February 2017, Vol. 244, No. 2
General
Driving Ahead for Secure Gas Compressor Operation
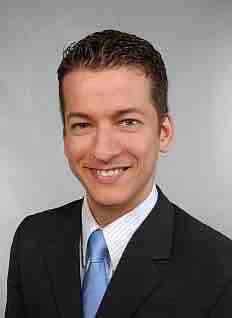
Electrically driven gas compressors have several advantages over compressors driven by gas turbines: The drive torque can be varied much quicker; the variable speed drive (VSD) system can be operated with high efficiency in a much broader operation range; there are no local greenhouse gas emissions.
In situations such as subsea installations, a VSD system may be the only option to power gas compressors. For these reasons, a number of large gas-processing plants employ electrically driven gas compressors.
Gas compression is energy-intensive, which means that high-power solutions for the VSD are required. A typical solution consists of a synchronous machine fed by a load commutated inverter (LCI) such as ABB’s largest drive, the MEGADRIVE-LCI.
The challenge for electrically driven gas compressor sites is that operations can be affected by disturbances in the grid. This was the case at the Statoil facility in Kollsnes, Norway. Its remote location means that weather phenomena such as storms occasionally cause brief disruption of the power lines, resulting in a sudden reduction of the grid voltage in one or more phases. Typically, the grid voltage is affected over a time span of 50-150 milliseconds (ms).
While these dips are only short in duration, they can have severe consequences. They can cause the LCI to trip due to inrush currents at the return of the grid voltage. Or, due to the sudden loss of drive torque, the compressor may enter unstable operating conditions such as surge, and is then tripped as a precaution to avoid mechanical damage and wear.
In either case, the operation of the gas compressor is stopped and a time-consuming restarting procedure needs to be carried out. The resulting interruption in the gas supply can mean financial losses that range into the hundreds of millions dollars a year for large facilities.
To address this issue, ABB has developed a model predictive torque control (MPTC) that has increased robustness in the case of grid disturbances. In particular, partial torque is now provided during partial loss of grid voltage.
The control scheme is based on model predictive control (MPC), an optimization-based control method that required the solution of a mathematical optimization problem at each millisecond on the embedded system.
Grid Disturbances
To understand the solution, it is useful to examine the nature of grid disturbances.
Symmetric and asymmetric dips: In an ideal three-phase system, the voltages in the three phases are sinusoidal with the same amplitude, succeeding each other with a phase shift of 120 degrees.
In the case of symmetric grid disturbances, the amplitude of all three phases is reduced by the same amount while the phase difference is unaffected. In the case of an asymmetric grid disturbance, the amplitudes of the three phase voltages are different, and also the phase separation of 120 degrees is not guaranteed.
Ride-through characteristics: The reaction of the frequency converter to grid disturbances depends on its physical properties as well as on the implemented ride-through procedure. The amount of energy stored in a frequency converter is negligible compared to the transmitted power. The power provided, and therefore the drive torque, depends on the type and depth of the voltage dip.
There are three classes of ride-through procedures:
- Zero-torque ride through: The operation of the frequency converter is interrupted, such that no drive torque is provided by the converter. Operation is resumed when normal grid voltage is available again.
- Full-torque ride through: The frequency converter continues its operation without reduction of the drive torque.
- Partial-torque ride through: The frequency converter continues operation, however, only partial torque is provided.
The amount of torque necessary to prevent the compressor from going into surge depends on its operating point. However, even if the available drive torque is insufficient to prevent surge, increasing the available drive torque delays the point in time when the compressor enters surge conditions. There is a longer grace period for the grid voltage to recover and for the initiation of protective measures for the equipment.
The requirements for the ride-through procedure can be summarized:
- Ensure the frequency converter does not trip, such as due to overcurrent.
- Supply either the requested drive torque, or, if that is not possible, as much torque as possible to prevent the compressor from entering surge.
- Compromise on agreed-upon secondary performance targets in order to increase the drive torque during a ride-through. Examples would be increased torque ripple or a small short-term DC voltage on the variable-speed drive (VSD) transformer.
