July 2022, Vol. 249, No. 7
Features
Making the Link Between DAS, Machine Learning, Digitalization
By Matt McDonald, Director of AI & Machine Learning, Fotech
There is increased pressure for pipeline operators to improve efficiencies, reliability and safety. One way these demands can be achieved, which is widely regarded as the way forward, is digitalization – whereby digital technologies seamlessly connect to advance processes throughout an organization.
One area that enables digitalization is the use of advanced smart sensors for pipeline monitoring.
Pipeline networks are monitored for assorted reasons, for example, for detecting third-party interference and theft “hot tapping,” or leaks. However, regardless of the application, operators want confidence in their monitoring technology and assurance it will perform to the highest levels, providing high accuracy and low false alarm rates.
They also need to be able to respond quickly to any threats. Distributed acoustic sensing (DAS) technology is key to achieving this.
Demand Speed
The 2020 Colonial Pipeline leak incident is an important reminder of just how essential pipeline monitoring is and why improved smart sensing is key. At least 1.2 million gallons of fuel spilled into a nature reserve when the United States’ largest fuel pipeline leaked.
It is thought that the leak went undetected for weeks; it wasn’t identified until some residents found a puddle of gasoline and raised the alarm. Clearly, operators need reliable leak detection systems that will raise alerts fast.
There are many types of existing monitoring and leak detection technologies available based on internal systems. For example, some use pressure and flow readings from supervisory control and data acquisition (SCADA) systems.
There are also mass balance and real-time transient modeling (RTTM) and sophisticated computational pipeline management (CPM) systems, which use metering and complex calculations. However, because these systems infer a leak by computing, they tend to have long detectability times and extremely low sensitivity to small leaks.
Furthermore, existing leak detection systems don't detect most spills. Data from the Pipeline and Hazardous Materials Safety Administration (PHMSA) show that since 2010 there have been more than 4,000 spills on oil and fuel pipelines, but leak detection systems identified only about 7%.1
Incorporating advanced sensing technologies such as DAS can help pipeline operators to identify alerts more quickly and accurately.
Introducing DAS
DAS technology is a modern smart sensing system that uses fiber-optic cables running adjacent to a pipeline network. It is currently installed on thousands of miles of pipelines worldwide and is proving to be an accurate and reliable way of monitoring pipelines.
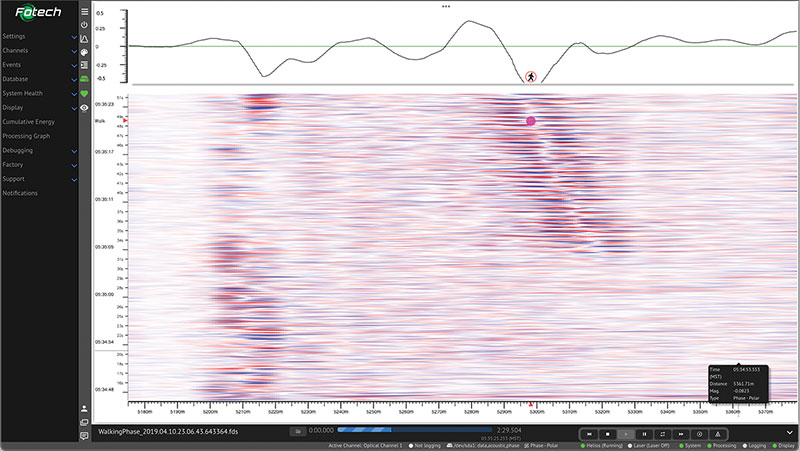
DAS provides continuous, 24/7 monitoring over long distances, up to 62 miles (100 km) – something that more traditional techniques cannot do. It also can detect a threat and raise an alarm within seconds.
DAS in Action
DAS essentially turns a fiber-optic cable into a sensor. The system is based on photonic technology to detect disturbances in the ground:
- First, thousands of laser light pulses are sent down a fiber-optic cable, and the fine pattern of light that is reflected back every second is monitored. If there is any disturbance, for example, ground displacement from a leak or mechanical digging, the soil experiences vibration, and this creates a strain on the fiber-optic cable. This changes the reflected light pattern, which indicates that an event has taken place.
- The second process incorporates advanced algorithms, processing techniques and machine learning to categorize the disturbances and alert the operator to the type of event that has occurred.
Meaningful Data
Operators need useful and actionable information. Making sure that data from the sensor are meaningful is vital. That is where machine learning (ML) comes in.
