March 2011, Vol. 238 No. 3
Features
NACE Interview: Integrity Management Solutions For Offshore Pipeline Corrosion
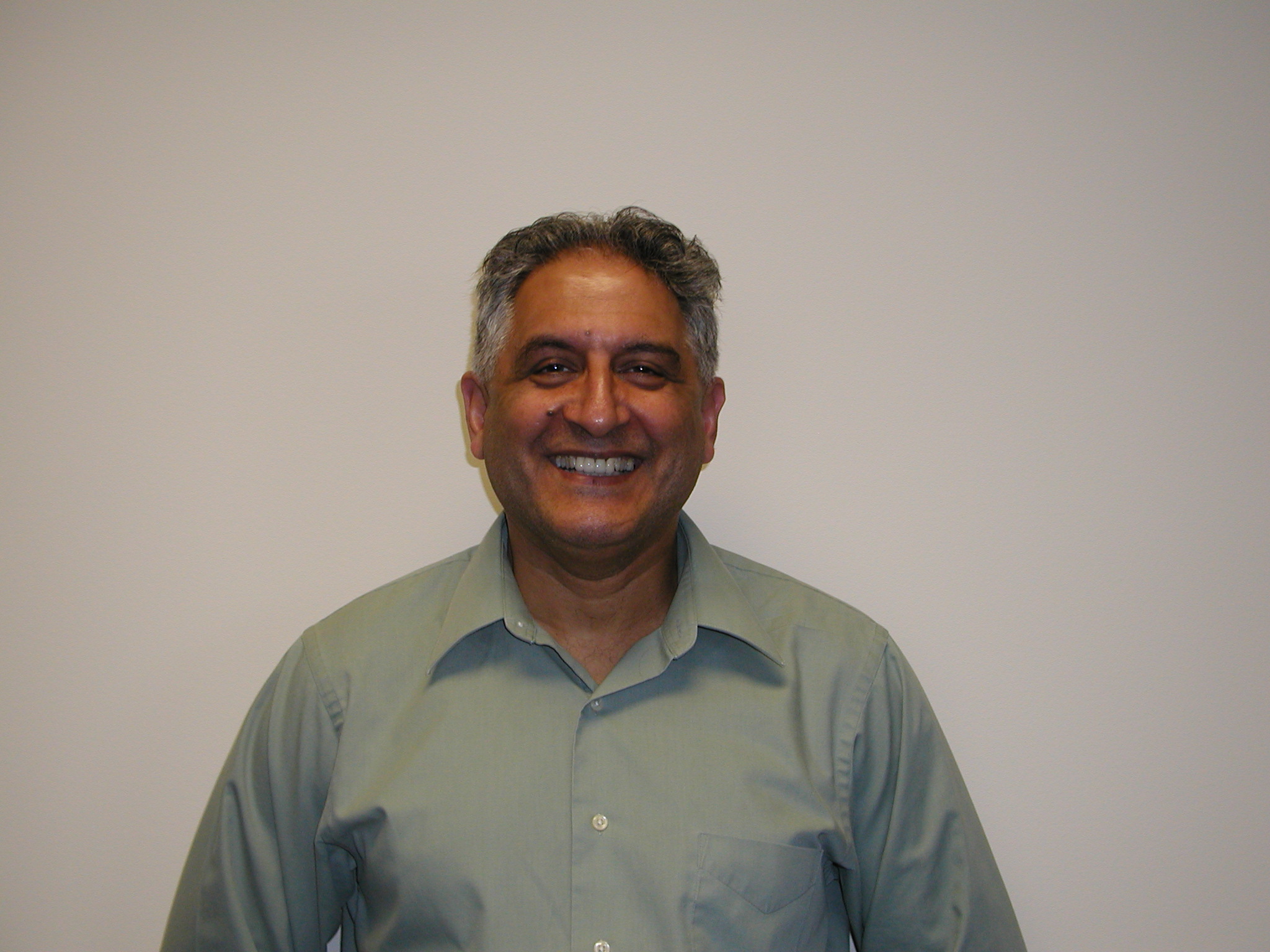
Corrosion of offshore oil and gas pipelines is a critical problem that can lead to catastrophic failure if not properly managed—from the design stage of the pipeline system through ongoing monitoring and maintenance.
Corrosion understanding and mitigation methods have greatly improved over time, but significant challenges remain in the difficult subsea environment, where assets can be located up to a mile deep or more.
The issue looms large on the radar scope of NACE International, The Corrosion Society, which has more than 25,000 members around the world involved in research and implementation of corrosion control methods such as protective coatings, inhibitors, cathodic protection (CP) and materials selection and design.
Says NACE Executive Director Bob Chalker, “NACE members are charged with protecting infrastructure and assets in every industry and in all types of environments and conditions while complying with strict regulatory requirements.
“Offshore pipelines pose particular challenges, not only from the harsh saltwater environment, but because they are difficult to access, especially as oil and gas companies explore, produce, and transport products from deeper and deeper water.”
NACE will present the forum, “Future Challenges of Deepwater Offshore Corrosion and Integrity Management,” at its annual conference, CORROSION 2011, to be held March 13-17 in Houston.
