July 2022, Vol. 249, No. 7
Guest Commentary
Dealing with Lack of Universal Sleeve Manufacturing Specifications
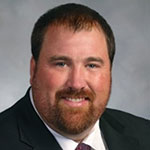
By Allan “Chip” Edwards, IV, President, Allan Edwards, Inc.
Full encirclement steel sleeves have been a popular repair solution for more than a century and are widely used by pipeline operators.
Yet, despite their common acceptance and steady popularity, there is no manufacturing specification governing the fabrication of steel repair sleeves either recognized or enforced by any regulatory body in the pipeline industry.
While plenty of regulations detail usages and applications for full encirclement sleeves, as well as minimum standards for their installation, there is no formal baseline that sleeve manufacturers must abide by when fabricating repair sleeves.
In short, this means that there is no standardized method for operators to verify the quality of manufactured sleeve material they receive from a sleeve vendor, aside from a visual inspection and any required documentation like material test reports (MTRs).
Regulations such as American Petroleum Institute (API) 1176 dictate which types of defects that repair sleeves can be used to reinforce. Other documents such as ASME B31.8 and ASME PPC-2 recommend welding procedures when installing repair sleeves as well as minimum wall thicknesses, design pressures, lengths and grade requirements that vary with each pipeline anomaly.
However, aside from visual inspection, heat number logging and MTR traceability, there is no acceptance (or rejection) standard used to assess the quality of manufactured repair sleeves, nor is there a required set of engineering tests that sleeves must undergo.
Manufacturing requirements and quality assurance testing have been left to individual fabrication shops to determine – unless operators provide their own unique sleeve specifications.
Repair Sleeves
Aside from the absence of a universal manufacturing specification, an interesting discussion point has arisen in recent years centering around the definition of a welded repair sleeve.
Some operators interpret a full encirclement sleeve exclusively as two pieces of split half pipe. By this definition, steel repair sleeves manufactured from rolled plate would not be considered a repair sleeve.
This distinction is marked by the intensive hydrostatic testing and other engineering tests that in-service pipelines – and, by extension, split half pipe sleeves – must undergo to qualify for service. These rigorous testing requirements alone act somewhat as a manufacturing specification.
Because of their stringent testing requirements – and the lack of a universal sleeve manufacturing standard – some operators prefer split half pipe sleeves to repair sleeves manufactured from rolled plate. Unfortunately, this type of repair sleeve can be extremely expensive for operators, results in substantial waste, and contributes to fit-up problems during installation.
Split Sleeves
The fundamental issue with constructing sleeves from split pieces of half pipe is that the inner diameter (ID) of the 180-degree sleeve half will not fit effectively over the outer diameter (OD) of the same size pipeline. For example, attempting to fit a 24-inch half pipe sleeve over a 24-inch pipeline will result in a fit-up gap because the pipe OD is larger than the ID of the split pipe sleeve.
To account for this ID/OD differential, the sleeve halves must each be cut to cover a minimum of 185 degrees of the pipe surface, or 370 degrees of the total circumference. Loosely translated, twice the amount of pipe is needed to complete a single split pipe sleeve repair compared to ordering the exact required amount of manufactured repair sleeves.
Even if a larger-diameter split pipe sleeve were used, it would have to be re-rounded to fit the smaller pipeline – a scenario not possible in the field. Fit-up issues are common with split pipe sleeve repairs because the sleeve halves have not been made to fit together well.
Understandably, the blurred regulatory clarity on sleeve manufacturing standards as well as the differing opinions on what constitutes a repair sleeve has led some operators to stay away from steel repair sleeves altogether, whether constructed from split pipe or manufactured from rolled plate.
What Now?
The bottom line. It is assumed that steel repair sleeves have a comparable integrity to pipeline steel. It is also assumed that steel repair sleeves are an effective long-term repair solution to reinforce pipeline defects. However, unlike pipeline steel, repair sleeves require no product validation testing to qualify them as a viable repair option.
While steel repair sleeves are presumed to provide the same reinforcement and pressure capacity as the pipeline steel they are repairing, sleeve manufacturers are not required to show any proof that this is true. Why is this? Because there is no industry-recognized universal product manufacturing standard or specification for steel repair sleeves.
This had led some pipeline operators to exclusively use sleeves constructed from split pieces of half pipe, despite their high costs and pervasive fit-up problems. While it is unrealistic to expect manufactured sleeves to be held to identical testing standards as pipeline steel, there should be a unified standard to which repair sleeves conform. Currently, there is none.
Do you think there should be?
Comments