May 2018, Vo. 245, No. 5
Features
Using Analytic Imaging Technology to Detect Leaks in Real Time
By Gurjeet Bansal, Intelliview Technologies
Pipeline operators are increasingly taking a more proactive approach to maintaining the safety of their infrastructure and securing high-consequence areas (HCAs) from potential product releases. And while the pipeline is the safest mode of transporting oil, occasionally unintended leaks can occur.
Liquid transmission pipelines typically employ a multi-layered approach to performing leak detection on mainline assets. These methods include aerial and ground surveillance methods, SCADA by remote control rooms and other supervisory applications, such as computational pipeline monitoring (internal) based leak detection systems.
A variety of leak sensors can also be deployed within facilities to aid with detection and monitoring, however, timely visual verification of an alarm can sometimes be a challenge for remote facilities such as pump stations and pig traps.
Human error, sabotage, corrosion, aging pipes, and fittings are known to be contributing factors that cause leaks. Susceptible sections within a facility include controlling valves, pig traps, pig receivers, meters, and pressure gauges.
To further mitigate the risk associated with leaks occurring in above-ground facilities, North American pipeline operator Enbridge researched ways of providing enhanced monitoring of leaks. Key requirements included the ability to timely detect very small leaks within a pumping or pig-trap facility, in a highly reliable manner.
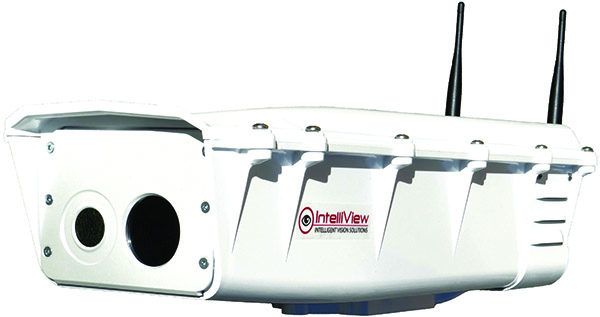
Canadian software company IntelliView Technologies responded in 2015 by developing a video based analytic system with the ability to automatically detect, visualize and notify of small fluid leaks, spills and pooling in short periods of time (seconds). The unveiling of a second generation technology followed in early 2017.
“Pump stations, pig launchers and pig receivers present a challenge because a release is normally very small and they require unique coverage of potential leak points” said Chris Beadle, VP for Sales and Marketing at IntelliView. “For a technology to be effective, it needs to provide sufficient coverage of the infrastructure and maintain an acceptable level of detection accuracy while returning very minimal nuisance alerts, all at an attractive and sustainable price point.”
Not the Right Fit
By design, external and internal leak detection methods widely used by the industry today are primarily intended for mainline transmission monitoring rather than pump station or pig trap environments. Acoustic cable based sensors could be negatively impacted by valves and pumps, and use of fiber cable may be restricted as it cannot be run through valves and pumps off of the mainline and the leak may not generate enough acoustic noise for the system to alarm. Moreover, these technologies do not have the ability to send a visual picture of a leak for verification, and so, would require a first response team to be dispatched to confirm an event.
Periodic inspections, whether on foot or by plane, involve direct visual scanning of equipment, providing the ability to pinpoint and address existing and emerging issues. However, both of these approaches are dependent on frequency of patrol and could potentially have gaps of monitoring time periods. A permanent or fixed imaging system, while providing constant access to current field information, does not by itself have real-time decision making power. The infusion of analytic software expands the capability of a camera by turning it into an automated detection and reporting tool, with video evidence enabling remote event verification.
Enbridge implements a combination of software and visual based surveillance techniques of its facilities, including 24/7/365, remote monitoring by control room operators and SCADA, dedicated control room based leak detection analysts, overlapping computational pipeline monitoring (leak detection) systems, and aerial and ground patrols. Enbridge is also proactive in the pursuit of enhanced technology, processes and training that contribute to enhancing safety and operational reliability. As a result, Enbridge continuously looks for emerging technologies which could enhance or add a layer of safety to their existing system.
“Enbridge has a defense-in-depth philosophy when it comes to leak detection. Having multiple layers of assurance provides better coverage and helps minimize risks,” said Cam Meyn, Leak Detection Testing & Research supervisor at Enbridge.