Chalker invited forum presenter Binder Singh—a 16-year NACE member with 28 years of nuclear, marine, and offshore corrosion experience—to answer a series of questions about subsea pipeline corrosion in particular and the latest solutions to control it.
Chalker: How serious of a problem is corrosion on offshore oil and gas pipelines?
Singh: Very serious. Many international surveys have revealed that offshore pipeline failures are attributed to internal corrosion more than 50% of the time. External corrosion is still an issue but is generally quite well addressed using good CP and coatings. The issues are more important and critical for deepwater pipelines whereupon designs are more complex; and inspection, monitoring, and repair are very difficult and costly.
Integrity management has tended to be regarded predominantly as a corrosion management exercise. This is now even more emphasized when dealing with deepwater conditions. The problems of corrosion and integrity management are compounded by the fact that project management is very heavily governed by costs and schedule. This is accepted as a fact of life but the odds are now moving more in favor of safety, reliability, and conservatism in both design and operations.
Chalker: What is it about the offshore environment that causes these assets to corrode?
Singh: Generally offshore environments and subsea reservoirs tend to be more corrosive than their onshore counterparts. On land, designers often get a chance to see the results of their work more readily; in contrast, the feedback cycle is more rare offshore and subsea, and thus a greater time lag exists between design, construction, and operations. Therefore, the dissemination of new information and/or knowledge is imparted more slowly. The situation is improving, however, as the offshore industry grows in stature and maturity. But materials and corrosion engineers should still be encouraged to follow up on the performance of their design and consulting decisions once executed.
Seawater is naturally corrosive but internal reservoir fluids can be even more so. Other physical parameters imposed by the subsea well, such as high pressures and high temperatures, can and do provide even greater corrosion stimuli to the pipelines and risers that are required to get the oil and gas products to market.
Subsea pipelines and risers are not easily inspected, and replacement parts and repairs can be far more challenging than is the case for equivalent onshore assets.
Chalker: What types of corrosion occur on offshore pipelines (internal and external) and what are the mechanisms?
Singh: It is all really about the exposure environments. Externally, we have seawater, and this environment is usually manageable using a combination of CP and coatings. However, for deep waters ( >1,000 feet) and ultra deepwater (>4,000 feet) under special circumstances, additional forces such vortex-induced vibration (VIV) and corrosion under damaged thick thermal insulation (a type of crevice attack) may prove to be a challenge, especially if the underlying fusion-bonded epoxy coating is compromised. However, close liaison between pipeline stress analysts and corrosion specialists has helped to identify such problem areas and formulate fit-for-purpose solutions. The use of intelligent pigging for pipelines in ultra deep waters also poses unique high-pressure challenges.
Internally, on the other hand, if you have reservoir formation or condensing waters present within the multiphase fluids, the contents of the pipeline can be very aggressive—especially with combinations of carbon dioxide ( sweet), hydrogen sulfide (sour), chlorides, sand, organic acids, etc. The aim is always to maximize production and that can often lead to physically aggressive flow regimes that in themselves can stimulate corrosion and erosion activity. Most damaging might be slugging, stratified, and misting flows. The key is “water wetting” either at the bottom of the line (water dropout) or top of the line (dewing or condensation activity). Other mechanisms such as microbial activity, corrosion under deposits, and weldment corrosion are also a problem under certain circumstances.
Chalker: What corrosion monitoring methods are commonly used, and which do you think are most effective?
Singh: There is rarely room to try out new technologies and most operators and clients therefore try to utilize established methods and technologies. For example, they use proven inspection and monitoring techniques such as smart/intelligent pigging, nonintrusive sand probes, intrusive electrical resistance probes and weight loss coupons. Specialist in situ corrosion spools such as the Field Signature Method and Ring Pair Corrosion Monitoring have been very usefully deployed. However, logistic or interpretation issues can still occur from time to time. In the future I think better integration of advanced polarization studies, x-ray diffraction, scanning electron microscopy, transmission electron microscopy and Raman spectroscopy (finger printing) may prove useful in conjunction with specialist coupons and corrosion spools.
Chalker: What are the differences when monitoring pipelines in shallow versus deep and ultra-deep waters?
Singh: The main difference is accessibility. Shallow (<200 feet) subsea pipeline locations can utilize limited diver inspections, but deep waters require remote-operated vehicle technologies for inspection, monitoring, and repairs. as a result, cost parameters, scheduling, manpower resources become more important we go into deeper waters. the demands are also heavier on deepwater designers to ensure that integrity solutions openly defined in terms of formal reports or statements. also, designs (especially at high pressure temperature) be so extreme “new” problems regarding materials corrosion often emerge, although these usually adaptations existing mechanisms. complex testing interpretation data trends. Chalker: How can potential corrosion problems be solved at the design stage of offshore pipelines; for example, material selection?
