June 2023, Vol. 250, No. 6
Tech Notes
Tech Notes: Cold Bonding Used to Restore Pipeline
By Mark Docherty, Belzona
(P&GJ) — Evaluation of a facility, based in the north of Thailand, found that a huge pipeline carrying high-pressure water for injection into oil wells was suffering from thin wall defects. The pipeline in question was made out of 39-foot (12-meter) pipe lengths that had been welded together.
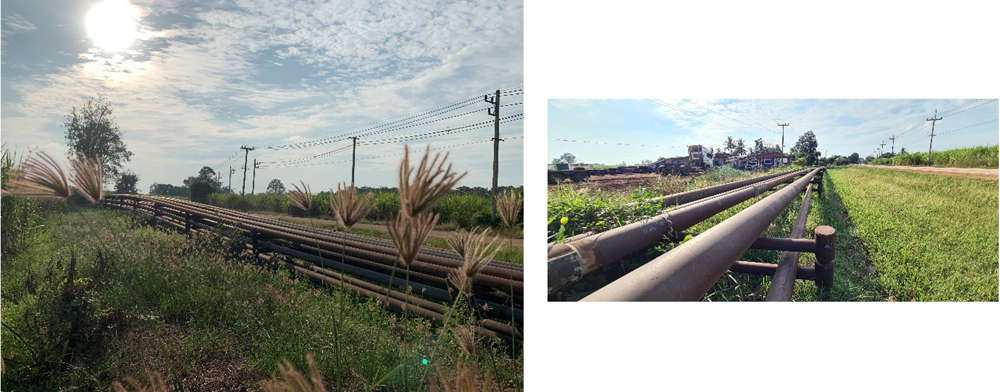
Upon inspection, it was discovered that the 2,000 psi of water and the weld filler material in use had resulted in internal corrosion defects at every circumferential weld joint. This caused the deterioration of pipe wall thickness, risking high-pressure leaks.
The customer had used Belzona previously and was impressed by the cold bonding process demonstrated on a defective joint, which led to an agreement to undertake the repair of the entire pipeline, requiring an estimated 11,000-15,430 pounds (5,000-7,000-kg) of Belzona 1111 metal.
Due to the scale of the project, repair would be completed in three stages. More than 1,000 joints were repaired in 2020, and the remaining defects were addressed in November and December 2022. The joints repaired in the first stage performance went well when placed in service.
The use of welding had been a in the past, leading to a preference for a cold bonding solution. Testing found that attaching carbon steel reinforcing plates, using Belzona 1111 as a bonding agent, would be most appropriate.
The simpler cold bonding repair would be more cost effective and ensure a faster return to service in line with the customer’s requirements.
The surface was prepared using garnet blasting and cleaner/degreaser to achieve an average minimum of ≥75 μm (3mils) profile and SA2.5 surface cleanliness for maximum adhesion. The atmospheric conditions were then tested to ensure that the relative humidity was below the maximum permitted 85% needed for the application to take place.
Welding rods were used to create a shim between the steel plates and the repair area to control the thickness of the application. The welding rods were bonded to the steel reinforcing plates and the repair area was identified using masking tape.
The repair composite was first applied to two of the four plates and the damaged pipeline joint and held in place using a fixed hoist while the product cured. Once the first two plates had bonded, the final two plates were applied and allowed to cure, fully encompassing the circumferential joint.
Comments