August 2019, Vol. 246, No. 8
Pigging Update
Case Studies for Intelligent Pigging of Unpiggable’ Offshore Pipelines
By Edwin Rosier, Inspection Services, Intero Integrity Services BV, Netherlands
Offshore pipelines are often challenging for pigging and inspection. Riser pipes are vulnerable and critical for the asset-owners, especially in the splash zone. Some pipelines end at a manifold (PLEM) or a buoy for loading ships. Sometimes wye-pieces are constructed in the line or different diameters occur.
Near the platform itself some difficult (unbarred) tee-pieces, back-to-back bends or factory 5D bends create challenging configuration that give ILI vendors a headache. And of course, the intern diameter of most pipes are smaller than average because of the heavy wall thicknesses due to higher pressures in the system.
Inspection company Intero Integrity (formerly A. Hak Industrial Services) gained much experience using creative solutions to tackle these” unpiggable” pipelines. Some anonymous case studies show it is possible to inspect (and clean or gauge) the pipeline for the offshore oil companies around the globe. We also consider jetty and loading lines, as well as subsea pipelines to this topic.
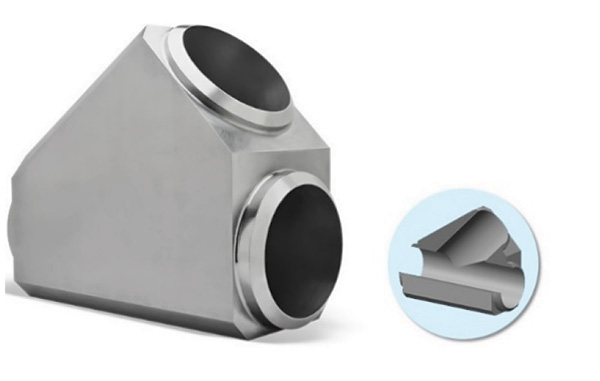
Most projects start with mobilizing offshore certified equipment to the platforms. This may include temporary pig traps, pumps in various types, electrical winches and some pipe spools to create a piggable and pumpable system:
- Dual-diameter pipelines can be handled using a Wilson pig as pulling body.
- Tethered tools need to be used when pumping is not possible.
- Bi-directional tools can sometimes be the only solution for jetty-lines or export lines to manifolds as well as for risers or other short pipelines.
- Pre-loaded pig launchers can be a solution to pass wye-pieces when pigging in one direction is only possible.
- Magnetic markers and divers are sometimes needed to secure a safe inspection operation.
- Creatives solutions to save water usage and handling can be found using piggy-bag lines.
- For some dry gas pipelines where flexible UT inspection tools are the only solution for safe pigging, the pipeline needs to be dried with nitrogen to enable operations afterward.
Introducing ‘Unpiggable’
Often the lack of any pigging facilities implies pigging has not been considered in the design and construction of the pipeline. Hence, more challenging features and geometries are likely present in the line. Additionally, such a pipeline has most probably never been pigged or cleaned before.
Due to the demand to transport the crude oil (and other facilitating liquids) from a wellhead at the seabed to a processing plant onshore a lot of pipelines are constructed in the past. From wellhead to a satellite or platform called a flowline. And from a satellite to a gathering or a separation platform and further on to mainland onshore.
In order to make an offshore inspection project possible we need to be aware of the more demanding safety requirements. Training your crew and having your equipment certified to lift onto an offshore platform is a necessity.
For us, this means having our pig traps and temporary product or water pumps certified. And the specialized equipment like nitrogen pressure vessels and vaporizers need to be available for offshore use as well.
Case Studies
Most of our solutions to inspect challenging pipeline configurations are practical solutions based on modification of our flexible inspection tool. By using our own test loop facilities, we can test the solution and making prove for the pipeline owner we can safely execute the underlaying inspection.
Riser inspection: Inspecting the splash zone of a riser, as a part of an offshore pipeline, is possible without setting up a pumpable pigging system. Instead of pumping a cleaning or inspection pig back to the platform one can use a tethered tool and pull the tools back with a cable on a winch. Figure 1 shows the set-up of this configuration for inspection purposes.
