July 2022, Vol. 249, No. 7
Features
Taking a Look at 5 Opportunities in a Hydrogen Economy
By Angel Wileman, manager of the Thermofluids Section, Mechanical Engineering Division, Southwest Research Institute (SwRI)
The United States and many other countries have set goals to reach carbon neutrality by 2050 or sooner. To achieve this end, entire economies will need to be decarbonized.
Some of the largest carbon contributors are the power generation, transportation, residential gas and manufacturing industries. For more than a century, petroleum products have fueled these activities, and extensive capital has been invested worldwide to build up petroleum-based processes and infrastructure.
Upending the fossil fuels industry and redesigning the power grid in one fell swoop would be cost-prohibitive. An alternative, such as transitioning to hydrogen gas that works with existing infrastructure, could offer a more natural progression away from carbon-based fuels.
Consider power generation. Across the U.S., 61% of electricity is generated from natural gas and coal-fired power plants. In comparison, only 20% of our power is generated by renewables. A 10-year industry-wide pivot to renewable electricity generation is estimated to cost more than $4.5 trillion dollars, including a $32,000 price tag for individual households.
Incrementally transitioning to alternative fuels using existing infrastructure offers distinct advantages. For example, the power generation industry could begin blending small quantities of hydrogen gas into its natural gas pipelines within the next few years. This blended gas can be used at power plants to create electricity, or it can be supplied to residential homes for heating and cooking. The automotive industry has taken similar steps by blending hydrogen into diesel and natural gas engines to decarbonize large industrial vehicles.
Even these incremental changes in processes create technology challenges to be overcome in transitioning toward net-zero carbon emissions. Hydrogen gas, the fuel discussed in this article, presents challenges with high generation costs, safety and material compatibility.
Transitioning to a hydrogen economy will require multidisciplinary approaches and broad expertise, particular strengths available at Southwest Research Institute (SwRI). SwRI engineers and scientists are collaborating across multiple disciplines, looking at the opportunities and obstacles associated with this potentially clean energy source.
For example, specialists from the Chemistry and Chemical Engineering Division are studying hydrogen generation and safety. Teams from the Mechanical Engineering Division are looking at distribution as well as how hydrogen could be used for power generation. And Powertrain Engineering Division specialists are examining different techniques for using hydrogen in transportation applications.
SwRI is leveraging multidisciplinary approaches, working with U.S. government agencies and industrial partners to address technology challenges to move us closer to a carbon-neutral future.
Hydrogen Generation
One of the primary challenges that must be solved is with hydrogen generation. How will the world make enough hydrogen to put a dent in carbon emissions at a price point comparable with fossil fuels?
SwRI assists clients in areas of “clean” hydrogen production and using hydrogen in the production of fuels and chemicals. SwRI’s broad technology base offers an “all-of-the-above” option for our clients to develop, optimize and scale-up advanced production processes.
Hydrogen is already an important feedstock used to produce many of today’s fuels, lubricants and chemicals. The two main methods for generating hydrogen are steam methane reforming (SMR) and electrolysis. Both processes have potential to create hydrogen with low-carbon emissions, if implemented with carbon capture or renewable energy.
Industry traditionally uses SMR to produce hydrogen, combining methane and steam to produce hydrogen and carbon dioxide (CO2). In 2018, the U.S. produced 10 million metric tons of H2 through SMR, producing about 90 million tons of CO2 emissions. Because SMR produces most of the hydrogen used today, it offers a tremendous opportunity for reducing CO2 emissions. SMR technology is fairly mature, so the challenges lie with decarbonizing that process to make clean “blue” hydrogen. New carbon capture technologies have begun the transition from the laboratory into field application.
As industry works to use these emerging technologies, SwRI can provide expert assistance in scaling them up into pilot-scale and field-scale demonstrations.
Electrolysis produces hydrogen by splitting water into hydrogen and oxygen using electricity, special electrodes and membranes. Electrolysis typically requires a lot of power, but when the power comes from renewable sources, the resulting hydrogen has a minimal carbon footprint and is called “green” hydrogen.
The downside of electrolysis is that it relies on certain exotic metals and traditionally high-cost membranes. SwRI is researching ways to lower the cost of electrolyzer construction and improve current efficiencies.
