November 2021, Vol. 248, No. 11
Features
Leveraging 2 Kinds of Wisdom to Support Asset Integrity
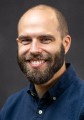
By Brian Cooper, President, HT Engineering
Imagine a bright, sunny Monday morning after a rainy weekend. In the office, your team is checking the input data from various sources for a risk assessment of your line, and all seems to be in order.
Then, imagine one of your field staff – we’ll call her Manuela – in her pickup truck on her way to visit the site of her crew’s next project. Manuela notices that the unusually heavy weekend storm scoured out a stream bed that previously covered a section of the line, so it’s now exposed. Maybe this is not an emergency, but it’s definitely a threat to the integrity of the pipeline.
Does Manuela have an easy way to report the problem – a way that allows her to indicate how serious the issue is and provide details so the Integrity team can adjust the risk profile of the segment and take appropriate action?
Data and Humans
For most pipeline integrity and risk assessment programs, there are two main sources of information. One is measurement-driven data that is fed into computational risk assessment tools. The other is information obtained from human observation or perception.
While hard data do require hardware, it’s usually not difficult to get it where it needs to go. However, human-driven information can be subjective and complex, and sometimes programs don’t have a good way to collect and incorporate it. But unless humans are removed completely from the integrity management process, human-driven information about potential problems must be identified, delivered, interpreted, and acted upon reliably and accurately if assets are to be kept safe.

With good data and good algorithms, rich insights can be gained – growing ever richer as more sensory devices deliver a broadening and deepening stream of data, and machine learning and other advances improve analysis and interpretation. As the results of computational risk assessment tools increase in value and the effort to obtain them decreases, it may be easy to leave the potential in human-driven information and assessment untapped.
However, at this point, there are simply not enough sensors in the world to replace the people who observe the operations and physical conditions of pipelines on a day-to-day basis.
Even if there were, no algorithms exist capable of replacing humans’ ability to recognize novel situations that present threats to integrity. And humans remain responsible for deciding how to respond to new information that doesn’t already have a place in the program’s “box.”
So, a comprehensive implementation of integrity management must include capturing insights and updates from staff – such as Manuela, and people like her – who have the personal experience on the line to notice issues like erosion at a waterbody crossing.
It must also include a process that responds to that information and incorporates it such that it appropriately influences the results of risk and integrity assessments. There are three areas to concentrate on to achieve this.
Programmatic
Putting systems in place for gathering and analyzing data is the first step in building systems that support gathering both human and electronic data. Integrity management systems can produce a flood of data – one of the keys is to gain operational insights from it.
We find that many pipeline companies are highly capable in gathering data and analyzing it for operational insights. They may be less effective at gathering and mobilizing human-generated ideas.
While the temptation might be to rely on members of senior management, it is important to get input from all levels of the organization. You also need to involve people like Manuela – people with the practical experience that comes from being out on the line every day.
Communication is a key aspect of pipeline integrity programs. You need good systems in place to make it easy for people like Manuela to report what she finds. This could include a dedicated phone hotline, or even just an email address – integrity@YourPipelineName.com – that is forwarded to people with the authority to make decisions on next steps.
Some companies have an online form that allows employees to report what they’ve seen. It’s whatever fits with your company’s culture and way of working.
Also, you need to make sure that the insights provided by operational staff and others are analyzed and interpreted soundly and consistently, so that risk assessments and priorities are adjusted accordingly.
Cultural
It is important to create an environment that values and uses human input. As well as providing the right tools, you need to create a culture in which those tools are being used.
Staff members who go to the effort of completing a field report on something like a washed-out streambed need to know that their input is valued and utilized. Otherwise, they won’t do it. Our industry has realized this with safety, and it’s time to think about integrity the same way.
As well as encouraging staff to voluntarily report integrity risks, it’s important to ask the right questions. Crew supervisors should be encouraged to get informal feedback from their crews.
One of the tools for doing this is decidedly low-tech: a box of doughnuts – or anything else that encourages tailgate conversations. These might include remarks like, “We’ve seen a lot of contractors’ trucks and surveyors’ flags. I hear that there’s a new subdivision going in, near the right-of-way.”
This might be a cue to have a conversation with those developers about the pipeline’s location, the need to call before they dig – and an upgrade to the risk profile of that part of the line. Open-ended questions can sometimes bring out insights that wouldn’t come with simple yes/no questions.
Once employees are made aware of the importance of informal feedback and the kinds of things to look for, it can help if they are incentivized to report. This can include anything from being included in their key performance indicators (KPIs) for annual review, to a restaurant voucher. Just be sure that systems are set up to reward good information, not just reports for the sake of reports.
News about sudden changes that may impact the line’s integrity are one thing, but you need to gather “soft” insights as well. This might include storing the fact that one of the landowners along the right-of-way rarely or never calls before digging.
Educational
The combined human and computational insights that you gather have a utility far beyond operational efficiency. They can be used to support training employees on how to operate the line safely. This can include refresher training, particularly when an employee is being asked to work on part of the line with which they are not familiar.
It can also include training new staff, providing them with the insights of other employees, some of whom are nearing retirement age. And don’t forget to use human insights to educate your algorithms. Ensure your tools and processes are easy to improve, and as people identify shortcomings in the computational model, update it accordingly.
Done right, human-driven and data-driven information can be combined to provide insights that help protect the integrity of your line – for improved safety, lower costs, and operational efficiency.
Author: Brian Cooper, PE, is president of HT Engineering, a pipeline specialist firm based in Grand Rapids, Michigan.
Comments