Corrosion
Importance of Moisture Analysis in Pipeline Transportation
(P&GJ) — Nearly every substance is affected by moisture, which can alter physical, chemical and electrical properties. When transporting hydrocarbons such as natural gas, the presence of moisture in the pressurized stream can create serious problems.
Offshore Pipeline Design for CCUS
(P&GJ) — Design and construction of CO2 pipelines are similar to natural gas transmission pipelines. However, there are differences like: thermodynamic modeling, blow down modeling, specifying the maximum water content, pipeline fracture propagation control, use of elastomer materials and performing a quantitative risk assessment, mainly related to release modeling and defining the allowable exposure limits. These factors require special attention for CO2 pipelines, when compared with natural gas.
Control Rooms: Achieving SCADA Operational Readiness, Compliance
(P&GJ) — Implementing a comprehensive control room management (CRM) plan in today’s energy market can be a challenging task in that integrating it with modern supervisory control and data acquisition (SCADA) systems adds layers of complexity to the project’s implementation and compliance requirements.
Tech Notes: Unpiggable In-Line Inspection Completed in South America
(P&GJ) — A team of Dexon pipeline engineers recently completed the inspection of a 20-mile (32-km), 3-inch diameter unpiggable or “challenging” underground petrochemical distribution pipeline, running from an onshore processing facility to a port on the South American coast.
Creative Coating Solutions Make for Smooth Pipeline Expansion
(P&GJ) — How does an ambitious gas pipeline expansion, running nearly half the width of Texas, get coated? One spiral weld section of pipe at a time. To protect the more than 250 miles of new pipe added to the Whistler Pipeline in the southwest of the Lone Star State, applicators got inventive – creating an efficient and resourceful approach that helped the job flow as smoothly as the energy resources the pipeline now carries to millions of customers.
Pipeline Leak Detection Audits Provide Invaluable Insights
(P&GJ) — Ensuring the continuing effectiveness of leak detection systems (LDS) is paramount for pipeline operators to meet tightening safety and environmental regulations and minimize the potential risks of catastrophic events.
AMPP Conference Takes Aim at Corrosion
(P&GJ) — AMPP’s Annual Conference + Expo at the Colorado Convention Center in Denver has attracted 5,607 attendees involved in the corrosion control industry.
Sources: Russia Set to Mothball Damaged Nord Stream Gas Pipelines
Russia's ruptured undersea Nord Stream gas pipelines are set to be sealed up and mothballed as there are no immediate plans to repair or reactivate them, sources familiar with the plans have told Reuters.
New Approach to Digital Pipeline Integrity Management
(P&GJ) — Pigging is an operation that is regularly required by pipeline operators for both cleaning and data collection (intelligent pigging). Managing pigging schedules and risks is a significant challenge to operators/pigging vendors without an intimate knowledge of the pipeline.
Nanoparticles Transform Pipeline Cleaning, Integrity Management
(P&GJ) — Oil, gas, and multi-phase pipelines can be fouled with several types of deposits or internally restrictive debris. The actual type of fouling is dependent upon several factors including: the production fluid characteristics such as hydrocarbon product, water, and gas composition; the presence and composition of common oilfield contaminants, such as hydrogen sulfide, carbon dioxide, mercury, arsenic, zinc, lead, iron, and manganese and operating conditions (e.g., temperature, pressure, pH, flow regimes, etc.).
Pipeline Operator TC Energy Says Stress, Weld Fault Caused Keystone Oil Spill
Pipeline operator TC Energy Corp. said on Thursday a combination of factors including bending stress on the pipe and a weld flaw might have led to the Keystone oil spill in December and that it was expecting a hit of about $480 million.
AMPP Appoints Dr. Amir Eliezer as New Board Chairman
(P&GJ) — The Association for Materials Protection and Performance (AMPP), a global nonprofit representing corrosion and coatings professionals and industries in 130 countries, has named Professor Amir Eliezer, Ph.D., as chair of the board of directors. His term began on January 1, 2023.
Study Shows Soil Moisture Plays Big Role in Spread of NG Leaks
(P&GJ) — Soil moisture content is the main factor that controls how far and at what concentration natural gas (NG) spreads from a leaked pipeline underground, a new study has found.
Predictive Corrosion Modeling – Rise of the Machines
(P&GJ) — Pipelines play an important role in the international transportation of natural gas, petroleum products and other energy resources. To ensure pipeline operational safely, instrumented inspections and assessments are completed on a recurring frequency.
Sherwin-Williams Finalist for P&GJ Award for Best Corrosion Technology
Sherwin-Williams Pipeclad 2060 Moisture-Resistant Overcoat (MRO) offers an innovative approach to minimizing pipeline costs via its exceptional damage protection capabilities. The MRO is applied over a traditional fusion-bonded epoxy coating and provides superior damage resistance during pipe handling, storage, and horizontal directional drilling applications.