Methane pyrolysis produces a new “turquoise” hydrogen from natural gas without CO2 emissions. The thermal process has been used commercially for years to create solid black carbon materials used in rubbers, tires, plastics and coatings.
It breaks down the methane in the absence of an oxidizer, producing hydrogen gas and a solid carbon byproduct instead of gaseous emissions. Industry is now researching unique reactor designs or process conditions to reduce the energy penalty and carbon footprint associated with the thermal-based conversion process. Chemists are also designing a flexible process that can adjust to market demands for carbon products.
– Eloy Flores III, Director, Chemical Engineering
Hydrogen Safety
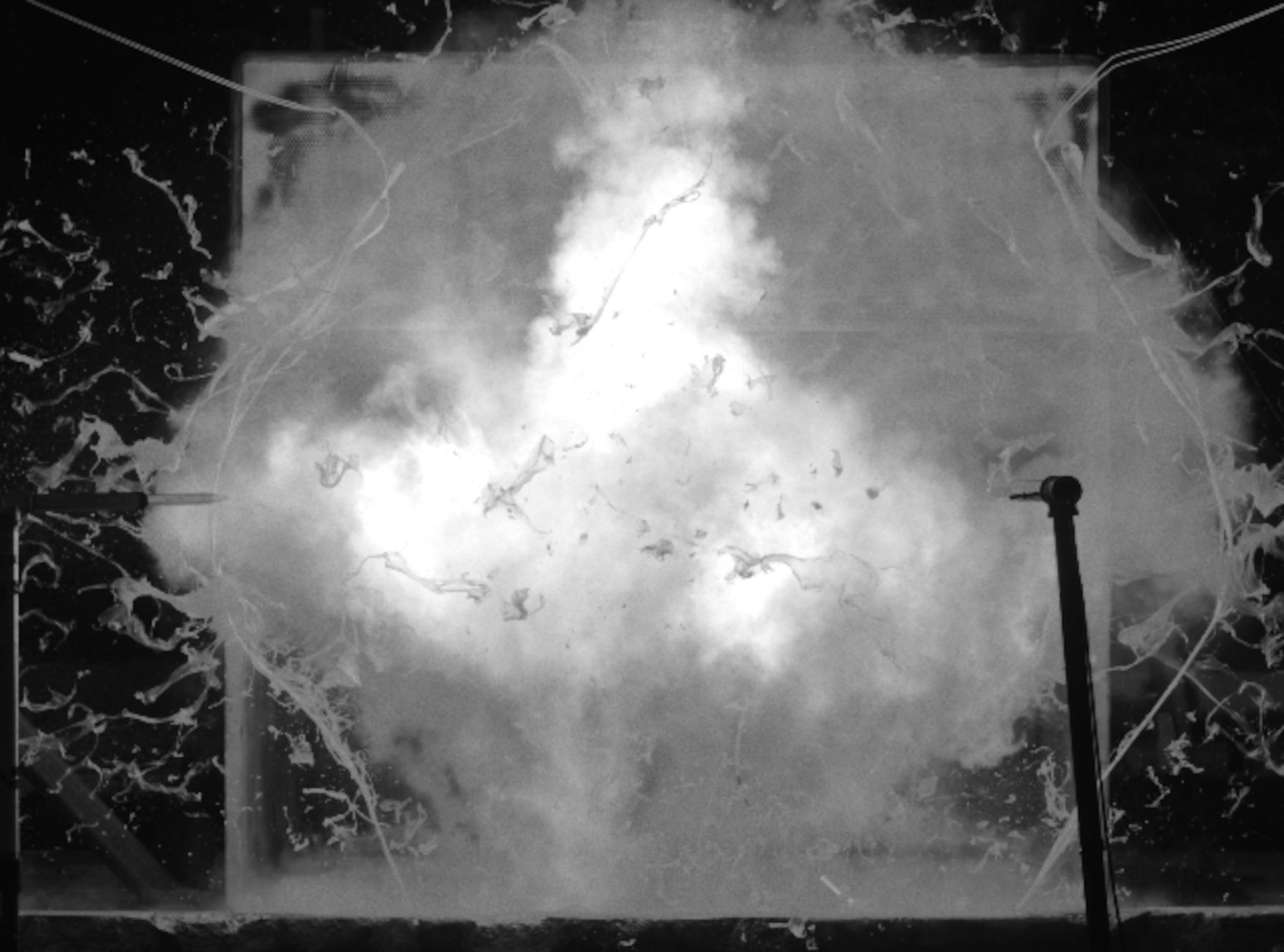
Hydrogen is a small molecule. It is also one-quarter the density of natural gas, which makes it difficult to contain. It can leak out of storage vessels and pipelines at a more rapid rate than natural gas, and when it escapes, it can ignite and/or explode over a wide range of concentrations.
