October 2013, Vol. 240 No. 10
Features
Five Key Challenges In The Oil And Gas Industrial Control System
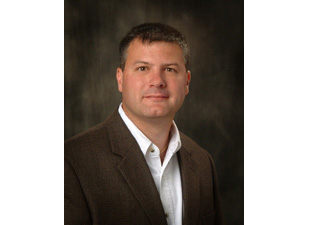
An Industrial Control System (ICS) is comprised of many disparate components, including hardware and software technologies, the system infrastructure–from the communications network to the physical plant–the human element for tasks that require manual intervention, and the environment.
To realize operational excellence, organizations must monitor and manage all aspects of the control system, turning data into usable business intelligence. To accomplish this, all of the components that comprise the control system must seamlessly interoperate with one another as if provided by a single vendor.
The system must be both reliable and able to withstand the elements that can affect operation. It must be extensible over time with the ability to scale and meet the needs of tomorrow. Lastly, the proper amount of security and safety must be built into the system to prevent costly downtime and damage, while safeguarding the environment and the surrounding community.
Who is responsible for implementing and maintaining the Industrial Control System and all of its components? The responsibility often falls on the shoulders of the oil and gas SCADA and measurement systems administrators. Unfortunately, these administrators may not have the proper training or experience for this role, or they may be overextended with other responsibilities. Due to the aggressive growth of shale as a source of natural gas in the U.S., qualified manpower for data collection is in increasingly short supply.
If fulfilling all of the requirements for data collection in these systems is considered a necessary evil for these administrators, what challenges must they overcome to ensure operational excellence? This article will explore the five challenges facing data acquisition today and how a robust, easy-to-use, and cost-effective communications platform can alleviate those challenges.
Challenge 1: Interoperability
In the oil and gas space, information produced by the ICS is typically required by a wide variety of applications, including: HMI/SCADA for visualization and control, Accounting Applications for Custody Transfer, Business Intelligence applications, and many others.
The hardware components can range from rod pump controllers, to flow computers and meters to PLCs and DCSs–and will vary depending on whether we are discussing upstream, midstream or downstream operations.
In a perfect world, all of this equipment would be standardized and provided by one enduring vendor. However, many oil and gas companies grow through acquisition and inherit sites comprised of disparate equipment–including sunsetting or legacy devices, or those that only speak native protocols. It is simply too expensive to rip and replace these with equipment the acquirer prefers. Therefore, there is demand for a solution to manage these brownfield sites as if the acquiring company developed them from scratch, and a broader industry need to quickly and effectively integrate both legacy and modern technologies within the SCADA enterprise.
Challenge 2: Functionality
Due to the remote nature of many oil and gas sites, the ability to communicate over a single telemetry method (such as radio, cellular, or satellite modem) with many field device types and the multiple networks that access them presents a communication challenge.
The importance of contextual data introduces an additional challenge. Some devices require a master to complete solicited requests while others publish data events in an unsolicited fashion to those interested in the data. The data acquired might be meaningless to the SCADA operator unless it is scaled or provided as a calculation with other data points from multiple devices.
Some data points change more frequently than others so the ICS must be configurable to accommodate these variations and ensure there is no loss of data. In the event that communication is lost and later recovered, the ability to collect missed data events is also a requirement.
Finally, optimal functionality requires the ability to collect both real-time data and API 21.1 historical audit (or EFM) data stored on flow computers?all in a network that might have limited bandwidth. The EFM data must be formatted into various files types depending on how the information will be used. It could be uploaded into measurement accounting solutions or inputted to a database for storage and operational analytics. Comprehensive functionality for these various conditions can be daunting and needs to be a consideration of the communications platform.
Challenge 3: Reliability
It’s no secret that the oil and gas industry is heavily driven by revenue. Custody transfer is the cash register of the industry and stakeholders use measurement data to determine compensation. Therefore, the systems that support this operation must be highly reliable. Downtime is expensive.
Real-time system health monitoring is essential for failure prediction and prevention, and allows operations to plan for and schedule maintenance during non-peak times in an effort to minimize downtime.
An effective monitoring and management solution must be highly reliable and robust, and provide the means for supporting device, network, and platform redundancies–as well as alarms and events to notify operators of impending problems. Further, a single tool for consolidating and managing data is more supportable and efficient–and therefore more reliable?than a multitude of disparate tools.
Challenge 4: Scalability
The number of operating oil and gas sites in the field continues to grow and each requires remote monitoring. It is too costly to place an expert at each site: experts need to be centrally located and provided with the necessary tools to fix an issue remotely, or to provide assistance to others who may be onsite. The amount of data required to effectively support this remote monitoring and automation also continues to grow.
Furthermore, growth via acquisition continues to increase the amount of assets that need to be monitored and controlled, and the number of users interested in the information these assets produce continues to rise. There are more data points available to users as a result of “the Internet of things”. And as automation technology improves, our ability to monitor and control an operation to improve efficiency and operational excellence constantly increases.
The perfect storm of industry growth and technological advancements has created a demand for truly scalable systems that do not require downtime to scale. And yet scalability may be the most elusive challenge in the oil and gas ICS because it tests our foresight and ability to plan for the unknown. The solution must meet today’s specification requirements and be scalable to support tomorrow’s operations?no matter what tomorrow may bring.
Challenge 5: Safety and Security
It is very common to have multiple operations, involving multiple users, within a single oil and gas drilling, production or transportation site. However, not all users should have the same access and privileges to the control system. Some users may only need to monitor an operation; others need to control it.
Due to the volatile nature of the products these sites produce, financial loss can occur within seconds and the safety of personnel and the environment can quickly be compromised. The high monetary value of goods and the social and political controversy surrounding the industry make oil and gas operations a primary target for cyber-warfare.
The Stuxnet worm grabbed the energy industry’s attention by proving that disabling and even destroying a facility is possible by infiltrating the system from outside? or even from within?the network. High-profile attacks like Stuxnet helped to move security concerns from the backburner to the forefront. And yet many control systems still rely on the OPC DA or “classic” standard, which is based on Microsoft Windows COM/DCOM and can present a security risk to automation systems.
Today’s OPC UA standard can provide user authentication that allows configurable restriction to sensitive data points based on identity, as well as the additional security of encrypting data as it passes between two designated nodes. This “UA tunnel” can facilitate connections through firewalls and even allow for secure communications over the Internet. Unfortunately, like any new standard, industry adoption of the OPC UA standard has been slow. Yet this reluctance to adopt new technology is being trumped by increasing security requirements and vendor’s capability to finally provide real world solutions.
The Solution
A comprehensive communications platform that ties all the parts together is needed in order to solve the interoperability, functionality, reliability, scalability, and safety and security issues discussed above.
The platform must be responsible for brokering communications between disparate devices and applications that are unable to natively communicate with one another. It also needs to provide the advanced functionality required to solve domain specific problems. Functionality requirements can range from controlling network characteristics, to prioritizing the collection of data, to performing analytics on raw data, among many others. The communications platform must be able to run uninterrupted and scale to meet the needs of tomorrow. Lastly, it must meet the security and safety challenges of today and be able to address the needs of tomorrow.
Is your organization overcoming these five challenges? If not, choosing a communications platform that addresses these challenges and fits the unique needs of your operation may be the first step.
Comments