August 2011, Vol. 238 No. 8
Features
Ultrasonic Guided Wave System Developed By PetroChina
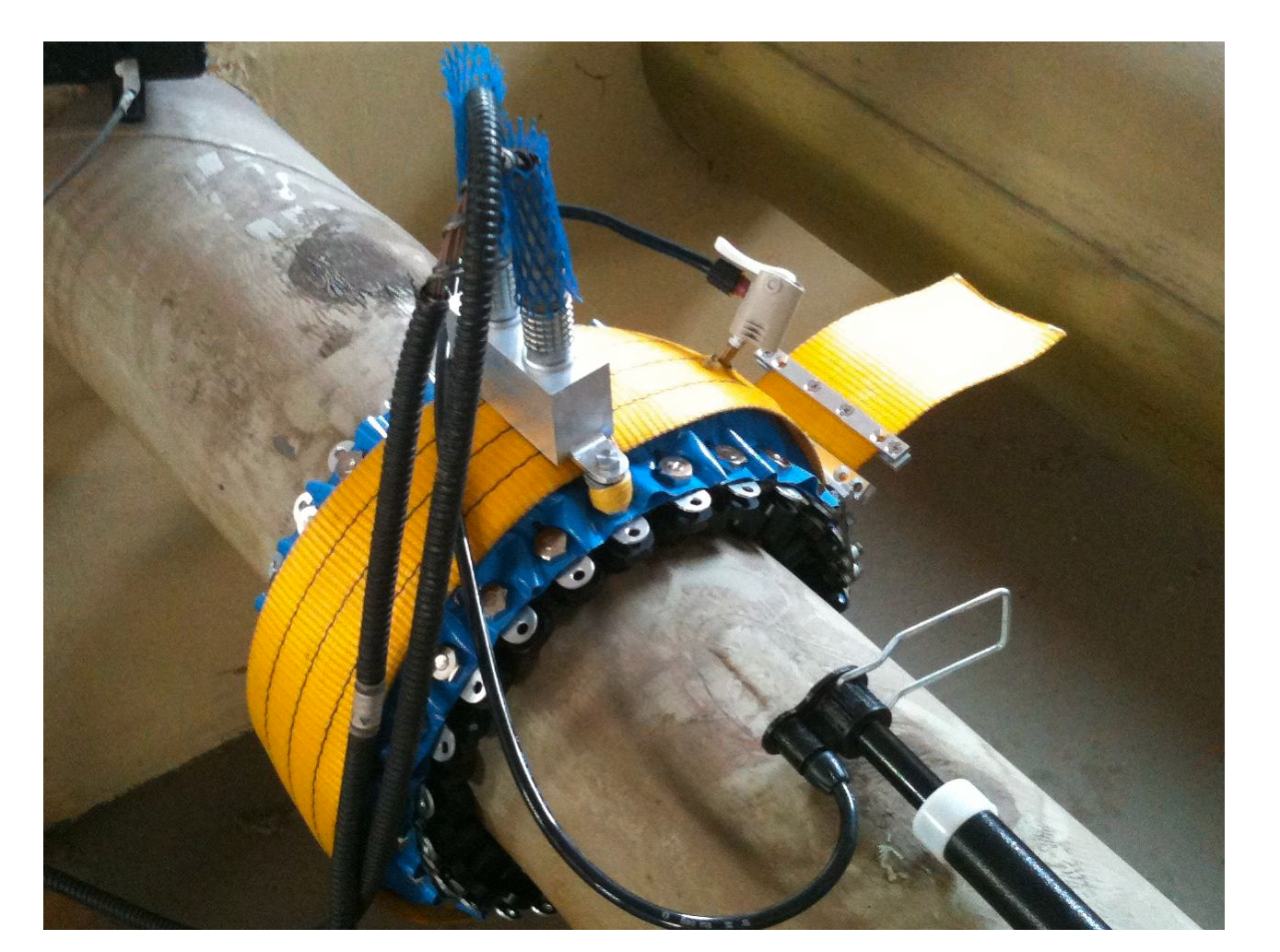
PetroChina Pipeline Research Center (PPRC) developed the PUGW-1 pipe screening system based on ultrasonic guided wave (UGW) theory during 2005-2009. PRRC is China’s largest research center focusing on oil and gas transmission and storage-related research.