Hydrogen is a colorless, odorless and tasteless gas, and its flames are nearly invisible to the human eye, making the hazard harder to detect. So, how do we safely harness and use this energy resource?
As hydrogen becomes a larger part of the energy sector, the gas will be integrated into homes and businesses. Using modeling and testing, SwRI takes a holistic, multitiered approach to assess risk and consequences and develop mitigation techniques.
In particularly complex or hazardous environments such as a chemical plant, engineers can use custom computational fluid dynamics models to investigate incident scenarios.
Using internal funding, SwRI developed a new computational capability to simulate gas-phase detonations for real-world scenarios that involve large-scale, complex domains and heterogeneous, multicomponent mixtures. SwRI researchers performed experiments to measure the overpressures that occur in a partially confined structure in the event of a detonation of hydrogen-air or methane-oxygen mixtures.
When models are not enough, SwRI performs large-scale experiments to gain a real-world understanding of the hazards of hydrogen gas. Engineers pressurize hydrogen vessels to their limit and test for weaknesses through scenarios such as bullet penetration and fire proximity.
SwRI also collaborated with the National Institute of Standards and Technology (NIST) to conduct a series of experiments, releasing hydrogen at various concentrations into full-scale residential garages – with and without an automobile present – that were then ignited. The findings helped create safety recommendations for the automotive industry.
– Alexandra Schluneker, lead engineer
Hydrogen Distribution
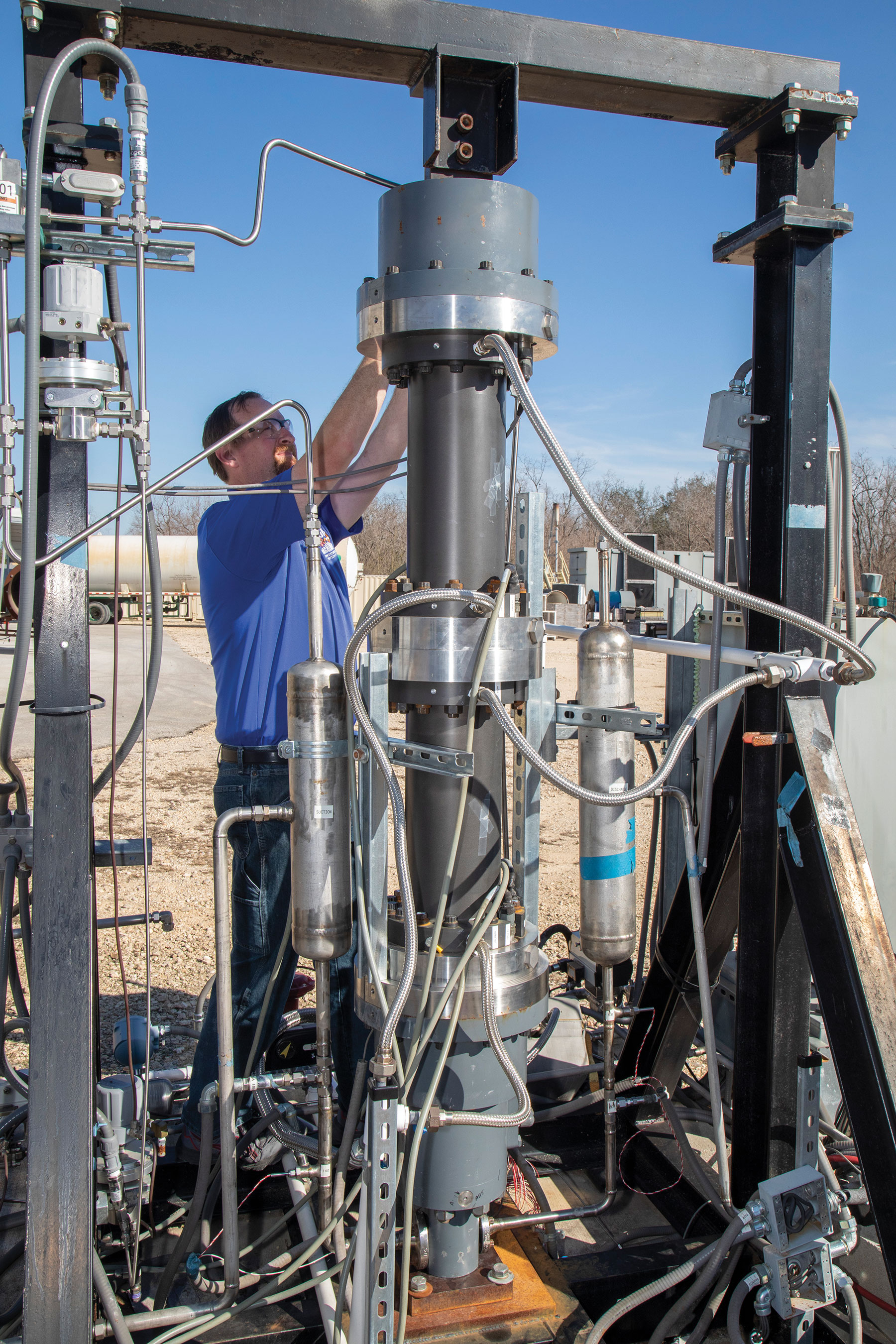
Moving hydrogen from the point of distribution to the point of end use presents an array of technical challenges. The low density of hydrogen gas presents efficiency challenges for pressurizing the gas and pushing it around the country in pipelines. Hydrogen’s associated small particle size also increases the potential for gas leaks in flow equipment.
In addition, hydrogen is associated with increased fatigue crack growth rates, dramatically reducing the toughness of typical flow component steels and welds. This can lead to catastrophic failures in distribution equipment. SwRI is conducting research to address these challenges across the gas distribution industry.
