incident as well as the operating conditions, past repair history and even specifics on the surrounding area. This access to information in an event can allow the operator to make a faster, more informed decision on how to react operationally and how to direct emergency response.
The integration of various data sets also provides a platform to perform complex analytics within a simple user interface. Specifically, using an integrated data technology solution to run near real-time, interactive threat, risk management analytics can enable an operator to detect a potential risk before it occurs and prioritize remediation efforts.
The integration of data and analytics in decision-making for pipeline management as part of an operator’s safety management system improves the safety, integrity and reliability of a pipeline, and allows an operator to stay compliant with regulations. It also allows the operator to be more efficient with its operating and maintenance (O&M) spending while improving throughput and uptime of its operations.
Continual Improvement
The bottom line on pipeline safety management systems, as with any management system, is to create an organizational culture of plan-do-check-act in which both internal and external stakeholders’ expectations are clearly understood and met by appropriately managing the risk of the pipeline life cycle, while simultaneously increasing the value to the enterprise. This change in safety culture will fail without leadership demonstrating the importance of working safely, of providing a safe and reliable service to customers, of being vigilant and of earning the trust of the public through performance. This is possible by embracing and implementing the continual improvement embedded in API RP 1173.
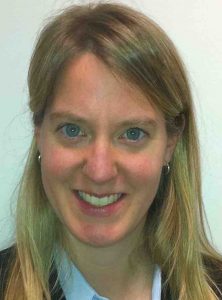
Comments