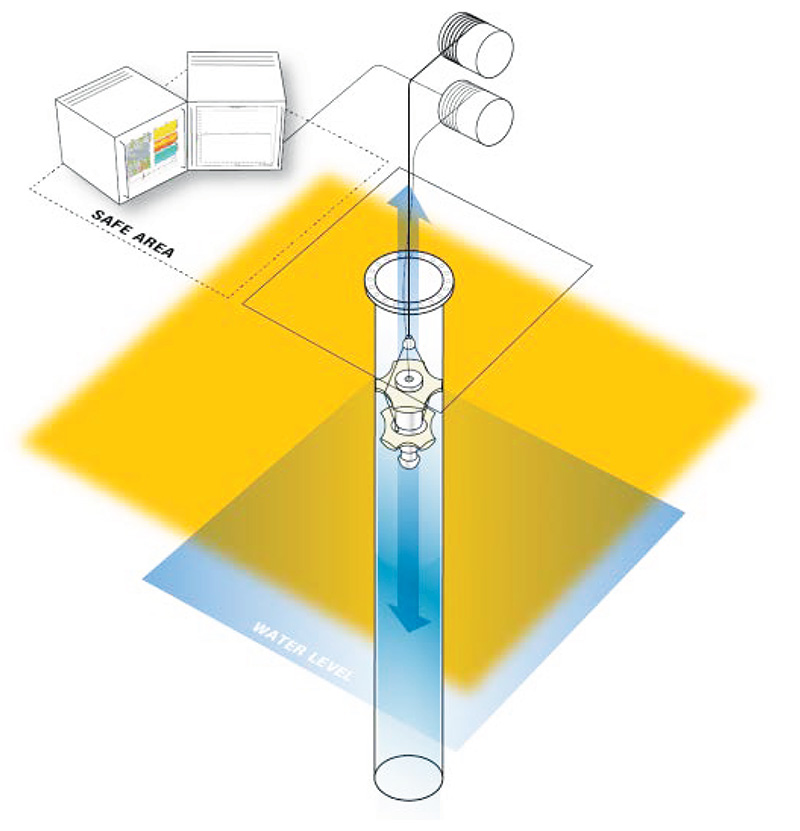
Bi-directional pumping of free-swimming tools through the pipeline can be modified. The tool can be moved vertically downward direction by adding extra weight to the tool. So, the riser pipeline must be opened and de-pressurized but still be filled with a liquid as the inspection couplant – mostly water but crude oil is also possible. (Additional HSE precautions need to be taken then to avoid pollution.)
Due to the Kaplan effect of a cable in a pipeline the limitation here is the number of bends and the total length of the pipeline. For this reason, the riser pipe is opened, and dismantled on the topside at the first flange. Preferably directly above the straight pipe of the riser.
A 90 gr bend mounted on top of the riser pipe.
Cleaning the pipe wall before UT inspection of the vertical pipe is more challenging, but luckily the vertical lines tend not to show much scaling on the wall. Various solutions are available, such as scrubbing with a steel brush chimney sweeper.
Challenging Configurations:
Often pipelines on the platform are engineered creatively. Due to the high pressures the pipes have high-pressure specifications, requiring in ring type joint (RTJ) flanges and heavy pipe wall like sch 160 or XXS.
Luckily for pigging purposes, most of the time bends have large radiuses like 3,0D or 5,0D although 1,5D factory bends also occur. For the Intero Piglet UT tool 1,0D or 1,5D bends are normally not an issue. In 2012, it at first got stuck in some 4-inch offshore pipelines. They should have been constructed as 3,0D-long radius bends, but 30 barg was not enough to push the tool.
We ran a caliper tool through the pipeline and found it had an ID of 77,46 mm at some point, probably due to the ovality of the sch XXS 3,0D bends.
The solution was to modify and strengthen the tool. Aa similar 3,0D bend was used to simulate the pipeline and execute a pull through test. Finally, we inspected four of these 4-inch challenging pipelines successfully for this customer.
Pre-Loading Launchers: In some subsea pipeline configurations installing a temporary pig trap is only possible by using a submergible launcher. For example, for pipelines ending up in a pipeline end manifold (PLEM) on the seabed.
After setting up an inspection protocol it might be necessary to either launch or receive cleaning and inspection pigs from subsea. Aa subsea receiver can receive several pigs in the receiver until retrieved.
One can pre-load a pig launcher with several cleaning or inspection pigs and launch to a platform or onshore installation. A special launcher with several branches is needed to launch the pigs one by one.
Using back pressure: In cases in which only bi-directional pigging is possible to clean and inspect subsea pipelines, there is another solution. For this, the line needs a gas rather than a liquid in the pipeline, and nitrogen is the safest solution.
A bidi pig can be launched to compress the available gas in the line until a certain pressure to be calculated. Retrieving the pig from the pipeline is now possible by letting the pressure drop from the launching side to push the pig back to launcher side; high pressures are required sometimes.