Compressing hydrogen for pipeline distribution or as a transportation fuel is energy-intensive and challenging from a materials and reliability perspective. To address the need for faster and higher compression rates, SwRI designed, built and tested a novel, hermetically sealed, linear motor-driven reciprocating compressor (LMRC).
This hydrogen compressor demonstrated enhanced reliability characteristics and leak-free performance for the transportation industry and beyond.
The U.S has approximately three million miles (4.8 million km) of natural gas pipelines, but only about 1,600 miles (2,575 km) are dedicated to hydrogen. As a result, the industry is investigating using existing natural gas piping networks to transport cleaner blends of natural gas and hydrogen.
SwRI is performing targeted research to understand potential impacts on pipeline operation, including relatively small volumes of hydrogen (up to 5%). Additional experiments and design activities will help industry address these challenges and include materials and leak detection testing for blended gases.
SwRI engineers are also characterizing how hydrogen blends affect the mechanical response of a variety of materials used in hydrogen gas transportation and integrating these results into integrity strategies. These fitness-for-service and engineering assessments are critical to determining safe operating conditions, minimum flaw sizes and inspection intervals.
SwRI performs mechanical testing in high-pressure hydrogen and blended-gas environments (up to 3,000 psi [207 bar] and 500°F [260°C]) by coupling autoclaves to servo-hydraulic load frames.
Engineers perform tensile, fracture toughness, fatigue crack growth rate, crack arrest threshold and strain-controlled and load-controlled fatigue tests according ASTM standards in relevant environments. This battery of tests is used to develop fitness-for-service analyses and ensure safe operation of structures and infrastructure. Additionally, SwRI supports the U.S. Department of Energy (DOE) HyBlend program to address pipeline material challenges caused by blending hydrogen with natural gas.