Here is the system at a glance. The PUGW-1 pipeline inspection system sets the standard for guided wave testing and is employed in many pipeline inspection tasks in PetroChina.
Today in the area of oil and gas transmission pipe inspection, high-resolution tri-axis magnetic flux leakage system is usually employed for the trunk line inspection, electro-magnetic inspection system is for the lateral-line inspection, and the ultrasonic guided wave inspection system is appropriate for the pipe in the transmission stations. These three techniques secure the pipe safety.
The PUGW-1 system uses low-frequency guided ultrasonic waves (usually 100 kHz) to inspect tens of meters of pipe from a single remote location. The advantage of this system is that it can detect defect conditions on pipe that is inaccessible – such as pipe under road crossings or pipe that is underground in oil and gas transmission stations. Another advantage is that the inspection can be performed while the pipe is in service. The system’s key features: 1) cross sectional area metal loss displays, 2) fast pipe survey and low cost, 3) easy to operate, and 4) portable.
Working Principle. The ultrasonic guided wave propagates along the axial direction of the pipe. The wave is composed of 1) a torsional wave and 2) a longitudinal wave.
The wave propagates along both sides of the pipe from the test point. When the wave meets the defect, part of the wave will be reflected. The reflected wave is composed of two modes, one of which is the axisymmetric wave and the other is the non-axisymmetric wave. The defect recognition is achieved by analyzing these two kinds of reflected waves.
In practice, a transducer ring is mounted on the pipe. Torsional waves are excited by tone-burst signals generated from the signal generator which is integrated into the instrument. When the wave meets a defect, the response wave will be received by the transducer ring. The defect information – i.e. signal amplitude and defect location – can be obtained by analyzing the axisymmetric and non-axisymmetric electrical signals which are transformed from the waves.
The transducer rings use mechanical or pneumatic pressure to couple piezoelectric transducer elements to the pipe being inspected. Transducers attached to the pipe send waves tens of meters along the pipe wall and the returning echoes indicate defects and other features. Therefore, long lengths of pipe are examined from one location. This allows difficult-to-inspect areas such as under roadways to be screened with ease. Minimal preparation before the test is required. Features: 1) no couplant required, 2) easy to install and uninstall transducer ring, 3) minimal cleaning required.
The PUGW-1 software offers the data collection, analysis and report generation options that greatly improve productivity and ease of report generation. The software is easy to use and user-friendly. Also, it has embedded documents, charts and various templates.
The software offers advanced analysis tools which dramatically increase sensitivity while simultaneously reducing false calls. This increases productivity. These analysis tools include: 1) detection of mode converted signals, 2) dynamic frequency sweeping, 3) automatic ring detection and configuration, 4) interface to GPS receivers, 5) sophisticated DAC prediction, 6) cross sectional area loss displays, and 7) detailed diagnostic information.
At the end of 2010, China had a total of 50,000 km of oil and gas pipelines. That number will double by 2015. This indicates a prosperous future for the ultrasonic guided wave technique and the PUGW-1 pipe inspection system.
—
PetroChina is China’s largest oil and gas producer and supplier, one of the world’s major oilfield service providers and a globally known contractor in engineering construction. In 2015, it will own 48,000 km of pipeline for natural gas, crude oil and products. An accurate, adaptable, and portable pipe screening system is desired by the company for pipe safety management.
Authors:
Weibin Wang, Ph.D., is director of the anti-corrosion branch of PetroChina Pipeline R&D Center. He has held this position since 2009. He is responsible for pipeline and storage tank inspection and assessment technique R&D and integrity management.
Zhanjun Feng, Ph.D., is the senior research engineer at PetroChina Pipeline R&D Center. He has held this position since 2009. He is responsible for pipeline inspection and assessment technique research and development. kjfengzj@petrochina.com.cn.
Jianfeng Chen is vice president of natural gas pipelines for PetroChina and is responsible for all research issues involving the natural gas pipeline company and its subsidiaries.
Hongjun Dong is director of the production department of PetroChina Pipeline Co. and is in charge of work associated with transmission stations and storage tanks.
Choumin Zhao is director of the S&T management department of PetroChina Pipeline Co. and is in charge of R&D project initiation approvals, checks and acceptances. He also is responsible for standards management.
Comments