Test Site
The Kollsnes plant processes natural gas from different oil fields in the North Sea. It has a capacity of 143 MMscm/d of natural gas. Dry gas is compressed and pumped through four pipe systems to Belgium, France, Germany and the United Kingdom. Six 41.2 MW export compressors are powered by VSD systems comprising dual-winding synchronous machines and LCIs.
The LCI is in a 2-by-6/6 pulse configuration with two parallel branches to reduce torque-pulsations. Each branch possesses a six-pulse thyristor bridge as line-commutated rectifier, a direct current (DC) link and a six-pulse thyristor bridge as load commutated inverter. The transformer employed onsite is a four-winding three-phase design, which is also connected to electric filter banks used for power factor correction and input current harmonic compensation.
The control variables of the variable speed-drive system are the firing angles (also called “control angles”) of the line-commutated rectifier and the load commutated inverter, as well as the excitation voltage for the rotor windings.
New Control Solution
The main element in the new development is the creation of a novel MPTC solution for the LCI. Compared to the classical control method, MPTC provides active control of the LCI firing angle which can be changed in the case of grid disturbances.
Furthermore, instead of executing independent control actions of the firing angles on the line side and the machine side, the MPTC coordinates both firing angles to reach the defined objectives. The controller also takes into account both alternating current (AC) voltage magnitudes and a constraint on the DC current can be defined to change the control behavior when the DC current is close to its boundary, thus helping to avoid overcurrent trips.
HIL Verification
Before the control solution was applied in practice, its effectiveness was verified on a hardware-in-the-loop (HIL) system by Typhoon, Inc. This consisted of the control hardware and the control software, exactly as onsite. The behavior of both the conventional control system and the MTPC solution were compared during a series of symmetric and asymmetric dips.
Symmetric dips: In the first scenario, the grid voltage magnitude was decreased in a series of voltage dips. Each voltage dip lasted for 200 ms and the voltage magnitude changed without transition within a microsecond.
Figure 1 depicts the grid voltage magnitude and the electric torque, first with conventional control (gray) and then with the novel model predictive controller (black). No trip occurred regardless of the controller used. However, the drive torque provided during the scenario differs significantly.
While the conventional control executes a zero-torque ride-through procedure for a grid voltage magnitude of 80% and below, the model predictive controller continues in operation and is able to provide partial torque. After the instantaneous reduction of the grid voltage magnitude, the MPTC requires about 25 ms to stabilize the drive torque to the steady-state.
Single-phase dips: In this scenario, instead of varying the grid voltage magnitude of all phase voltages, only a single-phase voltage is changed. Both controllers are able to provide more drive torque if only a single phase is affected (Figure 2). The MPTC, however, outperforms the conventional controller in terms of residual torque.
Based on the simulations, an estimate of the available drive power as a function of the remaining grid voltage was derived (Figure 3). This illustrates that the amount of residual power depends not only on the remaining voltage magnitude, but also on the number of phases affected by the grid disturbance. For extremely low grid voltages, operation of the drive is not possible.
Pilot Program
Following the HIL verification, the MPTC approach was implemented on two out of six export compressors at the gas treatment plant. This pilot program has shown that under normal grid conditions, the novel control solution works as expected.
During the course of the winter, a number of grid voltage disturbances occurred. One of these was an under-voltage event (Figure 4). The plots show the dip in the grid voltage and the corresponding torque – LCI with conventional control (black) vs. two LCIs with the MPC solution (dark and light gray).
The grid voltage was affected by a deep symmetric voltage dip down to about 30% of the rated grid voltage for 80 ms. This effect is a significant reduction of the available drive torque. While the conventionally controlled LCI executes a zero-torque ride-through, both MPC-controlled LCIs are subject to an undershoot from which they recover to provide 23% of the rated drive torque.
This result is a good match with the expectations raised by the HIL . The process was ultimately stopped by an external reason not related to the VSDS at 1.8s.
Following the test program at the Kollsnes plant, the MPTC solution has been implemented for three 7.5-MW booster compressors at Statoil’s Kårstø facility where the system regularly performed successful partial torque ride-throughs.
Summary
MTPC offers significant possibilities for the control of commercial multi-megawatt drive systems with much faster dynamic behavior where the underlying optimization problems need to be solved in under a millisecond.
It can help protect electric gas compressor operations during power and grid disturbances by providing the compressor with partial torque, preventing it from going into surge.
Comments