– Eugene “Buddy” Broerman, principal engineer
Hydrogen for Power Generation
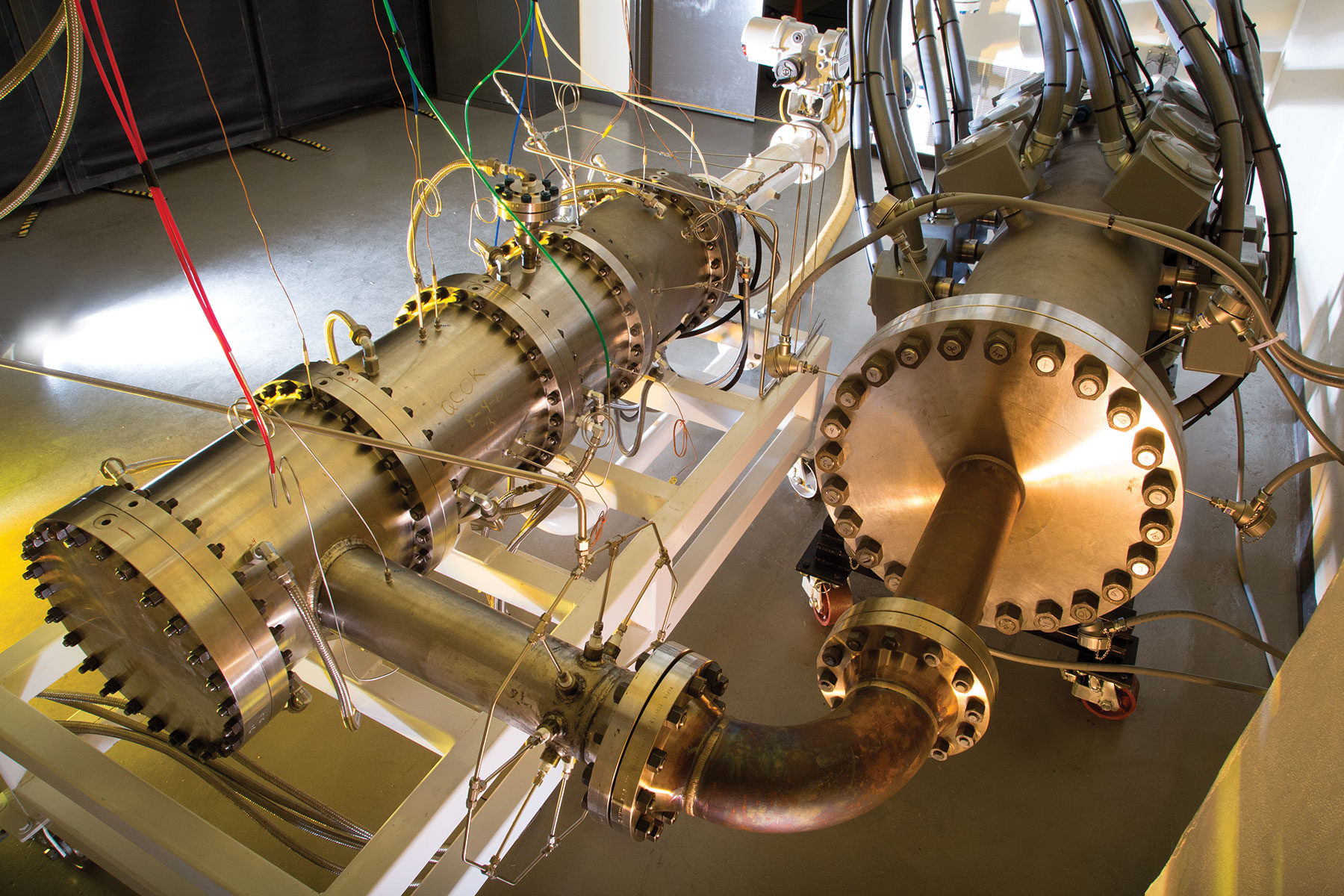
More than 40% of electricity in the U.S. is currently produced by burning natural gas in large combined-cycle power plants that often include both gas and steam turbines. Despite producing about half of the CO2 emissions of a coal-based power plant, natural gas power plants still produce significant amounts of CO2. In contrast, hydrogen-based power shows the potential for zero-carbon emissions.