An initiative by Enbridge led to collaboration with IntelliView to develop a solution that generated real-time alerts with pictures and video of the event.
A series of field trials and feedback concluded in 2015 with the installation of the first generation intelligent imaging and alerting system which combines the capabilities of advanced visualizing sensors and artificial intelligence. Two years of ongoing product development paved the way for the launch of a second generation system, the Dual Camera Analytic Module (DCAM) in 2017. After a successful pilot project, the new system was approved and recently installed for long term use at two Enbridge locations.
The first generation system architecture was made up of individual thermal and color cameras wired to a digital video processor containing the analytic and video management software.
According to Mike McKay, IntelliView's director of Field Engineering Services, “This first-generation technology typically required cable trenching and dedicated masts, which adds significant cost and time to installations. The second generation DCAM has been designed to utilize wireless communications and video stabilization to allow for mounting on light masts with power already in place. This results in much lower site and engineering costs.”
Contained inside the DCAM’s compact enclosure are two imagers, an advanced LWIR uncooled microbolometer core and a high definition color camera, a built-in video processing engine with improved leak analytics, and automatic climate control to suit extreme outdoor temperatures. As a standalone device geared toward remote and unmanned applications, it is small enough to be mounted on an existing stationary structure, such as a light post or a trailer, comes equipped with either wireless or Ethernet connectivity for communications and can be powered through a local source, fuel cell or solar panel.
Small Leak Detection
A thermal sensor creates a grey scale image by capturing the heat signature of objects within its field of view. Because thermal radiation is unaffected by lighting and weather conditions, the technology performs just as well in any environment. The radiometric optical core used in IntelliView’s DCAM goes further than a standard thermal camera by being able to cover a larger area with its higher range and resolution, and obtaining temperature data at the pixel level, which enhances the detection ability of the leak analytics.
Detection using the DCAM is achieved with the application of analytic software to live thermal and color video feeds. The system qualifies a leak onsite and within seconds is capable of sending an alert, image and video to a control room or third party monitoring company and to selected email recipients via cellular network or satellite communications.
The software uses the capabilities of a multitude of technologies in its leak detection solution. A series of proprietary algorithms, environmental filters and user set conditions are in place to ensure high detection accuracy, optimal image quality, better image stabilization and minimal false positives due to ambient factors, such as glare, shadowing, heavy rain, and snow.
Operators need to be able detect and verify small leaks early to facilitate a speedy response. “The amalgamation of technologies in the DCAM makes liquid leaks as little as 0.36 cubic meters per hour detectable at a distance of 60 meters,” said McKay. “Depending on the pipeline flow rate, this leak rate could be equivalent to 0.1% nominal rate” he added.
Very few providers of imaging solutions offer analytic software with their solutions. Even fewer specialize in leak detection and own their software. “As authors and holders of our software, we have the ability to quickly optimize and enhance our leak analytics to better address the needs of an application. Highly experienced engineers and video analytics experts make up our in-house development,” said Beadle. “We are constantly working to improve our solutions to help increase detection ability while lowering false alerts for our industrial clients.”
Above-Ground Applications
There are other oil and gas facilities where the application of this technology is potentially warranted. For instance, bitumen could escape from well pads utilizing steam assisted gravity drainage technology, heavy oil hydrocarbons could spill from a refinery, and liquid products could leach from a liquid storage tank.
Located remotely, oil and gas facilities face specific challenges in monitoring infrastructure integrity. These challenges include stationing permanent personnel on site, availability of power supply, and reliability of communications network. Moreover, transporting of personnel for maintenance and surveillance can be cost prohibitive.
These scenarios indicate potential value in the use of stationary imaging technology for leak applications and remote monitoring/inspections. The technology enables the continuous and live monitoring of equipment from a control center or a computer through a web-based interface, and the automation of alert generation. There is also the reduction of onsite personnel and windshield time from routine site visits and event verification.
Temporary or moving locations will particularly benefit from a camera based system given the ease of transport. Its mobility, small frame and flexibility in usage make it ideal for trailer and offshore applications. P&GJ
Author:
Gurjeet Bansal is Corporate Communications Manager at Intelliview Technologies, a Calgary-based developer and supplier of liquid leak detection and industrial remote monitoring solutions.
Comments