October 2017, Vol. 244, No. 10
Features
Asset Tracking and Traceability: Field-to-GIS Solution
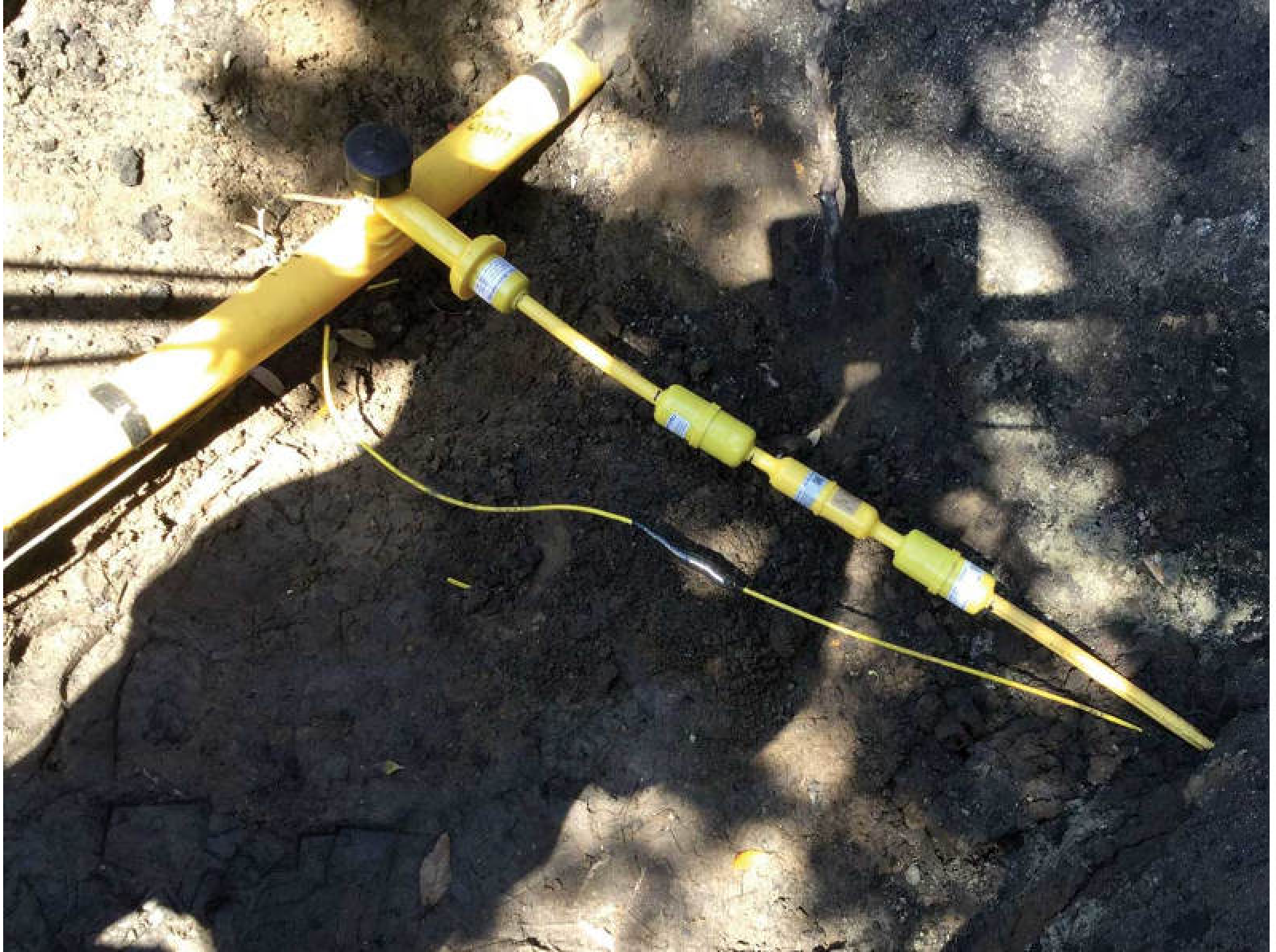
The industry has implemented a new materials traceability standard, ASTM F2897, that asset manufacturers are using to mark assets with standardized barcodes. In response to this standard, Pacific Gas and Electric Company’s (PG&E) has been working with vendor LocusView on a solution that leverages newly developed hardware and software to automatically create maps and material traceability records of assets during construction using GPS and barcode scanning.