GPT Industries Finalist for P&GJ Award for Best Coating Technology
GPT Industries' EVOLUTION is a patent pending product that is the first of its kind to be a fully encapsulated isolating gasket. This proprietary coating has a greater than 50% increase in dielectric strength over existing isolation kits and it is compatible with all media that may be present within oil and gas pipelines.
Lake Superior Competing for P&GJ Award for Best Corrosion Technology
Lake Superior Consulting’s Atmospheric Corrosion Inspection iLINE App, which helps pipeline owners maintain continuous pipeline operations while adhering to Atmospheric Corrosion Inspections, which are required every three years by the Pipeline and Hazardous Materials Safety Administration.
CPCM – An ILI Methodology to Assess the Effectiveness of CP
The role of cathodic protection (CP) is to mitigate damaging corrosion from the surface of the structure being protected.
Safety Techniques for Aboveground Natural Gas Pipelines
There are a variety of techniques used to enhance the safety of aboveground natural gas pipelines. Coatings to minimize corrosion are an example of a safety aspect used by natural gas operators.
DIMP-Related Pipe Replacement Work Continues in Full Force US
While the amount of work to replace cast-iron and bare-steel pipe has declined in volume since the implementation of the Gas Distribution Integrity Management Program in 2009, there is still plenty of construction left to be done.
Highway Traffic and the Effect on Pipelines
Ruptures of natural gas pipelines in right-of-ways of roadways are less common, but when they occur, the devastation can be far more extensive than the more common ruptures.
Increased Safety for Natural Gas Pipelines
Local hard zones can cause sudden stress corrosion cracking in the through thickness direction. To detect and eliminate these local hard zones reliably during plate production, Dillinger developed a special eddy current testing system.
Challenges of Installing a New Pipeline
During the installation of a new pipeline, corrosion engineers must consider many different aspects of the pipeline and its corrosion protection. On the surface it may appear simple, thinking only of coatings and cathodic protection, but once construction is underway, the tasks are many.
Nigeria Losing 200,000 BPD to Pipeline Damage, Minister Says
Nigeria is losing an average of 200,000 barrels of oil per day - more than 10% of its production - to pipeline vandalism, the country's information minister said on Monday.
Key Win for Enbridge Oil Pipeline as Minnesota Court Affirms Regulator Approval
The Minnesota Court of Appeals on Monday affirmed a state regulator's decision that there is sufficient need for Enbridge Inc to replace its Line 3 pipeline, handing the Canadian company a crucial victory in its lengthy battle with environmental opponents.
Libya Oil Pipeline Leaks Hitting Output, NOC Chief Says
The head of Libya's National Oil Corp (NOC) reiterated on Wednesday the need for funds for much needed repairs in the oil industry after corroded pipelines recently hit production.
Strategic Approach to Automated Leak, Rupture Detection
Remaining vigilant is the best approach when mitigating oil and gas pipeline leaks and ruptures, particularly with new legislation and other requirements that can lead to penalties and fines, not to mention the negative impact on a company’s image.
A Different Perspective on Pipeline Repairs
For the past few decades, the industry has been repairing pipelines in the same fashion. Typically, either welded steel sleeves are used on our pipe, Type A or Type B, or composite materials such as E-glass, carbon fiber and Kevlar are used to repair defects.
Evaluation of Metal Loss Corrosion with RSTRENG
Corrosion metal loss assessment is a method for evaluating the strength of corroded pipelines that includes criteria from ASME/ANSI B31G, which is a guide for the evaluation of the remaining strength of corroded pipe.
Inhibitor Development for Extreme Conditions in Deepwater
Deepwater exploration and production has seen a higher-than-average growth in the past 10 to 15 years when compared to other sectors in the industry, brought about by high and stable production and technological advances that have driven lifting costs down to all-time lows.
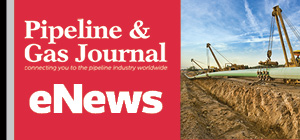
- Kinder Morgan Proposes 290-Mile Gas Pipeline Expansion Spanning Three States
- Enbridge Plans 86-Mile Pipeline Expansion, Bringing 850 Workers to Northern B.C.
- Intensity, Rainbow Energy to Build 344-Mile Gas Pipeline Across North Dakota
- Tallgrass to Build New Permian-to-Rockies Pipeline, Targets 2028 Startup with 2.4 Bcf Capacity
- U.S. Moves to Block Enterprise Products’ Exports to China Over Security Risk
- U.S. Pipeline Expansion to Add 99 Bcf/d, Mostly for LNG Export, Report Finds
- A Systematic Approach To Ensuring Pipeline Integrity
- US Poised to Become Net Exporter of Crude Oil in 2023
- EIG’s MidOcean Energy Acquires 20% Stake in Peru LNG, Including 254-Mile Pipeline
- Enbridge Sells $511 Million Stake in Westcoast Pipeline to Indigenous Alliance