Like natural gas, hydrogen can be stored for extended periods in underground caverns, either as pure hydrogen, in hydrogen carrier compounds such as ammonia or through molecular adsorption into materials. SwRI’s Sorption Science Laboratory evaluates the properties of potential hydrogen storage materials, measuring the performance of a variety of natural and synthetic adsorption materials.
For instance, SwRI is part of a team working on the integration and techno-economic assessment of a high-density Cryogenic Flux Capacitor that stores hydrogen in an aerogel material at cryogenic temperatures. The team will integrate this technology into a 100-MWh system at a natural gas combined-cycle power plant for evaluation.
Hydrogen is not, however, a drop-in replacement for natural gas in a conventional power plant because of the differences in combustion characteristics. Hydrogen has a much wider flammability range, lower autoignition temperature and faster flame speed than natural gas, which could result in damaging “flashback” conditions.
SwRI is helping design and test next-generation gas turbine combustors that adapt the combustor geometry for hydrogen. These hydrogen-appropriate designs include “micromix” injectors with many small flow passages.
Spark-ignited, natural gas reciprocating engines widely used for power generation, as peak-shaving assets for power plants or for distributed power generation, can be adapted to natural gas/hydrogen blends or pure hydrogen.
These power generation assets stabilize the grid as power demand fluctuates and provide backup power in the event of a supply disruption. Like gas turbines, reciprocating engines are sensitive to the combustion characteristics of hydrogen or hydrogen/natural gas blends that can contribute to abnormal combustion events resulting in engine damage.
Through a combination of simulation, single-cylinder and multicylinder engine testing, SwRI is developing port- and direct-injection combustion systems and strategies to enable the use of hydrogen and hydrogen blends in these engines, while minimizing chances for abnormal combustion.
SwRI has several specialized facilities to support the development of hydrogen engines up to 5 MW and can blend hydrogen with natural gas to facilitate engine testing.
– Tim Allison and Tim Callahan
Hydrogen In Transportation
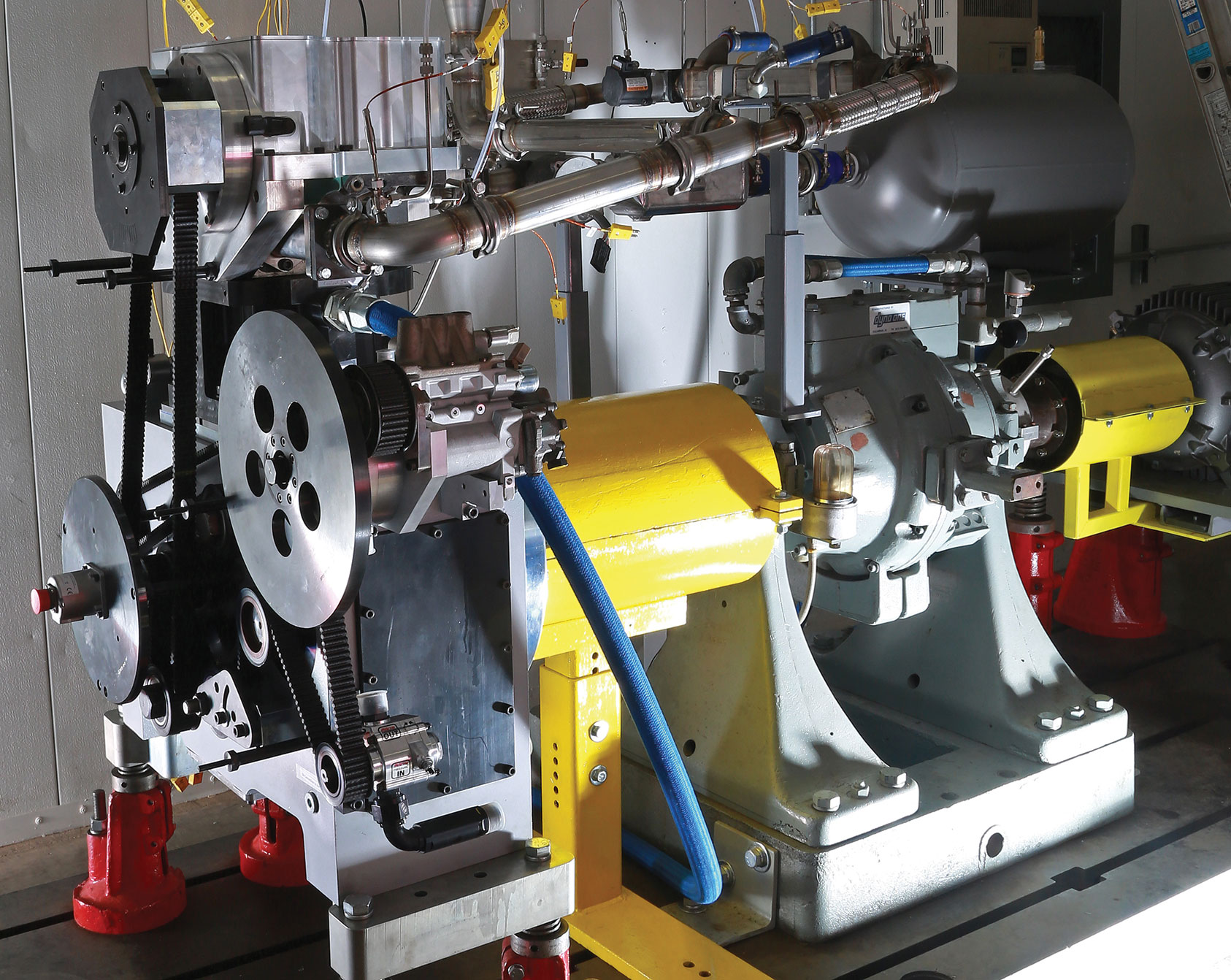
Transitioning the transportation industry to hydrogen fuel to lower tailpipe CO2 emissions is a major technology and infrastructure development undertaking. Traditional internal combustion (IC) engines power today’s ships, trains and automobiles (both highway and off-road), and there is no one-size-fits-all replacement technology.