Singh: It is crucial to engage materials and corrosion specialists early in the project (concept phase onward). Operators are now tending to agree with this concept and are investing more effort at the capital expenditure (CAPEX) stage, and better utilizing subject matter experts rather than passing on the problems and costs to the operating expense (OPEX) stage. This step change may be referred to as the extended CAPEX phase and conveniently helps bridge the hitherto “gray” gap between CAPEX and OPEX. The use of prescribed corrosion key performance indicators (KPIs) is one way to encourage and better quantify risk and resolve corrosion issues. The use of cross-asset (usually intra-company regional) materials and corrosion performance data is extremely helpful in the calibration of risk-based modeling.
At the moment probes and coupons are preferred to be stationed at the host topsides; however, there is a need for deep subsea probe and coupon insertion, on-load retrieval and reinsertion, and technologies to be developed so that more realistic corrosion data can be generated outside the realm of intelligent/smart pigging alone. The use of representative corrosion spools giving equivalent data may be one promising way forward in this area.
Chalker: What other comments do you have on how industry is addressing pipeline integrity management solutions in the highly challenging offshore environment?
Singh: The idea of change within our industry is often difficult to implement, especially when so much is knowledge and risk judgment-based. The industry tends to respond when a major mishap occurs. In the present climate, industry may certainly react with reappraisal of designs, enforced verification of critical items, tighter regulations, etc. The challenge may be to redefine what parts of the offshore systems are in fact safety-critical. These aspects may indeed be better dealt with via the concept of preliminary hazard identification and hazard and operability study (HAZID and HAZOP) workshops, preferably at the early design and later design stages whereupon subject matter experts are brought together to thrash out and reach a consensus on materials and engineering decisions. Such HAZOP studies should also be performed within the first couple of years of the operating phase. I believe that the most challenging issues are the corrosion and integrity of deep pipelines, particularly under stagnant excursion and impinging flows, and for deep steel catenary risers (touchdown zone and stress/flex joints in particular). Other challenges will likely be the real-time monitoring of weldment corrosion under deep conditions where human inspection is not possible. Advanced intelligent pigging will help, but there are needs for satisfactory and cost-effective alternatives.
One emerging method of much interest is the use of inherently safer design (ISD), which by definition invokes a different attitude to the design process, and might deploy the use of corrosion-resistant alloys such as thin (3-mm) internal lining or cladding materials. Typical corrosion-resistant alloys may be appropriate stainless steels or nickel alloys or, alternatively, solid duplex stainless steels may be contemplated. However, care is needed since the use of mixed materials can sometimes create new issues such as galvanic attack at exposed interfaces, but solutions can usually be engineered after failure mode effects and criticality analysis (FMECA) and HAZOP workshops define and resolve via subject matter expert roundtable consensus.
The idea of ISD linked to the layer of protection analyses (LOPA) also provides powerful tooling where the risks of corrosion are very high and the consequences of failure are severe, and thus greater conservatism is warranted. These concepts work best when the risks are designated to be “as low as reasonably practicable.” And to that effect, most worldwide governing bodies are now revisiting their own regulations and enforcement policies, and there are even signs of cross-company cooperation.
Unfortunately there is still a tendency for material corrosion problems to be solved in a subject “disciplinary” direction; for example: a coatings expert will look for coatings solutions, a CP expert will try to cite CP solutions, a metallurgist will go for metallurgical solutions, and a chemist for chemical solutions.
Sometimes it is important to step just outside the envelope and look to better engineer solutions, and the best approach for that is likely the multidiscipline HAZOP workshop, wherein good (often adversarial debate) can be more readily accepted.
The development and evolution of new standards and best practices for deep waters is a big plus and the use of joint industry project teams ”marrying” the best of academia with the best in industry is a major development in this regard. If used properly it could be the industry boon that is so highly desired.
The sharing and amalgamation of best corrosion and integrity management from the premier influencing offshore regulatory regions, namely the North Sea, Gulf of Mexico, Brazil, Canada, Australia, India, Asia, etc., is to be encouraged. Such an evolution would greatly benefit the whole industry, in that lessons learned—and near misses divulged—would be better understood and applied by all.
(Note: A version of this article was originally published in Offshore Technology International.)
Binder Singh is principal adviser at Wood Group Integrity Management in Houston. He has 28 years of corrosion industry experience. He has a Ph.D. from the Corrosion Center at the University of Manchester, England. He started his career in the U.K. nuclear industry, and has worked in the marine industry in the offshore North Sea and, more recently, the Gulf of Mexico. During his career, he has witnessed a major increase in the importance of combating corrosion that parallels the acceleration of deepwater activity. Singh is a Chartered Engineer, Licensed Professional Engineer in the State of Texas and Fellow of the Institution of Mechanical Engineers. E-mail: binder.singh@wgim.com.
Bob Chalker is the executive director of NACE International, the technical society for corrosion professionals. Founded in 1943 by 11 pipeline engineers, NACE now has more than 25,000 members in 110 countries and is involved in every industry and area of corrosion prevention and control. With a mission to protect people, assets, and the environment from the effects of corrosion, NACE offers technical training and certification programs, sponsors conferences, and produces industry standards, reports, publications, and software. For more information, please visit www.nace.org.
Comments