ML techniques train neural networks to classify pieces of data, and they automatically find the patterns in data to turn information into knowledge. This information can then be used to perform complex decision-making.
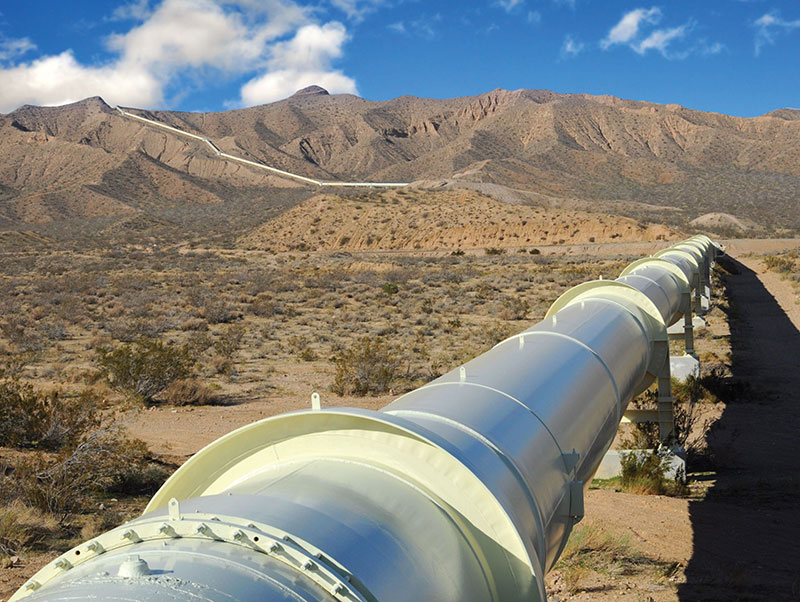
There are two challenges for ML. The first is to correctly identify the type of incident that has occurred. For example, if digging is detected, it is highlighted as a dig event, and not walking. Second, it can alert operators only when an event considered of interest has taken place. For example, the system needs to learn which incidents are unusual activity and require further investigation.
Nuisance alarms and reducing false positives are key issues to address with monitoring technology. For example, if spill detection technology is too sensitive, it can raise many false positives and operators will stop paying attention to these. ML is critical to reducing these. Algorithms in DAS are smart enough to ignore activities that are of no concern, reducing false alarms.
Smart sensors that incorporate ML provide an operator in real time with details about what happened, exactly where it happened and when it happened so they can have confidence in their system.
Automatic Responses
ML plays a significant role in advancing monitoring and detection, but what if the alert could automatically feed into a dedicated response? That is the next step toward achieving true digitalization, where digital technologies talk to each other to create efficiencies for operators.
Pipeline operators can be alerted to a threat within a few seconds using DAS technology, but the challenge then becomes how they respond to an alarm. Pipelines cover long distances, often across remote and difficult-to-access areas.
In such locations, it may take several hours or more to respond by road or by foot. In some cases, helicopters are likely to be a faster way to reach the location of a detected incident. However, this is a costly option and not suitable for pipelines where a tree canopy would make landing impossible.
In this case, unmanned aerial vehicles (UAVs) provide an attractive alternative to launch a fast response, to fly a direct route from base to the threat location. The latest DAS systems can be set up easily to operate with UAVs. DAS can automatically notify the UAV flight management system where the threat has been detected by providing Global Positioning System (GPS) coordinates in a message.
The UAV takes off autonomously and flies to the specified coordinates with the flight monitored from an operations room either at the pipeline operator’s security center or at the UAV service provider. UAVs can be used to capture visual and thermal images of activity and, if there are theft attempts, let the criminals know that they have been detected.
Threat Protection
Integrating DAS into a pipeline monitoring system enables operators to gain accurate intelligence quickly and efficiency, helping them to overcome one of their major challenges.
These smart sensors, which incorporate ML techniques, allow pipeline networks to advance on their digitalization journey to prevent both environmental and commercial disasters, to streamline pipeline integrity maintenance while optimizing pipeline efficiency.
DAS harnesses innovative ML computing and artificial intelligence to detect, to classify and to raise the alarm on integrity, leak detection and security events along a pipeline as they happen, in real time.
By going one step further and integrating a DAS monitoring system with UAV technology means operators can benefit from a powerful detection and response system to help protect against pipeline threats, to safeguard security and to reduce potentially catastrophic events.
References:
1 Soraghan, Mike, “https://www.eenews.net/articles/giant-n-c-spill-shows-gaps-in-pipeline-safety.
Comments