The Distribution Material Traceability project has been a priority for PG&E as it strives for traceable, verifiable and complete records. ASTM F2897 defines requirements for the data – including lot number, manufacturer, manufacturer date, size and type used – in the tracking and traceability Base-62 encoding system to characterize components used in plastic gas distribution systems.
Over the past two and a half years, PG&E has conducted three field pilots, each with an improved version of the technology that incorporates feedback from end-users. This article will share successes and lessons learned from these recent and on-going deployments.
The end goal is to maximize the amount of software automation for the electronic as-built data collection process and minimize manual data entry. Where automation isn’t possible, the software should guide the user through the data collection process and have control points in place to prevent user error and ensure accurate data collection.
Mobile Solution
LocusMap is a mobile application for creating as-built maps of new construction with tracking and traceability data for pipes, fittings and joints. Data collection is automated with high-accuracy GPS and barcode scanning to create efficiencies in the field and improve data quality. Data is delivered from the field to the office in real-time to reduce mapping backlogs and delays.
The technology delivers data in a GIS format that is ready for review by back-office GIS personnel prior to integration into the enterprise GIS. GIS features are created and material properties are populated automatically from information contained in the barcode, thus eliminating the need for field or office personnel to manually enter data.
Deployment Insights
The purpose of the pilots was to evaluate the technology and workflow worked for new plastic installations at PG&E.
Training – Field users learned the technology best through hands-on training. Being able to physically interact with the technology enhanced their learning experience. In addition, requiring users to practice on a prototype pipeline in the classroom helped to solidify the concepts. Quickly following this up with job shadowing at a real construction site was critical in ensuring that the users were comfortable using the technology.
Construction Practices – Installation workflow and at what point the users choose to collect the electronic data varies from crew to crew. For example, some users collect data gradually as the day progresses, while others prefer to wait until construction is complete to map the assets. PG&E worked with LocusView to add flexibility to fit data collection around existing construction workflows.
As a result, the new version of the application provided a guided process that walks users through the required data collection steps. PG&E users also gave feedback on how to make the interface easier to use, including the addition of bigger buttons and color schemes.
Field users initially expressed concern over the increased data collection tasks being added to their existing workloads. Currently, users don’t complete paperwork until the end of the day, or even a few days after completion of the job.
Since one of the goals of the technology is to reduce this delay, users are required to collect data as construction progresses. Based on pilot data, it takes about one minute to create a feature, populate attribute information, and place the feature on the map with high-accuracy GPS. A change-management effort will focus on addressing users’ concerns and ensuring open communication with their management.
Barcode scanning – The use of barcodes to capture field data will require construction crews to install assets in a manner that allows efficient data collection. This includes installing assets with the barcodes visible and accessible from outside the trench. Tight trench spaces and trenchless installation of plastic assets require alternate workflows to capture the barcode information in advance, and to match the barcode info with the correct GPS coordinates, once installed.
High-accuracy GPS – One of the main reasons for PG&E to use this technology is the ability to capture high-accuracy GPS coordinates for improved GIS mapping. PG&E’s requirements for GPS accuracy has been established at 6 inches. The initial pilot used a public, real-time kinematic (RTK) network to provide corrections to GPS data. Based on recent advances in GPS/GNSS technology, PG&E and LocusView elected to setup RTK-base stations to provide dedicated services to PG&E field users.
While providing more reliable accuracy, this solution required the development of a simplified process to automate the connection to the appropriate base station when the mobile application is opened, and maintains a consistent connection throughout the data collection.
GIS record – In order to fully understand the quality of GPS accuracy, PG&E needed the software to capture data on individual vertices for pipe (line features). The latest version of LocusMap meets this requirement and provides a richer data set to help GIS users understand the quality of individual points.
While data is collected with high-accuracy GPS, additional techniques are needed to create the connected network required for GIS. Jobsite pictures are useful in understanding the actual geometry of installed assets and can assist GIS technicians in learning complex configurations.