While battery power will likely be the ultimate low-emission solution for passenger vehicles, hydrogen shows promise for the remainder of the transportation industry. Hydrogen can either completely replace or supplement traditional fossil fuels in IC engines or it can be used in fuel cell powertrains. Both solutions lower tailpipe CO2; however, they also present unique technical challenges.
Hydrogen fuel cell electric vehicles (FCEVs) are on the cusp of maturity and an interesting alternative, particularly where battery power is not yet feasible, such as for large vehicles. However, fuel cells require a special high-purity hydrogen and are currently more expensive to produce and less durable than IC or battery powertrains. In contrast, the existing engineering, manufacturing and servicing infrastructure for IC engines is favorable for near-term transitioning to hydrogen IC engine solutions.
Using internal funding, SwRI is benchmarking one of the few commercially available FCEVs on the market, subjecting the vehicle to a barrage of tests and using the data to determine baseline characteristics. Benchmarking will allow SwRI to understand how current hydrogen-based FCEVs should perform and help establish a basis to compare future iterations and other FCEVs.
Additionally, because fuel cells require different accessories than traditional internal combustion engines, the data may help material component suppliers and manufacturers prepare for future needs.
SwRI Principal Engineer Dr. Graham Conway, a leader in the Powertrain Engineering Division’s Technical Planning and Roadmap Strategy steering group, is studying cleaner hydrogen-fuel engine applications.
Hydrogen fuel can also decarbonize tailpipe emissions in IC engines. Spark-ignited IC engines burn gasoline and natural gas while diesel fuels compression-ignition engines. Because properties of these fuels lend themselves to their respective combustion modes, hydrogen has unique properties, supporting both spark-ignition and compression-ignition engines.
For example, a high burn rate, low minimum ignition energy and wide flammability limits permit stable combustion under high-efficiency, dilute conditions. In spark-ignition engines, the low minimum ignition energy can also lead to challenges with controlling combustion, while high autoignition temperatures create challenges in compression-ignition engines.
SwRI has developed a multimode combustion solution that takes advantage of positive fuel properties while minimizing the effects of negative properties associated with each combustion mode. Using internal funding, engineers are testing and modeling the globally patented multimode solution to optimize each strategy.
– Graham Conway, SwRI principal engineer
Comments