Proper tools and carefully controlled speeds are required to avoid bypassing of the first bidi pig.
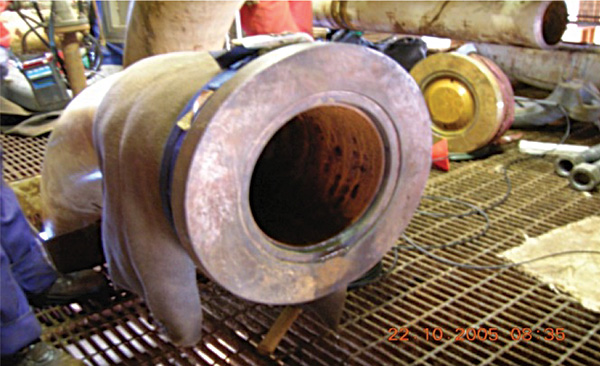
Dual-Diameter Inspection
Although maybe not always smart engineering, we experience dual-diameter inspections in North America, as well as in Asia. For example, a pipeline between two platform with 12-inch risers and a connection pipeline on the seabed with an 8-inch diameter.
Of course, the riser carries a thicker pipe wall, but still the difference between the inner-diameters is over 52% increase (194 vs. 295 mm ID).
In order to inspect the two 12-inch risers one could easily inspect the vertical parts bi-directionally with a standard 12-inch inspection tool, assuming it is bi-directional. But to inspect the 8-inch part of the pipeline to be reached through one of the 12-inch risers is more challenging.
The solution in this case was to mount a 12-inch pulling body, called Wilson, in front of the 8-inch inspection tool. This jeopardizes the failure risk when pumping this tool backward.
Smart pigging: Some offshore platforms or satellites are linked to each other by pipelines in order to make use of the facilities more efficient. For pigging and inspection this sometimes presents challenges.
This case is not an assumption, but a real inspection project executed successfully not so long ago.
The several satellites were linked by three pipelines. One is a typical wye piece construction, which can only be pigging in one direction. The other connection is a barred tee-piece.
Two subsea markers were placed at the branch side of these fittings on the pipelines. Vessels used the satellites in order to make pumping possible. Treated-seawater was used, which was then reused and pumped back to the launching side, in order to minimize the volume of contaminated water.
The necessary adoptions to the piping on the platform topside were made using temporary pipe spools and suitable pig launchers for the 8-inch and 14-inch displacement, cleaning and inspection pigs. The last important feature was making sure pigging was possible was making sure the valves at the receiving sides were closed when necessary to block the flow.
To displace the crude oil in the 14-inch pipeline MD, foam pigs were launched from the satellite. To displace the 8-inch pipeline, the marker was of use in order to stop the BiDi pigs in a controlled manner.
Here a BiDi pig came into play instead of foam pigs in order not to shred them through the bars and have them disappear. During these displacement runs the valves at all other branches were closed to create the proper flow direction toward the receiving platform.
After the displacement of all crude oil was completed, the bidi pig was retrieved from the 8-inch line by reverting the flow from one satellite. All other valves were closed in this situation.
For cleaning the pipelines, the cleaning pigs were launched from the satellite bi-directionally toward the fittings (wye-piece and barred-tee), then sent back using the pump spread from the support vessels to the main platform. The final cleaning run was executed from the separate satellite to the main platform in order have all debris and wax be removed from the lines.
The 8-inch pipeline was inspected first, after a gauging run is made by a dummy tool. The inspection tool was launched once from satellite to the tee-piece, and then sent back. During the next stages of execution, the temporary equipment on the 8-inch satellite was removed.
For inspection of the two 14-inch pipelines, the UT inspection tool was launched from satellites directly to the main platform. The 14-inch inspection tool was retrieved from the temporary receiving pig trap on the main platform.
Before dismantling all the temporary equipment from all the platforms, the pipelines were dewatered toward the main platform. The waCase Studiester was sampled and filtered before it was disposed of. P&GJ
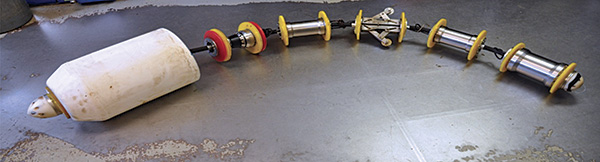
Author: Edwin Rosier is a mechanical engineering and also holds a degree in business administration in The Netherlands. He started his pipeline career in the military when he was appointed fuel pipeline specialist as an officer for the Dutch army.
Comments