However, PG&E wanted a solution that automatically created a connected network for simpler asset configurations. The project team is working to define “snapping rules” to automate the connection of assets to further reduce the time required to get assets mapped in the enterprise GIS.
Additional Applications
Beyond the collection of material and GPS data during new construction projects, PG&E and LocusView are working on additional applications to collect more information or cover other maintenance activities.
Locate, mark – Locating for one-call tickets is an excellent opportunity to capture location data for underground assets that can be used to update existing maps and records as part of routine operations. PG&E is testing the use of GPS to map existing assets during one-call locates and sending the data to the GIS department to update maps.
The locate-and-mark team maps the location of paint markings and any known features such as bends, tees, branches, meters and valve boxes. New standards, PAS 128 and ASCE 38 and CSA S250-11, provide effective frameworks to qualify accuracy and confidence of collected data. In the future, locate-and-mark personnel will be able to use GPS to locate assets.
Repairs/deactivation – Repairs provide an opportunity to cost-effectively collect data to update existing maps and records. GPS coordinates and basic material information, such as asset type, material and method of joining existing assets will be captured whenever they are exposed (such as during leak repairs).
There will also be a workflow for capturing deactivations in which existing assets are abandoned in the ground. Importantly, the technology will differentiate newly installed assets, existing assets and deactivated assets.
RFID markers – PG&E is also testing radio-frequency identification (RFID) markers to assist in locating difficult-to-find assets. The RFID markers, produced by the vendor ELIOT, will be used in conjunction with tracer wire in difficult-to-locate areas.
The RFID markers work in depths of 5 feet and can be programmed with asset information which can later be retrieved with ELIOT’s locating device. LocusView is working with ELIOT to create a method to transfer data from the RFID tags into the mobile application to enhance mapping and field-data collection. This will allow PG&E to capture GPS coordinates and the serial information of the ELIOT RFID markers when installed in the field, becoming part of the GIS record.
Plastic joint traceability – Joint traceability is becoming increasingly important. The technology captures information about how the joint was fabricated, including joiner name, equipment used, fusion parameters and inspection results. Joints are bar-coded to promote full traceability. Joiner’s operator qualification (OQ) status can also be recorded as part of the joint record. A joiner’s name and OQ status are captured from an employee OQ card and stored in the GIS record for the joint feature.
Pressure-test traceability – PG&E was one of the first companies to test the pressure test traceability system to create electronic pressure test records that can be monitored in real-time. The technology also creates electronic records that can be assigned to specific assets in GIS to provide full traceability.
Pressure and temperature during a pressure test can be viewed on the mobile application in real-time. Pass/fail criteria for a test are built into the application. If it is not within a defined range, such as 100-110 psi, and if the test is stopped early, the test will fail. The application will prompt the user to enter the reason for failures and allow the user to proceed to retake the test. All pressure-test attempts will be captured and failed tests will be able to identify problematic assets or procedures.
Mobile gas service record – the current version of the mobile application captures much of the data on PG&E’s gas service record (GSR). The goal is to expand the application to collect all GSR data electronically in a single application. Some GSR data is populated in the office and from other IT systems, so the application will need to integrate these new business processes. Field users will be able to view the pre-populated data and complete the GSR through a combination of GPS, barcode scanning, sensors and manual-data entry.
Where We Stand
The latest field pilot funded by the California Energy Commission involves a final six-month field pilot test including 20 users from different organizations involved in maintenance and construction, general construction and construction inspection, along with one contractor. The pilot deployment occurred over a six-week period that began in late April.
Two new locations were brought on board in July/August to participate for the remaining three months. One of the newest locations is testing the additional applications of plastic-joint traceability, pressure-test traceability and mobile gas service record. This is the largest scale field pilot conducted so far and will prepare PG&E for full deployment starting in 2018.
Authors: Danielle Mark is a gas engineer in the R&D and Innovation Department at PG&E, leading the evaluation and deployment of material tracking and traceability technologies.
Alicia Farag is CEO of LocusView Solutions and led the development of tracking and traceability technology at Gas Technology Institute.
Comments